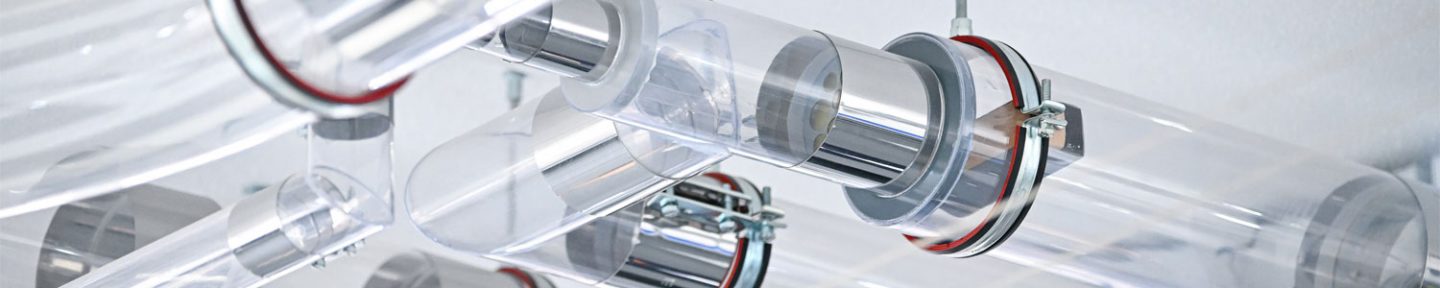
The history of the pneumatic tube goes back to the mid-19th century, when the English engineer Josiah Latimer Clark built the first functioning pneumatic tube system to transport telegrams within the London Stock Exchange. In Germany, Heinrich von Stephan, who later became General Post Director of the former German Reich, introduced the system for transporting messages and objects. The pioneering system was put into operation in Berlin on 1 December 1865 and connected the main telegraph office with the stock exchange over a distance of about one kilometre.
Over the years and decades, the pneumatic tube networks became longer and longer, sometimes covering several hundred kilometres, and increasingly sophisticated. They were used in particular in large cities such as Paris, Vienna and New York to send smaller objects, letters and information quickly and securely to telegraph offices, banks, ministries and newspaper editorial offices.
Systems that stand the test of time
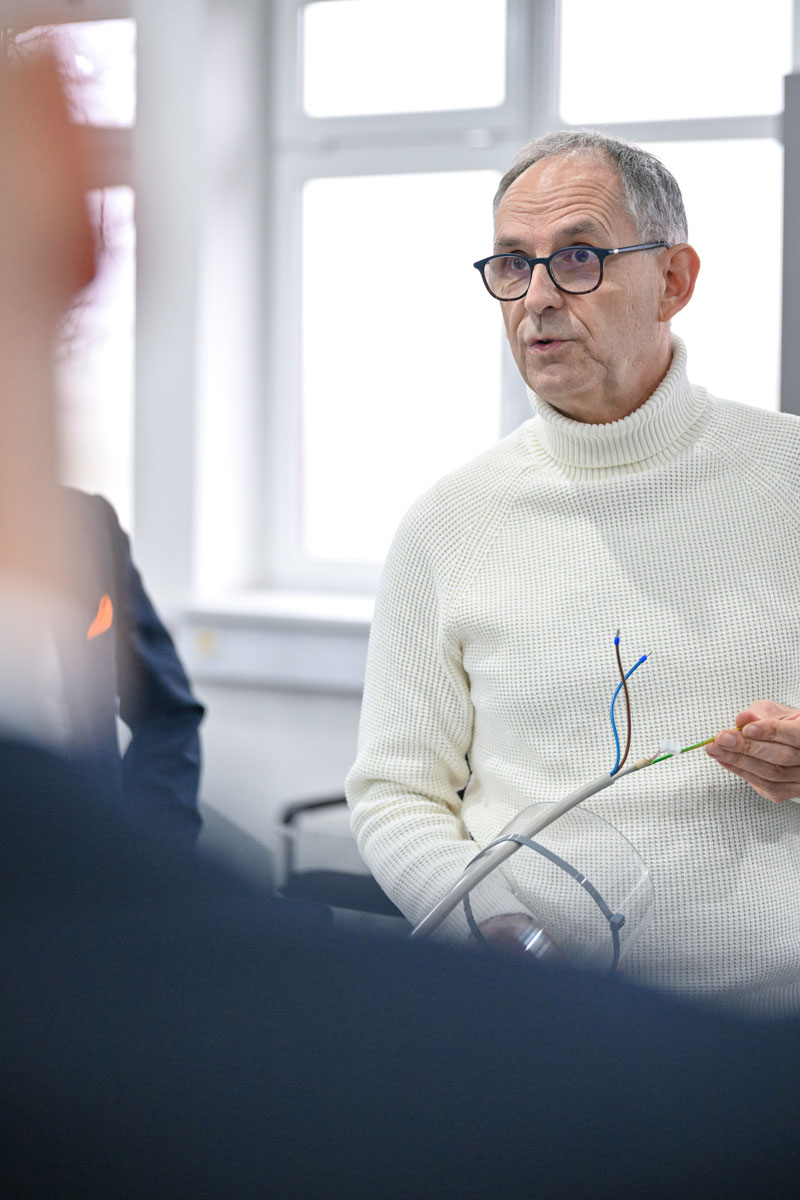
‘Today, most people are familiar with pneumatic tube systems from hospitals, for example for quickly sending blood samples to the laboratory or blood products directly to the operating theatre,’ explains Jürgen Wörle of aerocom. ’This is also correct, but it is also used, for example, in industrial plants, supermarkets, pharmacies, banks and large companies.’ The company, based in Schwäbisch Gmünd, has been producing and selling pneumatic tube systems for a wide range of customers since 1956. The basic principle of how the carriers are sent through the tubes has not changed much over the years since the company was founded or since the communication system was invented.
The systems consist of a system of plastic or metal tubes in which cylindrical containers, known as carriers, are transported. The system has various insertion or removal points, including flaps or locks, that can be controlled. A control centre can be used to regulate the air flow and direct the carrier to the correct station. The transported goods are moved by means of compressed or suction air, which pushes the carrier through the pipes at a speed of approx. 6 to 10 m/s, or by means of a vacuum that sucks the containers from the target point. Automatic points and a sophisticated electronic control system guide the carriers to the correct target stations.
Safe transport systems and works of art
‘We have a range of different customers,’ explains Jürgen Wörle. ’On the one hand, customers who use the pneumatic tube system because it is particularly fast, safe and reliable, and on the other hand, special projects that turn our systems into works of art, so to speak.’ The first group includes petrol stations, for example, which use the system to transport cash safely and discreetly to the in-house safe after the payment process, thus eliminating the need for robberies. Or steelworks, which have to quickly send hot steel samples in aluminium or stainless steel capsules to laboratories in order to adjust mixing ratios if necessary, thus losing as little production time as possible. The second group includes, for example, an installation at the Munich Patent Office and a cruise ship that has added a pneumatic tube system to its slide facility to transport glasses worn on the slides back to the slide entrance.
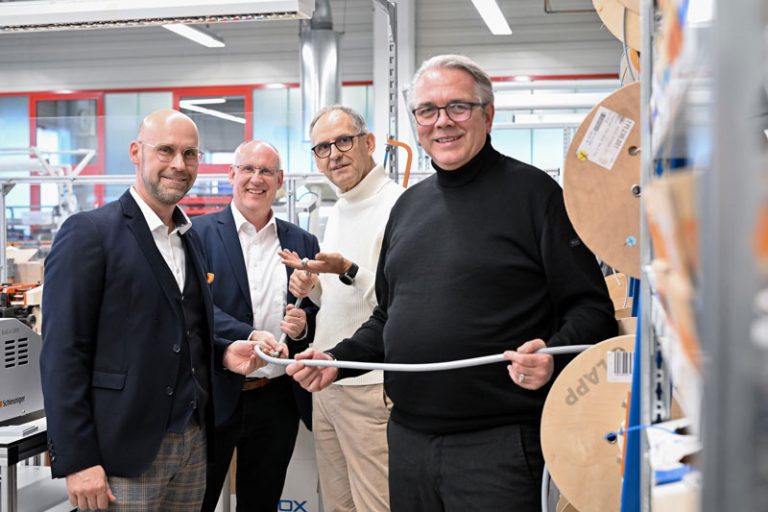
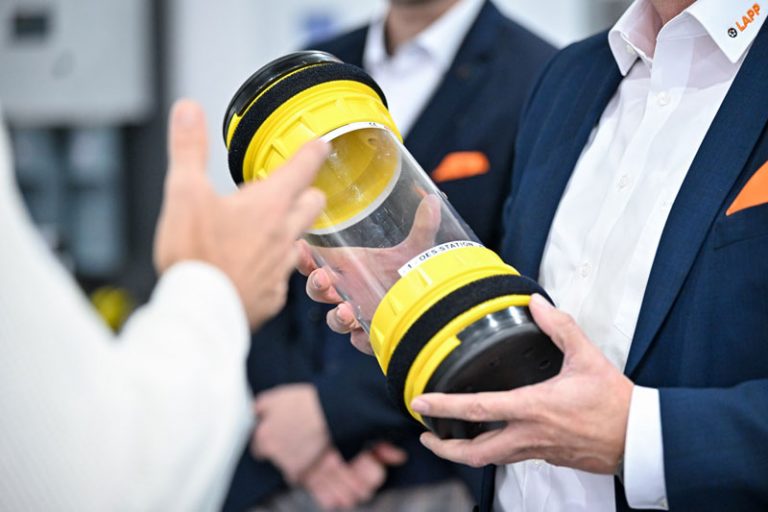
But how could the technology survive the many new communication options that have emerged since its invention? ‘It’s all to do with the way it’s transported,’ says Jürgen Wörle. “In hospitals, where a lot of things are time-critical, it’s quite simply the fastest option for getting something from A to B. It’s also reliable, safe, cheap and extremely durable.” When sent via pneumatic tube, data cannot be easily tapped, as can be the case with digital information, for example, through hacking. The simple yet intelligent technology behind the system makes people the biggest and almost only risk factor. Relatively little power is needed to operate it, the systems require little maintenance and both carriers and pipe systems only show signs of wear over a long period of time. ‘They even clean themselves, so to speak,’ says Wörle. Each carrier is equipped with carrier rings made of a soft fleece material similar to Velcro, which are used to reduce friction in the pipe system and to seal it for optimal use of the air flow. At the same time, they ‘sweep’ manually through the pipe system with each shipment and keep it dust-free. This is why pneumatic tube systems remain as popular as ever, with requests coming in from all over the world to aerocom.
Wanted: special cable that does double duty
What has changed over the lifetime of the pneumatic tube, however, is the amount of data that is generated for the control system, which has become increasingly complex. In addition to a reliable power supply, the systems also require a control cable that can transmit all data quickly and securely. One sticking point with pneumatic tube systems is that ‘it would be very difficult to lay two cables when installing the systems,’ says Jürgen Wörle. ‘That’s why we needed a special cable that combines both power and data and saves us space and a lot of time during installation.’
aerocom finally found the solution at LAPP. The world market leader for integrated solutions in the field of cable and connection technology developed a custom-made product for the customer. The customised solution combines power supply and data transmission in a space-saving way and with two different voltages in one cable. To ensure that this is technically safe, appropriate insulation is required. ‘The cable runs along the tubes of the pneumatic tube,’ explains Jürgen Wörle. ‘The 24 volts of the cable usually supply all devices and switches of the system with energy, so that the dispensing stations do not require any additional network connection.’ The customer receives two versions of the special cable from LAPP: in many cases, a cable with a PVC sheath can be used, but in areas with high safety requirements for fire protection, such as hospitals or public buildings, aerocom uses a halogen-free variant. Since aerocom places great value on the exact product properties of the special cable, no other cable from aerocom’s partners may be used for the pneumatic tube systems.
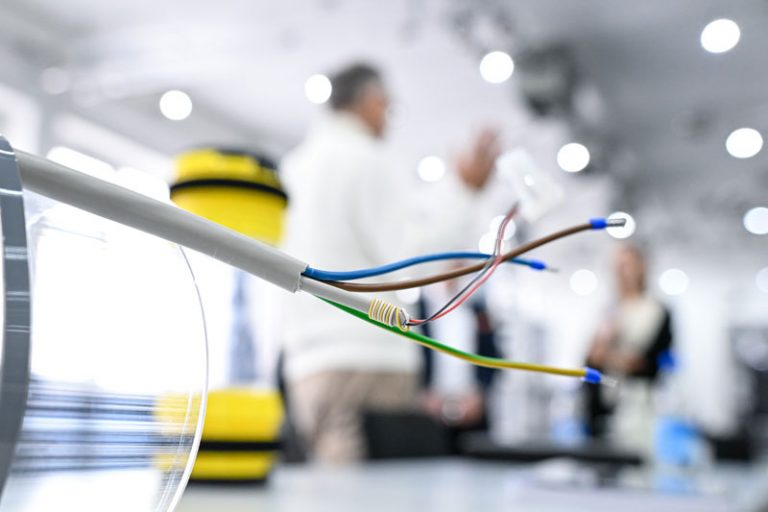
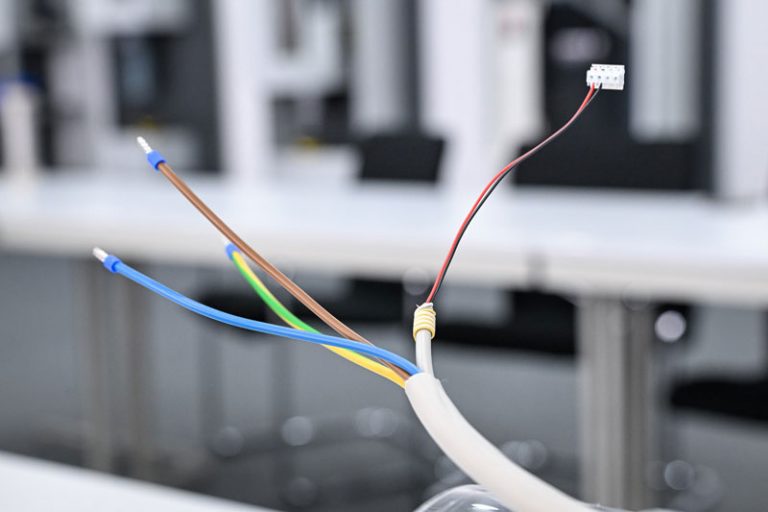
Tinkerers among themselves
‘As Swabian tinkering companies, LAPP and aerocom are a perfect match,’ says Jürgen Wörle, summarising the 15-year partnership between the two companies. “We distribute a high-quality product and therefore enjoy working with high-quality partners from the region. Proximity makes good cooperation much easier.” This has also helped them to get through difficult times together, Wörle continues. ‘Our cooperation has always been characterised by communication on an equal footing and mutual understanding.’
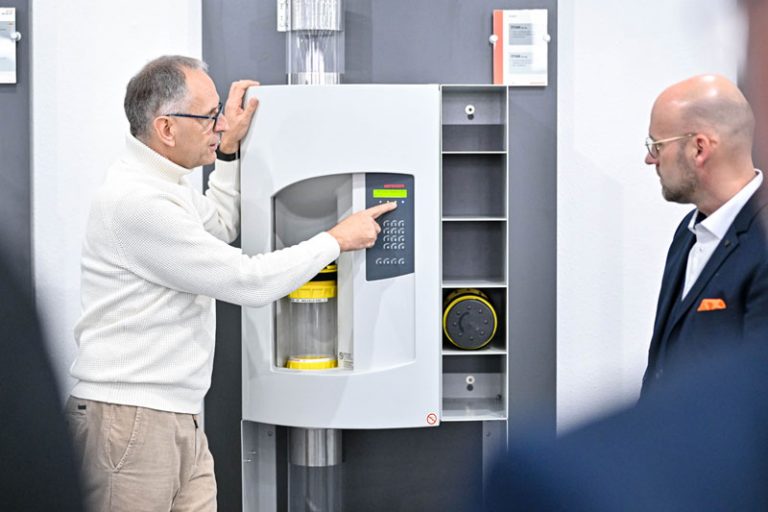
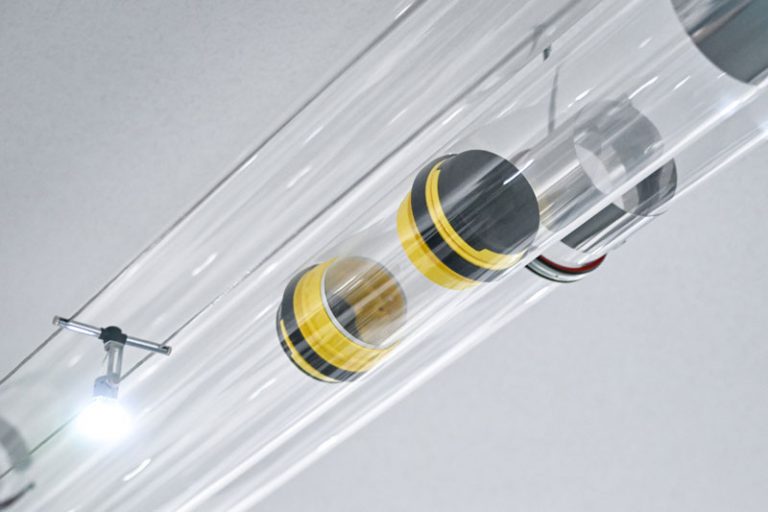
And so the cooperation is set to continue for many years to come – and the special line is even to be further developed. “With our systems, we are always at the cutting edge and therefore need components that can keep up,” explains Jürgen Wörle. Today, for example, all systems are centrally computer-controlled. For particularly large projects, such as the Heidelberg University Hospital, 4,000 carriers are sent every day through 35 kilometres of piping to around 190 stations on the premises. ‘All this generates a huge amount of data, which must be protected against electromagnetic interference,’ says Wörle. This is a challenge that LAPP is happy to continue to support aerocom with.
Aerocom GmbH & Co. Communicationssysteme
aerocom, the world’s leading manufacturer of pneumatic tube systems, was founded in 1956 under the name Aeropost. The company offers customised solutions for the fast and safe transport of materials and can look back on around 35,000 installed pneumatic tube systems. The systems are used in areas such as hospitals, industry, pharmacies and retail. The company has a high level of vertical integration and offers customers a round-the-clock on-call service.
Aerocom operates eight subsidiaries in Europe, Asia and Australia, employs around 135 people in Germany and around 120 abroad, and unites 85 partners and subsidiaries around the globe.