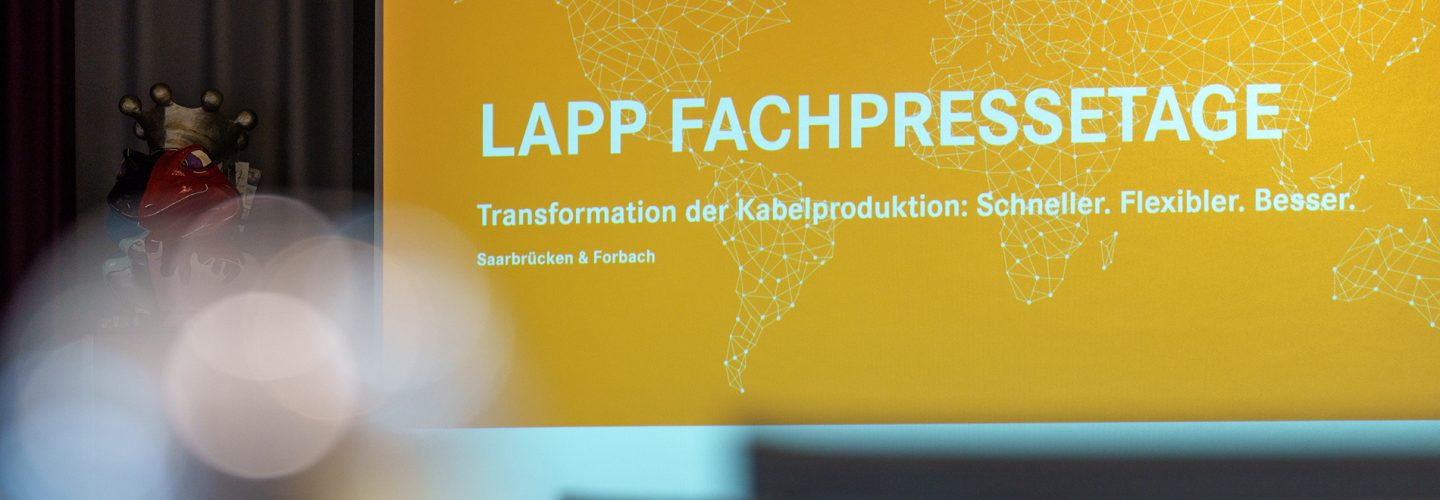
„Wir müssen den Erfindergeist meines Großvaters Oskar Lapp neu interpretieren. Die Bedürfnisse unserer Kunden haben sich stark gewandelt. Sie erwarten heute Mehrwerte, wenn sie Kaufentscheidungen treffen. Daher wollen wir das kundenorientierteste Unternehmen in unserer Branche sein“, fasste Matthias Lapp, Vorstandsvorsitzender der Lapp Holding SE die Strategie von LAPP zusammen. Gleichzeitig will das Unternehmen auch Technologietreiber bei Produkten und Dienstleistungen sein.
Im Fokus der Innovationsbemühungen steht die Spezialisierung auf ausgewählte Wachstumsbranchen wie Erneuerbare Energien, Intralogistik, Automatisierungstechnologie, Food & Beverage aber auch die Elektromobilität. Bereits heute steigt die Nachfrage nach Kabeln in diesen Bereichen enorm. Für LAPP bieten sich dadurch große Chancen, aber auch die Herausforderungen in der Produktion wachsen.
Produktionsnetzwerk wird optimiert
„Die Losgrößen werden immer kleiner, die Varianten vielfältiger, gleichzeitig wächst der Anspruch bei Material und Prozessen so nachhaltig wie möglich zu wirtschaften“, erklärt Hubertus Breier, Vorstand für Technik und Innovation der Lapp Holding SE. Daher arbeitet LAPP aktuell daran, das weltweite Produktionsnetzwerk zu optimieren, um Effizienz, Lieferfähigkeit und Flexibilität deutlich zu steigern. Kontinuierlich wird in allen Produktionswerken die Maschinenauslastung überprüft und die Kenngrößen wie beispielsweise die Overall Equipment Effectiveness (OEE) gemessen. Gleichzeitig versucht LAPP beim Materialeinsatz nachhaltiger zu wirtschaften. Es ist eine einfache Rechnung: wenn die Isolierung eines 10 Millimeter dicken Kabels bei einer Extrusionsgeschwindigkeit von 100 Metern pro Minute 10 Mikrometer dünner würde, könnte pro Stunde über eine Tonne Kunststoff eingespart werden. Denn ein Kabel hält heute in vielen Anwendungen oft länger als die Maschinen, in denen es eingesetzt wird.
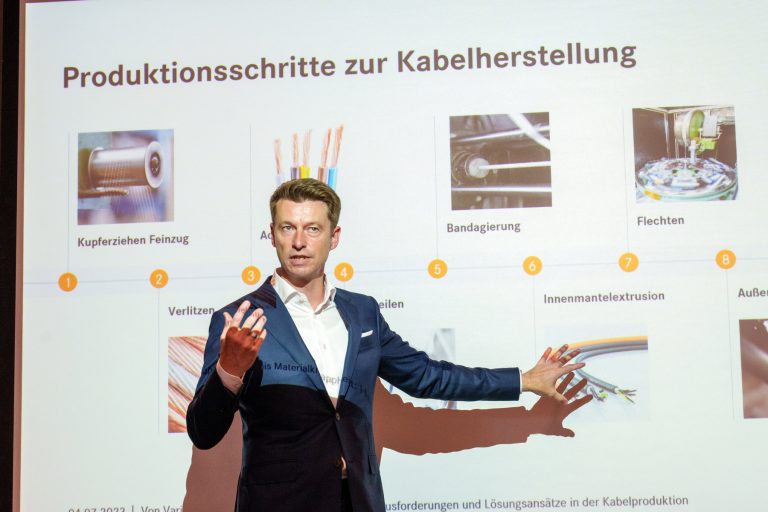
LAPP hat drei wichtige Handlungsschwerpunkte definiert:
- Die Digitalisierung in der Produktion, damit das Portfolio in der gesamten Supply Chain besser geplant werden kann. Ziel ist die komplette Transparenz des Planungsprozesses.
- Dekarbonisierung in der Produktion in Richtung eines niedrigeren Umsatzes von Kupfer, das im Durchschnitt für 88 Prozent des CO2-Fussabdrucks in den Produkten von LAPP verantwortlich ist.
- Diversifizierung: Ziel ist es, in allen Regionen möglichst unabhängig von einzelnen Lieferant:innen zu werden.
Hubertus Breier: „Allein kontinuierlich innovative Ideen am Markt zu präsentieren, garantiert nicht den Erfolg eines Unternehmens. Genauso wichtig ist es, diese Innovationen auch erfolgreich in den Produktionsprozess zu integrieren. Alles muss perfekt abgestimmt wie in einem Uhrwerk funktionieren. Das ist unsere tägliche Herausforderung.“
In Forbach wird die Produktion verdreifacht
Wie die Transformation der Kabelproduktion gelingt, hat LAPP bereits in der Câbleries Lapp SARL im französischen Forbach vorgemacht. Mit einem Strauß an smarten Veränderungen sollen dort die Produktionskapazitäten bis 2027 verdreifacht werden. Um dieses Ziel zu erreichen, hat das französische Team ein ganzes Bündel an Maßnahmen angestoßen oder bereits umgesetzt. So wird ein zusätzliches Produktionsgebäude errichtet, sodass sich die Produktionsfläche ab 2024 auf 28.000 m2 erhöhen wird. Ein wichtiger Baustein ist der Einsatz von neuen, flexibleren Maschinen. So wurde in Forbach in eine neue, fünfte Mantelstraße investiert. Mit ihr verkürzt sich der Rohstoffwechsel beispielsweise von PVC auf PUR von früher drei bis vier Stunden auf nur noch zehn Minuten. Das Besondere daran: Die HELICAL-Extruder benötigen bis zu 25 Prozent weniger Energie, erlauben eine niedrigere Schmelztemperatur und steigern den Ausstoß um bis zu 100 Prozent. „Wir können damit schneller heizen, schneller reinigen, schneller fahren und sparen noch dazu Energie“, fasst Stéphane Kaczmarek, Senior Vice President der LA EMEA Produktionsgesellschaften und Geschäftsführer der Câbleries Lapp SARL die Vorteile zusammen.
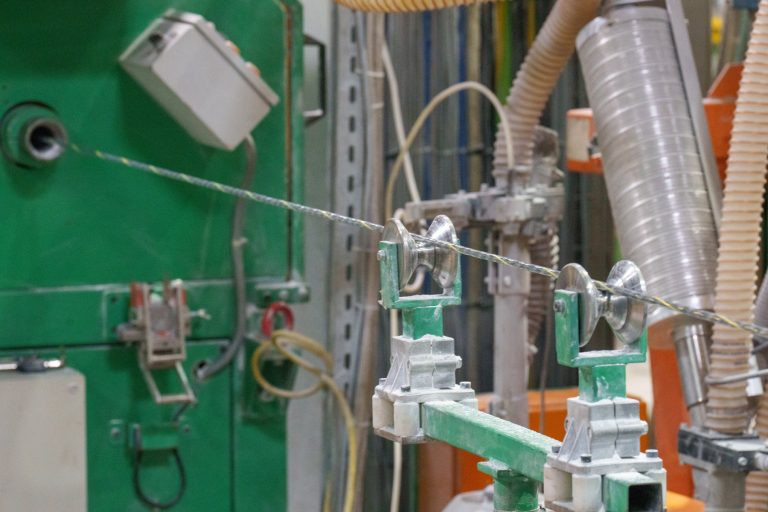
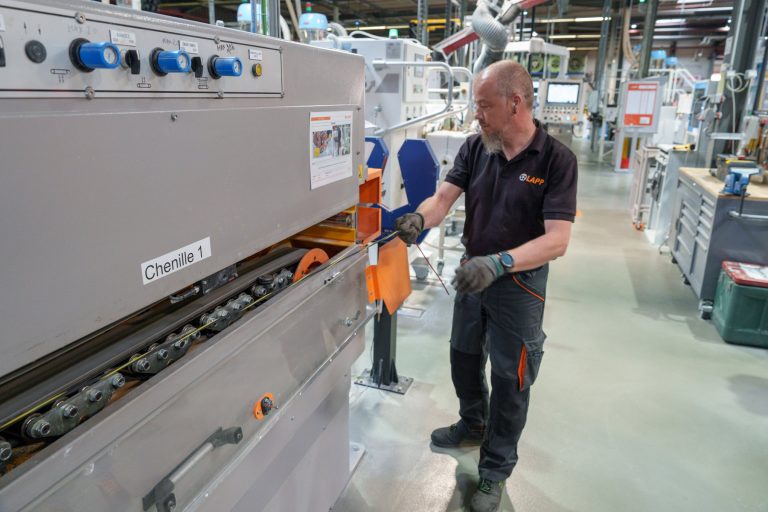
Zukünftig werden auch die vier älteren Mantelstraßen aufgerüstet und optimiert. Eine besonders kreative Optimierungsidee hatte das Team bei der Aderstraße. Traditionell ist das Layout einer solchen Produktionslinie in einer Linie aufgebaut. Um die Laufwege zu optimieren, sollte die neue Aderstraße in U-Form aufgebaut werden. Ziel war es, alle Arbeitsstationen der Anlage möglichst nebeneinander zu platzieren. Heute sind die Laufwege für die Mitarbeitenden um 96 Prozent kürzer, die Umrüstzeiten reduzieren sich von 10 auf sechs Minuten und die Maschine kann fast 50 Prozent schneller produzieren.
Um die Mitarbeitenden zusätzlich zu entlasten, werden ab 2024 einfachere Prozesse automatisiert. Statt Trommeln manuell auf Paletten zu laden oder Leerspulen von der Palette auf die Maschine zu hieven, werden künftig Roboter eingesetzt. Auch das Etikettieren werden sie übernehmen. Außerdem werden für den Transport der Rohstoffe an die Maschinen künftig fahrerlose Transportsysteme eingesetzt. Mittelfristig ist die Zentralisierung aller Kunststoffe mit einer automatischen Verteilung an die Extrusionsanlagen geplant. Und an jeder Linie werden außerdem Zerkleinerer zur direkten Wiederverwendung der Kunststoffabfälle installiert.
„Um in einem Hochlohnland wie Frankreich weiterhin erfolgreich zu sein, müssen wir es schaffen, bei gleichem Mitarbeitereinsatz immer effizienter zu werden. Durch die geplanten Maßnahmen werden wir daher mit unserem bestehenden Team dreimal mehr produzieren können. Mit unserer Smart Supply Chain wollen wir der beste, schnellste und flexibelste Hersteller in der Kabelindustrie werden“, unterstreicht Stéphane Kaczmarek.
Neuartiger Aufbau in Teamarbeit
Bei der Optimierung der Produktionslinien arbeitet das Team in Forbach sehr eng mit der französischen Firma Komax S.A.S. zusammen, einem global tätigen Technologieunternehmen, das sich auf Automatisierung und Extrusion konzentriert. Komax bereits zwei komplette Produktionslinien nach Forbach geliefert. Bei der ersten Produktionslinie handelte es sich um eine Mantelstraße, die nach Vorgaben von LAPP nicht in einer Linie, sondern in U-Form aufgebaut werden sollte. „Ziel war es, die Arbeit des Linienbetreibers so effizient wie möglich zu gestalten, indem die Bewegungen der Mitarbeitenden zwischen den Maschinen an der Produktionsline auf ein Minimum reduziert werden. Den neuartigen Aufbau haben wir gemeinsam mit dem LAPP Team erarbeitet, um die Bewegungsabläufe an der Linie so effizient und leistungsfähig wie möglich zu gestalten“, sagt Laurent Musitelli, Geschäftsführer von Komax. Dabei wurden jeder einzelne Arbeitsschritt und jeder Handgriff unter die Lupe genommen. Beispielsweise jedes Bedienpult so positioniert und optimiert, um möglichst schnell neue Produktionsprozesse einzurichten.
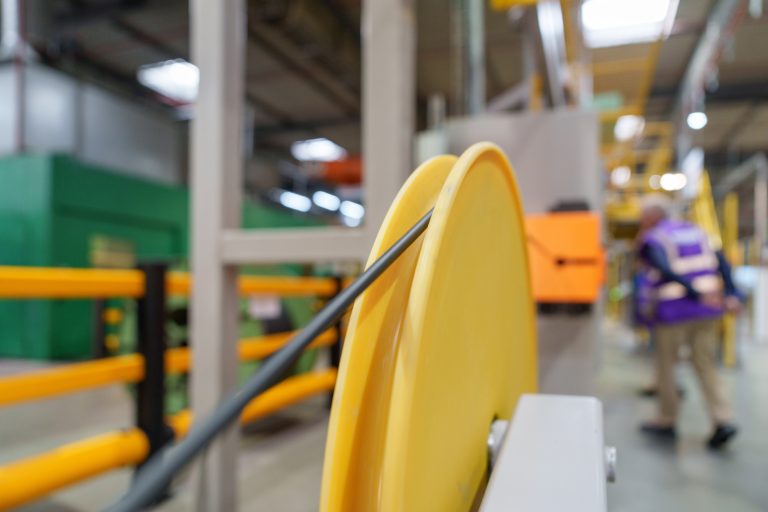
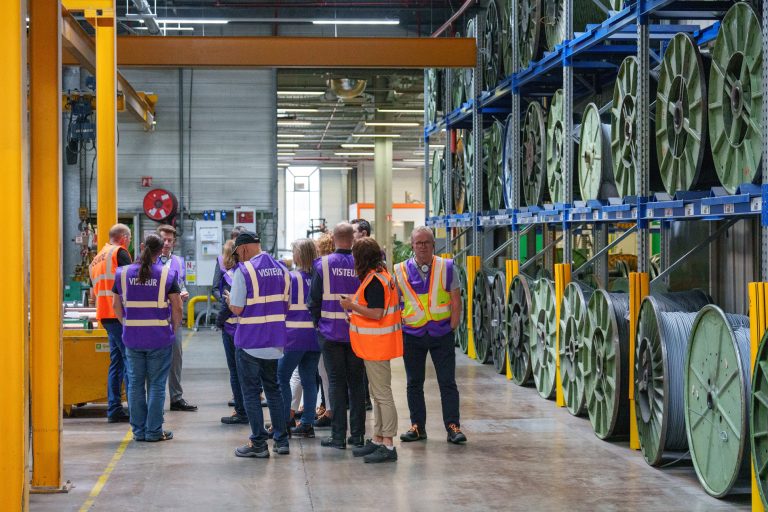
2022 hat Komax eine zweite sogenannte Fillerlinie geliefert. Das Besondere daran: Diese Filler werden aus recyceltem PVC-Kabelschrott hergestellt. Ein wichtiger Ansatzpunkt für mehr Nachhaltigkeit.
Eine dritte Produktionslinie von Komax wird in diesen Tagen in Forbach angeliefert. Sie übernimmt die Isolierung der einzelnen Kupferadern. Auch sie wird optimiert aufgebaut, um die Rüstzeiten um mehr als 90 Prozent zu reduzieren. Künftig wird innerhalb von Sekunden umgestellt werden können. Laurent Musitelli: „Nur durch enge Zusammenarbeit sind solche Verbesserungen möglich. Fortschritt ist immer möglich und durch langfristige Zusammenarbeit wird das Unmögliche möglich.“
Nährboden für neue Ideen
Aber auch beim Thema Gleichstrom geht LAPP in Forbach mit gutem Beispiel voran: Bei der Errichtung der neuen Produktionshalle sollen einige Verbraucher mit dem gewonnenen Gleichstrom aus der Photovoltaikanlage auf dem Dach in einem reinen DC-Netz mit weniger Wandlern und einer höheren Effizienz versorgt werden. Damit positioniert sich LAPP auch beim Gleichstrom als Technologietreiber. Matthias Lapp: „Technologie betrifft uns alle und muss von der Breite der Mitarbeitenden vorangetrieben werden. Die interdisziplinäre Zusammenarbeit ist ein Nährboden für neue Ideen.“