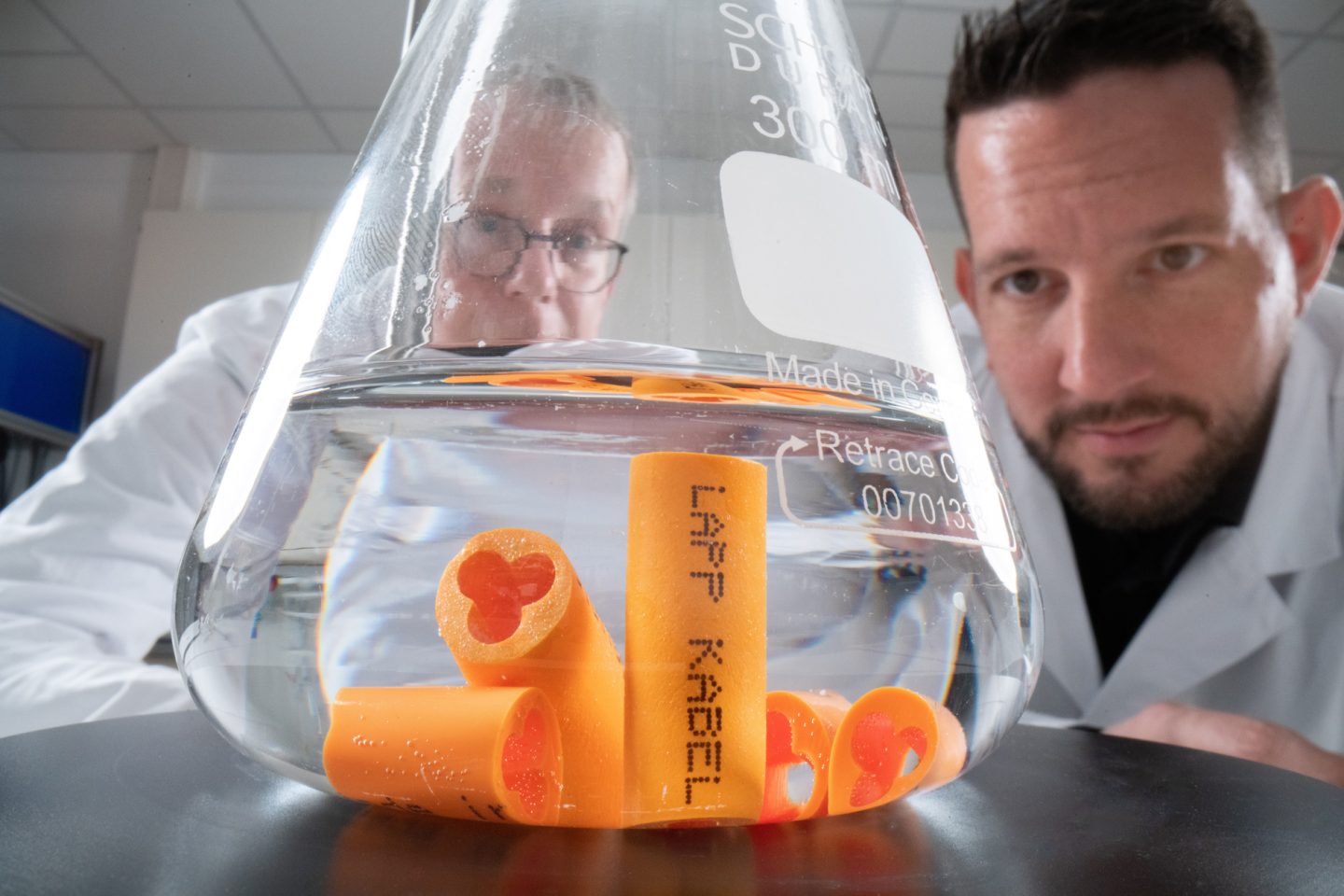
The supplier cannot understand the complaint: “But we tested the component in the test laboratory and everything was fine!” After all, it was the supplier’s pride and joy that he had established a sophisticated quality assurance system in his production in India. But now it turns out: the tensile strength test is invalid – simply because the laboratory employee who was on duty that day could not tolerate the air of the air-conditioning system and therefore switched it off. As a result, the test is carried out at 31°C and 70% relative humidity instead of the specified 23°C and 50% humidity, and gives completely falsified results.
Among the most common reasons for erroneous laboratory test results are unclear environmental conditions, mainly triggered by temperature differences or different humidity levels. To control these variables, standards such as DIN EN ISO 291 define a “standard climate” that prescribes a specific temperature and humidity. VDI/VDE Guideline 2627 additionally specifies the maximum permissible limit deviation for temperature. However, comprehensive air-conditioning of a room, including the control of temperature and humidity, is time-consuming and expensive.
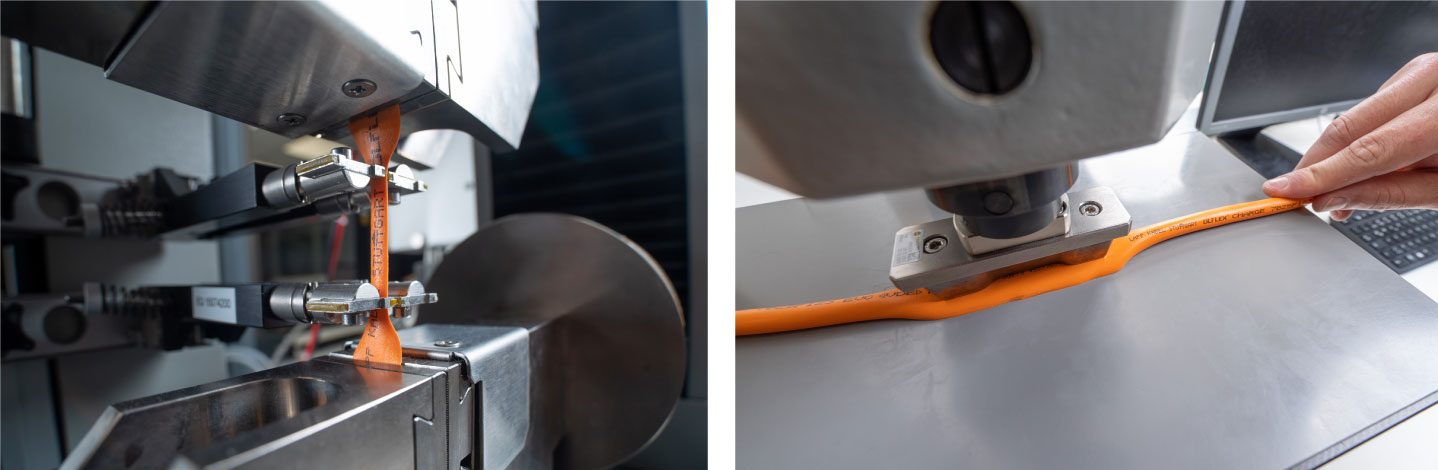
But it is even more expensive if production suddenly stops because a cable melts away out of nowhere – and at first nobody knows why. This is what happened at a Thai company. Within a few weeks, a cable had turned into a sticky mass and became unusable. The first thing to do is intensive troubleshooting. But LAPP can help quickly in such cases. Because the company operates laboratories all over the world – in Germany, Italy, France, the USA, South Korea, Singapore and India – it can react quickly to such enquiries and find solutions – even under the required conditions of a uniform “normal climate”. The result: the cable in production was brought into contact with certain chemicals for which it was not certified. As a result, it was damaged. Thanks to this test, the right cable for the Thai customer’s production environment was also found and delivered. “For us at LAPP, it’s worth the financial and time investment, because it’s the only way we can be sure worldwide that our test results and thus our products are of the highest quality and that we can recommend the right cables to customers for their applications,” says Jens Kärcher, Global Coordination Manager Laboratories at LAPP.
Small variation, big effect
How big the influence of the environmental conditions is depends on the type of test and the materials. Material testing or dimensional measurements in particular show large variances. For example, because many materials are “hygroscopic”, i.e. they absorb moisture from the environment and thus change their physical properties. Or because certain materials expand at higher temperatures and contract at lower ones. Thus, even small fluctuations can have a major impact on material properties such as brittleness, ductility, tensile strength or electrical conductivity.
Even with tight tolerance ranges, properties can be so temperature sensitive that a change of just 2°C can determine the outcome of a release test. For example, in the case of a highly filled, flame-retardant plastic that must have a tensile strength of at least 25 N/mm².
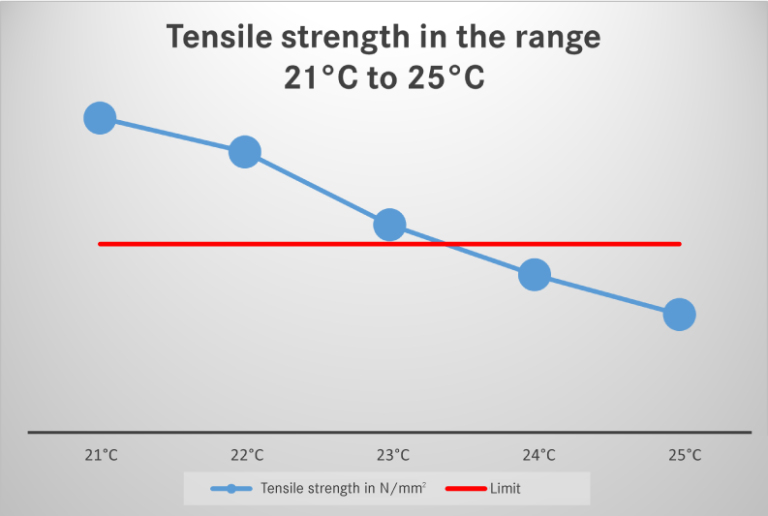
Accredited testing laboratory in Stuttgart
Jens Kärcher’s job is therefore to ensure that uniform environmental conditions are observed in all LAPP testing laboratories worldwide – within the framework of the standard specifications and, where necessary, even beyond: “We are committed to the highest quality in our components and services, we offer world-class logistics and support internationally, so it is only logical that we also go one step further with our testing laboratories.”
To this end, LAPP invests in state-of-the-art technologies and established processes to ensure maximum standardised test conditions and thus comparable test results. At its headquarters in Stuttgart, LAPP is currently even applying for accreditation of the testing laboratory according to DIN EN ISO/IEC 17025, a globally valid standard for laboratory accreditation for testing and calibration with general requirements for competence, impartiality and methodology.
Because: Trust is good, control is better, control under comparable conditions is best.