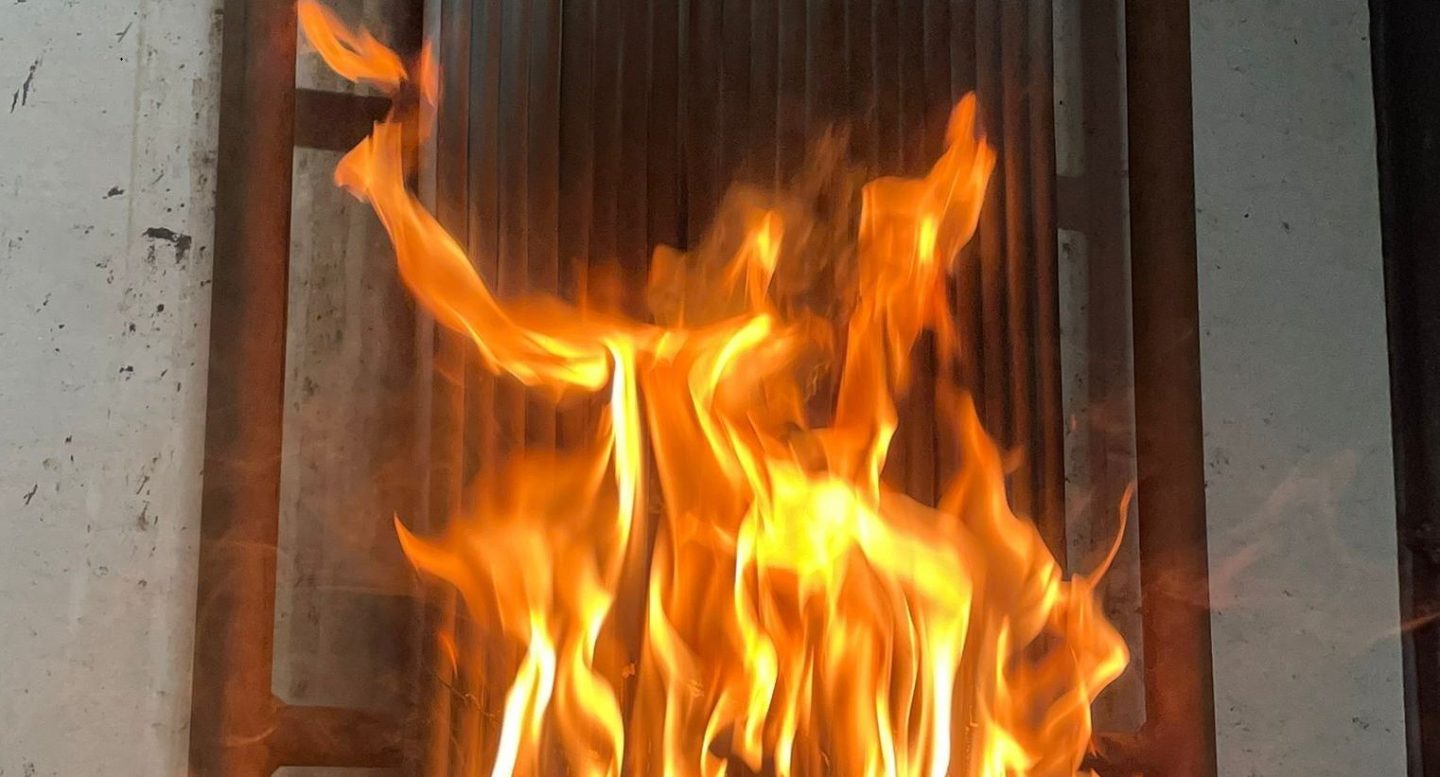
One customer, for example, is the National Centre for Oncological Hadron Therapy in Pavia, Italy. One of only six synchrotrons for tumour therapy in the world is located there. This synchrotron accelerates atomic nuclei to high speeds in order to remove tumours in the brain that are difficult to operate on. As there are people in the therapy building, the European Construction Products Regulation (CPR) law, which has been in force since 2017, comes into play. It applies to all products that are permanently installed in buildings where people are present. CPR assigns these products to different classes, which differ in terms of their fire behaviour. For this reason, CPR-classified signalling cables were required for the instrumentation in the bunker where the synchrotron is located. The company carrying out the work asked LAPP subsidiary Camuna Cavi whether they could recommend a product that could fulfil the required data transmission properties and was also CPR-tested. With success.
Extensive tests
In summer 2022, LAPP supplied 1.6 kilometres of the FG16XHOHM16 cable (corresponds to the German variant J-H(St)H PiMF). The product name refers to a signalling cable manufactured with insulated polyolefin-based conductors and equipped with static shielding. It fulfils the requirements of CPR class Ca-S1b,d1,a1, including EN 50399 for determining the emission of heat and smoke in the flame test, or IEC 60332-1-2, a test that checks the spread of flame on a single insulated cable. In addition, there were further tests in accordance with IEC 60754-2 (determination of gases produced in the flame) or IEC 61034-2 (determination of smoke density).
“We immediately realised that the law would affect many of our customers,” recalls Luigi Sterli, Innovation and Technology Manager at LAPP Camuna Cavi. Unfortunately, not all customers realised this at first. Many initially waved it off, claiming that CPR did not affect them. A mistake, as it soon turned out. Shortly afterwards, numerous customers contacted Camuna Cavi because they needed CPR-classified cables, says Sterli. There was increasing demand from refineries and the chemical industry in particular.
State-of-the-art test laboratory
The enquiry from Pavia, as well as from numerous other customers, did not catch the Camuna Cavi team unprepared. The company has been operating test benches for the above-mentioned standards for a long time and already offers a wide range of CPR-classified products. As CPR has led to an increase in enquiries, the management decided in April 2022 to convert a hall on the company premises into a state-of-the-art laboratory to replace the old one. The 300 square metre space now has all the necessary testing facilities, including a four metre high chamber in which cables are suspended vertically and exposed to a flame. A light sensor measures the density of the flue gas. The laboratory also carries out tests that are not yet required in CPR, such as fire resistance tests. Because toxic gases and smoke can be produced during such tests, the laboratory is equipped with an activated carbon filter and an exhaust gas scrubber.
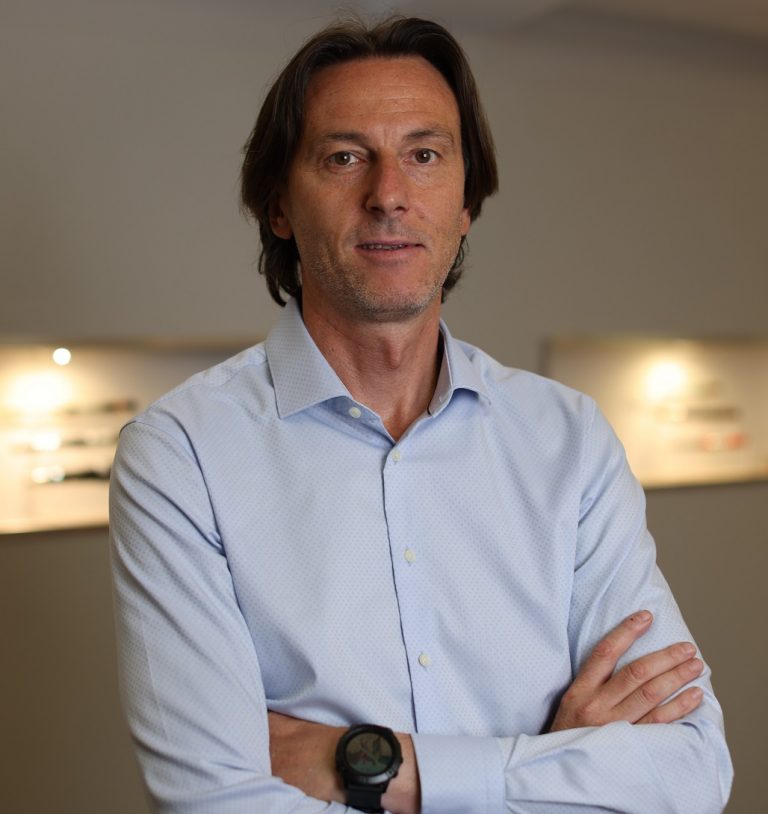
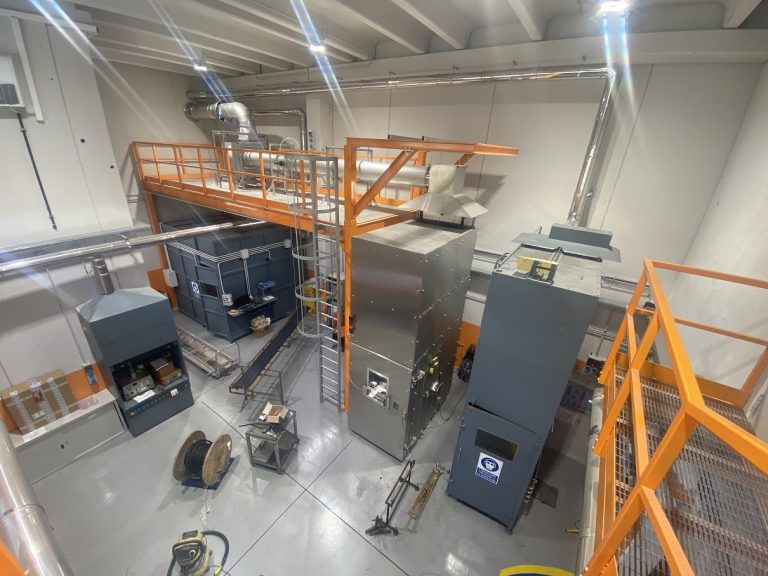
Camuna Cavi has tested the cables for the Synchrotron in its laboratories in accordance with the following standards required by current CPR regulations:
- EN 50399: Measurement of heat emission and smoke development of cables during the flame development test.
- IEC 60332-1-2: Test for vertical non-propagation of flame on a single insulated conductor or cable.
- IEC 60754-2: Testing of gases produced during the combustion of materials extracted from cables. Determination of acidity (by pH measurement) and conductivity.
- IEC 61034-2: Measurement of the density of smoke emitted by cables during a fire.
All these tests ensure excellent performance in terms of non-spread of fire and low emission of halogen gases and toxic vapours.
CPR for hydrogen factory
Luigi Sterli’s tip: “Take care of CPR early on when you are planning a project and don’t think it won’t affect you.” A customer of LAPP Poland also quickly realised that CPR certification was required for the permanently installed cables needed to set up a hydrogen factory in Hungary. The customer required 300V metering and thermocouple extension cables in accordance with the EN 50288-7 design standard, which had to fulfil the flame retardancy requirements of IEC 60332-1 and CPR class Eca and guarantee a wide operating temperature range of -40°/+105°C. A whole package of single-pair to 16-pair cables was required. In the end, the customer opted for LAPP because the Polish colleagues, in cooperation with Camuna Cavi, provided him with a customised overall package. Other manufacturers were not able to fully fulfil the requirements. It only took around seven months from the initial enquiry to the order being placed.
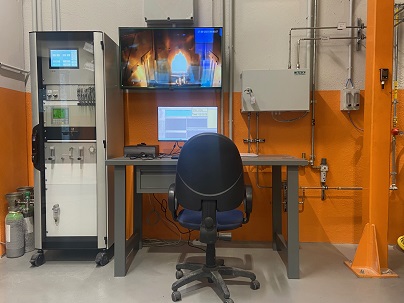
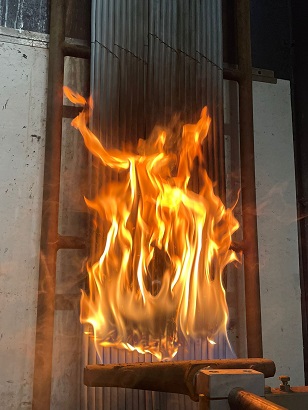
Safety made of steel
Absolute safety was also an issue at an oil extraction plant in Ukraine. The plant processes sunflower seeds, rapeseed and soya into edible oil and is so efficient that it can distribute and store up to one million tonnes of products per year.
For their construction, the electrical installation regulations that apply to the electricity sector in Ukraine had to be complied with. This law precisely defines the rules for the use of cables in potentially explosive atmospheres. The requirements are particularly strict in oil production facilities.
Initially, the customer had opted for standard cables in fully covered metal trays. However, when it came to the implementation phase, the customer opted for a steel armoured cable. In order to meet the customer’s requirements, Camuna Cavi, in collaboration with colleagues from Lapp Ukraine, developed a special customised solution of multi-core cables with cross-sections from 1 to 185 mm² with high temperature resistance (up to 105°C), shielded and armoured.
Specifically, it was a cable with an armoured layer and UV-resistant outer sheath. It had to be flame-retardant in accordance with IEC 60332-3-22 Cat. A and – if required – it also had to be supplied with an optional tinned copper wire braid as a shield for operating temperatures of up to 105°C. The Camuna Cavi team developed this customised solution in no time at all. It took just three months from the initial enquiry to the order being placed.