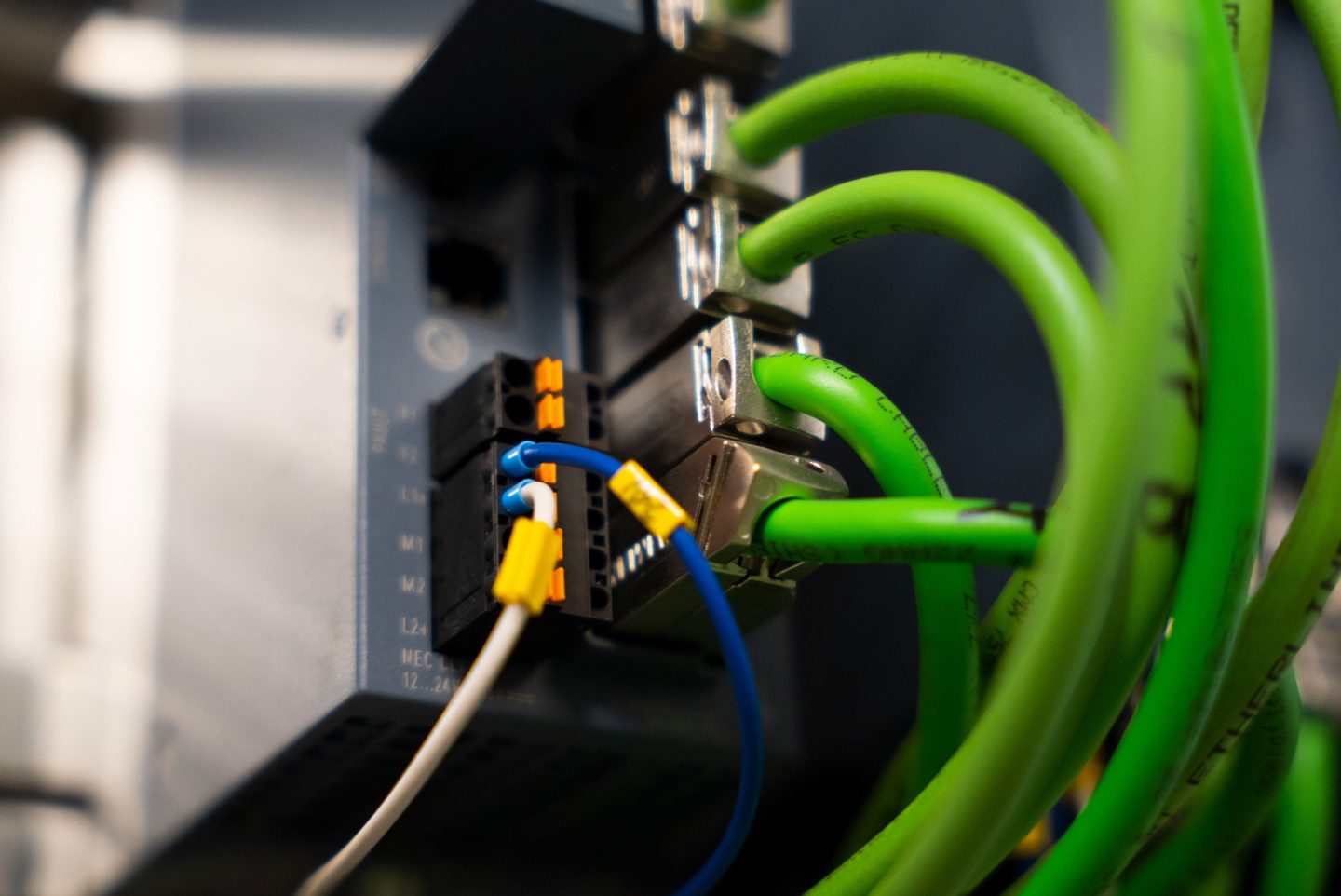
The Smart Factory is the ideal for many companies and, en route to this, the networking of machines and systems will continue to increase. Even today, a fully functioning network technology is one of the most crucial factors for a company to run well: if the digital nerve system fails, the industrial machinery will also come to a standstill. This can quickly become expensive and is extremely harmful for usage-based business models. IT and OT cybersecurity is therefore more and more trending as an industry topic, and rightly so. But external influences are not always necessary: around 50 percent of network failures are simply due to errors or defects in physical connections.
This is where the expertise of LAPP, the global market leader for integrated solutions in the field of cable and connection technology, lies. Today, the company already offers over 110 different services in addition to corresponding products – from configurators to customer-specific cables or assemblies and digital self-services on the website, right through to just-in-time deliveries. The Network Approval Service, a comprehensive approach to connectivity implemented by LAPP experts to ensure that a machine is fully commissioned, is a brand new addition to the LAPP portfolio. “With the Network Approval Service, we really take every cable into our hands,” said Dr Patrick Olivan, Senior Manager Business Development Services at LAPP, one of the leading people behind the new services. The service is primarily aimed at mechanical engineers. “In discussions, we realised that it is difficult for our customers to prove to their respective end customers that a complex machine has been optimally constructed and will be in operation without faults for many years,” Dr Olivan continues. “By having the machine tested and certified by our qualified PROFINET engineers, it is easier for them to guarantee a high level of plant availability, particularly by optimum connectivity and network technology.”
The Network Approval Service has been developed from the LAPP Health Check Service. The latter is similar to a health check and helps customers to minimise the risk of their existing industrial machinery failing due to weaknesses and faults in connectivity and ensuring ongoing low-maintenance operation. As a result, older machines are usually examined in cases where it is unclear how long they will continue to function without faults, or machines that have undergone an upgrade or retrofit and therefore need to guarantee an increase in performance. Customers receive a transparent overview of its condition and weaknesses, together with suggestions for improvement. The first companies have already benefited from the services: in all tests carried out so far, we have been able to detect latent weaknesses. “As a solution provider, we want to work more closely with our customers. It is not just about our individual components, but also about adding value for our customers, relieving the work load and eliminating risk in their processes.“
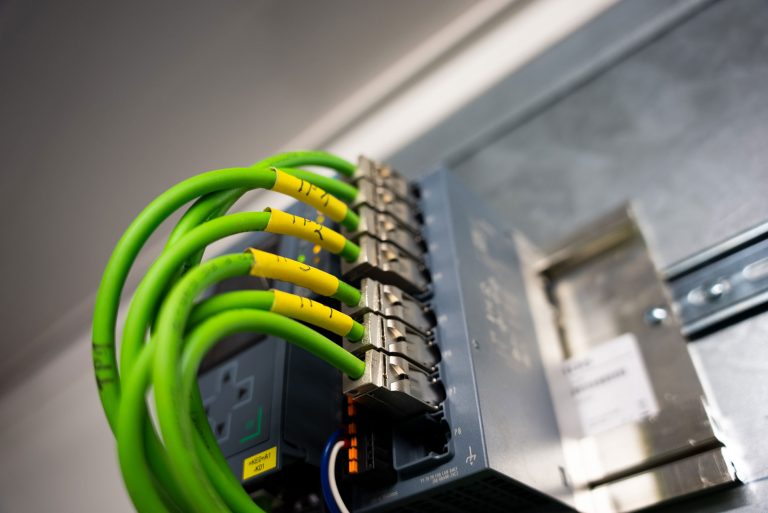
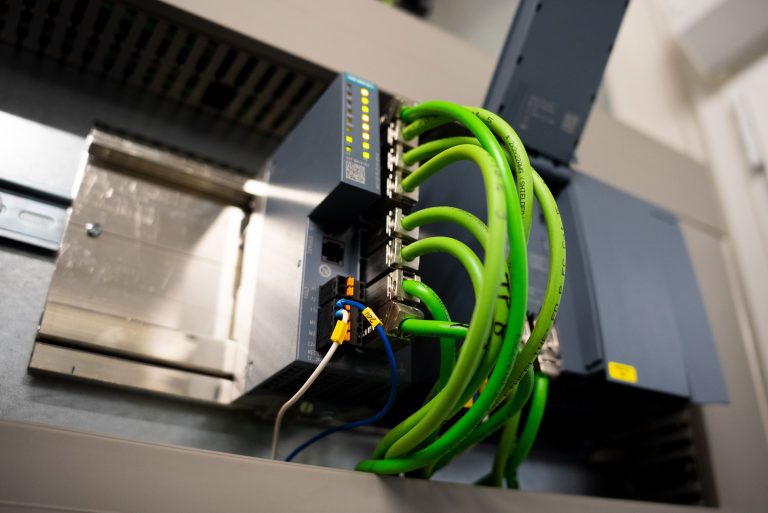
With the Network Approval Service, qualified experts from LAPP test the machine’s “nerve pathways”, i.e. the PROFINET networks and their components. Customers then receive a certificate that confirms the quality of the machine and its connection technology and ensures a binding commitment for five years, as well as a report on network communication and configuration and on the diagnostic messages of the network and devices. The scope of service also includes a cable certification report for the cables tested separately and an EMC checklist. If the findings uncover weaknesses, countermeasures are suggested that are necessary for successful acceptance. “This has two further advantages,” says Dr. Patrick Olivan. “On the one hand, this strengthens the trust in our customers’ machines and systems. However, by visiting the customer on site and taking the time for the review, we can also gain an in-depth understanding of the customer, their work and their needs, and can adapt ourselves and our portfolio more precisely to the customer’s needs.”
The LAPP Health Check Service is similar to a preliminary examination and can be used repeatedly by customers on a regular basis. If the experts encounter a need for optimisation, this is indicated and an upgrade can be performed. The overall package of both services – before commissioning and regularly during operation – makes the systems more resistant to errors and downtimes, as around half of all failures are down to connection problems with connectors, cables and switches, for example due to mechanical or environmental stress, ageing, low-quality products, incorrect earthing or a poor network.
The LAPP team of certified PROFINET engineers uses special devices such as the “Atlas 2” from PROCENTEC, a member of the HMS group, or the “PN quick tester” from LEADEC for the two services and thus scans the entire machine network for weaknesses and errors. This is accompanied by a visual inspection, whereby they check products selected are suitable for the application, design and its condition. The target group is primarily medium-sized machine builders or production operators, who generally do not have their own staff for such cases or are happy to hand over the job due to capacity constraints. As a result, LAPP can support these customers in commissioning or even carry out the health check in production for older existing machines. The aim is to constantly accompany customers and their machines and provide them with specialist support in order to guarantee reliable operation.
Practice shows faults are often found in details
At NLT Automation GmbH, the global market leader in automation for the adjustment industry, LAPP service has already been able to prove its worth in practice. There, the experts from LAPP analysed a new machine that cuts coils into strips for the metal industry. NLT was convinced from the outset that no weaknesses in connectivity would be found. At the time of testing, the M9 machine was not only very new, but also fitted exclusively with high-quality components, including cables from LAPP and managed switches for a more stable network and better error diagnosis. In addition, the power and data connections were tidily separated with respect to EMC to avoid interference. These made good prerequisites for fault-free operation. “During our test, we were able to confirm the high quality of the machine to NLT,” explains Dr Patrick Olivan. “With this knowledge, NLT can now operate safely at the end customer.” The only thing that needed to be retrofitted was due to the test values of a data cable indicating electromagnetic interference. LAPP and NLT then worked together to improve the installation. “We were very confident about our position,” says Micha Glave, Managing Director at NLT. “In fact, despite the excellent design and installation, EMC problems are difficult to predict and prevent. Only an inspection can provide certainty,” adds Dr Olivan. Apart from this one cable, the LAPP experts were able to ascertain and certify that connectivity in the NLT system was very well designed and set up in terms of maintenance and reliability.
On the other hand, this shows that even a very well set up machine and connection solutions can still have unforeseen weaknesses. Sources of errors are often hidden in the smallest of details. And it takes connectivity experts like LAPP to locate these. Not only can they quickly identify weaknesses, they can also provide the right solution right away.