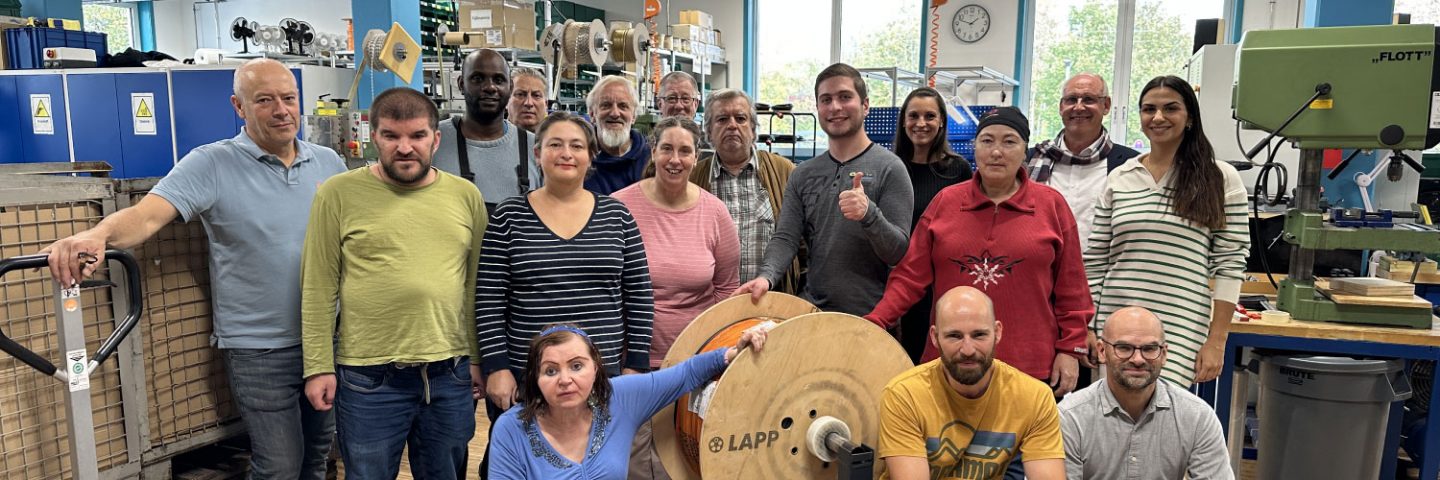
8 a.m.: Start of work at the Donau-Iller Werkstätten in Ulm-Böfingen. Before the members of the team head to their workstations, they hold the morning meeting. This is where tasks are assigned and information about new developments is provided. Anyone who isn’t feeling well can be assigned easier work. The group leader Peter Bopp and his colleague try to avoid pressure and piece work. The Employees don’t just have the assembly in mind but also, above all, the people: they are team leaders, supporters and care staff at the same time. Around 1,300 ‘clients’ – as people with mental, physical and psychological illnesses are called here – work in Böfingen and at the other five Donau-Iller Werkstätten sites in the Ulm and Neu-Ulm area, which are run by Lebenshilfe Donau-Iller.
One of the clients is Ms Tarar, who was overwhelmed who was overwhelmed in her previous job in elderly care and was no longer able to work, and she was no longer able to work. For the past six years, she has been “happier and more satisfied than ever” in the in the work centre in Böfingen where she works in electrical assembly. She has previously tried out housekeeping and packaging, “but I like it best in electrical assembly”, she says, smiling.
Cable assembly for renowned customers
The work centres work closely together with companies from the region. Böfingen, for example, has specialised in the assembly of cables in the electrical department. Customers include manufacturers of motorhomes, industrial welding plants, cooling units for lorries and material testing machines. Many customers have been manufacturing here for 30 years and are thus contributing to successful inclusion. There is no mass production in Böfingen. Unlike other facilities that only deliver large quantities, the work centres specialises in small quantities of up to a maximum of one thousand pieces.
The collaboration with LAPP has been around almost equally as long – since 1996. The contact came about because many work centres customers prefer to use cables from LAPP for quality and delivery capability reasons. “Quality is also very important to us, which is why we like to use LAPP components”, says an employee responsible for procurement in Purchasing. He either orders directly from Joachim Hentschel, who manages the work centre as Account Manager at LAPP, who manages the work centress as Account Manager at LAPP, or the components are made available via the customers who order them from LAPP. 90 percent of the cables are of the ÖLFLEX® Truck 170 FLRYY type, which LAPP produces in its largest plant, Câbleries Lapp in Forbach, France.
The Donau-Iller Werkstätten
The Donau-Iller Werkstätten have been around for 40 years. The six work centres in Neu-Ulm, Illertissen, Senden, Blaustein, Jungingen and Böfingen employ 1,300 clients. There are also 80 external jobs via the Centre for Work and Education and 40 employees at the inclusion company ADIS.
In Böfingen, there are currently 158 clients with psychological illnesses who are looked after by 48 employees. Areas of work in Böfingen include electrical assembly, housekeeping, wood processing, cable assembly, metal processing, assembly and textile processing. Around a dozen companies from the region are customers, mainly purchasing small quantities from the work centres.
The parent of the Donau-Iller Werkstätten is the Donau-Iller counselling organisation, which supports around 2,500 people with disabilities at over 30 sites in the region of Ulm / Neu-Ulm. It offers a large network of counselling, education, care, leisure and work opportunities with the aim of making inclusion more innovative and human.
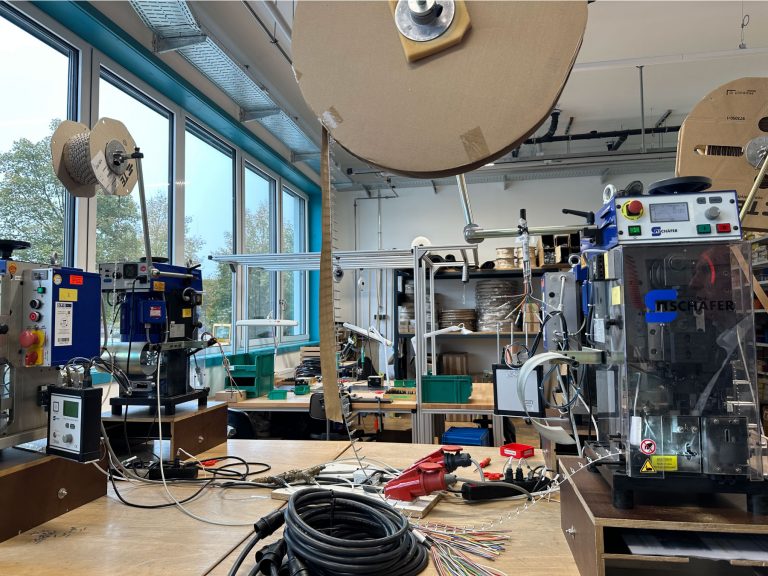
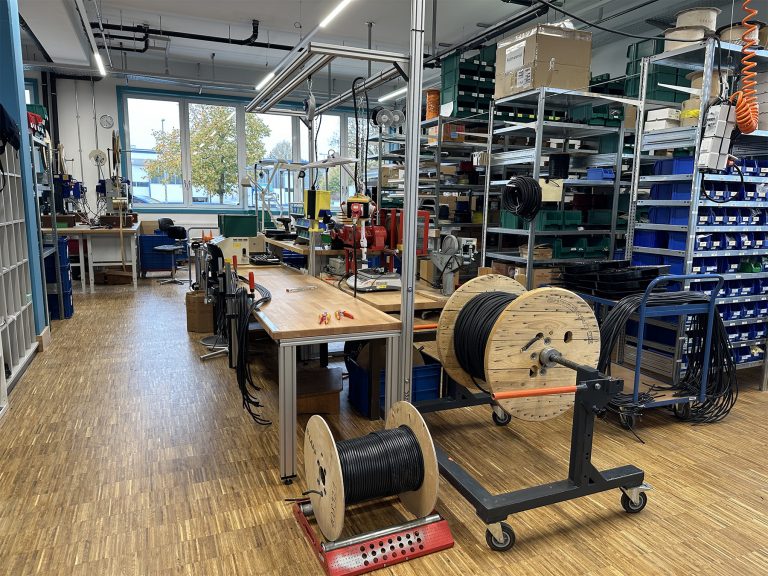
Quality instead of complexity
The quality of LAPP cable pays off for clients too, as it makes their work much easier. The individual cores are always arranged in the same way in the cable and thus fit perfectly into the testing machines, without having to sort the cores in advance or laboriously cut them differently. At each workstation and at each sub-step, the clients independently test the quality criteria using specially adapted tools with visual and acoustic aids. One client independently programmed crimping monitoring and voluntarily comes to work earlier each day for this. “We encourage personal responsibility and train our clients well so that they can carry out quality management on their own”, says Peter Bopp. If mistakes occur, this is not the fault of the client. “In such cases, we are responsible as group leaders and need to explain the work steps better.” The aim is to train the clients in such a way that they notice or can prevent mistakes themselves, and that they learn from them.
LAPP factory visit
“No client should be overworked or under-challenged”, says one of the employees. The two group leaders for electrical assembly are responsible for finding just the right demands to place on each person, depending on their daily form. They break down work packages into small individual tasks so that the clients understand them and receive the right stimulus.
It is highly motivating when clients can experience where exactly their work is being used. For example, the 27 clients from the electrical assembly department went on a tour of a customer’s factory. A tour of LAPP’s cable plant in Stuttgart and the warehouse in Ludwigsburg is also due to take place soon. For similar excursions and other activities such as swimming, Nordic walking, IT courses and English lessons, each client has a monthly hourly quota available, which they can freely invest in what are known as work-related offers. “Every day here is different”, praises Ms Tarar, “There is still so much left for me to learn and I can continue to grow.”
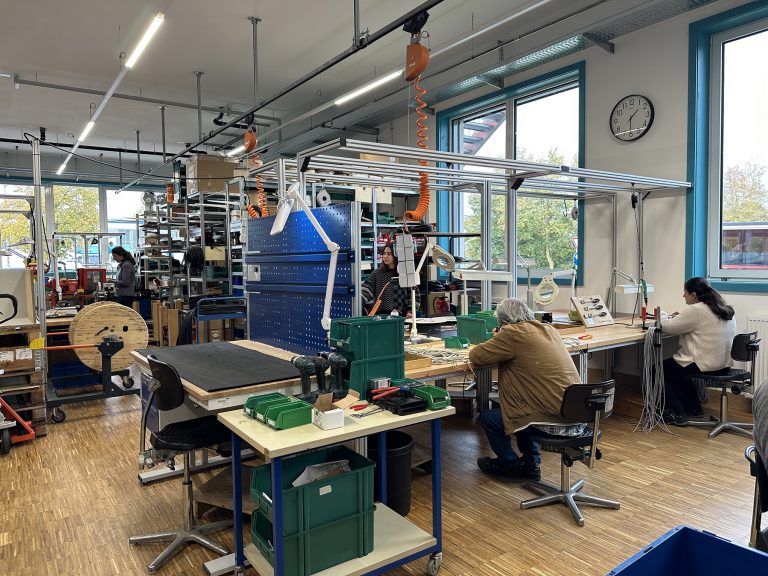