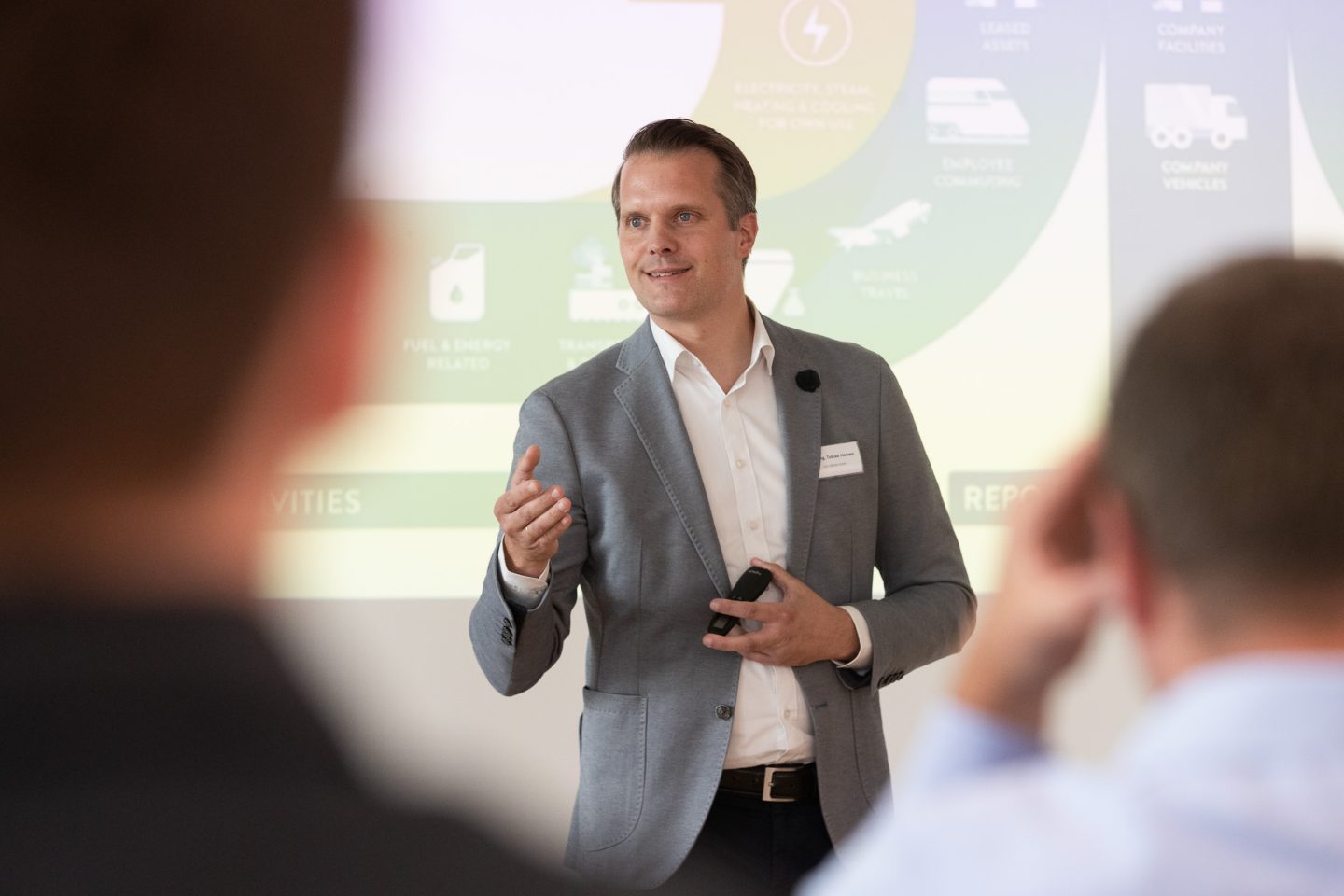
On 18 July, Heinen spoke at LAPP’s European headquarters as part of the “Cross-Industry Innovation Workshop” and gave initial insights into his expertise on the topic of “sustainable production”. The event was initiated by LAPP in order to exchange ideas with representatives of various industrial companies in Baden-Württemberg and to jointly develop sustainable solutions for the future of the industrial sector. This is a sensible and innovative approach, says Heinen, because the issue of sustainability can only be tackled successfully across company boundaries. Often the idea is to network across companies in order to be more effective together. However, implementation is rarely done, even though it is so important.
After all, a company alone cannot manage to reduce its CO2 footprint in such a way that climate neutrality prevails. This is because emissions are made up of several components, not all of which a company can influence.
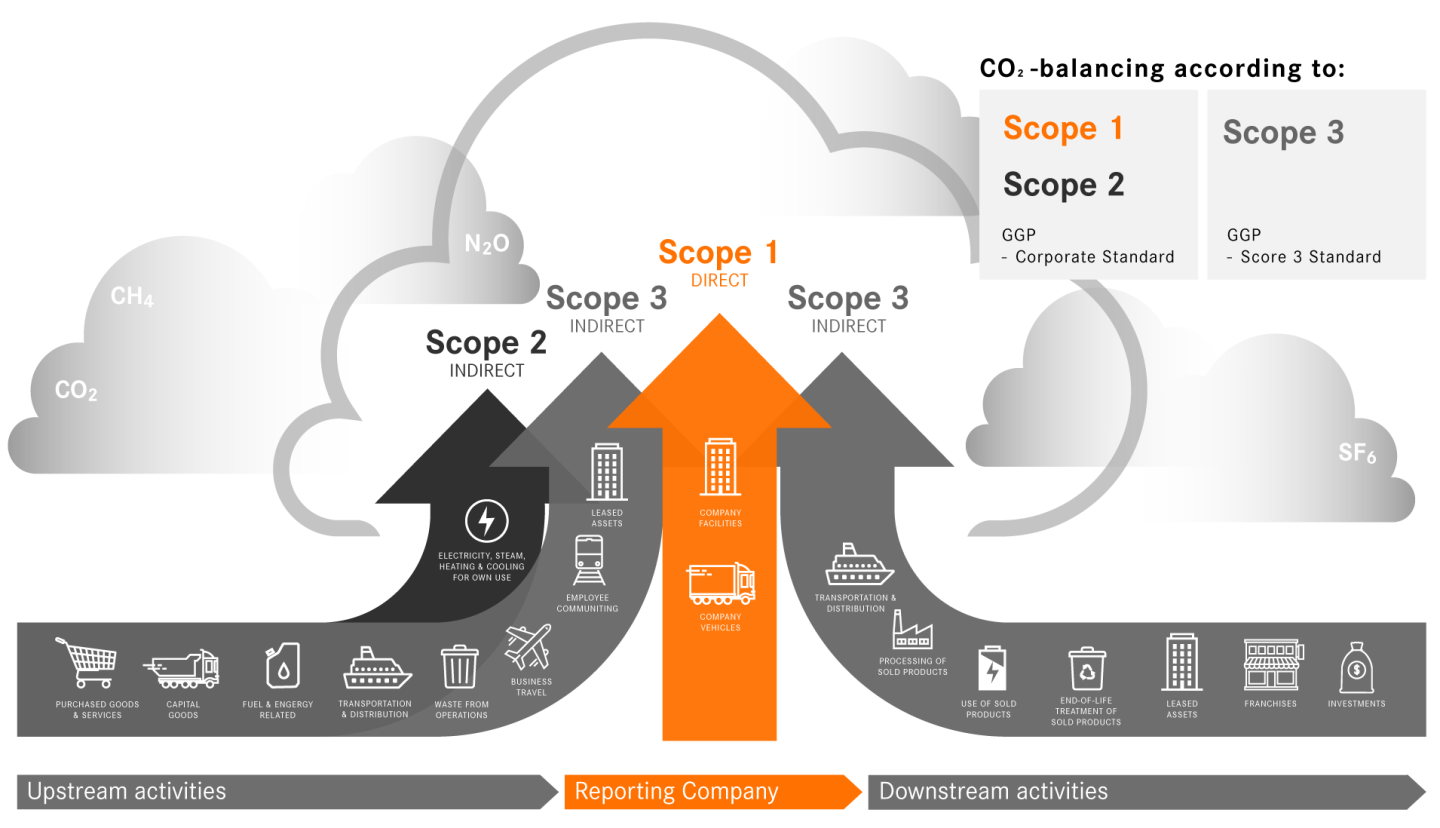
The Greenhouse Gas Protocol (GHG), a proven standard for climate accounting, identifies so-called “gate-to-gate” emissions, i.e. those that occur from the receipt to the dispatch of goods within a company. In addition to these direct emissions (Scope 1), for example from company-owned equipment and vehicles, the GHG also specifies the indirect emissions (Scope 2) caused by external energy supply. These can be controlled and reduced independently. Outside a company’s own sphere of influence, however, there are also the other indirect emissions (Scope 3), which can be found, for example, in the supply and distribution chain.These can only be effectively reduced if the companies that are part of the supply chain work together on a solution – such as the participants in the workshop at LAPP.
According to Heinen, it is particularly difficult for manufacturing companies like LAPP to reduce their carbon footprint because a large proportion of their emissions are generated upstream, where they have no control. “This becomes relatively clear when you consider that these companies process metals or plastics. These purchased raw materials contain an enormous amount of emissions that were generated during the original production of the material”, says the industrial engineer.
His expert solution? First of all, sweep up as much as possible on your own doorstep. In concrete terms, this means drastically reducing emissions that are within our control. “If everyone does their homework in their own factory first, we will be better off overall,” says the expert.
The first step is to optimise existing processes to operate more efficiently within the existing system. For example, Heinen recommends using less energy or water, or optimising the use of material to reduce waste. Companies could also start by optimising their lighting, compressed air, motors or ventilation technology. This is followed by the second and much more challenging step of transformation: “This is where we really have to rethink and try to completely redefine processes. This is an enormous challenge”. Nevertheless, Heinen is calling for the transformation step to be taken without delay, because he sees the lucrative business of the future in precisely those solutions that help to drastically mitigate the challenge of climate change. For example, he says, you could make your own factory carbon neutral, so that instead of consuming energy, it actually produces energy that can be used elsewhere or sold. “Taken together, these challenges are worth the effort,” he says. There is not even the need to reinvent the wheel for a successful transformation: Heinen points out that many best-practice examples are based on existing technology, such as heat pumps. All that is needed now is to take the step of applying them consistently.
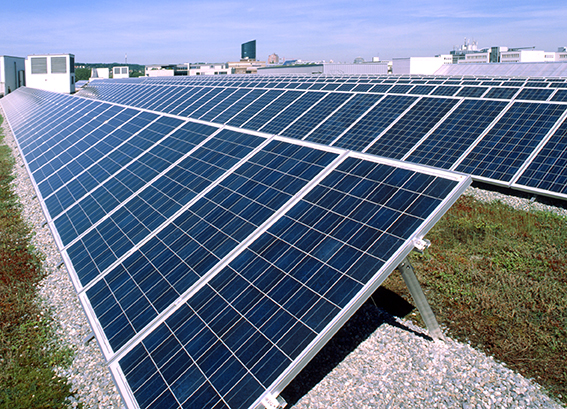
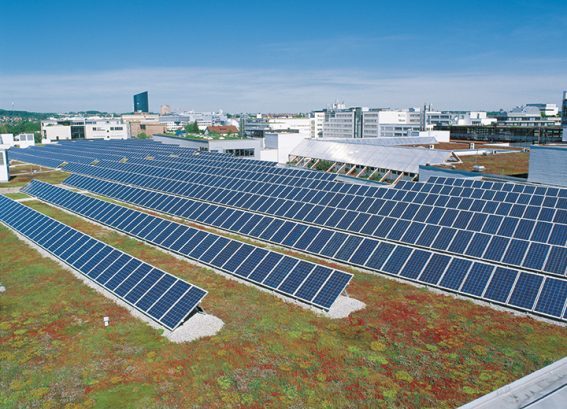
LAPP is taking this step with several sustainability projects – and has been doing so for many years. In 2005, the company put into operation the first of four photovoltaic systems. In 2022, the two PV systems at the Stuttgart site and the two at the Ludwigsburg site generated almost 2 million kWh of electricity – enough to use on site and to feed into the grid. Based on the positive experience over the years, further PV systems are planned. In addition to this power generation solution, LAPP is also using sustainable solutions for heating and cooling. Geothermal energy, thus the heat stored in the earth’s crust that is accessible to us and extracted from the subsoil by means of a heat pump, is used by LAPP, for example, to cool buildings. At the Stuttgart cable factory, waste heat from compressors is used to heat drinking water and the building.
Heinen identifies the main barriers to implementing these and other sustainability measures in companies as being the costs involved and the fear of technical risks. His appeal to companies? “We must accept the need for sustainable production methods and implement them consistently. It is time to think differently and tackle the challenges of climate change now!”. Fortunately, Heinen believes that this rethink has already taken place among the next generation. The students in his class already have a deeper understanding of sustainability and environmental protection than the majority of today’s business leaders. In his view, this could help make sustainability the next evolutionary step in industrial production after digitalisation (Industry 4.0). A kind of “Industry 5.0” where sustainability is seen as the “new normal” in production. This approach shows that the goal of carbon neutrality is not a distant utopia, but a vision that can be achieved with optimism, commitment and inter-company cooperation for the sake of the environment and future generations. So why not start reducing emissions today?