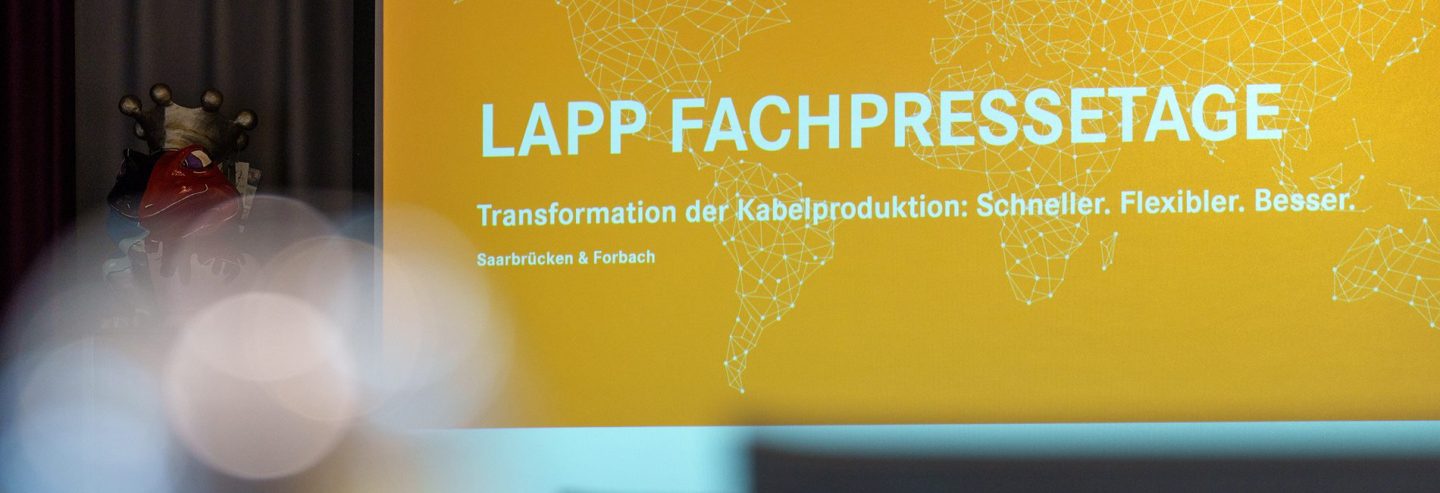
“We have to reinterpret the inventive spirit of my grandfather Oskar Lapp. The needs of our customers have changed greatly. Today, they expect added value when they make purchasing decisions. That is why we want to be the most customer-oriented company in our industry,” Matthias Lapp, CEO of Lapp Holding SE, summarised LAPP’s strategy. At the same time, the company also wants to be a technology driver for products and services.
The focus of innovation efforts is on specialising in selected growth industries such as renewable energies, intralogistics, automation technology, food & beverage, but also electromobility. The demand for cables in these sectors is already increasing enormously. This offers great opportunities for LAPP, but the challenges in production are also growing.
Production network is optimised
“The batch sizes are becoming smaller and smaller, the variants more and more diverse, and at the same time the demand for materials and processes to be as sustainable as possible is growing,” explains Hubertus Breier, Board Member for Technology and Innovation at Lapp Holding SE. For this reason, LAPP is currently working on optimising its global production network in order to significantly increase efficiency, delivery capability and flexibility. Machine utilisation is continuously checked in all production plants and parameters such as Overall Equipment Effectiveness (OEE) are measured. At the same time, LAPP is trying to be more sustainable in its use of materials. It’s a simple calculation: if the insulation of a 10-millimetre-thick cable were 10 micrometres thinner at an extrusion speed of 100 metres per minute, more than one tonne of plastic could be saved per hour. After all, in many applications today, a cable often lasts longer than the machines in which it is used.
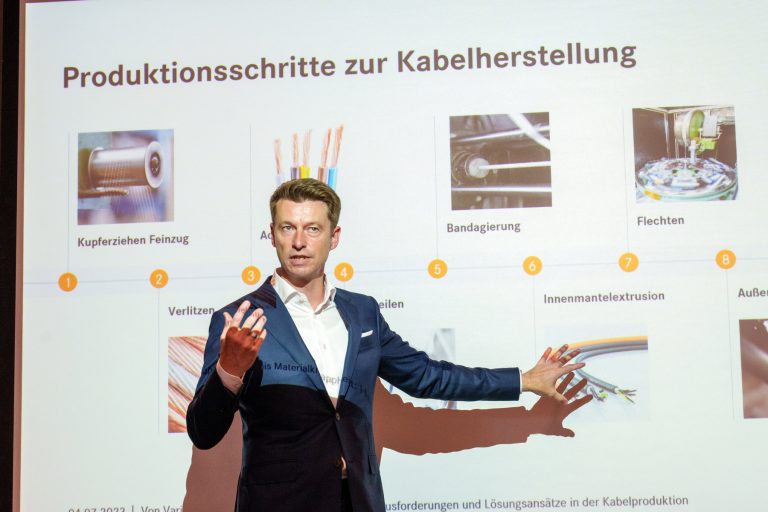
LAPP has defined three key areas for action:
- Digitisation in production so that the portfolio can be better planned throughout the supply chain. The goal is complete transparency of the planning process.
- Decarbonisation in production towards lower sales of copper, which on average is responsible for 88 per cent of the carbon footprint in LAPP’s products.
- Diversification: The aim is to become as independent as possible from individual suppliers in all regions.
Hubertus Breier: “Simply presenting innovative ideas to the market on a continuous basis does not guarantee a company’s success. It is just as important to successfully integrate these innovations into the production process. Everything has to work perfectly coordinated like clockwork. That is our daily challenge.”
Production tripled in Forbach
LAPP has already demonstrated how to transform cable production at Câbleries Lapp SARL in Forbach, France. With a bouquet of smart changes, the production capacities there are to be tripled by 2027. To achieve this goal, the French team has initiated or already implemented a whole bundle of measures. For example, an additional production building is being constructed so that the production area will increase to 28,000 m2 from 2024. An important component is the use of new, more flexible machines. In Forbach, for example, investments were made in a new, fifth jacketing line. This shortens the raw material changeover from PVC to PUR, for example, from three to four hours in the past to just ten minutes. The special thing about it is that the HELICAL extruders require up to 25 per cent less energy, allow a lower melting temperature and increase output by up to 100 per cent. “We can heat faster, clean faster, run faster and save energy to boot,” says Stéphane Kaczmarek, Senior Vice President of the LA EMEA production companies and Managing Director of Câbleries Lapp SARL, summarising the advantages.
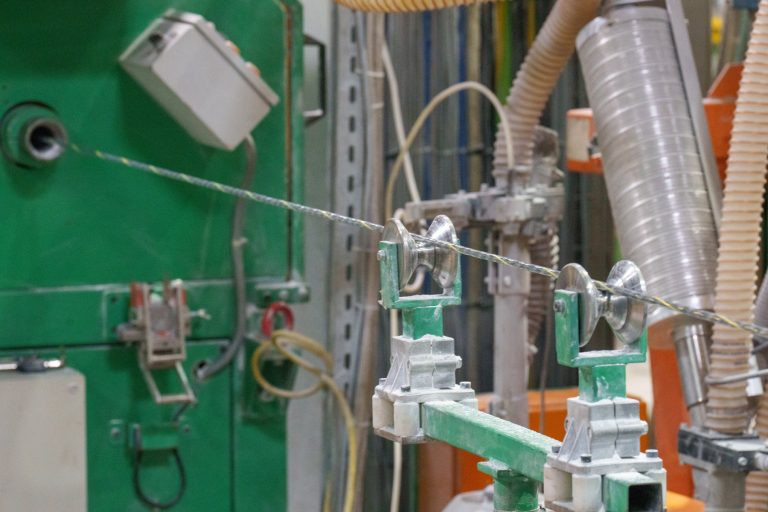
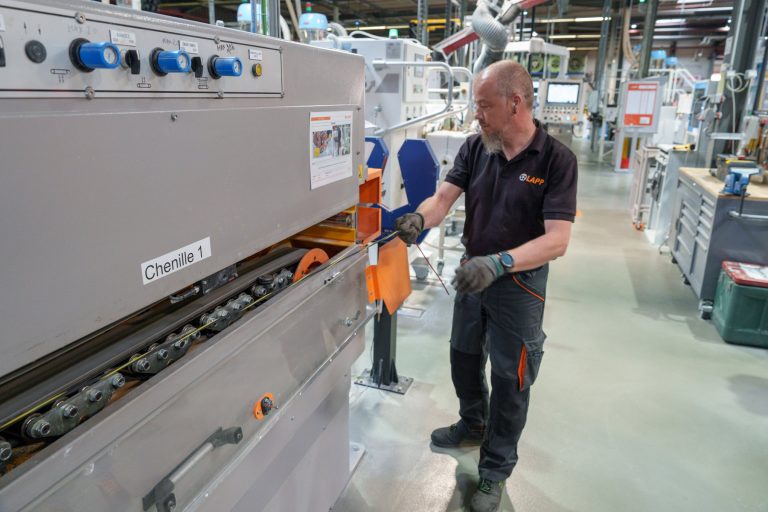
In the future, the four older jacketing lines will also be upgraded and optimised. The team had a particularly creative optimisation idea for the core line. Traditionally, the layout of such a production line is built in a single line. In order to optimise the walking distances, the new core line was to be built in a U-shape. The goal was to place all the work stations of the line as close to each other as possible. Today, the walking distances for the employees are 96 per cent shorter, the changeover times are reduced from 10 to six minutes and the machine can produce almost 50 per cent faster.
In order to further relieve the employees, simpler processes will be automated from 2024. Instead of manually loading drums onto pallets or lifting empty spools from the pallet onto the machine, robots will be used in future. They will also take over labelling. In addition, driverless transport systems will be used to transport raw materials to the machines in the future. In the medium term, it is planned to centralise all plastics with automatic distribution to the extrusion lines. And shredders will also be installed on each line for direct reuse of the plastic waste.
“In order to continue to be successful in a high-wage country like France, we have to manage to become more and more efficient with the same number of employees. The planned measures will therefore enable us to produce three times more with our existing team. With our Smart Supply Chain, we want to become the best, fastest and most flexible manufacturer in the cable industry,” emphasises Stéphane Kaczmarek.
Innovative structure in teamwork
In optimising the production lines, the team in Forbach works very closely with the French company Komax S.A.S., a globally active technology company that focuses on automation and extrusion. Komax has already delivered two complete production lines to Forbach. The first production line was a jacketing line, which according to LAPP’s specifications was to be set up in a U-shape rather than in a single line. “The aim was to make the line operator’s work as efficient as possible by reducing the movements of the employees between the machines on the production line to a minimum. We worked out the novel set-up together with the LAPP team in order to make the movements on the line as efficient and powerful as possible,” says Laurent Musitelli, Managing Director of Komax. In the process, every single work step and every move was scrutinised. For example, each control panel was positioned and optimised so that new production processes could be set up as quickly as possible.
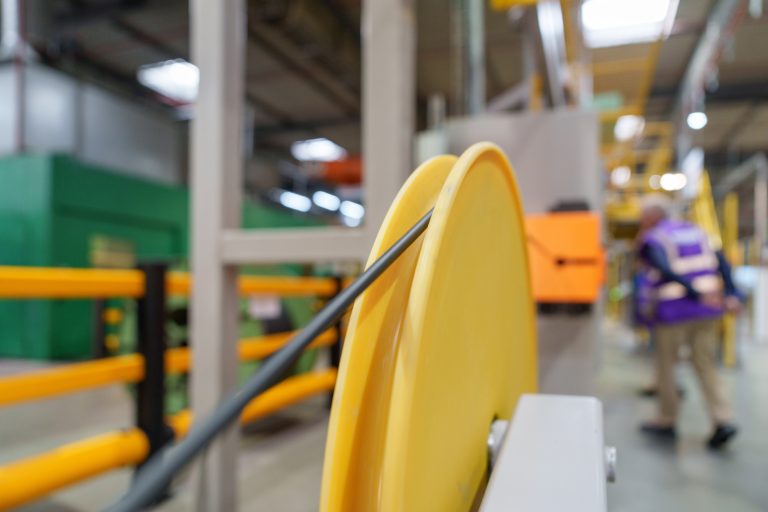
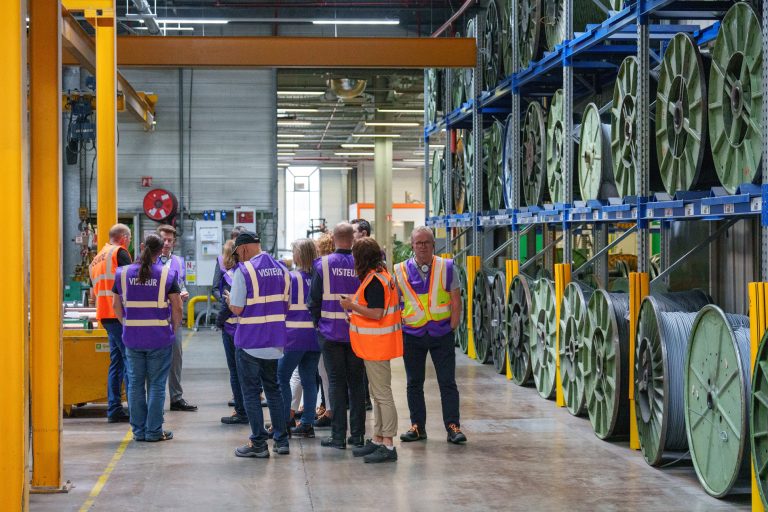
In 2022, Komax delivered a second so-called filler line. What makes it special is that these fillers are made from recycled PVC cable scrap. An important starting point for more sustainability.
A third production line from Komax is being delivered to Forbach these days. It will be responsible for insulating the individual copper wires. It, too, is being optimised to reduce set-up times by more than 90 percent. In future, changeovers will be possible within seconds. Laurent Musitelli: “Only through close cooperation are such improvements possible. Progress is always possible and long-term cooperation makes the impossible possible.”
Breeding ground for new ideas
But LAPP in Forbach is also setting a good example when it comes to direct current: when the new production hall is built, some consumers are to be supplied with the direct current generated from the photovoltaic system on the roof in a pure DC network with fewer converters and higher efficiency. LAPP is thus positioning itself as a technology driver for direct current as well. Matthias Lapp: “Technology affects us all and must be driven forward by the breadth of the workforce. Interdisciplinary cooperation is a breeding ground for new ideas.”