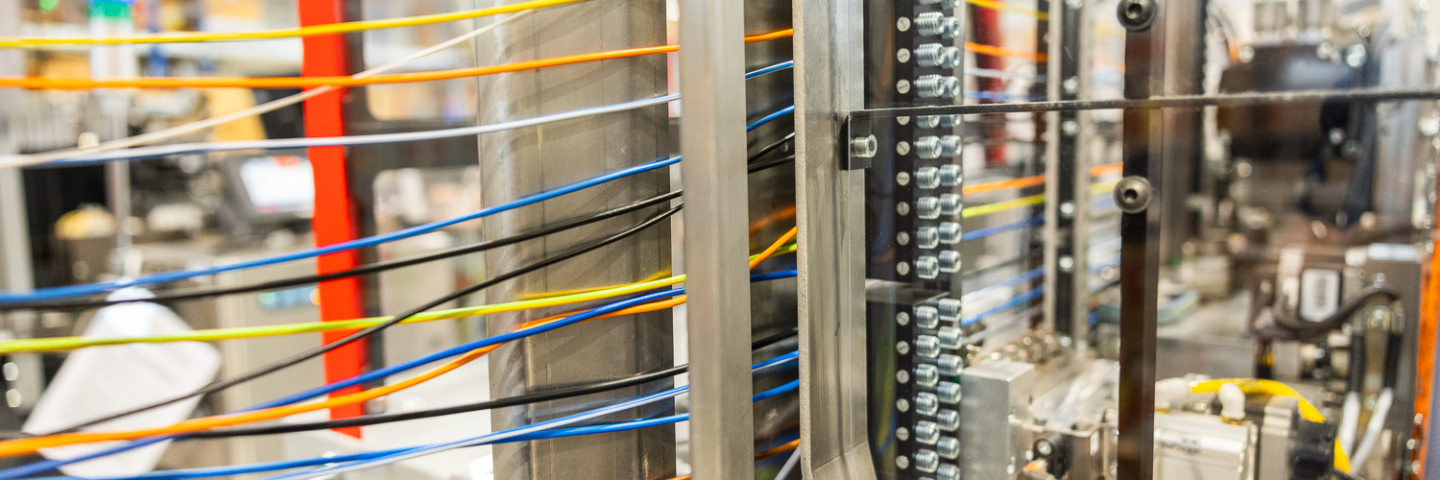
Imagine a tangle of colorful wires, carefully bundled and neatly laid in control cabinets. Each strand has a precise purpose. These works of art are usually created by skilled electronics engineers who can read and understand complex circuit diagrams in order to connect the correct strand to the intended component. A time-consuming task that requires a high degree of precision. This is because the single-core wires have to be cut to the correct length and labeled in advance, the ends have to be stripped and then fitted with a ferrule. But what if there was a time and cost-saving solution to this problem? WUSTEC, a company from Dunningen-Seedorf in Baden-Württemberg, is pursuing precisely this goal. The company is revolutionizing switchgear construction with pre-assembled and printed wire harnesses.
A visionary speaks straightforwardly
Ralph Schmid, founder and Managing Director of WUSTEC, has been in the business for over 20 years. He is surprised that “control cabinets and electrical systems are often still wired as they were 30 years ago”. His now more than 200 customers prove how things can be done differently. “By using fully automated wire harnesses, our customers save up to 80 percent in assembly time”. What’s more, customers no longer need highly qualified specialists, as pre-assembly simplifies wiring considerably. And pre-assembly offers yet another advantage: there is no strand waste.
From a garage company to an internationally active company
WUSTEC was founded in January 2000, when Ralph Schmid was 24 years old and working for a switch cabinet manufacturer. When his employer was offered a machine for printing single wires, Schmid immediately recognized the potential. With his confidence that printing the strands could optimize switch cabinet construction, he was also able to persuade his bank to grant him a credit for the purchase of the machine. Initially, Schmid ran his company on the side in a rented garage. Here he started out as one of the pioneers in the industry with printed wire sets.
In tune with the times
The fact that WUSTEC is doing so well is also due to the fact that Schmid is constantly looking for innovations. The company from the Black Forest was one of the first to use ultrasonic compaction, a process in which the wire ends of stranded wires are compressed into a single unit. This eliminates the need for ferrules and optimizes electrical conductivity and contact resistance. As no machines for automated ultrasonic compaction were available on the market for a long time, he initially supplemented one of his KOMAX machines for printing and assembling the strands with a device for ultrasonic compaction with the support of KOMAX, the world market leader in automated cable processing. And because Schmid is constantly looking to optimize his production processes, this is by no means the only home-made device to be found in the Swabian inventor’s modern production hall.
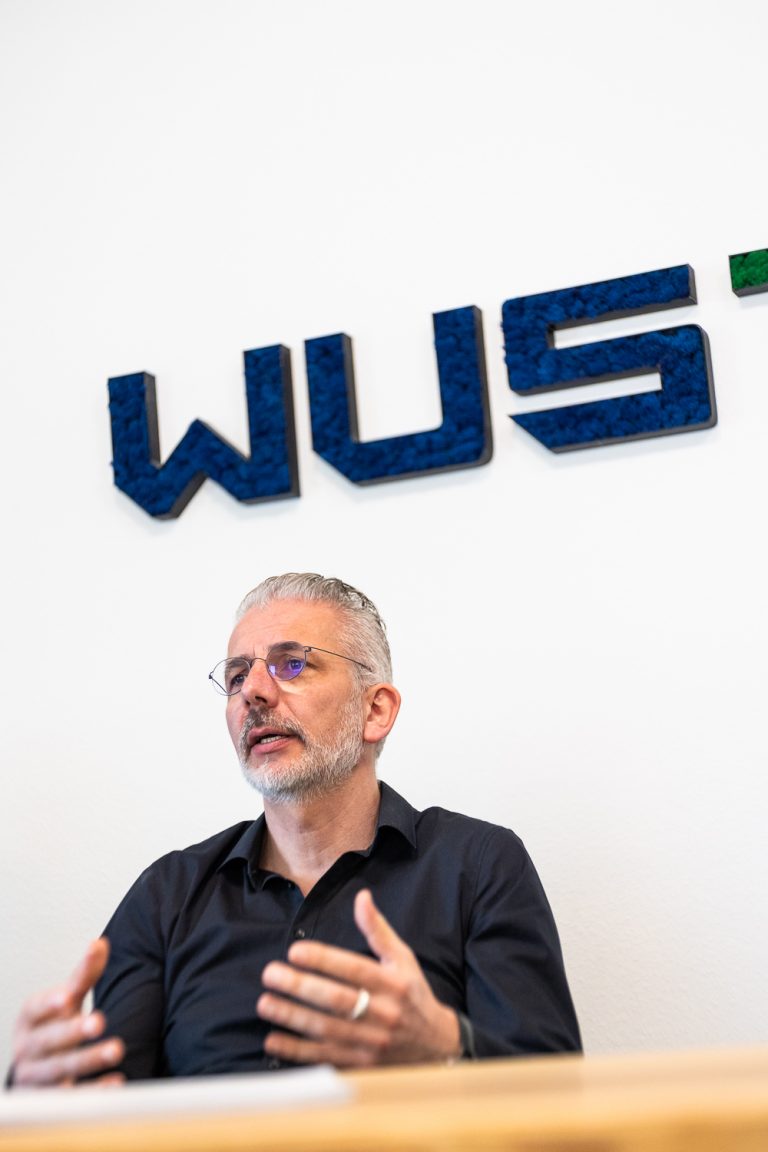
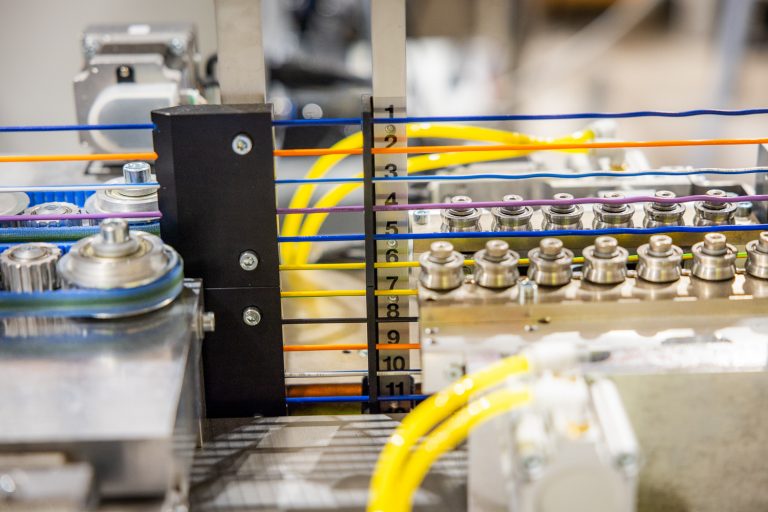
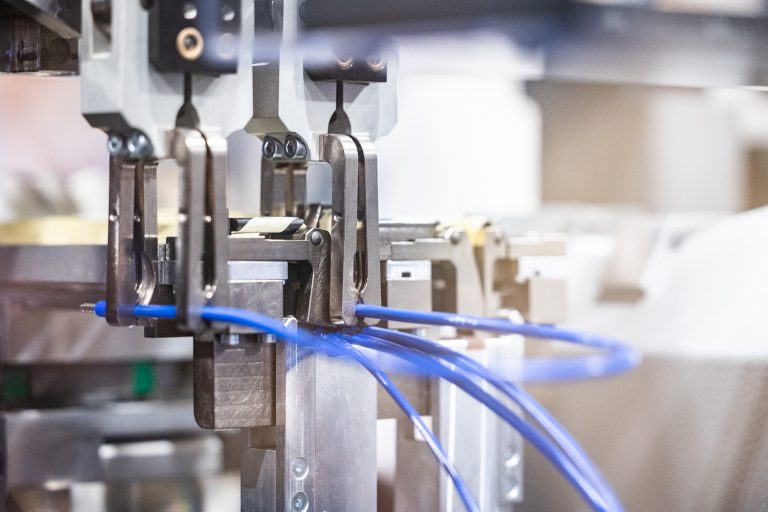
Digitalization for automation
Schmid is also setting standards in digitalization with his Wiremaster bundling software. Before WUSTEC became a member of the KOMAX Group in 2023, Schmid had already invested a lot of time and money in programming the software. But it was only with the support of KOMAX that “development really took off”, explains Schmid. And because he is always on the lookout for optimization potential, functions for processing production data or for production control, for example, are currently being further developed. The aim is to use the software to make in-house production more efficient. In the future, customer orders are to be managed in such a way that the internal changeover time can be optimized. A glance at the production hall shows just how much effort is involved. Dozens of different colored strands can be found on the shelves and have to be manually fed into the assembly machine as required.
Right from the start
Schmid’s strength of will, drive and vision not only convinced his bank, which financed the first machine. Peter Marx, a former sales employee at LAPP, also immediately recognized “the great human and entrepreneurial potential of the company founder”. He was certain from the outset that “WUSTEC would grow”. And because start-ups need support, Marx supported Ralph Schmid with his expertise and suitable materials “so that the new company could gain a foothold in the market”. A decision that paid off. Today, WUSTEC prints and assembles around 7,000 kilometers of cable a year with 27 employees. Many customers specifically request ÖLFLEX® connection and control cables. For Milena Bialas, the first trainee at WUSTEC and now responsible for Operations and Human Resources, “ÖLFLEX® is the established brand in the cable industry”, and therefore synonymous with quality and market leadership. An assessment that Schmid shares: “In many areas, ÖLFLEX® is simply set as the standard.”
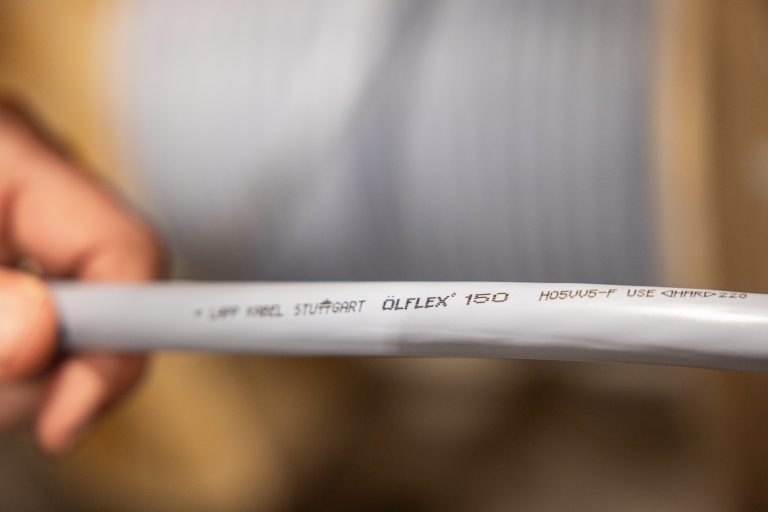
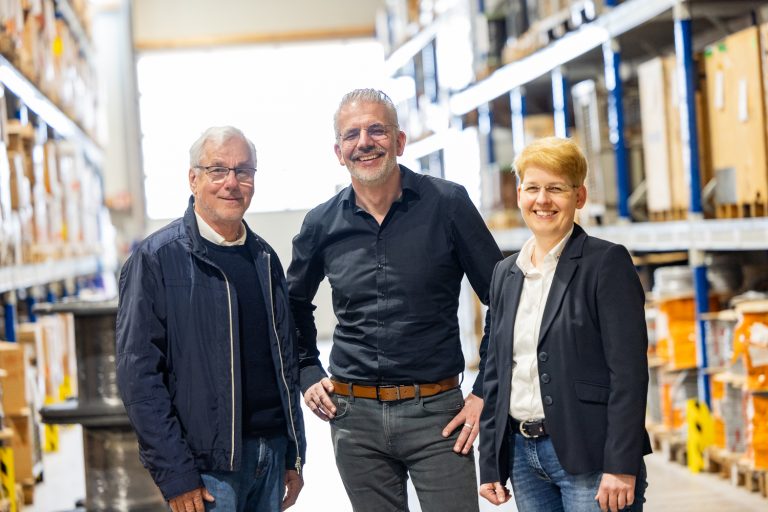
Cooperation at eye level
But it is not only the product quality, the variety of articles or the high level of reliability that make LAPP an “indispensable partner for us”, says Schmid. The cooperation is also excellent. “LAPP always treats us as equals,” Schmid emphasizes. The exchange between the leading provider of integrated solutions and branded products in the field of cable and connection technology and WUSTEC continues to be close. Schmid particularly appreciates LAPP’s flexibility. “They also supply us with partial quantities of rarely required strands, which relieves us financially,” says the Managing Director. The supply of large cardboard boxes, from which the cables can be fed into the WUSTEC machines more easily than from the cable drum, is also a project “with which we support automation,” says Janine Kuhlmann, sales representative at LAPP.
“Automation Ready”
One project that is particularly close to Schmid’s heart is cables that are “Automation Ready”. This refers to a cable with virtually no tolerances in terms of the cable diameter. This is a new requirement for manufacturers such as LAPP. According to Schmid, electronics engineers who wire a control cabinet as it was 30 years ago are not interested in how large the deviations are. However, if the start and end points are printed on the strands, things look very different. As the individual wires for printing are fed through sleeves in the machine, productivity depends heavily on whether the strands match the diameter of the sleeves. “Large tolerances mean that the cores have to be changed more frequently for the printing process,” explains Schmid. A problem for the entrepreneur, who also relies on in-house automation to reduce his costs. As “LAPP doesn’t just offer products, but solutions,” says Kuhlmann, quality managers and product developers at LAPP are also in close contact with WUSTEC. Kuhlmann is already certain: “Cables that are ‘automation ready’ have a future – and not just at WUSTEC.”
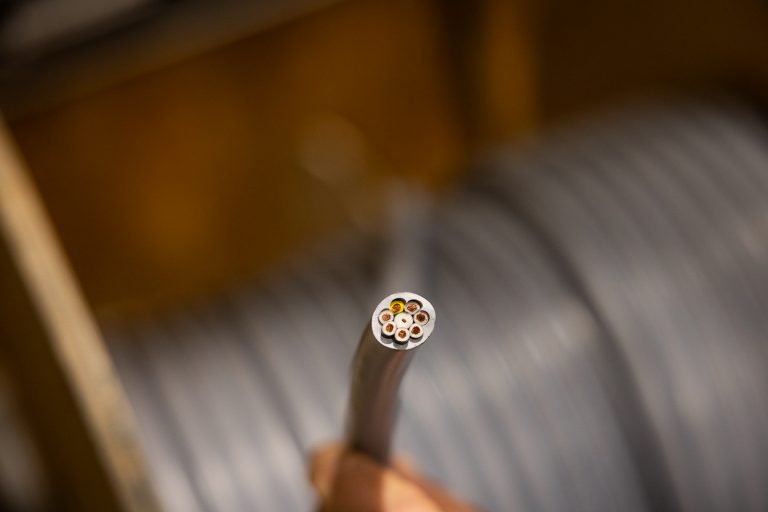
