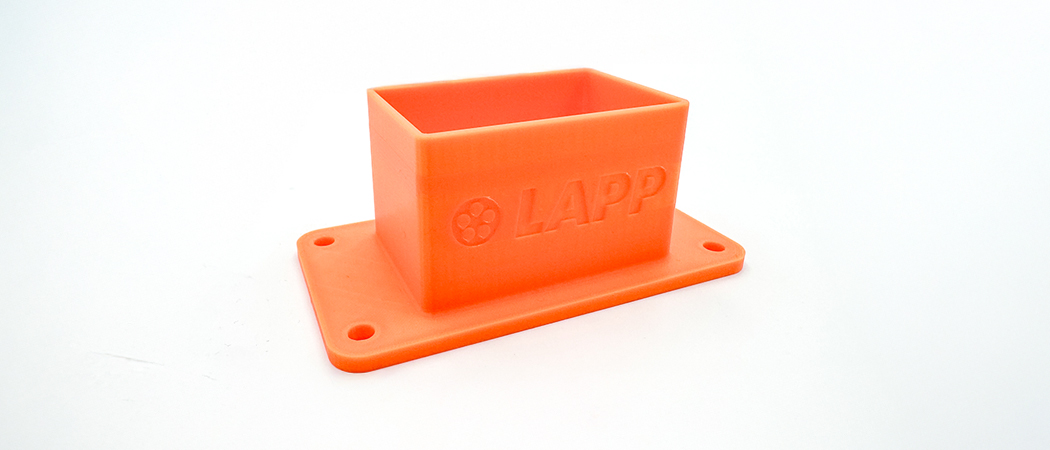
Die Wurzeln des 3D-Drucks reichen zurück in die frühen 1980er-Jahre. Im Jahr 1983 entwickelte der US-amerikanische Ingenieur Chuck Hull das Verfahren der Stereolithografie (SLA) – und meldete es 1986 zum Patent an. Damit war das erste additive Fertigungsverfahren geboren: Flüssiges Harz wurde mithilfe eines UV-Lasers schichtweise gehärtet – Schicht für Schicht entstand so ein physisches Objekt. Kurz darauf folgten weitere Verfahren, etwa das Fused Deposition Modeling (FDM), das heute weit verbreitet ist, oder das Selektive Lasersintern (SLS). Sie alle basieren auf demselben Prinzip: Statt Material abzutragen, wird es schichtweise hinzuaddiert – ganz im Sinne maximaler Ressourceneffizienz.
Vom Prototyp zur Serienreife
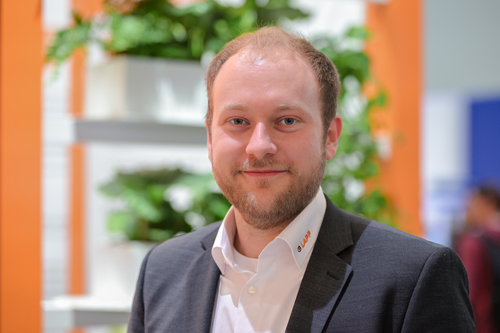
Lange Zeit war der 3D-Druck dann vor allem in der Produktentwicklung zu Hause – ideal für die schnelle Umsetzung von Prototypen, Testgehäusen oder Designstudien. Doch mit steigender Materialvielfalt und immer leistungsfähigeren Druckern begann für die Technologie der Sprung in die Serienfertigung. Heute nutzen Branchen von Automotive bis Medizintechnik additive Verfahren für komplexe Bauteile, die mit konventionellen Methoden nicht so leicht herzustellen wären. „Das Verfahren ist auf diese Weise sehr flexibel und effizient“, weiß Dr. Philipp Baron von LAPP. „Prinzipiell erlaubt der 3D-Druck eine dezentrale, bedarfsgerechte Produktion direkt vor Ort – ohne lange Lieferzeiten oder Werkzeugkosten und das ist gerade in Zeiten geopolitischer Unsicherheiten und volatiler Märkte unter Umständen ein echter Wettbewerbsvorteil.“ Der Weltmarktführer für integrierte Lösungen im Bereich der Kabel- und Verbindungstechnologie setzt mehr und mehr auf das innovative Druckverfahren, das bisher weniger im Bereich der Kabel, dafür aber umso mehr im Bereich der Steckverbinder Einsatz findet.
Innovationsmotor für kundennahe Entwicklung
So hat LAPP in den vergangenen Jahren in diesen Bereich, auch bekannt unter dem Markennamen EPIC®, investiert: neue Entwicklungsprozesse, neue Lieferanten, bessere Zusammenarbeit mit den Schnittstellen – und auch in Maschinen und Know-how im Bereich Additive Fertigung. Mit dem 3D-Druckverfahren können Kundenanforderungen noch schneller und kosteneffizienter umgesetzt werden. Am Standort in Stuttgart steht daher seit einiger Zeit eine hochmoderne Anlage, die sowohl für die Herstellung von Prototypen als auch Serienbauteilen genutzt werden kann. Mit Dr. Philipp Baron, in der Vorentwicklung zuständig für das 3D-Druckverfahren, sowie Stevens Sehic, Teamleiter Steckverbinderentwicklung, steht das notwendige Expertenwissen an der Seite der Druckmaschinen.
„Mit dem 3D-Druck fertigen wir laufend Prototypen, die wir intern selbst nutzen, um Ideen und Designentwürfe innerhalb kürzester Zeit realisieren zu können“, erklärt Dr. Philipp Baron. „So können wir viele Teile effizient testen und mit ihnen forschen oder beispielsweise ihre Steckbarkeit prüfen.“ Mit dem Verfahren lassen sich aber auch leicht Sonderwünsche von Kunden berücksichtigen oder schlicht und einfach testen, ob eine Komponente gut in der Hand liegt. Erfüllt ein neu entwickelter Steckverbinder dann alle Tests, die am 3D-gedruckten Prototypen durchgeführt werden können, können alle Neuerungen in die Serienherstellung integriert werden.
Schnelle Lösungen, echte Wettbewerbsvorteile
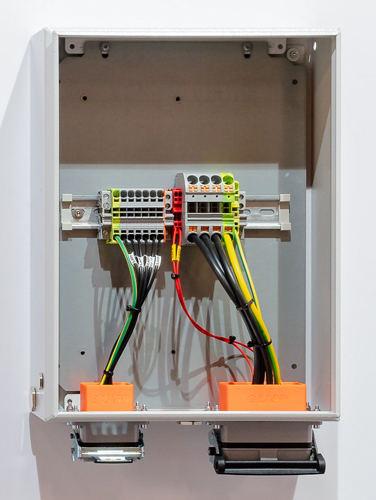
So schilderte etwa ein Kunde LAPP ein Problem mit Feuchtigkeit in den von ihm produzierten Schaltschränken. Selbst eingebaute Entfeuchtungselemente halfen bei der durch Temperaturunterschiede kondensierenden Luftfeuchtigkeit an den Innenwänden der Schränke nicht. Über kurz oder lang sammelte sich die Feuchtigkeit im inneren des Schaltschranks an und lief dann in Richtung der durch den Boden eingeführten Steckverbinder. Die Konsequenz: drohende Fehlfunktionen und mögliche Kurzschlüsse. Abhilfe schuf der Kunde bisher mit einem gelaserten Edelstahl-Bauteil, das den Steckverbinder von der Flüssigkeit abschirmte – eine aufwändige und teure Lösung, die keinen hundertprozentigen Schutz bot.
Eine Herausforderung für LAPP. Das Ziel: Eine einfache Lösung, die Feuchtigkeit von den Steckverbindern abhält und mit Standard-Bauteilen kompatibel ist. Schnell stellt das Expertenteam von LAPP ein Konzept auf und nimmt erste Druckversuche vor.
„Bereits drei Tage später sind die ersten serienfähigen Prototypen in LAPP Orange fertiggestellt – in der Serienproduktion technisch umsetzbar mit einem UL-zertifizierten Material.“
Der Kunde ist begeistert von der Hands-on Mentalität bei LAPP und der zügigen Lösungsfindung – eine große Chance für den Hersteller von Verbindungslösungen.
Für die EPIC® Serie von LAPP sind auf diese Weise und mithilfe des Additiven Fertigungsverfahrens bereits zahlreiche Steckverbinder sowie -komponenten entstanden. Darunter beispielsweise der EPIC® H-B 16, der sich durch sein verbessertes, rechteckiges Steckerdesign auszeichnet, der EPIC® H-Q TS M25, eine Eigenentwicklung von LAPP, die ein neuartiges Gehäuse mit Innengewinde für Kabelverschraubungen sowie kompakter Bauform aufweist, oder auch der EPIC® MCS-HC 2, ein Moduleinsatz für ein modulares Steckverbindersystem, sowie der EPIC® POWER M23, ein robuster Kontaktträger aus UL-zertifiziertem Material mit filigraner Struktur.
Technologie mit Entwicklungspotenzial
Die Beispiele zeigen: Additive Fertigung ist mehr als nur eine technische Spielerei – sie verändert, wie in der Industrie gedacht, entwickelt und produziert wird. Besonders dort, wo individuelle Kundenanforderungen schnell und flexibel umgesetzt werden müssen, spielt der 3D-Druck seine Stärken aus. Doch trotz aller Vorteile sind auch Herausforderungen nicht von der Hand zu weisen: Die Standardisierung von Materialien, Zertifizierungsprozesse sowie die Integration in bestehende Produktionslinien sind komplex. Dennoch: Die Technologie entwickelt sich rasant weiter, und mit ihr wächst das Einsatzspektrum – auch bei LAPP. Für Unternehmen wie den globalen Anbieter von Verbindungslösungen aus Stuttgart bietet die Additive Fertigung damit nicht nur Antworten auf heutige Fragen – sondern auch einen Weg, um den Herausforderungen von morgen kreativ zu begegnen.