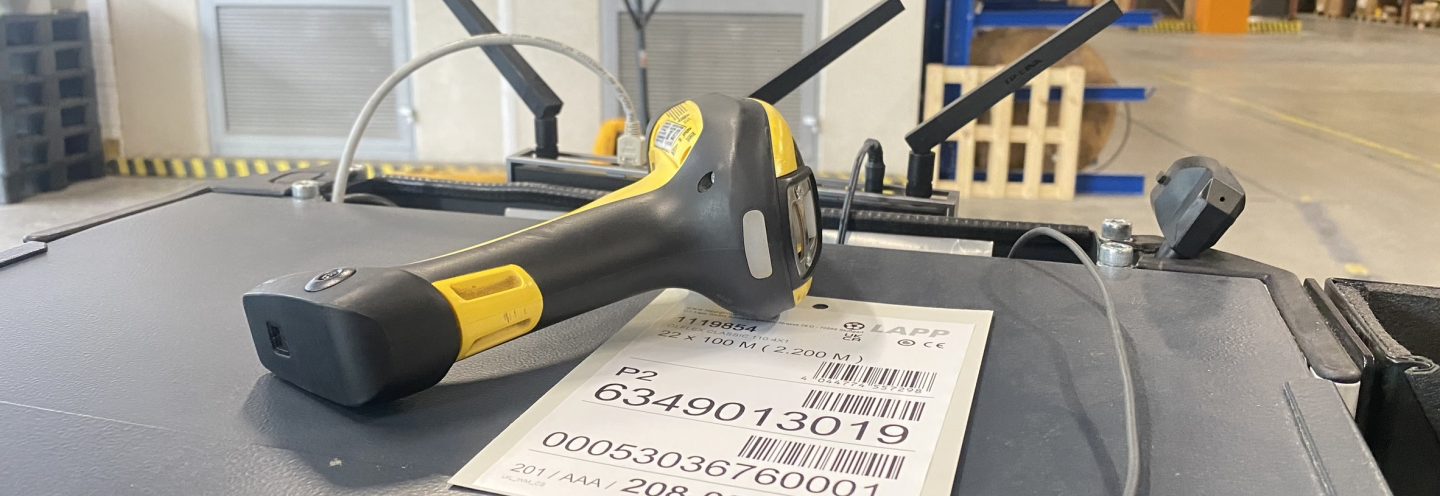
Logistik erinnert manchmal an das Kultspiel Tetris. Kontinuierlich kommen neue Bausteine – in diesem Fall Pakete oder ganze Paletten hinzu, und müssen schnell an die richtige Stelle bewegt werden. Werden Fehler gemacht, gibt es Chaos. So auch in der Logistik. Doch so zweidimensional übersichtlich wie im Spiel sind die Prozesse in der Realität nicht. Sie sind komplexer und umfangreicher. Nimmt man zum Beispiel die Intralogistik von LAPP, dem Stuttgarter Weltmarktführer für integrierte Lösungen im Bereich der Kabel- und Verbindungstechnologie, so findet man drei verschiedene Arbeitsbereiche: den Wareneingang, die Schneidabwicklung und den Versand. Dazwischen gibt es klare Prozessketten, innerhalb derer die Packstücke bewegt werden. Und diese erfordern eine präzise Koordination.
Um die Pakete und ihren Inhalt jederzeit verfolgen zu können, nutzen Mitarbeitende der LAPP Logistik selbstklebende Etiketten zur Kennzeichnung der Waren. Dazu sind die Logistiker:innen an ihren Arbeitsplätzen mit Druckern ausgestattet. Wenn sie ein Packstück bearbeiten, geben sie die nötigen Daten in den PC ein, drucken das Etikett aus, ziehen es von der Trägerfolie ab und kleben es auf das Paket. Damit kann die Ware jederzeit in der Logistik nachverfolgt werden. So laufen die Prozesse reibungslos ab. „Das System bietet zunächst erstmal viele Vorteile“, erklärt Allen Frederick, Mitarbeiter Logistics Systems and Services bei LAPP, „stellt uns aber vor ein entscheidendes Problem: Es produziert Massen an Sondermüll.“ Und zwar in Form der gelben Trägerfolie, die nach dem Abziehen der Etiketten keinen Nutzen mehr hat und im Müll landet. Bei vier Millionen Etiketten im Jahr kommt da einiges zusammen, weiß Frederick. Auch das Carbonband, das für den Druck benötigt wird, muss regelmäßig getauscht werden. Hier entsteht weiterer Abfall.
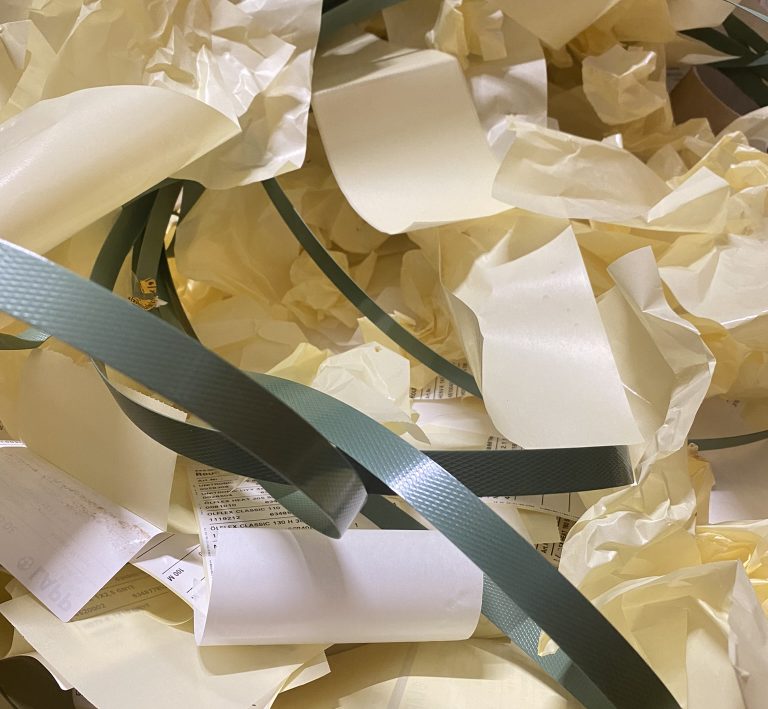
Ein Müllstreifen von Stuttgart bis Lübeck
Das war Allen Frederick schon vor Jahren ein Dorn im Auge. In der LAPP Logistik gehört er zum Team des First-Level-Supports, das sich um Probleme rund um Hard- und Software kümmert – und auch stehts an der Optimierung bestehender Systeme arbeitet. „Angenommen, man nimmt eine Deutschlandkarte zur Hand und zeichnet eine gerade Linie von Stuttgart bis Lübeck – dann hat man die Länge des Streifens an Trägerfolie, die in der Logistik in Stuttgart jährlich an Müll zusammenkommt“. Rund 571 Kilometer. Und der Müllstreifen ist nicht nur lang, sondern auch schwer: 5,5 Tonnen bringt er auf die Waage. Mehr als fünf Kleinwagen. Dabei stören Frederick zwei Probleme: „Erstens ist die Entsorgung teuer. Bei der Masse kommt LAPP auf knapp 1.400 Euro im Jahr“, erklärt Frederick. Zweitens sind sowohl die Entsorgung als auch die Produktion von Trägerfolie und Carbonband eine Belastung für die Umwelt. Allein die Herstellung des Trägermaterials für den Bedarf der LAPP Logistik verursacht fünf Tonnen CO2 im Jahr. Das entspricht der Hälfte des jährlichen CO2-Fußabdrucks pro Kopf in Deutschland.
Die Lösung ohne Träger
„Es muss doch auch andere Etikettiersysteme geben“, dachte Frederick im Jahr 2019. Die Abschaffung von Einwegprodukten im Haushalt oder der Gastronomie ist schon lange ein Thema. Warum nicht auch in der Logistik? Doch die Suche nach Alternativen war schwierig – es gab schlichtweg keine. Frederick gab sich mit der Situation nicht zufrieden und blieb dran. Im Februar 2021 schien dann plötzlich des Rätsels Lösung gefunden zu sein: „Linerless Labels“ – also trägerlose Etiketten von Zebra Technologies. Diese kommen ohne die silikonbeschichtete Trägerfolie aus, denn sie tragen sich selbst. Es handelt sich dabei nicht um einzeln vorgefertigte Etiketten, sondern um ein aufgerolltes Etikettenband, mit der Klebefläche auf der Unterseite und der Druckfläche auf der Oberseite. Da es mit einem Spezialkleber versehen ist, ist das Aufrollen problemlos möglich. Dabei haftet die Klebefläche auf der darunterliegenden Druckfläche. Eine fertige Rolle wird in einen für das Verfahren speziellen Drucker eingesetzt, der die Oberseite ohne Carbonband bedruckt – denn es kommt ein Thermodruckverfahren zum Einsatz. Das jeweilige Etikett wird dank eines integrierten Messers auf die benötigte Länge abgeschnitten. Die fertigen Etiketten lösen sich leicht von der darunterliegenden Fläche ab und hinterlassen keine überschüssige Trägerfolie und auch kein zu entsorgendes Carbonband. Nicht nur der Müll entfällt dadurch komplett. Es stehen sogar mehr Etiketten pro Rolle zur Verfügung – insgesamt 748 Stück, im Gegensatz zu den bisherigen 475.
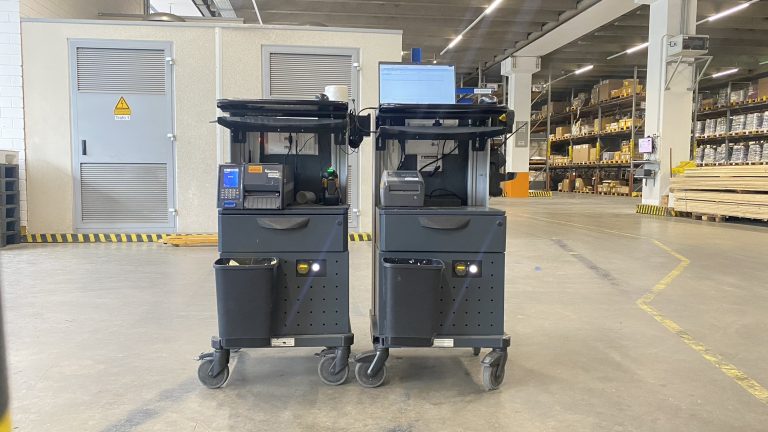
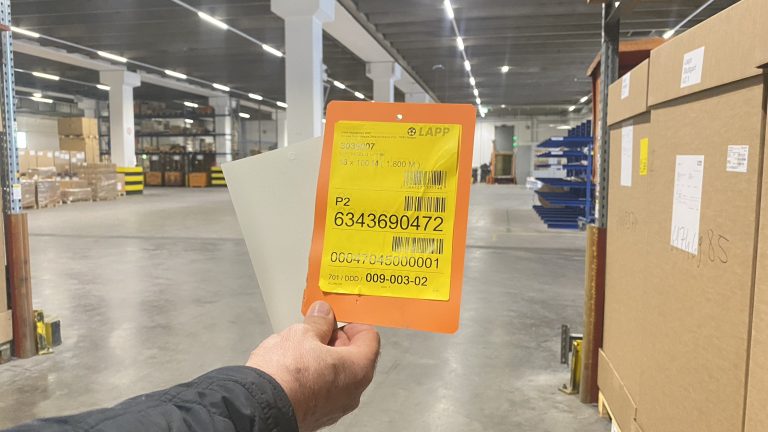
Test auf Herz und Nieren
Frederick war überzeugt und wollte für dieses Verfahren nun einen Testlauf in der Stuttgarter Logistik von LAPP starten. Maria Dobritzsch, Global CSR Managerin bei LAPP, gab nach einem Vorort-Besuch im Stuttgarter Logistikzentrum direkt grünes Licht für den Probelauf. „LAPP arbeitet stets daran, Prozesse nachhaltiger zu gestalten und Ressourcen einzusparen“, erklärt Dobritzsch und ergänzt: „Mitarbeitende spielen dabei eine entscheidende Rolle. Sie kennen die Prozesse sehr gut und können so leicht Optimierungspotenziale identifizieren.“
Anfang 2022 wurden insgesamt drei Stationen für den dreiwöchigen Probelauf umgebaut – im Versand und im Wareneingang. Über mehrere Stunden hinweg wurden die Abläufe beobachtet. „Anfangs hatten wir eine konkrete Herausforderung“, erinnert sich Frederick: „Nämlich der Druck im Eilverfahren.“ Wenn Mitarbeitende beispielsweise 30 Etiketten in einem Durchlauf drucken möchten, war dies mit dem bisherigen Verfahren kein Problem. Man gibt den Druckauftrag mit der entsprechenden Etikettenanzahl ein und dann kommt ein langes Band mit fertigen Etiketten aus dem Drucker, die man nach und nach abziehen kann. Beim Linerless-Verfahren funktioniert das so nicht. Denn das Etikett muss direkt vom Drucker entnommen werden. Man hatte die Befürchtung, dass sich bei solchen Sammeldrucken ein Etikettenknäuel bildet und alles verklebt, so Frederick. Für diese Herausforderung gab es jedoch eine simple Lösung: Ein Sensor im Drucker sorgt dafür, dass der Druckprozess bei großem Druckvolumen so lange pausiert, bis das Etikett abgezogen wird. Also kein klebriges Chaos. Ganz im Gegenteil: Durch den sequenziellen Einzeldruck, gibt es kein Risko mehr, dass Etiketten vertauscht werden, da sie immer direkt angebracht werden müssen.
Kostensenkung auf vielen Ebenen
Doch das ist nicht alles. Viele weitere Vorteile des trägerlosen Etikettierens haben LAPP letztlich überzeugt, das System nach dem Testlauf nun weitläufig zu implementieren. Durch das Verfahren werden Kosten gespart – nicht nur wegen des Wegfalls der Entsorgung. Standarddrucker für das Linerless-Verfahren kosten über die Hälfte weniger als die bisherigen Geräte. Durch weniger Material sinken auch die Transportkosten – und es wird weniger Lagerfläche bei LAPP benötigt. Durch das endlose Etikettenband, das vom Drucker beliebig beschnitten werden kann, müssen keine unterschiedlichen Etikettengrößen mehr beschafft werden. Je nach Kundenspezifikation kann die Etikettengröße beliebig angepasst werden.
Ein weiterer Pluspunkt ist zudem die verbesserte Zeiteffizienz: „Früher mussten wir die Etikettenrollen viel öfter wechseln. Bei dem Linerless-Verfahren hat sich das durch mehr Etiketten pro Rolle deutlich reduziert. Dadurch haben wir weniger Stillstandzeiten“, so Frederick. Durch den Wegfall des Carbonbands spart man beim Wechsel noch zusätzliche Zeit.
Doch nicht nur über die Reduktion von Kosten und Zeit freut sich LAPP, sondern auch die verbesserte Umweltbilanz: „Mit dem trägerlosen Verfahren können wir unseren CO2-Fußabdruck reduzieren. „Solche Maßnahmen sind enorm wichtig für unsere Weiterentwicklung als Unternehmen und die Erreichung unserer Nachhaltigkeitsziele.“ Und auch Allen Frederick ist zufrieden. „Die Mitarbeitenden wollten das System nach dem Testlauf gar nicht wieder hergeben“, lacht er. Auch international ist das Interesse bei LAPP groß. Die Testphase im Logistikzentrum Stuttgart ist bereits erfolgreich abgeschlossen und das System wird dort nun implementiert „Natürlich werfen wir die alten Geräte nicht sofort weg. Wir nutzen sie parallel weiter und ersetzen sie dann sukzessive“, erklärt der Logistikspezialist. Der deutschlandweite Rollout an allen Logistikzentren von LAPP soll bis Ende 2024 abgeschlossen sein.„. Reibungslose Abläufe in der Logistik – ohne Müll, ohne Chaos und mit vielen glücklichen Gesichtern. So wie man es sich wünscht. Und so wie man sich eine gute Runde Tetris vorstellt. Nur eben komplexer.
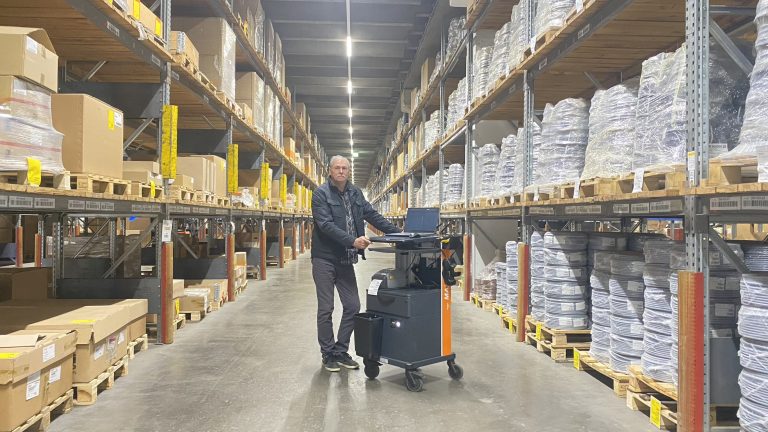