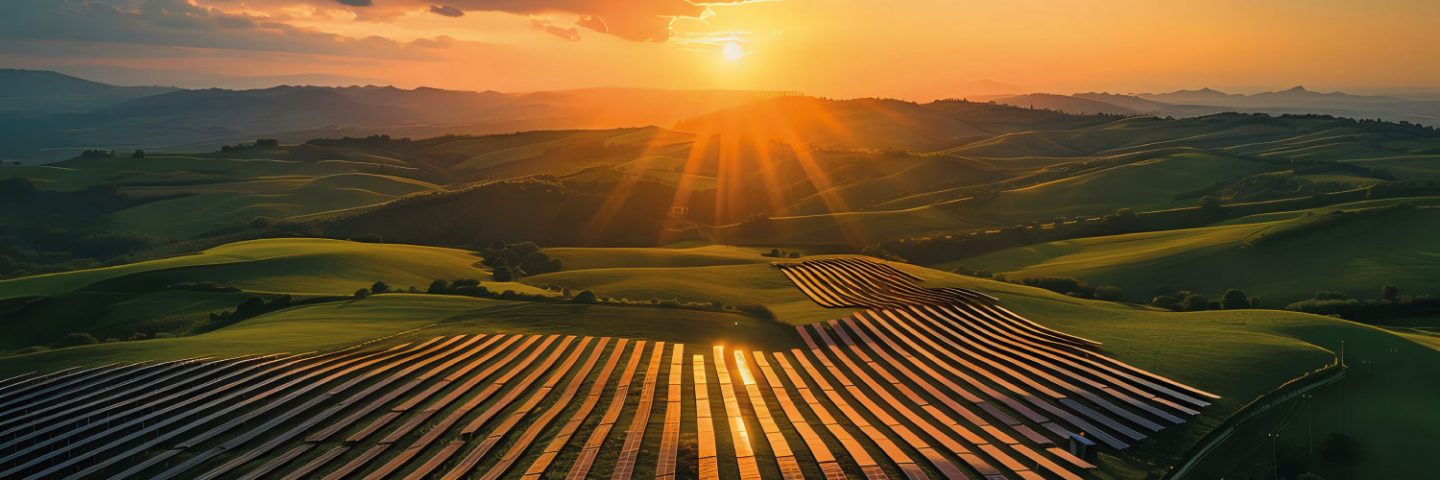
„Pożar w parku słonecznym – przyczyna nieznana, straty w milionach.” Takie tytuły pojawiają się, gdy system fotowoltaiczny wywołuje pożar. W takim przypadku zazwyczaj płoną tylko pojedyncze moduły, ponieważ systemy są odpowiednio zabezpieczone. Jednak oprócz szkód materialnych, utraty energii i wymiany uszkodzonych paneli, operatorzy napotykają na większy problem. Jeśli przyczyna pożaru jest nieznana lub wynika z usterki technicznej, kwestionowane może być całe okablowanie parku słonecznego. Średniej wielkości instalacja może mieć ponad 5000 połączeń. Sprawdzenie każdego z nich pod kątem poprawności montażu to kosztowny i czasochłonny proces. W przypadku szkody, odpowiedzialność za instalację spoczywa na instalatorach lub deweloperach projektu. Firmy ubezpieczeniowe również obarczają och winą.
W jaki sposób wada techniczna w okablowaniu może spowodować pożar?
Przyczyną pożaru często jest błędna instalacja lub brak właściwej konserwacji. Podczas montażu na miejscu, oprócz modułów słonecznych, dostarczane są także przewody i złącza. W zależności od odległości między modułami oraz odległości od paneli słonecznych przez wykop kablowy do falownika i zasilania sieciowego, wymagane są różne długości przewodów. W związku z tym, odpowiednią ilość przewodów tnie się na miejscu z bębna. Następnie przewód musi zostać odizolowany, a na obu końcach zaciskane są styki. Na końcu dodawane są obudowy złącza i przewód połączeniowy jest gotowy do użycia. Te etapy robocze, wykonywane na miejscu parku słonecznego w systemie just-in-time, mogą prowadzić do wielu błędów. Na przykład, podczas zaciskania, jeśli nie wszystkie druciki są prawidłowo połączone w styku. To prowadzi do błędnych połączeń, a w konsekwencji do nadmiernego oporu kontaktowego podczas przesyłania energii, co generuje ciepło. Inny błąd może wystąpić, jeśli połączenie między przewodem, a złączem nie jest odpowiednio zabezpieczone przed naprężeniami. W przypadku takiej wadliwej instalacji, połączenie wtykowe może się poluzować lub całkowicie oderwać, co często umyka uwadze. Nie zawsze przerywa to przepływ prądu. W najgorszym przypadku może pojawić się iskra, która spowoduje pożar.
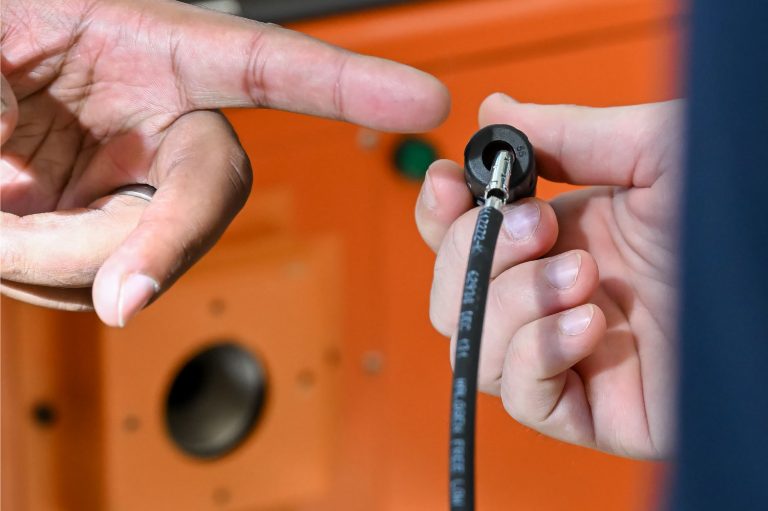
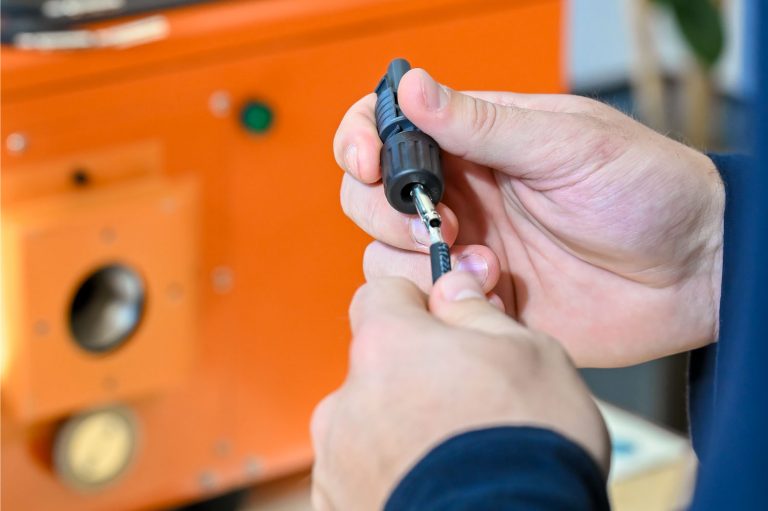
Problem montażu można rozwiązać u źródła
Aby zredukować lub nawet wyeliminować słabe punkty, firma LAPP opracowała całą gamę innowacji. „Przemyśleliśmy projekt złącza z perspektywy inżynierskiej. Stwierdziliśmy, że poprzednie rozwiązania nie są idealne” wyjaśnia Michael Zahl, dyrektor zarządzający Contact GmbH Elektrische Bauelemente, która produkuje złącza. Podczas przeprojektowywania złącza, inżynierowie LAPP skoncentrowali się na poprawie wrażeń dotykowych. Nowa konstrukcja obudowy zapewnia również sprzężenie akustyczne podczas montażu. Po pełnym dokręceniu przewód nie może już zostać wyciągnięty.
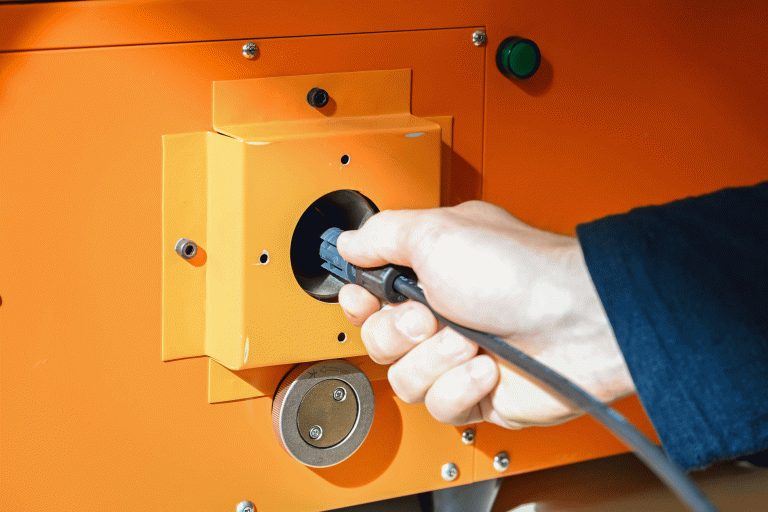
Jednak inżynierowie LAPP wiedzieli, że to nie eliminuje ryzyka błędnego zaciskania. Jak więc rozwiązać ten problem? „Zaciski są wykonywane na miejscu, bez stałego stanowiska roboczego. Każdy krok musi być wykonany z najwyższą starannością. A mimo to, od czasu do czasu, pojedyncze druciki, które nie są całkowicie zamknięte w styku, umykają uwadze” mówi Alexander Denk, wiceprezes jednostki biznesowej EPIC® w firmie LAPP. „Dlatego zaczęliśmy myśleć, jak ułatwić życie monterom na miejscu. Mianowicie, poprzez automatyzację procesu zaciskania.”
Maszyna została zaprojektowana zgodnie z wymaganiami LAPP. Klienci mogą już zamawiać wstępnie zmontowane przewody solarne w różnych długościach, od jednego do dziesięciu metrów. Dostępne są również indywidualne rozmiary opakowań i etykiety. Zautomatyzowany montaż, z odpowiednim protokołem, gwarantuje bezbłędne przewody połączeniowe. Wynalazcy tego rozwiązania są zadowoleni. Michael Zahl podsumowuje: „Dzięki temu możemy wyeliminować przyczynę błędnie okablowanych parków słonecznych. Odciążamy monterów na miejscu i możemy certyfikować wysoką jakość okablowania w protokole.” Alexander Denk dodaje „To prawdziwa wartość dodana dla naszych klientów.”
Patchcordy solarne jako usługa oferowana przez LAPP
Zautomatyzowany montaż to już przełomowa innowacja. Jest dostępna na rynku tylko dzięki firmie LAPP. Przy budowie parków słonecznych często zdarza się, że odpowiednie długości przewodów można określić tylko na miejscu. Zależy to od odległości między modułami słonecznymi. Aby umożliwić korzystanie z zalet zautomatyzowanego montażu podczas instalacji na miejscu, Alexander Denk i Michael Zahl pomyśleli „Dlaczego by nie dostarczyć rozwiązania bezpośrednio do klienta?” Pomyśleli, stworzyli, zrealizowali. W przyszłości klienci będą mogli uzyskać to rozwiązanie bezpośrednio na miejscu instalacji, na przyczepie.Zamiast mozolnej pracy ręcznej, wymagającej wielu narzędzi i odpowiedniej powierzchni roboczej, monterzy będą musieli jedynie stworzyć przewody połączeniowe w dwóch prostych krokach, korzystając z maszyn. Dzięki temu eliminowane są błędy związane z siłą naciągu lub zaciskaniem.
Informacje dodatkowe:
LAPP oferuje klientom wstępnie zmontowane kable patchowe do paneli słonecznych w zaledwie dwóch krokach montażowych.
W pierwszym kroku zacisk jest automatycznie tworzony, przy monitorowaniu siły zacisku.
Następnie złącze jest umieszczane na zacisku i montowane z momentem 5 Nm za pomocą automatycznego połączenia śrubowego. Test odciążenia dokumentuje, że przewód patchowy jest prawidłowo połączony, odporny na manipulację i odporny na warunki atmosferyczne.
Dzięki mobilnemu rozwiązaniu „Patch Cable as a Service” ten etap produkcji jest teraz możliwy również na miejscu, podczas instalacji parku słonecznego.
„To nie tylko znacząco ułatwia pracę monterom na miejscu. Oznacza to również, że instalatorzy lub deweloperzy projektów mogą dostarczyć operatorom parków słonecznych udokumentowane certyfikaty potwierdzające, że okablowanie jest poprawne i nie ma ryzyka wystąpienia pożaru” mówi Alexander Denk.Taki certyfikat może być również przydatny dla operatorów w przypadku uszkodzenia, ponieważ może zostać wykorzystany przez firmy ubezpieczeniowe. „Dzięki protokołom LAPP dostarcza operatorom dowód na jakość zainstalowanego okablowania, a tym samym zapewnia sytuację, w której wszyscy odnoszą korzyści” dodaje.