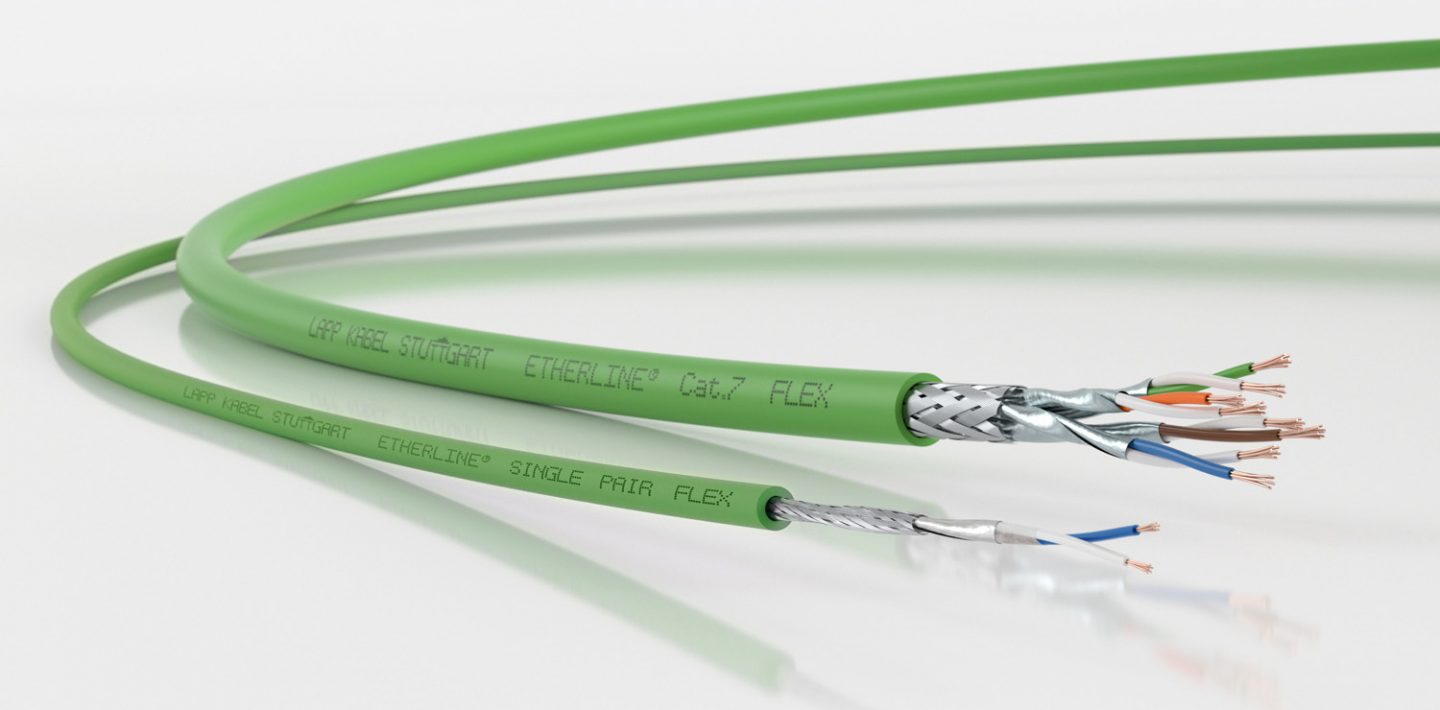
For decades now, fieldbuses have been used for communication in automation applications. However, they have increasingly been reaching their limits and have no longer been able to meet the communication requirements of modern SmartFactories. Replacing fieldbuses with Ethernet has resulted in new challenges, not least in the installation technology. While the best known example, PROFIBUS®, got by with a single pair of cores in the bus cable, PROFINET® needed two pairs for 100 Mbit/s Ethernet. In some applications, Gigabit Ethernet is already being used in factories, which requires four pairs of cores. The problem is clear. Compared to fieldbuses, there has been an increase in the field installation work needed and the potential for installation errors. As a result, Ethernet has not been able to establish itself at the lowest field level right down to individual sensors and actuators. Instead, special solutions with quick and easy installation have persisted. However, additional translators or gateways are required to connect these to the higher-level Ethernet. An integrated Ethernet installation with reduced installation effort would definitely be more advantageous.
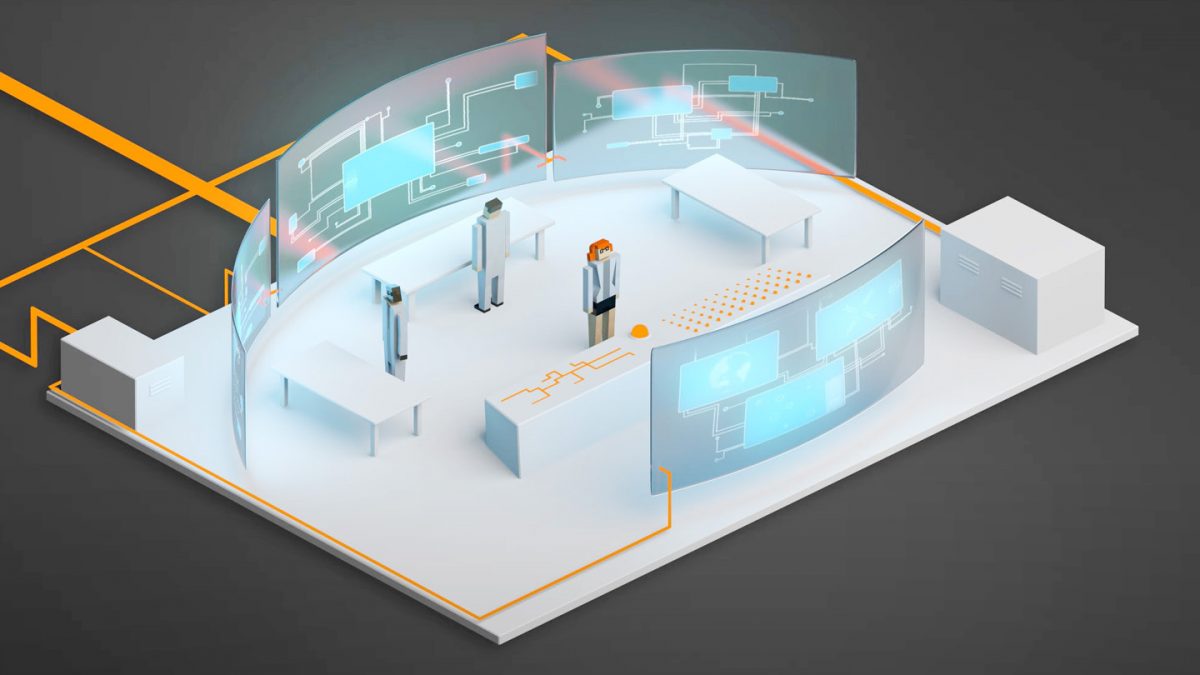
Video: Industrial Communication by LAPP – Your network from a single source
Single-pair Ethernet enables Ethernet-based communication via a single pair of cores. Thanks to the reduction to just two cores, the technology is very interesting for industrial automation applications. Connectors are primarily installed in the field, i.e. on site in the system. Here, installation work and installation errors can be considerably reduced. Furthermore, the cabling requires less space and can reduce component costs. Standardisation is an important factor for broad market penetration of new communication systems. Single-pair Ethernet is covered by several international standards. For example, three IEEE standards relevant to industry (see table) have been defined for different applications.
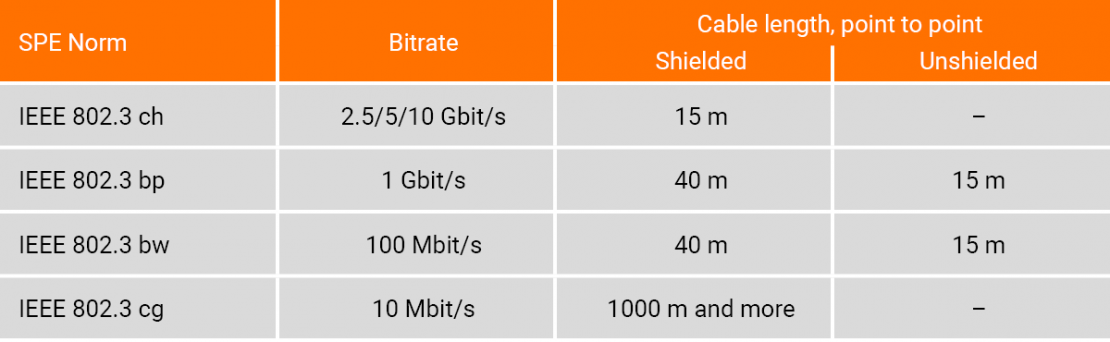
Single-pair Ethernet also considers the power supply for the terminal devices. With Power over Dataline (PoDl), it is possible to supply power to the Ethernet users via the data network cable, similar to today’s Power over Ethernet (PoE). This further reduces the amount of cabling work. For devices with moderate power requirements of up to 50 watts, there is no need for the additional cable for the power supply. In automation applications, this would apply to sensors for example.
The uses mentioned are just a few examples where the use of single-pair Ethernet can bring benefits. The required application-specific planning and installation guidelines still have to be created. This work has begun, including in user organisations such as Pi for PROFINET® and ODVA for ETHERNET/IP. LAPP is actively involved in this work. LAPP started developing cables at an early stage. With the ETHERLINE® T1 product family, a portfolio of single-pair Ethernet cables is already available for use in industrial machinery and systems.
Broad market penetration will require standardised and uniform connectors. The connectors for SPE are described in the IEC 63171 standard. The standard contains six different connector faces. The IEC 61171-6 connector has excellent opportunities to establish itself on the market. This connector is propagated by the SPE Industrial Partner Network. LAPP became a member of this consortium of well-known companies in order to help SPE technology make its key breakthrough in industry. Different designs based on this connector face are being developed for specific applications. For the IP20 area inside the control cabinet, a connector is used that is similar to the current RJ45 in terms of the locking tab mechanism. Connectors based on the established M8 and M12 principle are in development for use outside the control cabinet in the IP67 area.
Further information on LAPP Industrial Ethernet:
Product Selection by Protocol Standard
Product Selection by Application