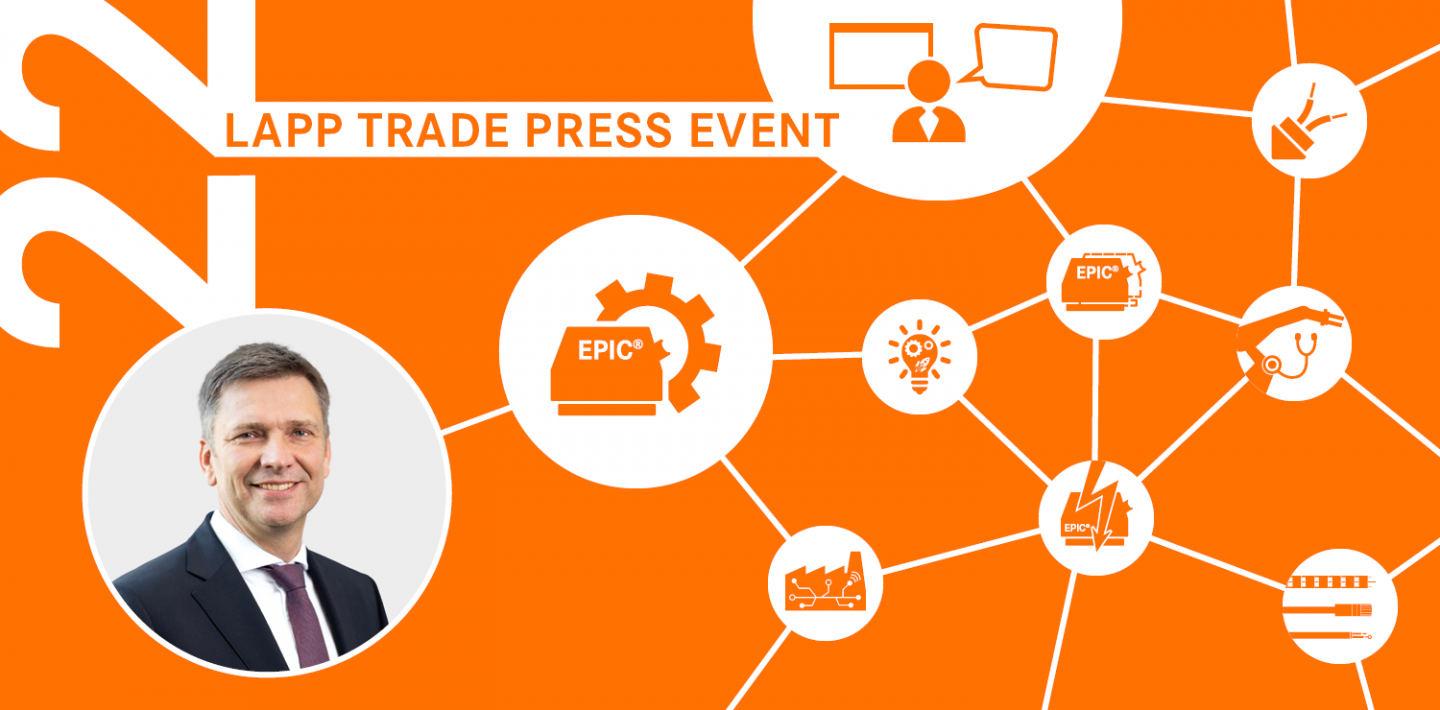
Networked industry is constantly in a state of flux. The German Zukunftsinstitut or ‘Institute for the Future’ identifies twelve global mega-trends that are set to affect all levels of society and thus also influence industrial connection technology. Two of these trends – connectivity and customisation – are the biggest development drivers here. Connectivity describes the principle of networking based on digital infrastructures. For industry, for example, this means that an increasing number of sensors are being integrated into machines under the banner “Industry 4.0”, allowing remote access and real-time data availability and making machine-to-machine communication increasingly important. The second trend, increasing individualisation, is aimed in particular at self-realisation in a personal context. However, there is also a strong trend towards individualisation in the industrial environment. This means that plant operators need machines tailored to their requirements which must therefore be customised in their development and manufacture.
These two mega-trends – connectivity and individualisation – also have a huge impact on connection technology, which needs to be more robust, standardised and considerably smaller. Ultimately, more and more connections need to be made in the same installation space. This is not possible without miniaturisation and power compression.
LAPP, the global market leader for integrated solutions in cable and connection technology, also has to face this challenge, as components such as cables and connectors are also subject to this ongoing change process.
In the cable sector, for example, the solution is Single Pair Ethernet. But what about connectors? What influence do standardisation and miniaturisation have on development, or has the development of connectors already reached its limits?
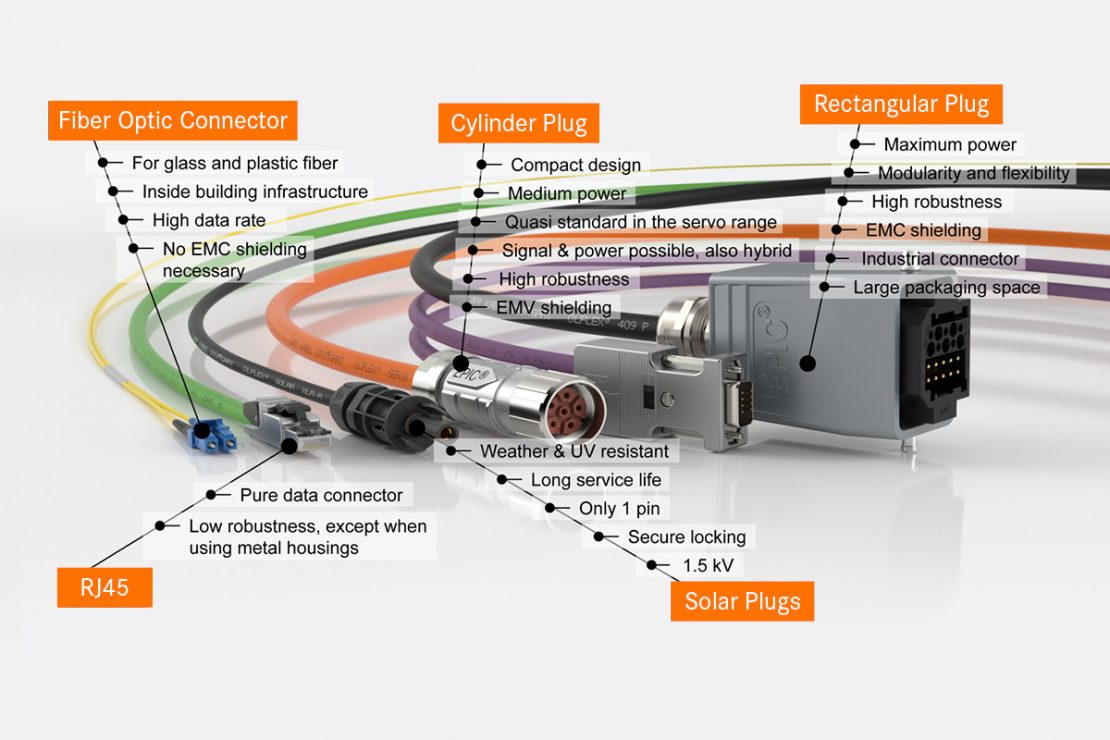
“I’m absolutely convinced that there is still plenty scope when it comes to connectors. Miniaturisation and increasing connectivity are the driving force behind development in industry. This will also lead to increased performance and further standardisation in connection technology”, stresses Georg Stawowy, Member of the Board for Technology and Innovation, Lapp Holding AG.
At LAPP, the connector has always been deeply rooted in the DNA of the Stuttgart-based family company. Before the company was founded in 1959, Oskar Lapp (1921 – 1987) had worked for a renowned market leader for industrial connectors, where he was responsible for southern Germany. He had already made a name for himself with his innovative ideas. He developed the first rectangular connector for the company.
From the very beginning, the founding couple Oskar and Ursula Ida Lapp positioned their company as a “one-stop shop” in connection technology – and the principle is still a recipe for success to this day. So shortly after the first industrially manufactured ÖLFLEX® power and control cable was launched, LAPP also offered connectors under the brand name EPIC® (Environmental Protected Industrial Connectors). With the worldwide introduction of customised assembly solutions under the name LAPP Harnessing Solutions, connectors became increasingly important for LAPP. While electrical connections used to be hardwired, soldered and then often not touched for a long time, their place is now taken by connectors that can be disconnected and reconnected again thousands of times, always creating a reliable contact.
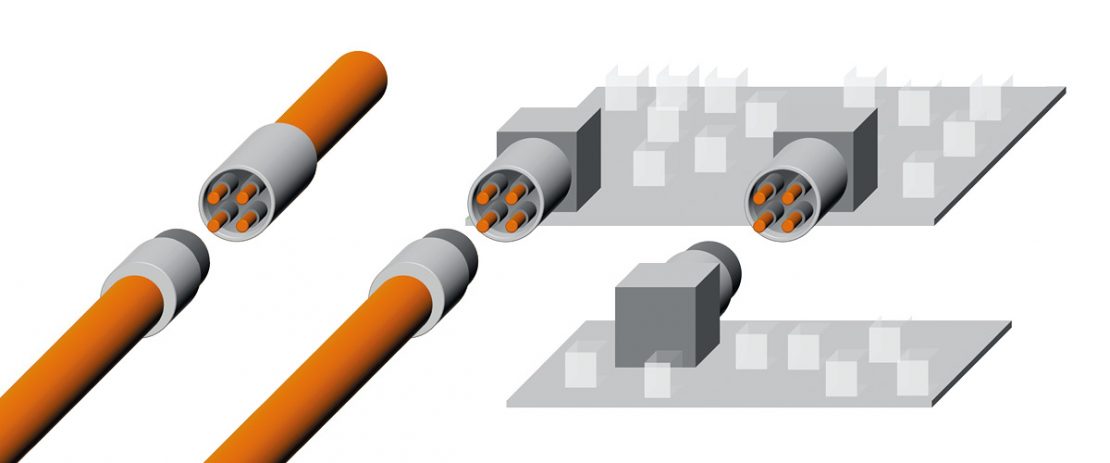
Today, LAPP offers a flexible system of rectangular, round and solar connectors made up of extremely robust housings, cables, inserts and contacts, which enable simple and safe connection and disconnection of cables and wires. LAPP’s portfolio includes all common types of connectors. With the EPIC® configurator alone, you can assemble your individual industrial connector housing with locking concept and cable entries yourself. A total of 138 million possible configurations is possible. With the particularly robust EPIC® MH rectangular connector system, the connector frame can be equipped with both LAPP connector modules and standard modules available on the market – and assembly is far easier than with conventional folding and sliding frames. The user has almost unlimited combinations available: 2 to 36 pins, currents of up to 100 A, voltages of up to 1,000 V, data with bandwidths up to Cat.7.
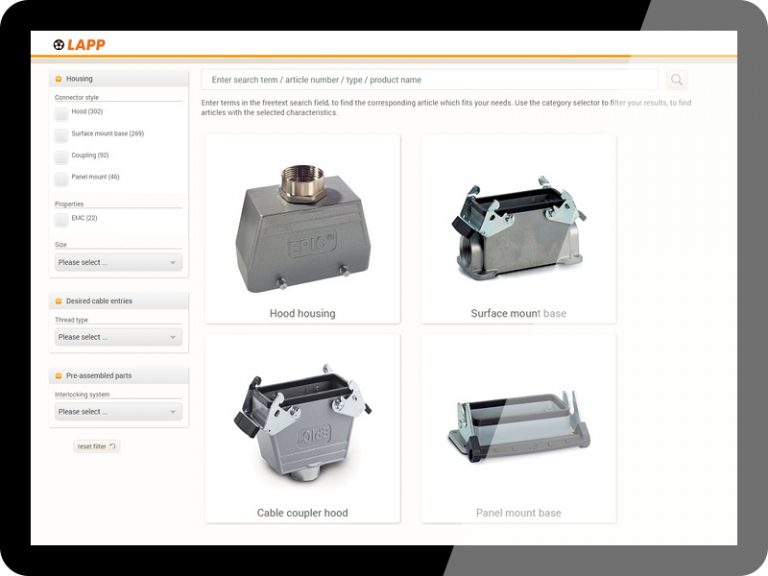
The EPIC® configurator, you can assemble your individual industrial connector housing with locking concept and cable entries yourself
For transmitting digital data (signal, power + hybrid), LAPP has rectangular and circular connectors in its portfolio. Standards are the thread sizes M23 and M17 as well as space-saving M12 connectors. As the de facto standard in servo applications, they are extremely robust and boast good EMC screening. There are also particularly weather- and UV-resistant solar connectors with reliable locking and long service life, the RJ 45 data connector, and connectors for glass fibre cables for building infrastructures with high data rates.
But what are the prospects for the connector? On the one hand, connectivity is constantly increasing due to an increasing number of functions (sensors, condition monitoring, remote access etc.) and performance in the machines, yet the installation spaces in machines are shrinking or at least remain the same, on the other. As mentioned above, this necessitates miniaturisation of the connectors. Unfortunately, this is not so easy. Physics also sets limits for connectors. Because, to achieve maximum current, contact thickness is crucial – a very special challenge when it comes to miniaturisation. The maximum voltage is primarily influenced by two factors: the air gap defines the distance between conductors, the greater the distance, the greater the voltage. Then there is the so-called creepage distance. This is the connection along the insulation that influences the voltage depending on contamination.
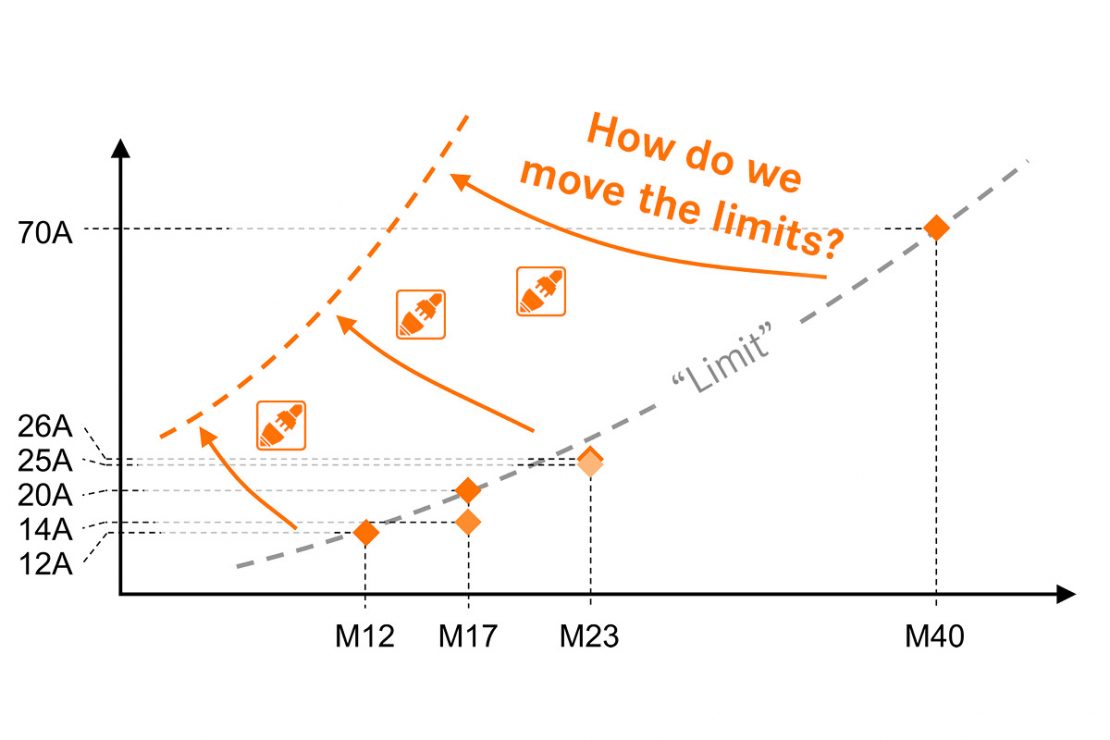
But what does this mean for the performance of connectors? Circular connectors from LAPP (M12 to M58) are currently available for currents of 12 to 150 A. The challenge now is to break the existing limits with design innovations. The new M12L connector not only handles currents of 16 A (previously 12 A), it is also the smallest M12L connector in the world (see presentation by Martin Guserle).
Alongside connectivity, increasing individualisation is the second important trend. “This leads to an increasing diversity of variants and modularity, as well as a high level of standardisation among our customers”, says Georg Stawowy. The objective: custom production. This is why the connectors used should be as standardised as possible. Production systems need to be increasingly flexible. This requires the modules to be easy to reconfigure, which can only be achieved using standardised connectors.
The Discussion of the issue of wireless and 5G versus physical connection with cables and connectors is ongoing. It is clear that wireless and cables will coexist in factories in the future. However, cables and connectors remain the first choice where it is indispensable that machines communicate among each other quickly and free of interference – such as in transmitting sensor data in real time or for supplying power to drive systems. Where data reliability and latency are crucial, there is no alternative to the connector. Another advantage is that wired connections are less susceptible to hacker attacks than wireless connections. Wireless connection technology will therefore not replace cable-based systems and connectors, but supplement them at the most.
But where is the journey going? The idea of creating an easy connection between modules with a simple contact interface, i.e. by simply attaching the module to be connected to the machine, for example, is being discussed more and more frequently. This means that particularly robust connection solutions are required in industry that can withstand temperatures, dirt and vibrations. This would not be possible without a connector.
To sum up, increasing connectivity and greater individualisation are the driving forces behind development in connection technology. If connectors are to remain the solution of choice in the industrial environment, they need to be significantly advanced in terms of miniaturisation, standardisation, performance capacity and robustness.