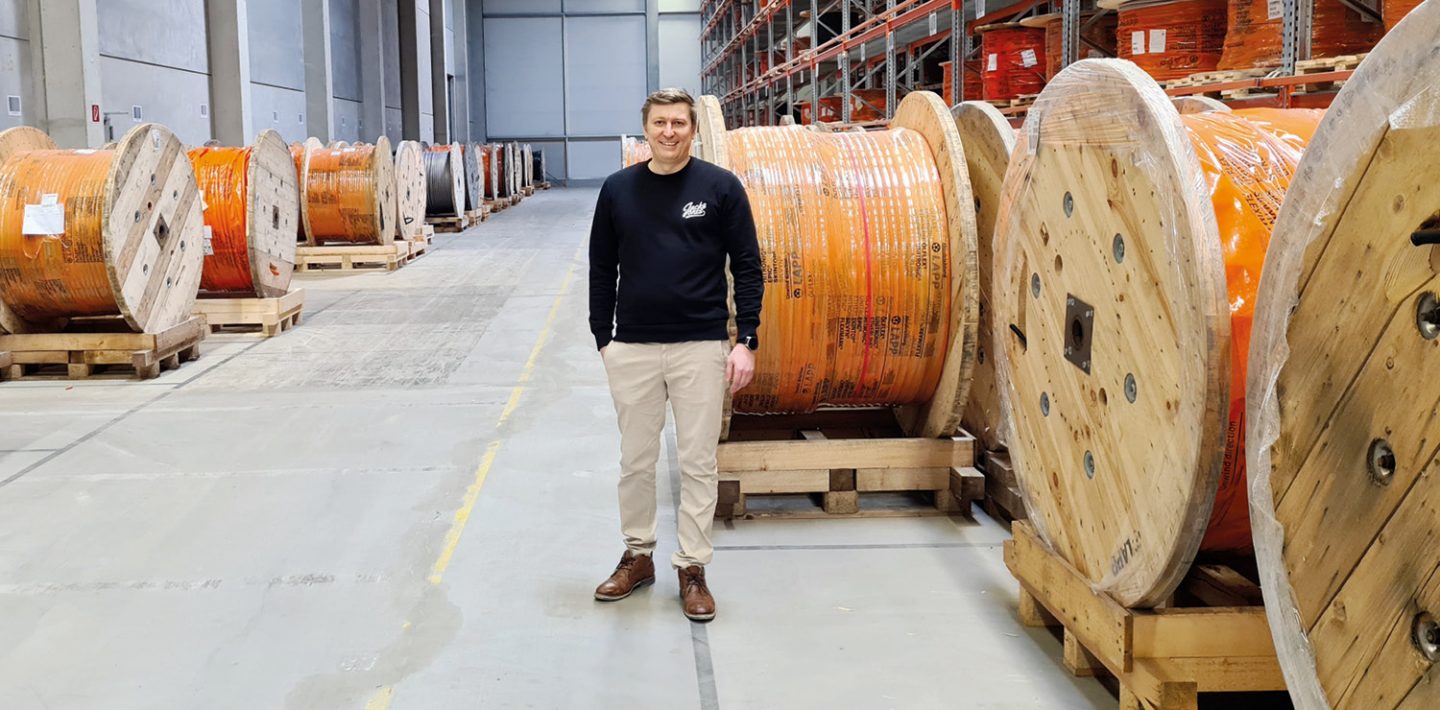
LAPP is also taking this opportunity – and Johann Zimmer had the idea. Since 2017, he has been working at LAPP in the logistics and service centre in Ludwigsburg. In the Logistics Systems and Services department, he focuses on optimising processes and services. “I studied Technical Logistics Management at Heilbronn University, and in our 6th semester we had to put logistics projects into practice at large companies such as Daimler, Kärcher or Porsche. I wanted to have LAPP there,” says Johann Zimmer.
Prof. Susanne Hetterich, Professor in the Business Administration and Logistics Department at Heilbronn University, was happy to accept the offer from LAPP. The first two projects by students have already been successfully completed.
One team of four students developed a new tool for risk analysis in Ludwigsburg. Why? Due to the high level of automation in the logistics and service centre, the failure of individual components or software solutions could lead to a complete system shutdown. The project focused on a method of assessing risks as realistically as possible and identifying preventive measures to minimise the possibility of the failure. The main focus was on IT technology and maintenance. The new tool has been in use in Ludwigsburg since the end of February. Further logistics sites will follow.
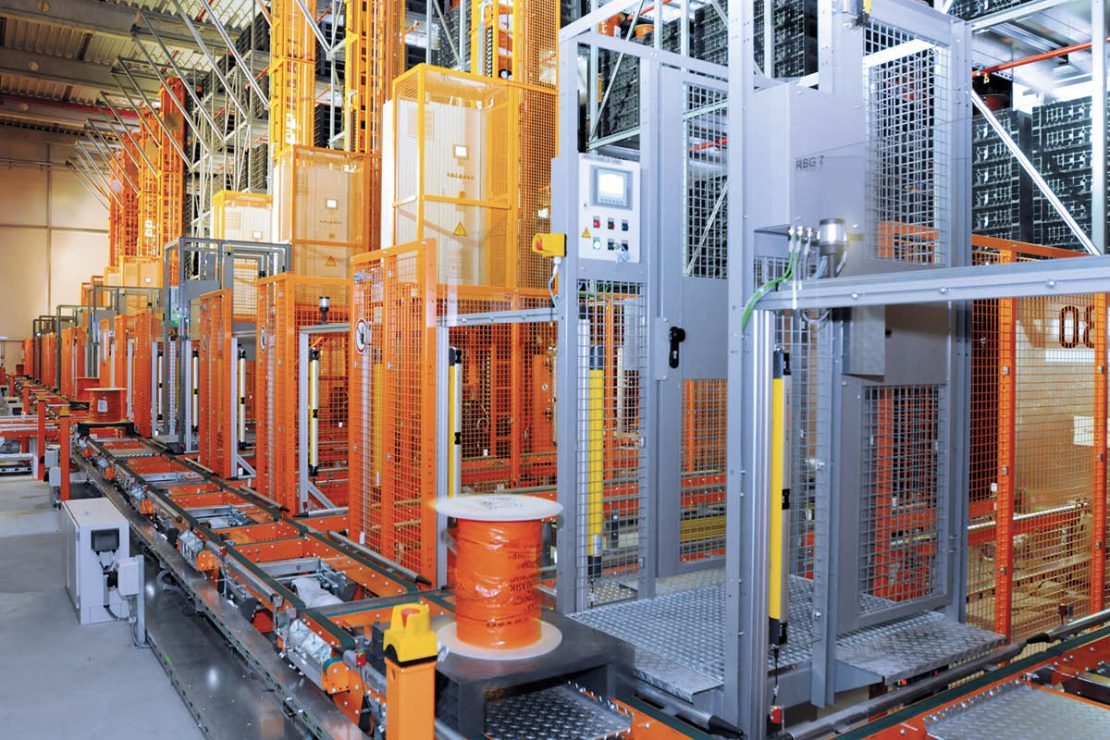
In the second project, four students took a closer look at the topic of long lengths. They examined how the use of large drums could increase logistics efficiency in terms of costs, delivery times and sustainability. To elaborate: At present, the production plant in Forbach (France) supplies standard lengths of 100, 500 and 1000 metres. If Forbach were to increasingly supply large drums of 10,000 metres to Ludwigsburg instead, there would be several advantages:
- Customer orders can be fulfilled more quickly from Ludwigsburg.
- The use of one large drum instead of several small drums reduces set-up times and lowers process costs.
- Stock levels can be optimised.
- Cutting from a large drum results in up to 85 percent less scrap – which saves costs.
- Simpler incoming goods processes.
- Sustainability in packaging. Instead of packaging each small drum with film, only the large drum has to be packaged.
- Less journeys from Forbach to Ludwigsburg and CO2 savings
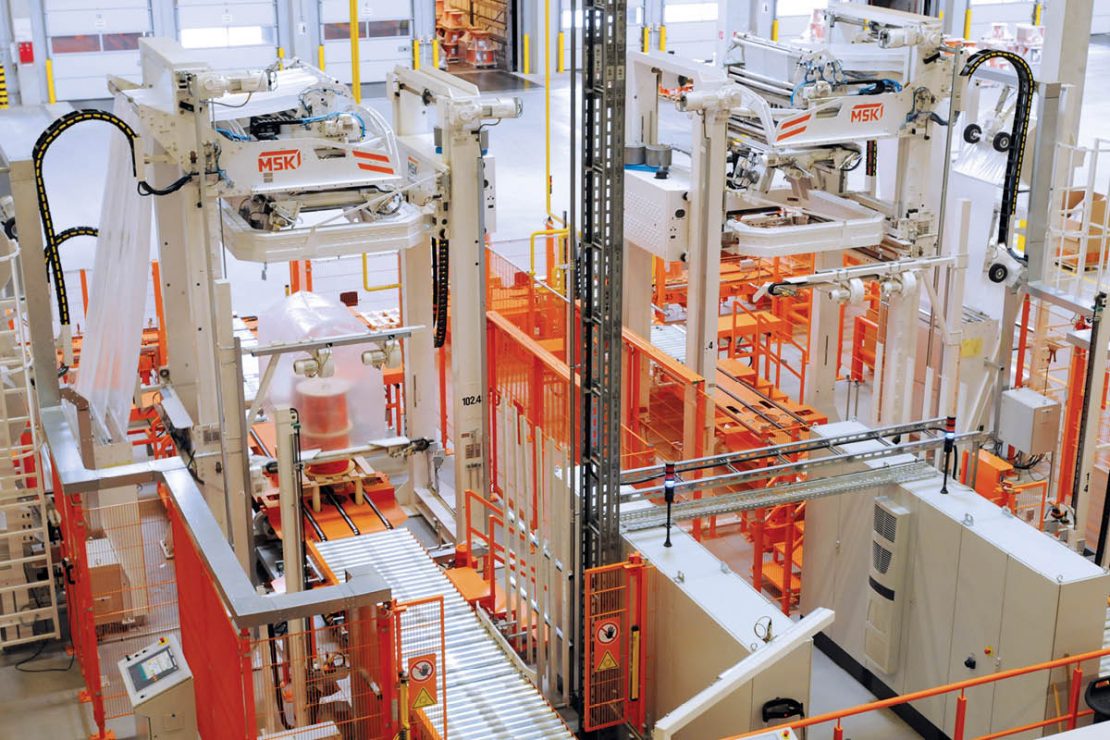
Johann Zimmer: „For individual articles such as the ÖLFLEX® CLASSIC 110, we have already switched to large drums. However, further conversion to large drums requires major changes in IT and additional investments. The additional effort involved in cutting also has to be taken into account.“
LAPP will also be offering projects for students in the current semester. Prof. Susanne Hetterich: “Our students’ joint projects on the Technical Logistics Management course with our partner companies are a win-win situation for all sides. Our students can apply their learnt knowledge to a practical problem and the partner companies have, on the one hand, the opportunity to bring in new unbiased perspectives and know-how and, on the other hand, can get to know future skilled workers and, possibly, recruit them for the company at an early stage.”
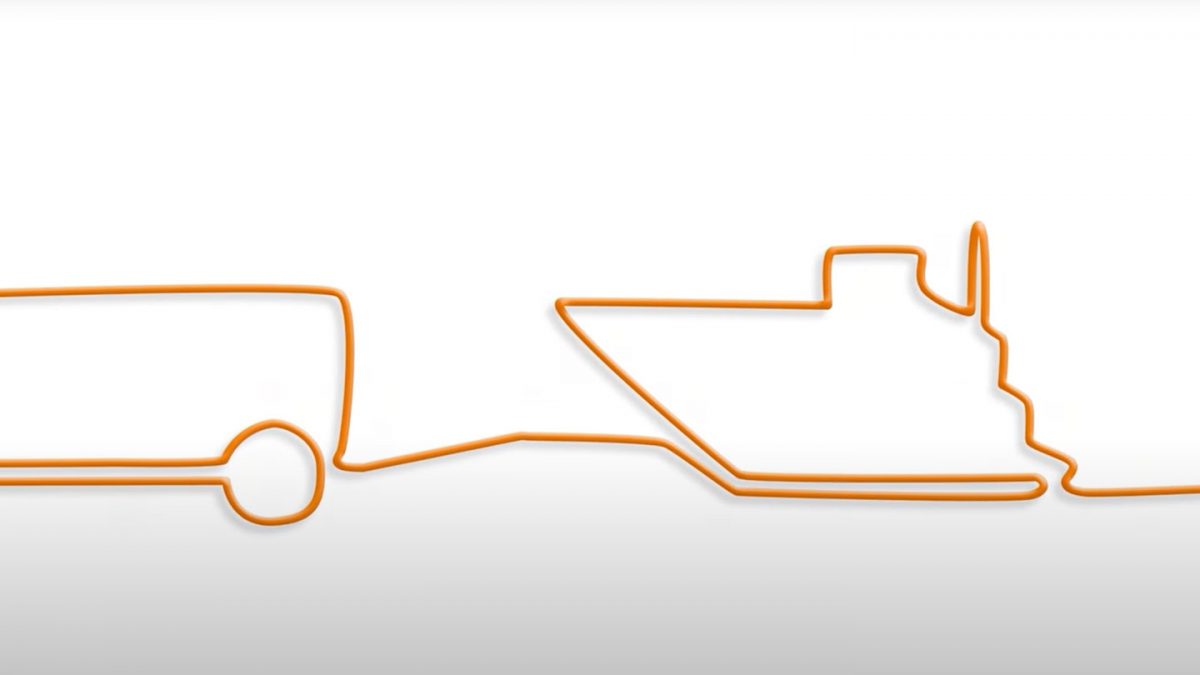
Video: © LAPP Logistics – There for you worldwide