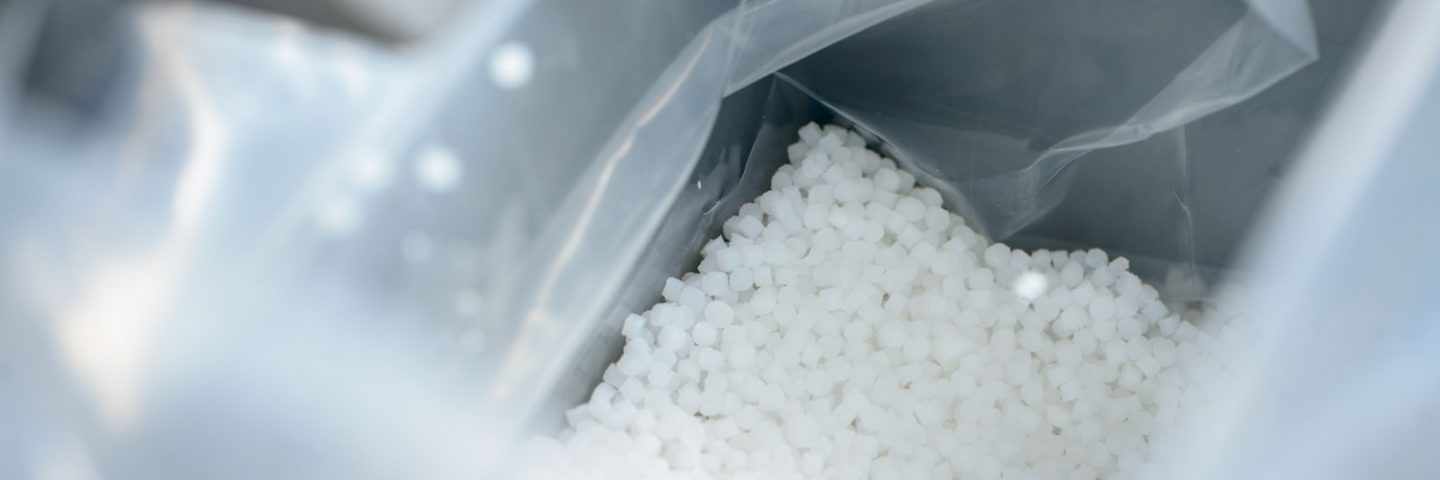
A great deal of expertise is required for the in-house production and development of plastic mixtures and compounds. This is because the art of engineering in cable production lies not only in how the cable is constructed, shielded or stranded, but also in its sheathing. However, not all plastic sheaths are the same; they differ significantly in terms of properties such as flame resistance, tensile strength and heat resistance. For many applications, new special compounds, i.e. plastic mixtures, have to be developed that have exactly the properties that are required.
But to develop a new compound for a cable sheath, you can’t just mix two materials together. “Compounds are very complex products,” explains Pascal Wolfer, a materials scientist with a PhD from Swiss company Lapp Engineering AG, who is responsible for compound development together with two other colleagues. “They contain up to 20 individual components. For a customer-specific requirement, we usually test between six and ten formulations per development loop.” When a customer approaches LAPP with a requirement, a team of experts at LAPP develops various formulations based on the specifications of the application.
The iterative process comprises several steps, from analysing the specifications and formulation to trial extrusion and the subsequent production of a cable prototype. The development loop is usually carried out several times until all requirements for the compound have been met. “We need around two to six months per loop,” says Wolfer. He is also a member of the LAPP team of experts, which is made up of colleagues from Germany, Switzerland, India and Korea and is intensively involved in compound development and production. The aim is to increase LAPP’s competitiveness.
Did you know?
In materials science, the term “compound” refers to a combination of two or more substances that have been combined to create a new material with special properties
More independent thanks to a deeper value chain
“The easiest way to increase competitiveness is to go deeper into your own value chain,” explains Matthias Lapp, CEO of the Lapp Group. The solution: the company’s own compounding plant in India. “For a solution provider like us, the step of starting compound production is an obvious one. This way, we are not dependent on suppliers and can also position ourselves as the market leader,” says Lapp, explaining the strategic decision. And it works: With the help of our own production plant, the costs for compounds can be reduced by five to twenty per cent compared to purchasing from external suppliers. This in turn also pays off for LAPP customers.
Local-for-local production in India
But why India in particular as a location for compound production? There are several reasons for this: Around 50 % of the products currently produced at the LAPP plants in Bhopal and Bangalore are customised for the Indian market and meet local standards, particularly with regard to the local price structure and technical features. “The requirements for cables and plastics are very high in India, so the main focus here is on solutions for very specific requirements, for example for Indian rail transport,” explains Matthias Lapp.
Accordingly, this also requires plastics that fulfil certain requirements, but the number of suppliers in this area is small. They would have to be transported from the manufacturers to India and through the customs of the individual Asian countries. The consequence: dependence on suppliers and long transport routes with considerable CO2 emissions. “That’s why we decided to set up our own compounding plant, which we can use to develop and produce materials in India and for India,” says Matthias Lapp, adding “And this has another decisive advantage: we can now determine exactly how the plastics should be composed and decide on the customised mixtures for our products ourselves.” The raw materials for the compounds are preferably purchased in India. The Indian subsidiary commissions the formulations from its Swiss colleagues at Lapp Enginnering AG. Once the experts in Switzerland have successfully completed the iterative process, customised production begins at the Indian plant.

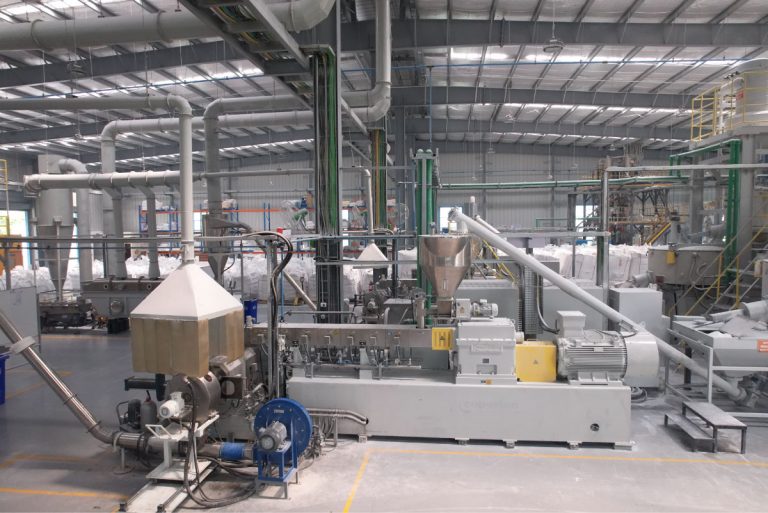
India is booming
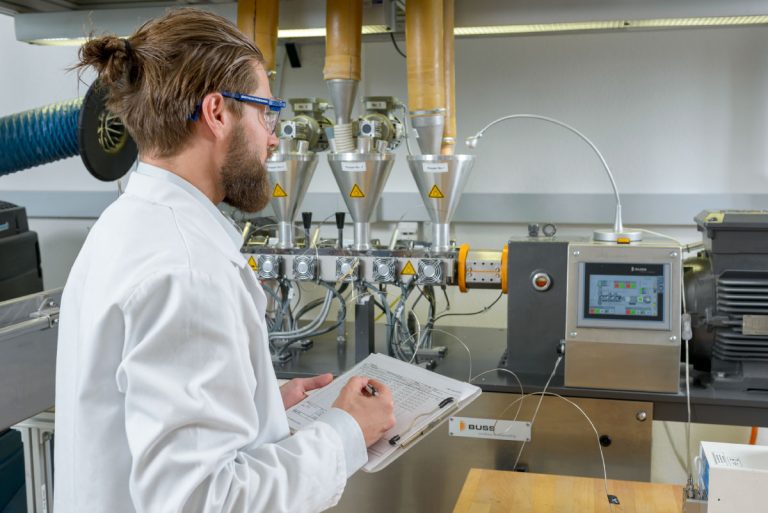
But that is not the only reason for LAPP’s decision to locate here. The leading provider of integrated solutions and branded products in the field of cable and connection technology has been present on the Indian market since 1998. While other companies focussed exclusively on China for many years, LAPP established close relations with what is now the world’s most populous country at an early stage – and was absolutely right to do so. Not only does India have one of the largest and fastest growing populations in the world, but the Indian economy has also experienced steady growth in recent decades. Accordingly, the country has a large number of well-trained specialists and talented people, an ever-improving infrastructure and a growing middle class. While new market players in India still have to contend with barriers to market entry, LAPP is already established here and has literally grown with India’s development. “The decisive factor here was our patient approach to the country and its culture,” says Matthias Lapp. “India works differently to Germany and Europe. We recognised the pace at which business develops here and got involved. That has definitely contributed to our success.” Accordingly, LAPP intends to further expand its strong position in India and is investing heavily in the region and the Indian market as part of its corporate strategy.
Accordingly, the new production facility in Bhopal covers an area of 36,000 square metres. Equipped with the latest technologies, including an automated dosing system, large-scale production can be realised here. “We are proud of our team in India and their commitment to innovation at LAPP,” said Matthias Lapp at the inauguration of the plant in spring 2024, praising the joint efforts of the national company’s employees.
PVC and special compounds from our own production
The plant focuses on the plastic polyvinyl chloride, or PVC for short, which is frequently used for cable insulation and sheathing. PVC is an excellent insulator for electrical cables and protects against short circuits and electric shocks. It can also withstand high temperatures and is resistant to many chemicals, oils and solvents. As a naturally flame-retardant plastic, the particularly durable PVC reduces the risk of cable fires. It is therefore often the first choice for customers in the mechanical engineering and industrial sectors. Two of the three production lines in the newly opened plant are therefore also designed for this popular plastic.
In addition, LAPP’s Indian colleagues produce special compounds for customised solutions on a third production line at the site. This results in innovative compounds with unique properties for a wide range of applications, enabling LAPP to stay one step ahead of the competition while quickly meeting new market requirements or standards. This is particularly important for customers who have to fulfil high legal or regulatory requirements from industries with strict safety and quality standards, such as aerospace or medical technology. For LAPP itself, this means above all being able to offer consistently high product quality and ensure efficient utilisation of raw materials – without being dependent on the quality of an external supplier. Around 13,000 tonnes of plastic per year currently roll off the production line at the in-house production facility. Capacity is set to increase gradually over the coming years.
“All of this works above all thanks to the great cooperation between the LAPP national companies and the colleagues who are dedicated to this project,” emphasises Pascal Wolfer, for whom compound development and production at LAPP has become a matter close to his heart. There is a close dialogue between all those involved. Pascal Wolfer has already travelled to the Indian production plant several times, and an Indian colleague visits the Swiss development team in return. Lapp Engineering AG works closely with its Indian colleagues not only in the development of formulations, but also in the evaluation of compounding equipment and the optimisation of manufacturing processes.