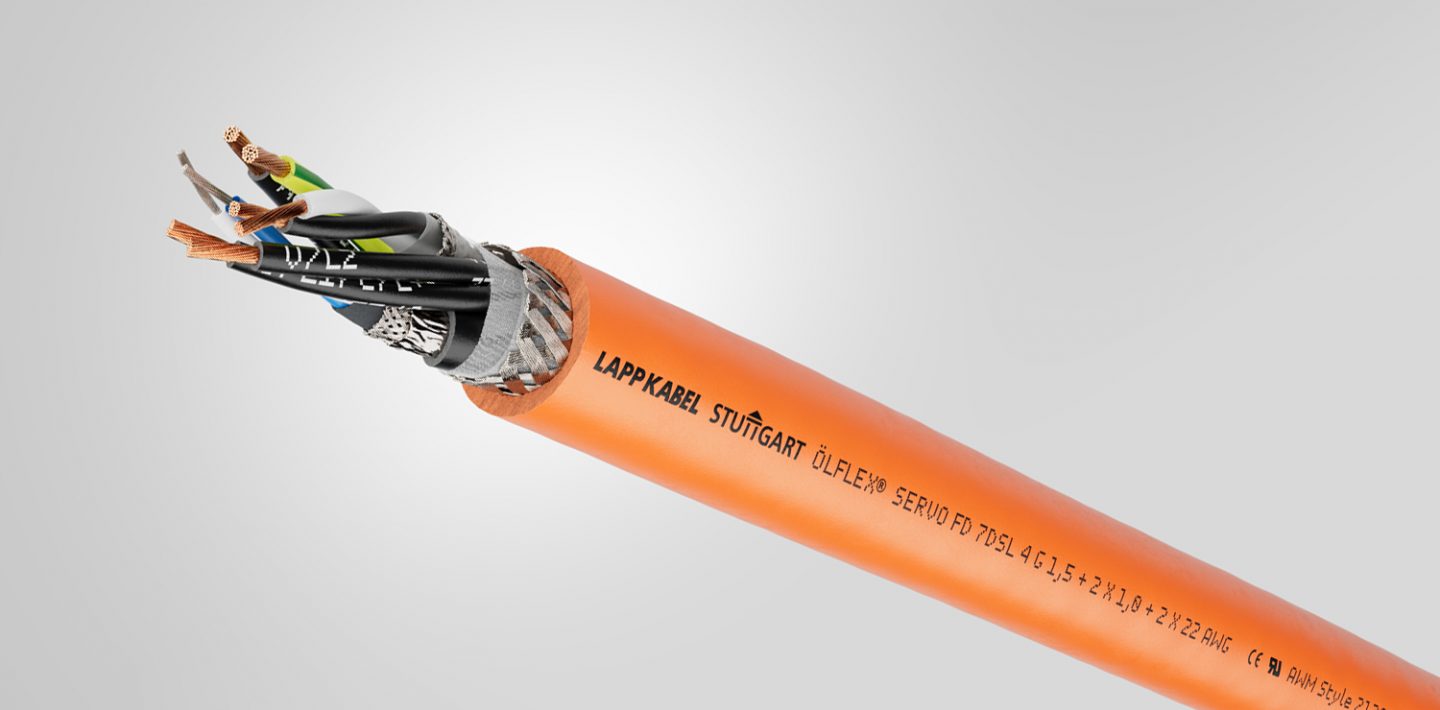
The LAPP catalogue currently contains over 40,000 items, and the range continues to grow. A large part of the portfolio is made up of cables that transmit electrical energy, switching signals or data. With such a wide range of products, there is something for every customer requirement, no matter how unusual – or so you would think. In fact, the product managers at the world market leader for integrated solutions in the field of cable and connection technology receive several enquiries every day from customers who cannot find what they are looking for in the catalogue. There can be various reasons for this. Perhaps the customer needs technical properties that do not yet exist in this combination, or wants to supply their product to a region or industry where special standards apply for which the catalogue does not contain a certified product.
When such requests come in, LAPP’s product management team springs into action. It evaluates product ideas from customers or market or industry requirements and uses this to develop a product requirement that, among other things, defines the structure and, above all, the functionality of the cable. To do this, LAPP engineers use their experience from more than six decades of cable design and thousands of customer projects, but also information from various databases on materials and standards. Each new design is subject to a risk assessment that determines the parameters within which the product can be operated safely. Then product samples are manufactured, tested (internally) and a possible product certification is carried out. After successful testing and certification, the product is released for production.
This process usually takes six months, but can take significantly longer if the product development team has to break new technical ground or extensive testing and certification is necessary.
Standards require redesign
In about half of all customer enquiries, standards and specifications are the reason for developing a new cable design. In addition to global or continental standards such as IEC, EN and UL, there are numerous binding specifications that only apply in one country or market. For example, India has its own standard for photovoltaic cables, which is based on IEC but has a few special features. It prescribes a different type of printing and special tests. Another example: in the industrial environment, products are defined by industry standards that emerge through new technologies. These include, in particular, the servo and motor cable segment, but also the Ethernet technology segment with solutions for Single Pair Ethernet. In addition, LAPP maintains production facilities worldwide and is therefore close to its customers and markets. Special cables are manufactured where they are needed, which avoids long delivery times and is ecologically and economically more sustainable.
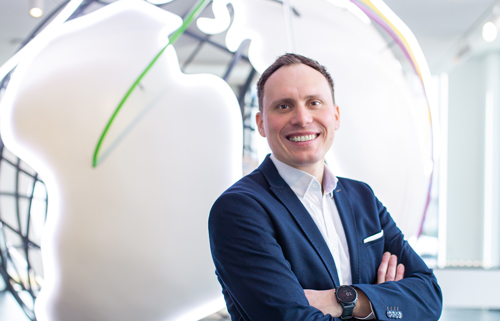
To keep track of all the norms and standards, LAPP has set up a standards office in Stuttgart. It deals with the relevant norms, standards and specifications worldwide and maintains a comprehensive database of all requirements. At the same time, LAPP is involved in standardisation committees worldwide to promote practical solutions. Its experience is highly valued there.
‘Not everything is described in normative terms, and we have a certain amount of freedom that we use in cable design, also in the interest of the customer,’ says Alexander Terpe, Head of Product Development Cables. In doing so, the team always carries out a risk assessment – “because every product must be safe,” says Terpe.
Conflicting requirements
This is important, for example, when customers define specifications that are so challenging that they cannot be met by a standard cable. This is because certain properties can contradict each other. For example, a highly flame-retardant cable usually has a jacket with a high proportion of additives. However, such materials are not as mechanically robust, which means that this cable is not suitable for the millions of movements in a drag chain. In this case, the developers can find a compromise, for example by recommending a larger bending radius, which reduces the stress on the material in the drag chain. Or the customer has to make sure that the cable does not come into contact with certain chemicals under any circumstances, because that would also reduce the durability of the flame-retardant plastic compound.
‘If we slim down the requirements for a cable, this is entered in the data sheet and it is considered a new product,’ says Terpe. This does not mean that a completely new design is always necessary. Similar designs can fulfil different functions and requirements by using different compounds.
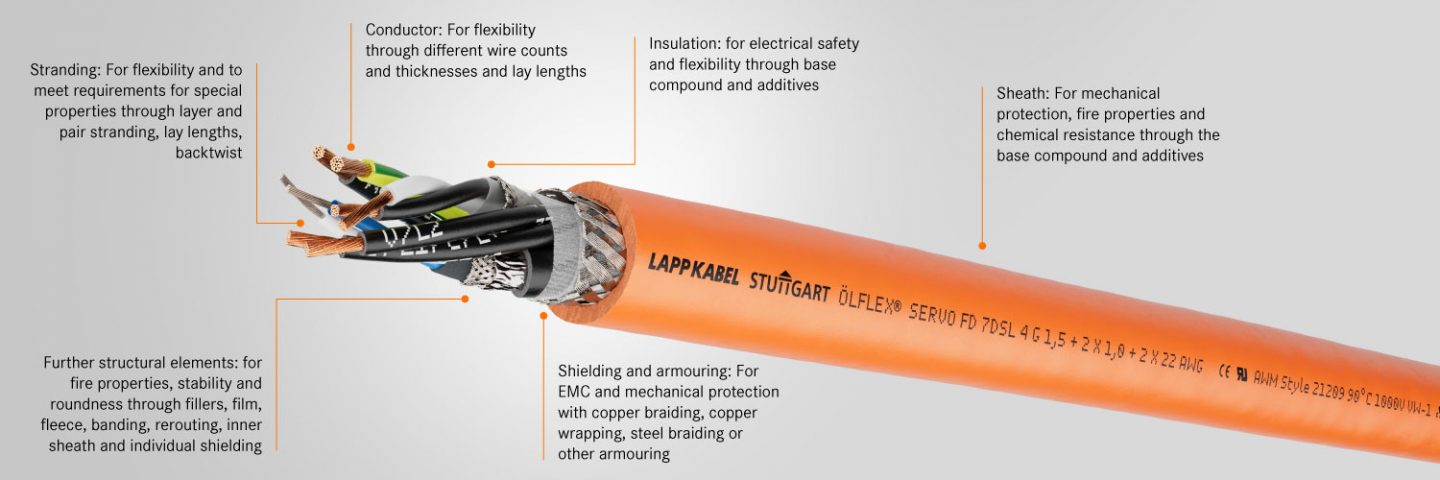
Special cables with additional functions
If a customer needs a cable that is not similar to any standard cable, Falk Ritzau’s team comes into play. Six employees design special cables according to specific customer requirements. This often involves hybrid cables with additional functions. These are cables that contain hoses for hydraulics or pneumatics in addition to electrical conductors. LAPP produces such hybrid cables for oil drilling platforms, for example. But even a purely electrical cable can be a special cable. A request from a fish farm in Norway was a real exotic. To keep salmon lice away, which are harmful to farmed salmon, LAPP developed a cable that generates electrical fields in the water, a kind of electromagnetic cage against the parasites. The engineering achievement here lies not only in the cable design, but also in the interpretation of the correct operating parameters.
LAPP also supplies customised cables in small quantities. If customers only need a few hundred metres of a cable, they don’t have to have a whole bunch of drums gathering dust in their warehouse.
Cable design with AI?
‘Without laboratory tests, it won’t work in the future either,’ says Alexander Terpe. Nevertheless, cable development is becoming more and more data-driven. LAPP, for example, has a material database in which several hundred plastic compounds are described. New ones are constantly being added, while others are being dropped, for example because certain ingredients are no longer allowed under new regulations. New compounds take account of the trend towards greater sustainability. LAPP, for example, recently presented the first cables with partially bio-based sheathing materials.
This raises the question of the extent to which artificial intelligence can support cable design. The data is still too inhomogeneous, but that will change. ‘I can imagine that in a few years we will be designing cables with AI support,’ says Terpe. This would have a major advantage: ‘LAPP’s expertise is in the minds of our excellent employees. AI could help to make that expertise more readily available within the company.’