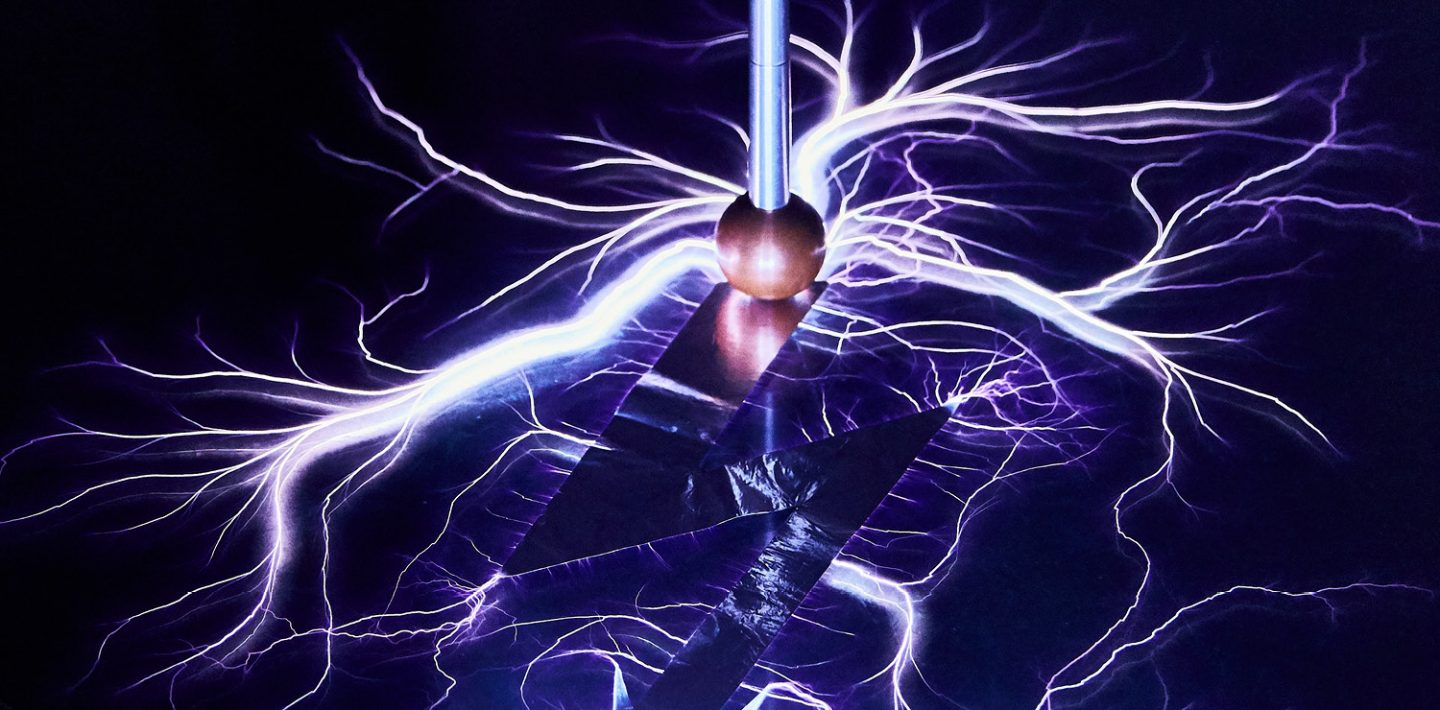
The use of direct current, however, could also bring about much additional potential in industry and private life. This is particularly the case if the source for electricity generation comes from renewable energies such as photovoltaics. These energy sources produce direct current (DC), which has to be converted into alternating current (AC) via inverters. On the other hand, if the end consumer is once again a digital device such as a laptop, iPhone, LED lamp, charging station for electric vehicles or an intelligent production unit in a factory, this would require double conversion, as these end consumers only work with direct current. As a result, conversion losses are incurred. Initial analyses estimate a rate of 3 to 5 percent. Experts have calculated that if the entire electricity grid in Germany were to be converted completely to direct current, about 25 percent of total energy requirements could be saved by 2030.
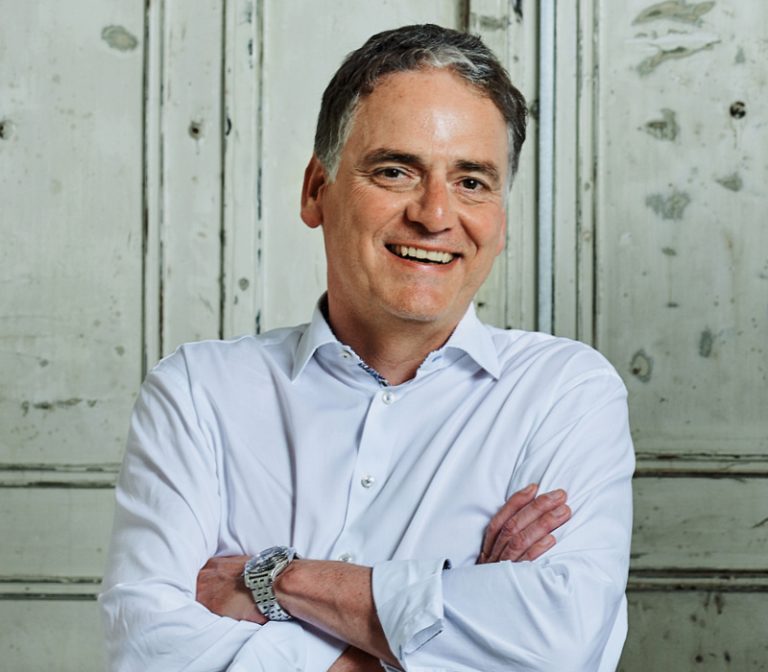
Guido Ege, Head of Product Management and Product Development at LAPP, is convinced: “We are increasingly living in a DC world. The long-term abandonment of fossil energy sources can only be managed efficiently if we are consistently switching more and more to direct current and avoid conversion losses. In short, we need a turning point without change.”
But the consistent introduction of direct current is still somewhat laborious. Until now, there are only niche applications in industry. Large automobile manufacturers, for example, have installed test cells. We are talking about efficiency gains of 5 to 10 percent, which can be further increased by integrating recuperation energy. But the big hit is missing. There is still a need for action at many levels. Nevertheless, LAPP has addressed the topic of direct current at a very early stage and is active in the development of cables. The company already has a cable portfolio for a wide range of applications.
These cables include the ÖLFLEX® DC 100 with new core colour coding according to EN 60445 (VDE 0197):2018-02 (updated in 2018) for direct current cables: red, white and green-yellow. Other cables include the ÖLFLEX® DC Servo 700 for stationary applications and the ÖLFLEX® DC Chain 800 made of TPE for moving applications. Or the first DC robot cable ÖLFLEX® DC robot 900 with core insulation made of TPE and a PU sheath. This makes LAPP a pioneer in the development of cables for low-voltage direct current networks for industrial applications.
There are still further issues regarding standardisation, and DC-compatible components need to be provided, for example, on connectors and switches. Further research is required here, as with direct current, for example, an electrical interference arc does not extinguish itself. This can be life-threatening.
With direct current, you need new components, for example switches, so that the arcing fault is extinguished
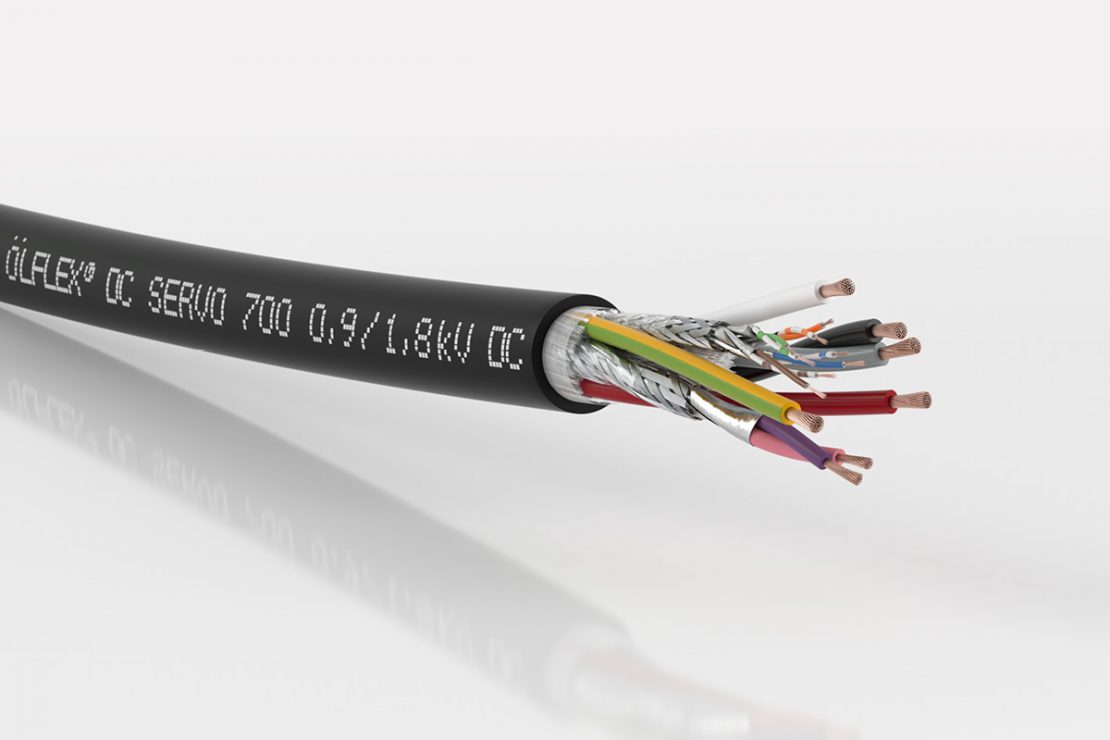
There are still many unanswered questions. That is why LAPP is a supported partner in the DC Industry2 research project. In this project, researchers from the Fraunhofer IPA and Fraunhofer IISB have worked together with 40 partners to develop a concept for an intelligent DC supply system and test whether this DC system can supply a production hall with direct current economically. The German Federal Ministry for Economic Affairs and Energy BMWi is supporting the project, which will run till the end of 2022. LAPP is researching the long-term stability of insulation materials for cables.
In advance, LAPP and the Ilmenau Technical University of Technology had discovered in experiments that a few insulation materials exhibit a different ageing behaviour in a DC field than in an AC voltage field. For example, researchers from the Ilmenau University of Technology have loaded single cores with different insulation materials in a water bath at 80°C with 1 kV DC voltage over a period of 2,590 hours to track the effects in fast motion. The results show that almost all insulating mixtures equally withstand AC and DC stress. However, a few PVC compounds, halogen-free compounds and FRNC (flame resistant, no chloride) failed faster in DC than in AC. For instance, it is not yet clear what happens in the plastic chemically and physically. Possible causes could be the decomposition of the polymer or its swelling in water, the release of additives or the formation of “water trees”.
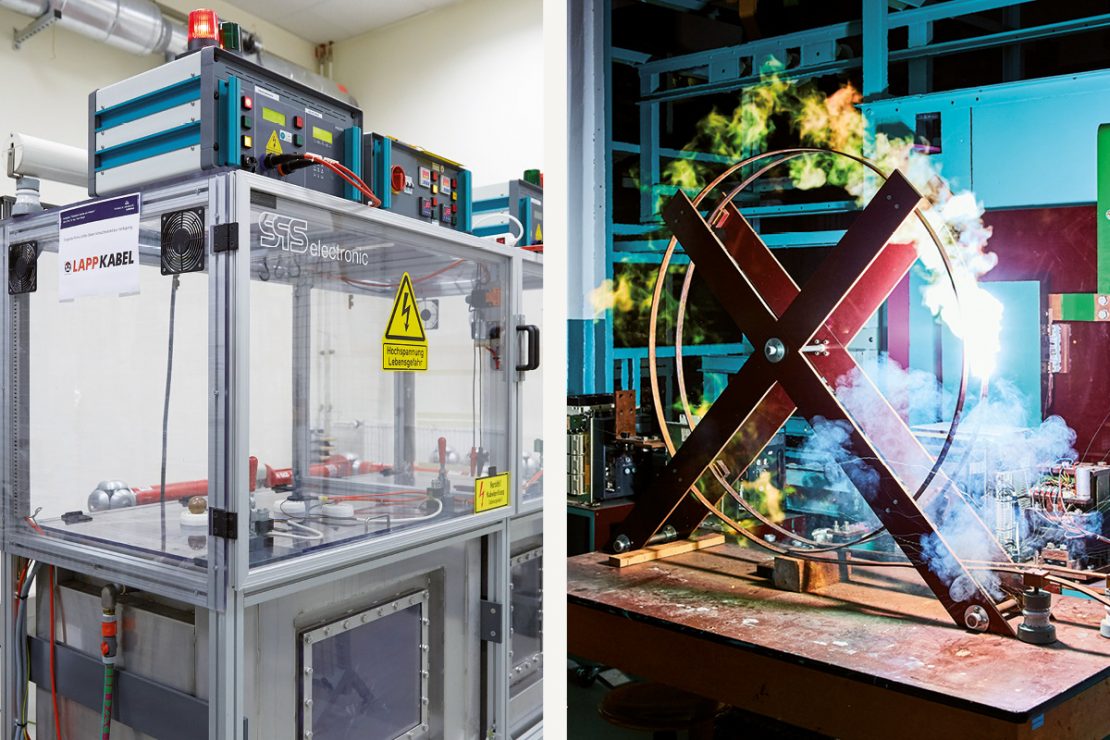
“We see major economic opportunities in direct current. Not just for the automotive and process industries. By reducing conversion losses, we increase efficiency. If converters are no longer required, we need fewer components and therefore less space. Renewable and decentralised energy sources can be integrated more easily,” Guido Ege adds, listing the benefits.
A direct current supply would also be the ideal requirement for drives to re-feed energy into the DC grid when braking. As with electric or hybrid cars, this energy would be stored in batteries until the drive accelerates again. This energy could also be used to supply consumers with high power requirements, for example, when welding. This would allow the companies to reach load peaks and would not have to obtain high amounts of energy from the grid for a short period.
“DC technology will decisively change industrial production and the energy supply of cities and neighbourhoods. This makes it an important element of the energy revolution,” emphasises Guido Ege.
![]() |
|
When it comes to direct current, LAPP is already a partner in demand. For years, LAPP has had a comprehensive DC-compatible portfolio for photovoltaic and wind turbines. However, conversion losses in wave power farms are also avoided with DC. For example, a wave power plant belonging to Munich-based company SINN Power is in operation in the port of the Greek city of Heraklion. In future, the ÖLFLEX® DC 100 direct current cable for the 800 V DC bus will be used for the decentralised mini grids.
Although medium and high voltage (HVDC) are not part of LAPP’s business, it is often still the company’s partner of choice for special infrastructure projects. LAPP has developed a tailored solution for the Sortimo Innovation Park in Zusmarshausen. |
Here, LAPP has developed the complete DC BUS for connecting the charging stations, including hybrid DC cables for control and online monitoring. The cable specially designed for the charging station consists of an aluminium conductor with a cross-section of 30 mm2.
The core insulation is electron beam cross-linked and is made of polyethylene. The screening is achieved by means of copper wires applied in a spiral over the core. The special feature is that the structure is supplemented by two stainless steel pipes, each with six fibre optic cables. These pipes are used to measure temperature and signal an alarm if the temperature at the charging points becomes too high. The BUS is then used to control where appropriate free charging capacities are available as an alternative. |