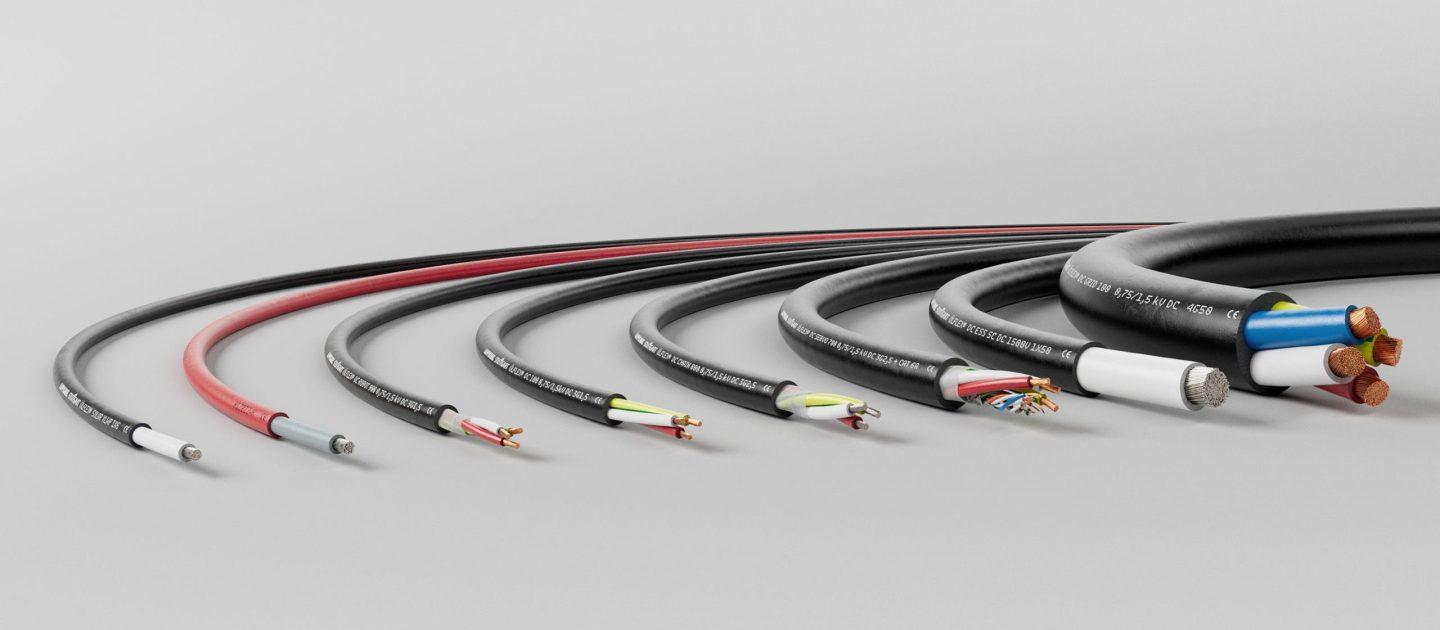
Specifically, the LAPP experts are researching the long-term stability of insulation materials for cables and the insulation strength of the core insulation used, since cables for direct current applications age differently from cables designed for alternating current. In addition, together with partners in projects and the Open Direct Current Alliance (ODCA) the global market leader for integrated solutions in the field of cable and connection technology works with network structures, earthing and regulation of the networks in terms of stability and storage design and error monitoring management. These are all topics that are becoming relevant when thinking about DC.
The idea of converting industrial production facilities to direct current has a long history. Industry and research have been working together to implement the energy revolution in industrial production for some time now. However, this will only work if companies such as LAPP disseminate knowledge about direct current networks. For this reason, LAPP is a founding member of the ODCA (Open Direct Current Alliance), which was formed in 2022, the successor project to DC-INDUSTRIE and DC-INDUSTRIE2, and also offers the world’s first direct current portfolio in the field of connection solutions. Long ago, the Technology Advisory Council, which advises LAPP on future-oriented technological issues, identified DC as a trending topic. This enabled LAPP to reposition its global research and development, as well as the management of laboratory and test centre activities, and to align them with flexibility and agility to this topic.
“We are increasingly living in a DC world,” says Guido Ege, Head of Product Management and Product Development at LAPP, summing this up. “The long-term abandonment of fossil energy sources can only be managed efficiently if we consistently switch more and more to direct current and avoid conversion losses.”
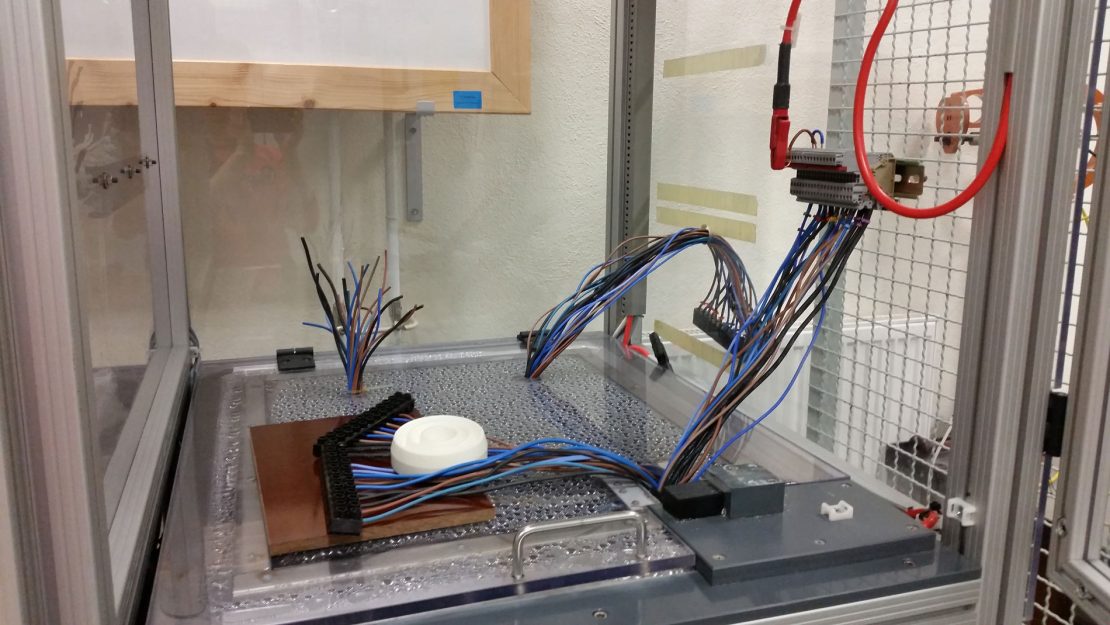
Save money and resources with direct current
After all, through the elimination of individual conversion stages or of complete converters, conversion losses can be reduced or even eliminated altogether. In this way, a considerable amount of energy can be saved. The transmission losses for cables and wires are also lower than for alternating current. More than 10% can be saved here in terms of energy. Calculations show a saving of just over 3 to 4% when recovering and using energy in motors and drives (recuperation), since the braking energy can be used and fed back in more easily when using DC. At the same time, energy losses are lower. This is due to the higher DC mains voltage, which leads to lower conductor currents and the inapplicability of idle power. In addition, photovoltaic systems, for example, generate direct current that no longer needs to be converted into alternating current.
There is also potential for savings if we consider the resources required. For instance, there is no need for electronic components such as converters, conversion stages and filter systems. On the other hand, significantly less copper and conductor materials are required for direct current too. This is due to the lower number of cores in the cables (3 instead of 4 or 5 cores) and the smaller conductor cross-sections required. This is possible thanks to a smaller current flowing at a higher DC voltage, which transports the same power as alternating current. A saving of around 25 percent on copper is possible here. This can be seen, for example, in the ÖLFLEX® DC 100 from LAPP, which is used, for example, in plant and mechanical engineering and is designed for energy-saving use in DC networks for industrial plants.
Saving potential for commercial storage
Purchasing electricity is currently becoming increasingly expensive, making the finding of places where energy costs can be saved of particular interest to factories. The switch to direct current also offers great potential here, as the technology reduces failure costs by providing better protection against power cuts, thus preventing potential downtime in production and data processing. Early fault detection can be achieved in modern DC networks through digitalisation and ongoing monitoring. In addition, if the factories have their own photovoltaic system, for example on a flat roof, depending on the design, part or all of the company’s own requirements can easily be covered from their own supply source.
In order to further reduce the grid fees, it is worth taking a look at what are known as commercial storage systems, i.e. energy storage systems used in commercial and industrial environments. These allow companies and traders to store excess energy and summon it as necessary. They can be implemented in different ways, including battery storage, thermal storage, compressed air storage and other technologies. In this way, they help to cover energy requirements during peak periods, stabilise the power supply – and reduce costs. If there are no converters and switches for connecting battery storage systems, energy can be obtained more quickly and efficiently in DC networks. This means that the energy can be efficiently stored or purchased for a later date without any conversion losses.
Essentially, anyone setting up a new factory today should consider direct current, particularly in production applications with high power requirements (e.g. arc welding or other welding applications) or factories that generate power themselves on site using renewable energies. DC is just as important for systems that control, position, accelerate and brake devices and machines precisely using a variety of servo drives, for systems with robotics applications in which dynamic movements are performed and for large office buildings.