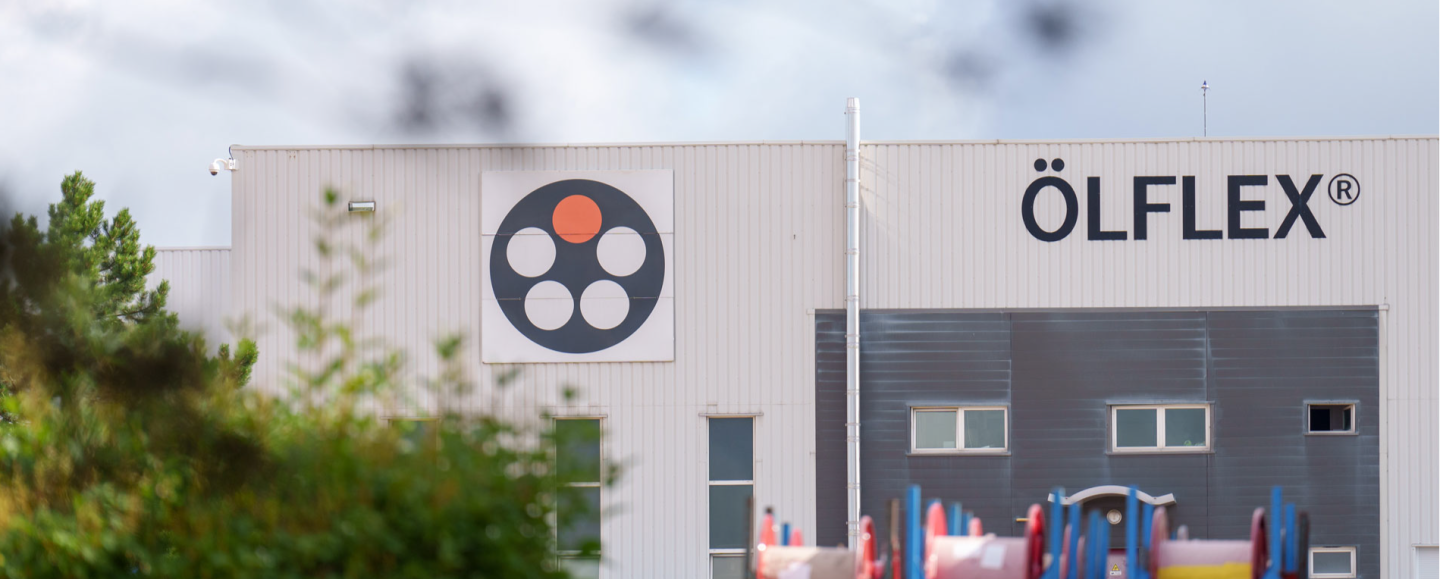
A turnover of 133 million euros, 260 employees, 120,000 kilometres of copper cable produced per year and a weight of more than a hundred fully loaded freight wagons: Câbleries Lapp in Forbach, France, is the largest plant in the Lapp Group, which operates a total of 25 production sites worldwide. In order to improve the productivity of the factory after numerous extensions and enlargements, management decided to restructure the production lines and in particular the value stream in the five halls. Over the next three years, 95 percent of the machines are to be replaced and a sixth hall will also be built. Ultimately, the objective is to double productivity.
Restructuring of the production plant is also the perfect time to tackle relevant optimisations with regards to energy and resource efficiency. Cable production, of course, requires energy, especially for the numerous extrusion lines where core and sheath material is applied. LAPP management told themselves this was also the best time to introduce new technologies for greater energy efficiency opted to design the supply of a new sixth hall and the adjacent hall with direct current. In recent years, the global market leader in the field of integrated cable and connection technology has helped to drive the development of DC technology (DC = Direct Current) and become a founding member of the Open Direct Current Alliance of ZVEI e.V.
Braking, recovering and saving
It’s a tempting idea. For years now, certain consumers in factory halls have used direct current, such as LED lighting, ventilation or direct current motors. The mains alternating voltage (AC = alternating current) has to be rectified for these, subsequently leading to conversion losses. It would be better if these were to be supplied directly with direct current. In addition, speed-controlled motors are operated via frequency converters with a DC intermediate circuit, e.g. conveyor systems, welding robots or servo motors. In this case, the DC intermediate circuit can be supplied directly, thereby avoiding a conversion stage. The same is true with regards to energy generation. Photovoltaic systems generate direct current and batteries always accumulate this. A direct current grid would additionally facilitate recovery of braking energy from motors e.g. in the dynamic movement of large masses, and reuse of this directly in the factory grid, as in the case of recovery in electric or hybrid cars.
In short, anybody serious about reducing energy consumption in production facilities should consider using direct current or implementing hybrid grids. A pleasant side effect of this is that, due to the disappearance of the third phase (with DC: DC+ and DC- and neutral conductors) and thus of a conductor in the cables and wires, as well as the higher voltage level of currently 650V deko and the resulting smaller conductor cross-section, DC cables require at least 25 percent less copper. This increases material efficiency and reduces costs.
Companies still probing
Direct current grids have not yet been able to gain a foothold within industry due to the topic only now emerging from research and entering the industrial implementation phase and, secondly, because even today not all components for DC are available with the necessary certifications yet (e.g. the required DC branches or AC-DC converters). However, this is improving thanks to the excellent groundwork carried out by the research project DC-Industrie and its successor project DC-Industrie2. There, the research partners, including LAPP, developed standards on how to build DC grids – known as the DC system concept. LAPP has investigated the effects of direct current on a cable and what needs to be considered here. As well as the different colour code for AC cables according to EN 60445 and the already lower number of phase conductors, a smaller cross-section can often be used due to the higher voltage selected. In addition, the influence of DC in the low-voltage range on the insulation material was investigated. The standardisation (UL 758) provides for identical tests for AC and DC cables. The insulation material can basically be used in the same way in the event of low voltage; for individual materials in combination with a very high moisture load, a higher penetration strength must be guaranteed. LAPP is meanwhile the first manufacturer to offer a comprehensive portfolio of ÖLFLEX® power and control cables for DC, which are suitable for various applications, from fixed installation to continuous movement in cable chains.
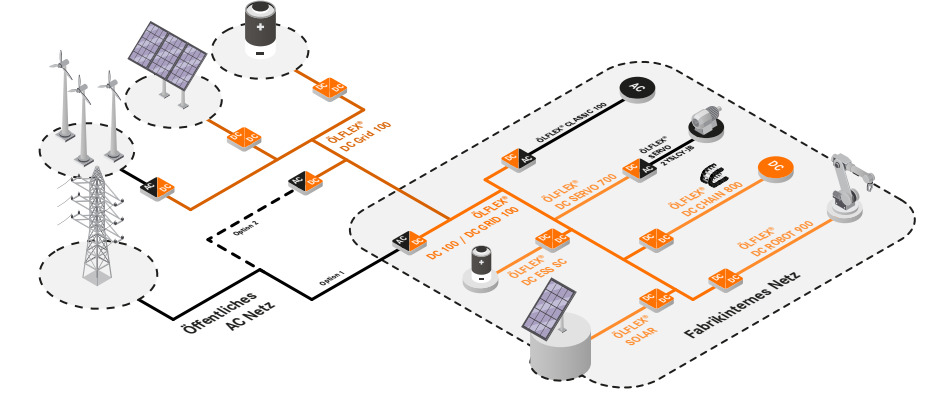
20 percent energy savings
Another reason that presumably makes potential users hesitate is the fact that there has been little experience with direct current in a factory environment to date. With the plant in Forbach, LAPP and the Fraunhofer Institute for Production Technology and Automation IPA in Stuttgart are planning to create a pilot that will act as guidance for other factory planners. As part of a concept study, the IPA laid the foundations for setting up a direct current grid with an inventory of the generators and consumers in the plant and a step-by-step plan. The costs and ROI were also taken into account, meaning that ten percent of consumers could be supplied with direct current immediately. Taken together, this amounts to 1.5 gigawatt hours per year. Above all, a high saving potential can be expected here, as these are motors for cutting lengths, in which large drums and thus masses are accelerated and significantly decelerated. This means that the energy no longer has to be diverted “unused” via resistors but is recovered in the grid. The planned equipping of the plant with photovoltaics and the construction of charging stations for electric vehicles will lead to direct connection of DC generators and other DC consumers to the grid.
Implementation with partner network
“For the time being, the direct current grid at the plant in Forbach is a concept study,” stresses Dr Susanne Krichel, Head of Innovation and Advanced Technology at LAPP. It is now time to check the implementation and the available components step-by-step. Initially, the DC network infrastructure will be built in Hall 6 “on the green meadow” and retrofitted in Hall 1. The photovoltaics on the roof are then connected to the building technology. In the next steps, more consumers will be added, taking advantage of the maximum power of the photovoltaic system. In the long term, all electricity consumers could be connected to the DC grid, with recovery and battery accumulators, if necessary, playing an important role. If everything goes according to plan, the other halls will also be converted to DC, adds Eric Lebert, Technical Conductor at Câbleries Forbach.
They depended on partners, “because with direct current, there is no company that can do everything,” said Krichel. At the same time, technical development continues. Companies from the ODCA of ZVEI e.V. are working on an AIC (Active Infeed Converter) that better coordinates the AC and DC grid and thus reduces peak loads. Experiences with a supplier of DC components that has already converted an entire factory to direct current shows that the maximum peak power that the operation receives from the grid has significantly reduced. The company saves a lot of money because it gets significantly more favourable terms from the electricity provider.
Susanne Krichel believes that a factory that works 100% with direct current is possible, but not likely – the future will be in hybrid networks and grid concepts adapted to the needs of the factories. “What is feasible and what makes economic sense? Our goal is to answer these questions in Forbach.“
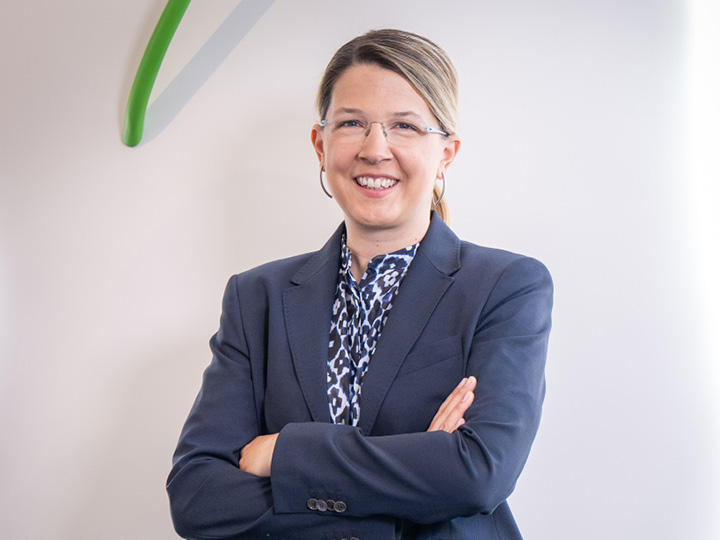
LAPP Whitepaper „Calculating the cable cross-section for direct current”
Benefit from the knowledge of our DC experts. The guide will help you calculate and select cable and wire cross-sections for AC and DC systems.
Download LAPP Whitepaper