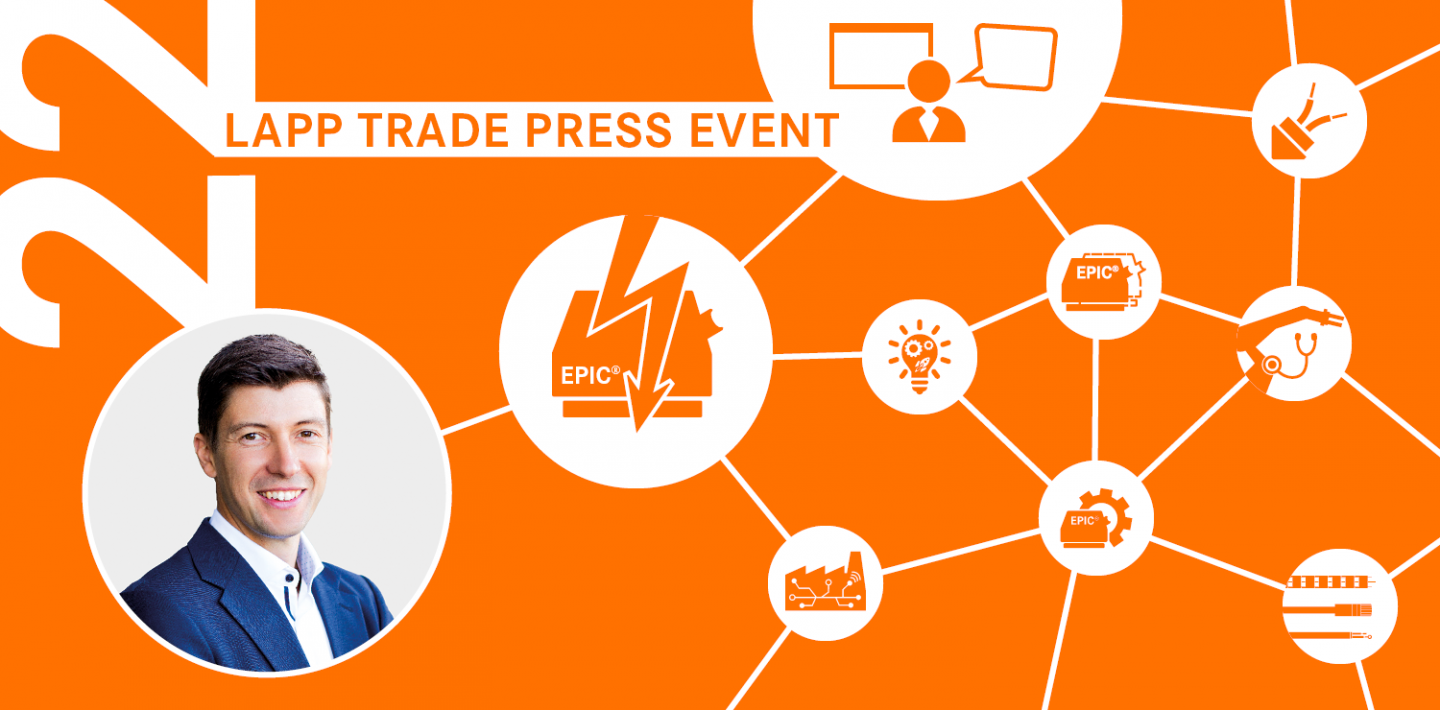
Modern high-current connectors must be able to safely carry high operating and residual currents as well as current pulses. A low contact resistance must be achieved in the new condition and retained for the entire service life. The many factors that need to be considered show that this is not so easy: the selection of suitable conductor and coating materials, the design of the geometry of the plug, socket and any present contact elements, and the definition of the necessary assembly parameters. In addition to the basic, known analytical approaches, numerical methods can also be used in the design.
“The role of connectors is often underestimated. In actual fact, tailored selection is hugely important for reliable operation and for a long service life of the entire system,” emphasises PD Dr.-Ing. habil. Stephan Schlegel, Chair of High Voltage and High Current Engineering, Technical University of Dresden.
Importance of live connections
In electricity supply networks, power is fed from conventional power stations and increasingly from renewable energy converters such as photovoltaic or wind power systems. They feature a modular design and millions of installed current-carrying connections ensure that electrical power is available 24/7 at home and in industrial facilities. The downtime in Germany is currently approx. 20 minutes per year, which cannot be beat by any other country. This requires a high level of reliability and safety from the system and therefore from the components. The use of connectors is of central importance here. They are essential for separable system parts and to compensate for relative movements between equipment, for example as a result of thermal expansion during operation. Such connectors are highly loaded components and therefore have to meet numerous minimum requirements.
This includes, in particular, a high current-carrying capacity due to a low contact resistance, a compact design due to a high power density, high operating temperatures due to temperature-resistant conductor and coating materials and stable tribological behaviour for a high number of connection and sliding cycles. All of these factors are essential for a long service life.
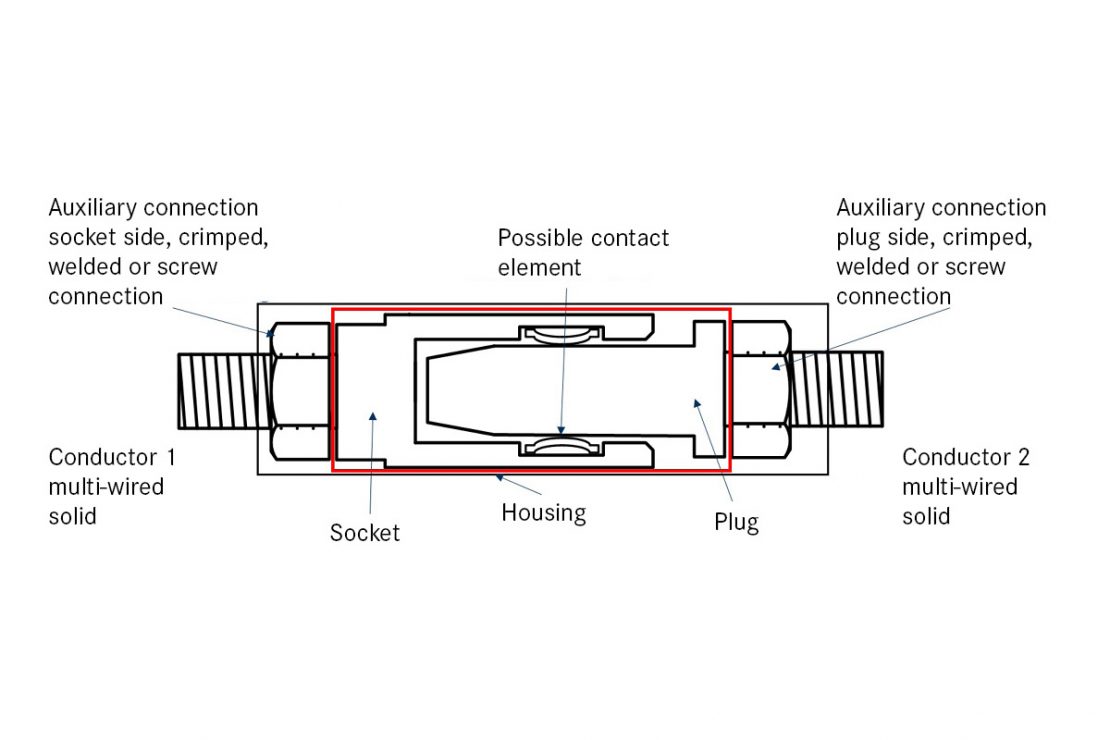
Connectors: design, operating principle and requirements
Connectors consist of two auxiliary connections, which are used to connect the conductors to the plug and socket. These are produced with pressed, welded or screw connections. The main connection between the plug and socket can be established using contact elements, finger contacts or slotted sockets. This must be designed in such a way that there is always a sufficiently high contact force to achieve the lowest contact resistance as well as low friction wear.
Correct selection of contact materials
The contact and long-term behaviour largely depends on the contact and spring materials used. For conductor materials, the main factors are high electrical conductivity, good thermal conductivity, temperature stability, high mechanical strength and, if applicable, spring properties and good mechanical machinability. This is why copper alloys are the top choice for this. For coating materials, the key factors are low impurity levels on the surface, good adhesion to the conductor material, temperature stability of the structure, low welding inclination and high wear resistance. Gold-based and silver-based contact materials are the most commonly used for high-load connectors.
The softening temperature of the conductor and coating material also plays an important role as the limit operating temperature for constant and short-term current load. The aim is to improve contact and long-term behaviour by choosing the right coating. A low-alloyed gold coating with an intermediate layer made of nickel is recommended for a maximum physical limit temperature of 180°C. New silver-palladium coatings are expected to be usable even up to 200°C. At the same time, research is being conducted to further develop the coatings in order to achieve higher operating temperatures and thus a stable material structure and greater wear resistance. By using certain lubricants in dispersion layers, the number of connection cycles can be increased by reducing the friction value between the contact partners. There are self-lubricating silver coatings with particles made from graphite or with particles made from WS2, MoS2, SiC, Bi2S3, hBN or SnS currently under research, which could be a good alternative to conventional contact lubricants. A research project on this is topic is currently under way as part of the professorship.
Design according to physical behaviour
In order to understand the relationship between contact force and contact resistance, physical knowledge about contact and long-term behaviour is required. In addition, the finite element method (FEM) – a numerical process used for different physical tasks – can be used to examine certain relationships. This method can be used to support the electrical and mechanical configuration of the macroscopic structure (socket, plug geometry and contact element). One challenge is simulating the electrical contact to correctly reproduce the electrical thermal behaviour. In some cases, this is not possible with the standard functions of computing software. This is why the Technical University of Dresden has developed expanded modules. The aim was to assess whether the mechanical and electrical thermal loads are lower than the strength of the materials used with minimal use of materials. Short current spikes/residual currents in which heat conductivity and/or heat storage dominate in the material are particularly challenging. Due to the non-homogeneous temperature distribution in the contact in these cases compared to the homogeneously flowing conductor, the I²t criterion (criterion for short-term overload capacity of electrical components) is no longer applicable. For very short pulse currents, a numerical calculation is necessary to be able to consider the influence of the thermal capacity on the temperature distribution.
Ageing, service life and testing
The ageing of live connections is influenced by five factors: force reduction (creep and stress relaxation), diffusion (formation of intermetallic phases, contact adhesion), frictional wear (abrasion and adhesion), electromigration (vacancy migration) and chemical reactions (oxidation and galvanic corrosion). Ageing leads to an increase of the contact resistance, power loss and thus the connection temperature. This process accelerates damage to the connection and surrounding components such as the insulation.
The ageing mechanisms are heavily temperature-dependent. They can be calculated using the Arrhenius equation, which describes the quantitative temperature dependence in physical and primarily chemical processes. However, the service life also largely depends on the current-carrying capacity, the current level and the duration of the current flow. Depending on the operating conditions, specific ageing tests are necessary to calculate the service life for the application. Standard tests do not fully meet these requirements.