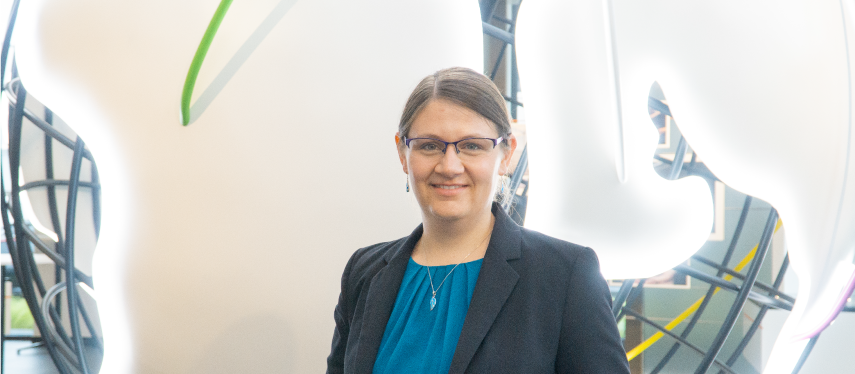
LAPP’s history as an expert in cables and connection solutions began in 1957 with the invention of the first cable with differently coloured wires. Since then, all LAPP products have one thing in common: they are largely made of plastic – and this will never change! In simple terms, a cable always consists of an electrical conductor surrounded by insulating materials. If you take a closer look at the structure of a cable, you will see that it is not just a single sheath: Different copper conductors are each covered with an insulating material, such as PVC or PE, to – as the name suggests – isolate them from each other. Depending on the application, an inner sheath or shield of copper braid or foil may also be required. An outer jacket is then produced to protect the cable from mechanical stresses, chemical mixtures and temperature effects. Depending on the requirements, this can be made from different plastics such as PVC, TPU or TPV. Since each layer of plastic in the cable serves a specific purpose, it is important to think carefully about whether and how to switch to green materials.
This is where Silvia Lajewski comes in. Her job at LAPP is to research this area and develop solutions to make the use of material in LAPP products more sustainable. But why is LAPP taking this step? “As plastics are a key component of our products, it is important that we take a close look at this material,” explains Silvia. “Sustainability is also firmly anchored in our corporate strategy, so we want to make our products as a whole, including the use of plastics, more sustainable.”
Silvia explains that this is possible by first breaking down the different groups of plastic. The best-known group is probably the one containing conventional plastics, which are based on fossil resources and make up the majority of plastics produced worldwide. In 2021, for example, they accounted for around 90%. So-called “bioplastics” offer an alternative. “However, not all bioplastics are the same and this does not automatically mean that they are sustainable,” explains Silvia. “Plastics differ not only in the way they are produced, but also in their degradability. So, there are plastics that are called bioplastics that are still based on fossil resources because they are easily biodegradable”.
So-called ‘bio-based’ plastics, on the other hand, are the sustainable alternative to conventional plastics because their raw materials are of plant or animal origin and can be harvested within a maximum of two growing seasons.
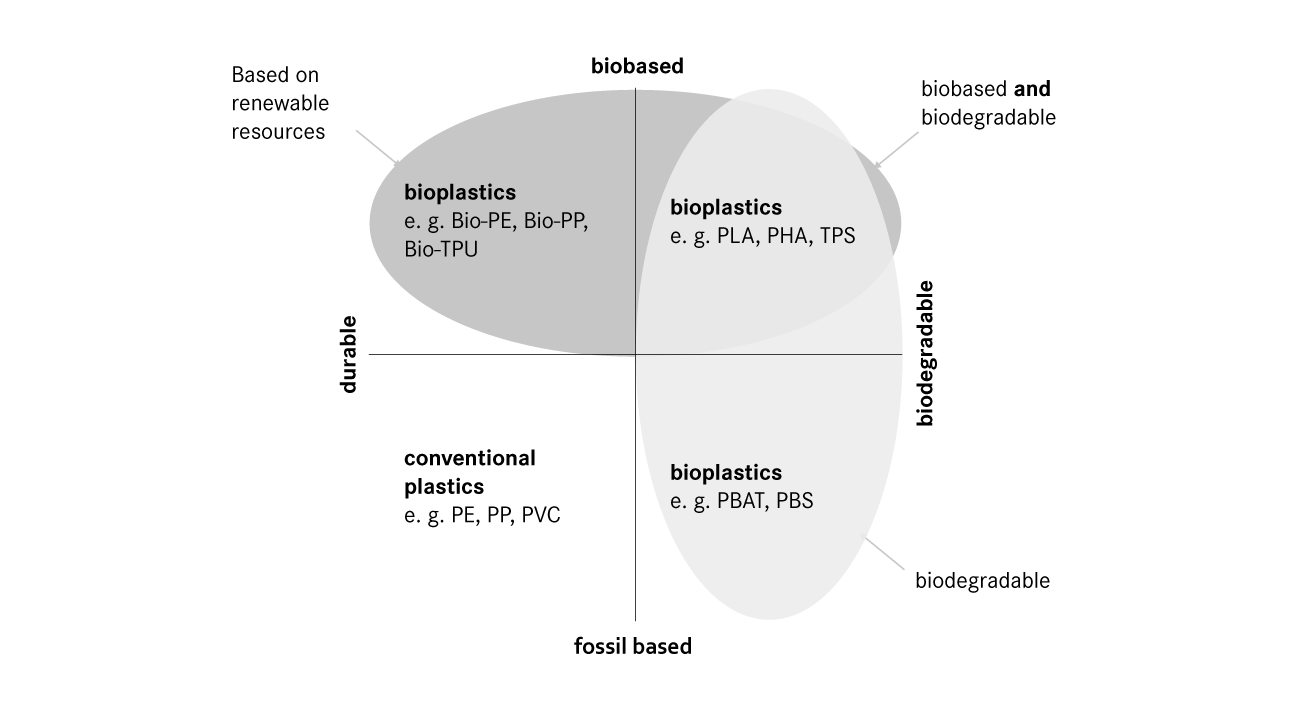
For LAPP, the expert sees the solution in bio-based plastics that are not biodegradable, because “in technical applications, a high level of durability and therefore a long service life are generally desired. After all, it would be anything but advantageous if the cable sheath decomposed without leaving any residue during use.” This can be achieved with completely new polymers such as polyethylene furanoate (PEF), the use and processing of which must also be completely re-evaluated. However, it is also possible to produce chemically identical materials from bio-based feedstocks such as bioethanol, as the familiar conventional materials. According to the expert, these plastics do not differ from conventional plastics in terms of their long-term durability. By utilising renewable resources, however, they can achieve a closed CO2 cycle if production and processing are also designed to be CO2-neutral. “The possible sources of bio-based plastics are as diverse as they are numerous: bacteria and algae, sugar, rapeseed, sunflower oil, but also agricultural residues such as whey,” says Silvia.
What makes a polymer a plastic?
The chemical term polymer refers to high-molecular compounds of hydrocarbons that are made up of several thousand to several million small repeating units (monomers). A polymer in its pure form must be prepared with suitable additives, a plastic is therefore a technically usable material made of polymers and additives.
This diversity makes it possible to develop tailor-made solutions that meet the requirements and objectives of sustainable plastics use. Although the market for bio-based plastics is still in its early stages, Silvia Lajewski emphasises that this could change. “In particular, the use of agricultural residues as raw materials for bio-based plastics is currently being intensively researched in order to ensure the availability of these materials,” she explains. The focus on source also makes sense because it ensures that there is no shortage of resources in other areas, such as feeding people and animals.
LAPP has already taken this approach and is starting to see results. Silvia is proud of the ETHERLINE® FD P Cat.5a for Industrial Ethernet, which is the first series product made from a bio-based compound in the company’s portfolio . This corn-based bio-polymer has the same properties as the TPU variant made from fossil raw materials.
LAPP is also testing the use of recycled materials, known as rPlastic, as an insulation and sheathing material for cables. Prototypes are being tested for their cable-specific mechanical, chemical and electrical properties, and could significantly reduce the carbon footprint of future products.
Silvia concludes the interview optimistically: “At LAPP, we are proud to be at the forefront of sustainable innovation. Our research and development into plastics shows that the future can be greener and more sustainable. We invite all interested parties to discuss these ground-breaking developments with us and work together towards a sustainable future.”
With this in mind, Silvia calls on companies to see the path to sustainable plastics solutions as part of the journey towards climate neutrality and therefore as a shared endeavour. A transformation that will not only change products, but also the way we look at plastics.