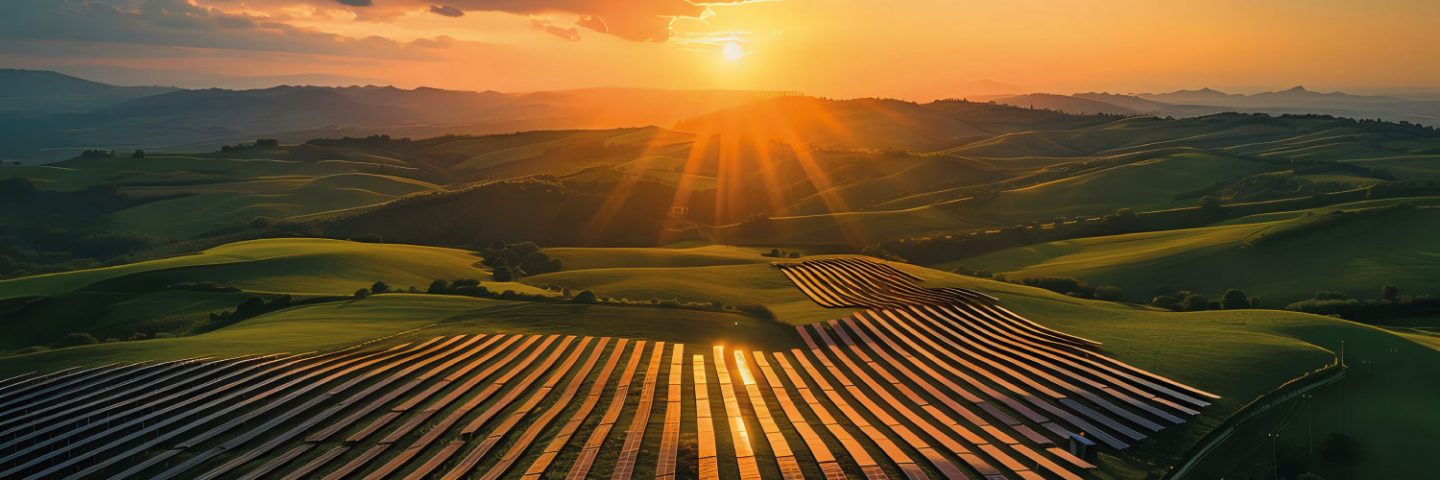
‘Fire in the solar park – cause unknown, millions in damage.’ These are the headlines you’ll see when a photovoltaic system catches fire. When a solar park catches fire, it usually only affects a few local modules, as the systems are installed with appropriate protection. However, in addition to the damage caused and the loss of power, as well as the necessary replacement of the affected panels, operators usually face an even greater challenge: if the cause remains unexplained or is even confirmed as being due to a technical defect, the cabling of the entire solar park is called into question. A medium-sized plant can easily comprise over 5,000 connections. Checking all of these individually to ensure that they have been installed correctly is a laborious and costly process. In the event of damage, solar park operators, as well as insurance companies, hold the installers or project developers responsible.
How can a fire be caused by a technical defect in the cabling?
The cause of a fire is often due to faulty installation and maintenance. During on-site assembly, the cables and plug connectors are delivered in addition to the solar modules. Depending on the distance between the modules and from the solar panels via the cable trench to the inverter and the grid feed, different cable lengths are required. Therefore, the required cable metres are cut from the drum on site. Then the cable has to be stripped and crimped at both ends. Connectors are then added at both ends, and the solar patch cable is ready for use. These work steps, which are carried out just-in-time outdoors on the site of the solar park, can lead to many errors: for example, during crimping, if not all the cores are properly connected in the crimp contact. This leads to faulty contacts and thus to excessive contact resistance during power transmission, which generates heat. Another fault can occur if the connection between the cable and the connector is not properly strain-relieved. In the event of such a faulty installation, the plug connection can loosen or come loose, which often goes unnoticed. This does not always interrupt the current flow. In the worst case, a spark can occur that causes a fire.
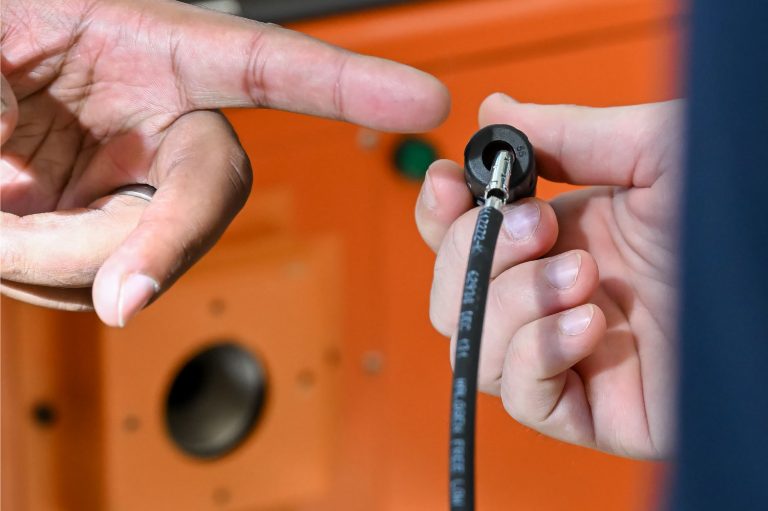
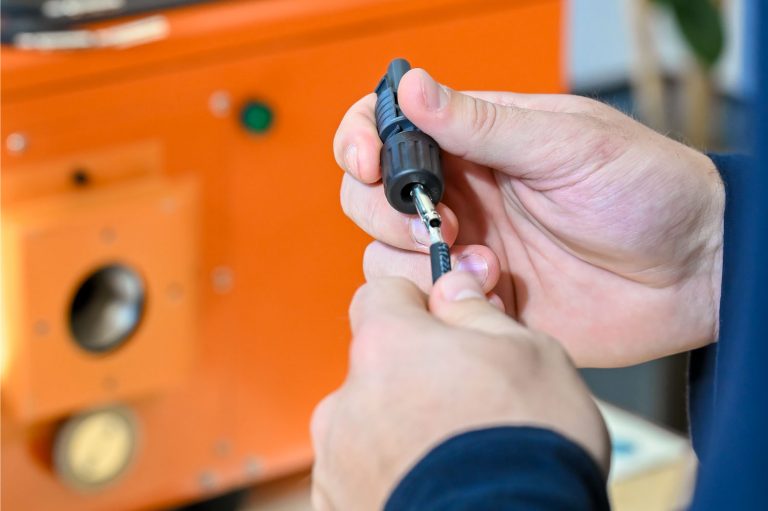
The problem with assembly can be solved at the root
To reduce or even eliminate these weak points, LAPP has developed a whole range of innovations. ‘We have rethought the connector design from an engineering perspective and have already determined that the previous solutions are not ideal,’ explains Michael Zahl, Managing Director of Contact GmbH Elektrische Bauelemente, a LAPP subsidiary that produces the connectors. When redesigning the plug-in connector, the LAPP engineers therefore initially focused on improving the haptics. In addition, the new structure in the housing ensures acoustic feedback during assembly. Once fully tightened, the cable can no longer be pulled out.
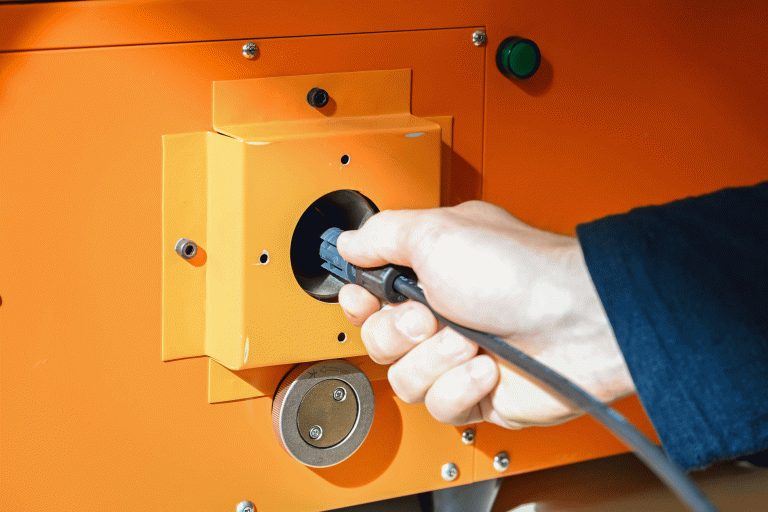
But the LAPP engineers knew that this does not eliminate the risk of an incorrect crimp. So how can this problem be solved? ‘Since these crimps are made on site, without a fixed workbench, every single step must be carried out with the utmost care. And yet, every now and then, individual wires that are not completely enclosed in the crimp go unnoticed,’ says Alexander Denk, Vice President Business Unit EPIC® at LAPP. ‘That’s why we started thinking about how we could make life easier for fitters on site. Namely, by automating the crimping process.’“
The machine was designed according to LAPP requirements and customers can already order prefabricated patch cords in individual lengths from one to ten metres, with customer-specific packaging sizes and patch labelling. Automated assembly with the appropriate protocol guarantees error-free patch cords. The two inventors of this solution are satisfied. Michael Zahl summarises the advantages: ‘This enables us to eliminate the cause of incorrectly wired solar parks. We relieve the burden on installers on site and can certify the high quality of the cabling in a protocol.’ And Alexander Denk adds: ’This brings real added value for our customers.’
Solar patches as-a-service from LAPP
Automated assembly is already a groundbreaking innovation that is only available on the market today from LAPP, the leading provider of integrated solutions and branded products in the field of cable and connection technology. When constructing solar parks, however, it is often the case that the appropriate cable lengths can only be determined on site based on the distances between the solar modules. In order to also enable the advantages of automated assembly during on-site installation, Alexander Denk and Michael Zahl thought: Why don’t we bring the solution to the customer? Thought, tinkered, done. In the future, customers will be able to obtain this solution directly at the installation site on a trailer. Instead of the laborious manual work that used to be required, with a handful of necessary tools and without a proper work surface, the installers now only have to create the patch cables in two steps using the machines. This eliminates tensile strength or crimping errors.
Info box:
LAPP offers customers pre-assembled solar patch cables in just two assembly steps.
In the first step, the crimp is automatically created with crimp force monitoring.
Then the connector is placed on the crimp contact and mounted with 5 Nm using the automatic screw connection. The strain relief test documents that the patch cable is connected correctly, is tamper-proof and is weatherproof.
With the mobile solution ‘Patch Cable as a Service’, this production step is now also possible on-site during the installation of a solar park.
‘This not only makes the work of the fitters on site considerably easier. It also means that the installers or project developers can provide the solar park operators with documented certification that the cabling is correct and that there is no possibility of fire here,’ says Alexander Denk. This certification could also be useful for operators in the event of damage, as it could be used by insurance companies, because: ’With the protocols, LAPP provides operators with proof of the built-in quality and thus, so to speak, a win-win situation for everyone involved.’
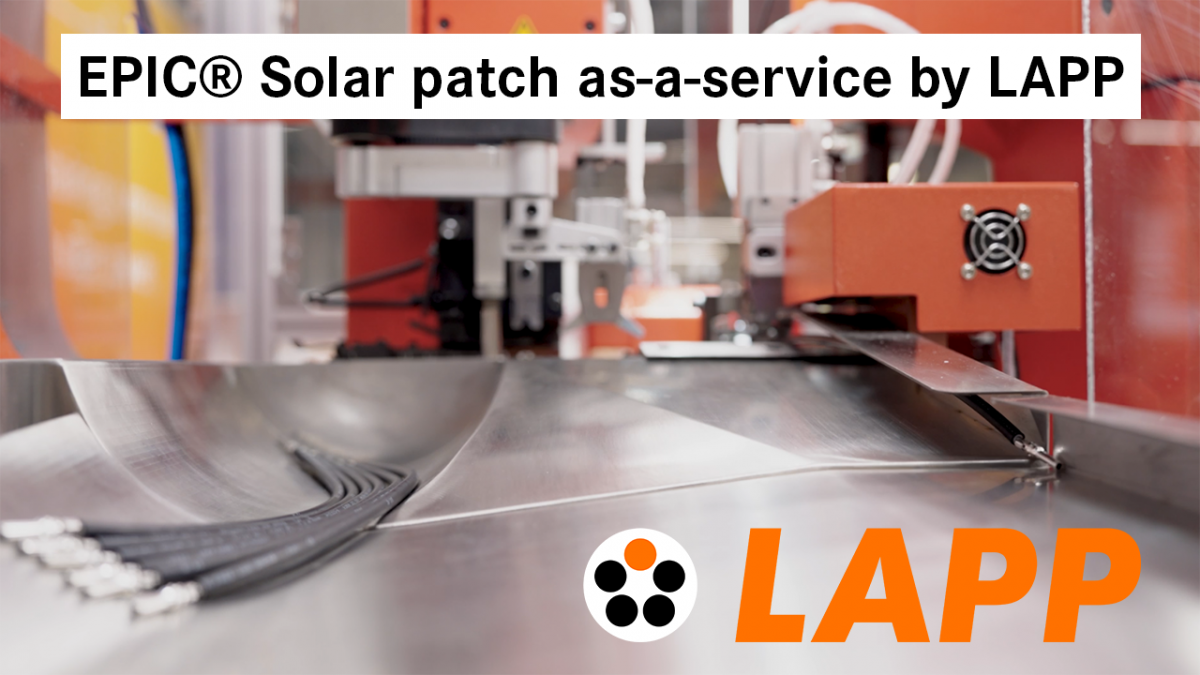