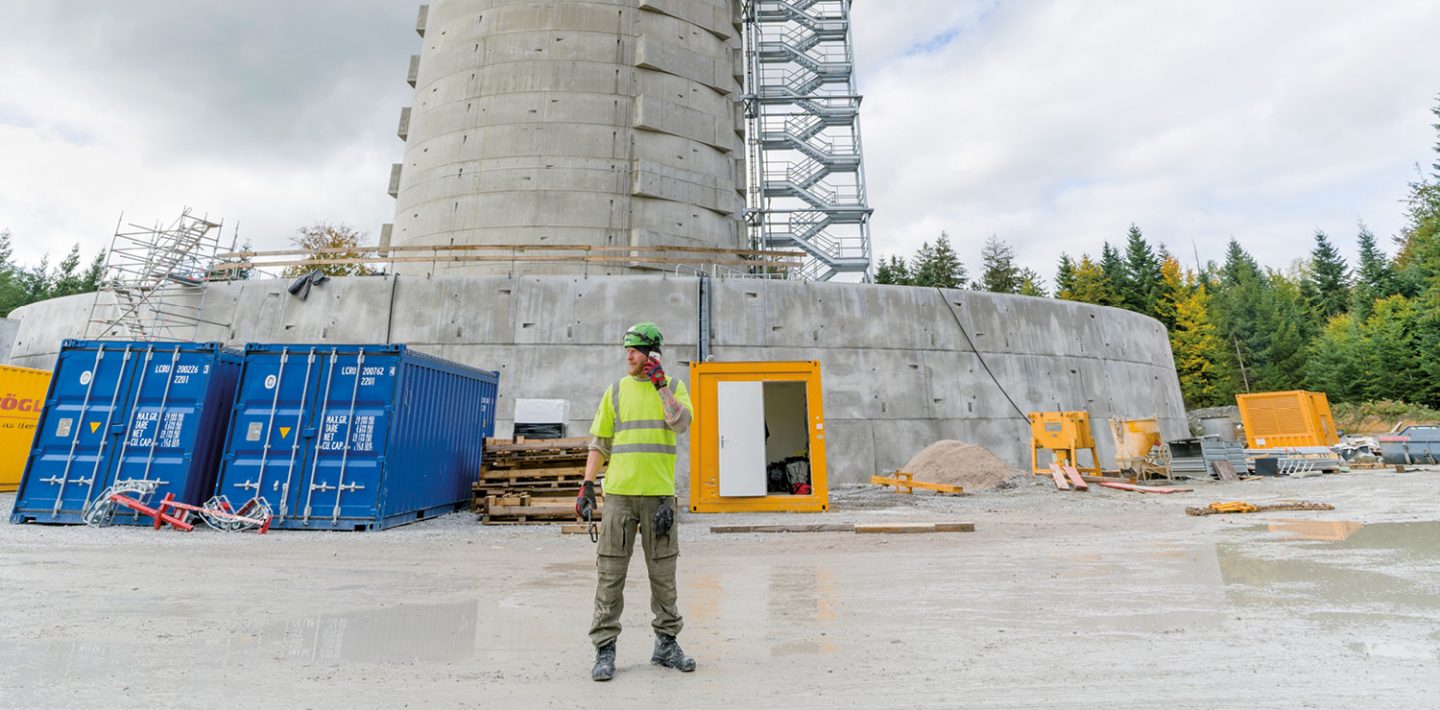
At first glance, the figures for the expansion of wind energy in Germany look good: At the end of 2019, around 29,500 wind turbines were operating onshore, between them producing almost 54 gigawatts and generating 106 terawatt hours of energy per year, with a further 26 TWh from offshore plants. But as we said, this is just the first glance. In fact, wind energy is not really in a good situation in Germany. This year, the first older wind turbines will no longer qualify for statutory support. The Renewable Energies Act, which was introduced in 2000, guarantees operators that the energy will be purchased at high prices – but only for 20 years. This could therefore make older plants uneconomical at a stroke. The wind energy industry even fears that in the coming years the number of older plants being decommissioned will exceed the number of new ones being constructed.
One reason for caution is a new law under which the Federal Ministry of Economics wants to introduce minimum distances between the plants – reducing the available areas. Grid operators do not like wind energy because it is not available continuously, only when the wind is blowing, which makes grid control more costly. This could be avoided if wind turbines could store unused energy in a stiff breeze and then feed it into the grid when energy is scarce. The ideal solution would be a combined wind farm and pumped storage power plant. But they don’t exist, do they?
Yes, they do. Since 2017, on a ridge at Gaildorf near Schwäbisch Hall four giant rotors have been turning, harvesting the energy from the wind that blows over the Limpurger hills. If you could imagine the perfect location for a wind turbine, this would be it. Each wind turbine delivers 3.4 megawatts of electrical power and generates more than 10 gigawatt hours of energy per year, enough to supply around 5,000 households. The other three wind turbines, which stand like sentinels on the hill a few hundred metres apart, have an identical design and deliver the same power and energy. The wind turbines are among the highest in the world with their hubs at 180 metres and the tips of the rotors reaching a height of 246 metres. Every metre counts, as every additional metre of altitude means 0.8 percent more energy.
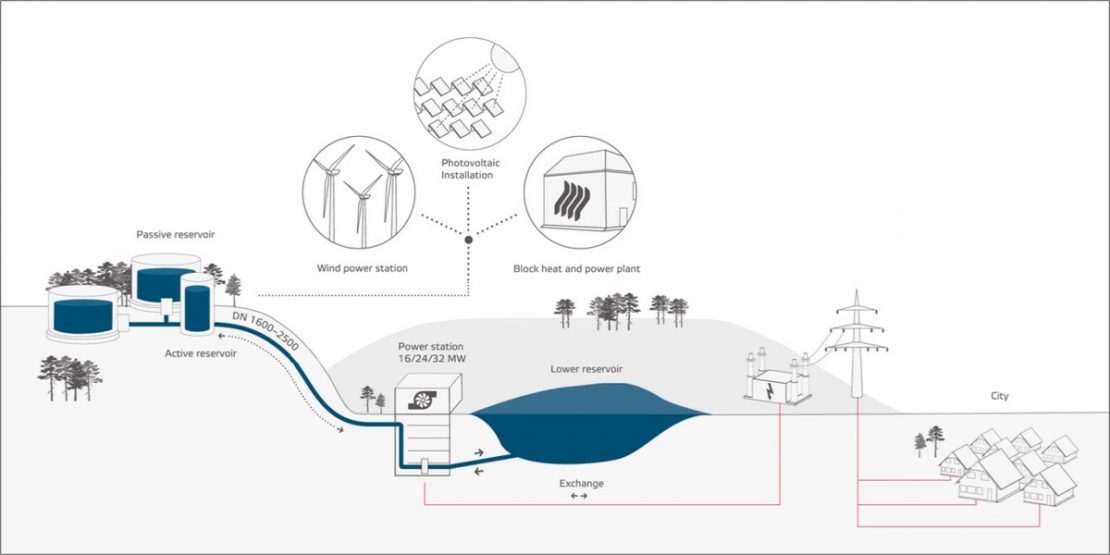
Storage system in the base
However, the plant in Gaildorf is not only special because of its size. Even a amateur can see that there is something different about the huge towers. The lower section is strangely thickened and stands in a huge round reservoir. If there is excess wind power or electricity in the grid, this electrical energy is used to pump water up and into these two reservoirs. If electricity in the grid is scarce, the water falls 200 metres down into the valley and powers three turbines. The principle of the pumped storage power plant is almost 100 years old. What’s new here is that a plant for generating renewable energy and a pumped storage system are at the same location, in fact they are housed in the same construction. The thick base of the wind turbine – the active reservoir – can hold 7,100 cubic metres of water, while the large external pool, known as the passive reservoir, contains a further 43,000 cubic metres. The active reservoirs are connected by a two metre thick pipe, which leads down into the valley under the bed of the Kocher river and into an artificial reservoir. At the beginning of operation in 2017, 160,000 cubic metres of water were removed from the Kocher and pumped up into the reservoirs.
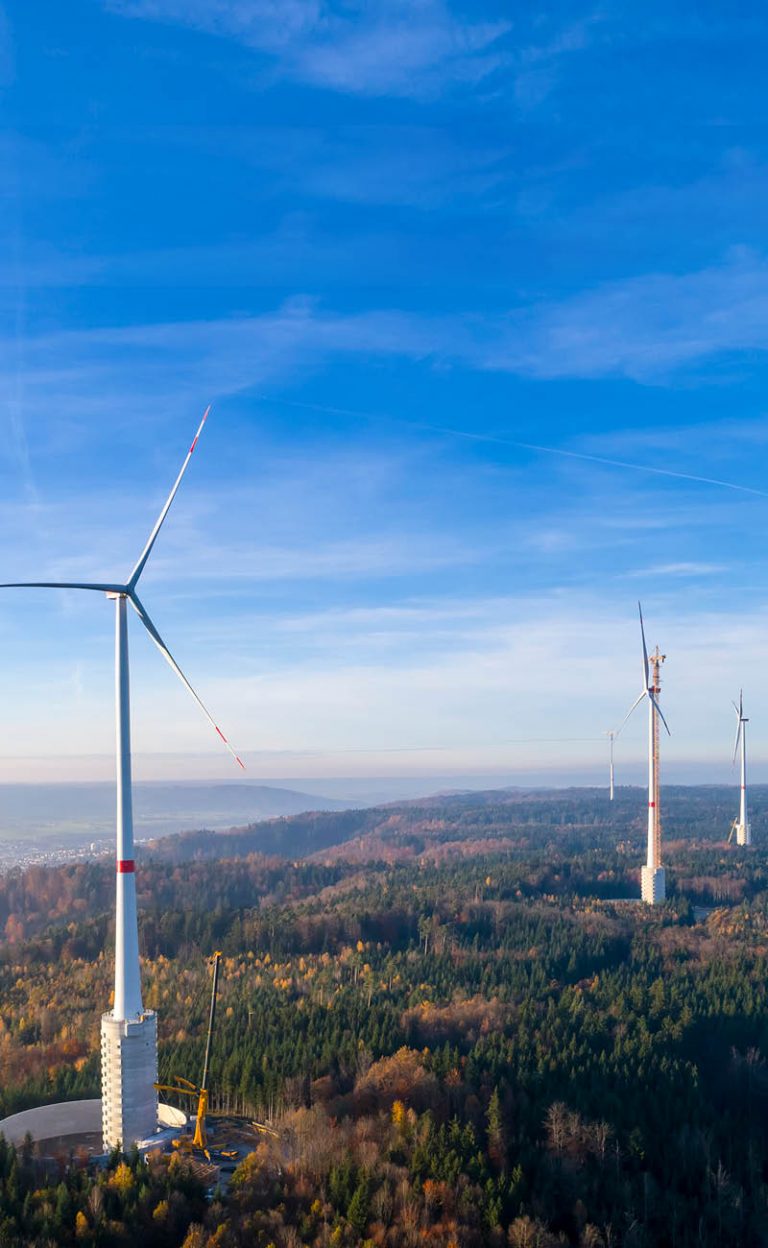
No energy revolution without storage
The energy content of the natural energy storage in Gaildorf is 80 megawatt hours. This can offset several hours of calm but also cover short discrepancies between generation and demand in the grid. Switching from feeding into the grid to storage or vice versa takes just 30 seconds. This increases flexibility and opens up additional sources of income, as the plant can offer well paid grid services to compensate for instability and changes in the grid frequency or to provide idle power.
The towers were constructed by Naturspeicher GmbH, a subsidiary of the Max Bögl Group based in Neumarkt in the Upper Palatinate. To avoid any surprises, only suppliers who are listed with General Electric, the manufacturer of the wind turbine, were able to submit tenders. The same applied to the cables. Here, LAPP was chosen. The Stuttgart-based global market leader in cable and connection systems has already supplied cables for the nacelles in other GE plants. This was a prerequisite for Max Bögl to approach LAPP to be a supplier for the cables in the tower in Gaildorf. “We received a specification from General Electric, which lists the exact specifications for each cable, such as dimensions, temperature, torsion, weather resistance and much more”, says Andreas Müller, Key Account Manager Wind Energy at LAPP.
Just in time cables
But it wasn’t just the quality of the cables that had to be right, it was the logistics too. Each of the around 100 cable drums had to be on the construction site precisely when that particular cable type was needed. Any delays in the tightly scheduled construction process would have led to stoppages on the site. At the same time, the huge cable drums were not allowed to take up too much space on the four tight sites in the middle of the forest. The LAPP project team solved the problem with two containers: In the first, full cable drums waited to be used, while the second was used to collect the empty drums and regularly transport them away. Everything was done just in time. Max Bögl’s trust has paid off: LAPP completed the order on time.
LAPP supplied the following cables for the four wind turbines in Gaildorf:
Nacelle
Tower
- Aluminium cable
- ÖLFLEX® CLASSIC 110
- Data cables
Infrastructure
- Power cable for 20 kilovolt medium voltage
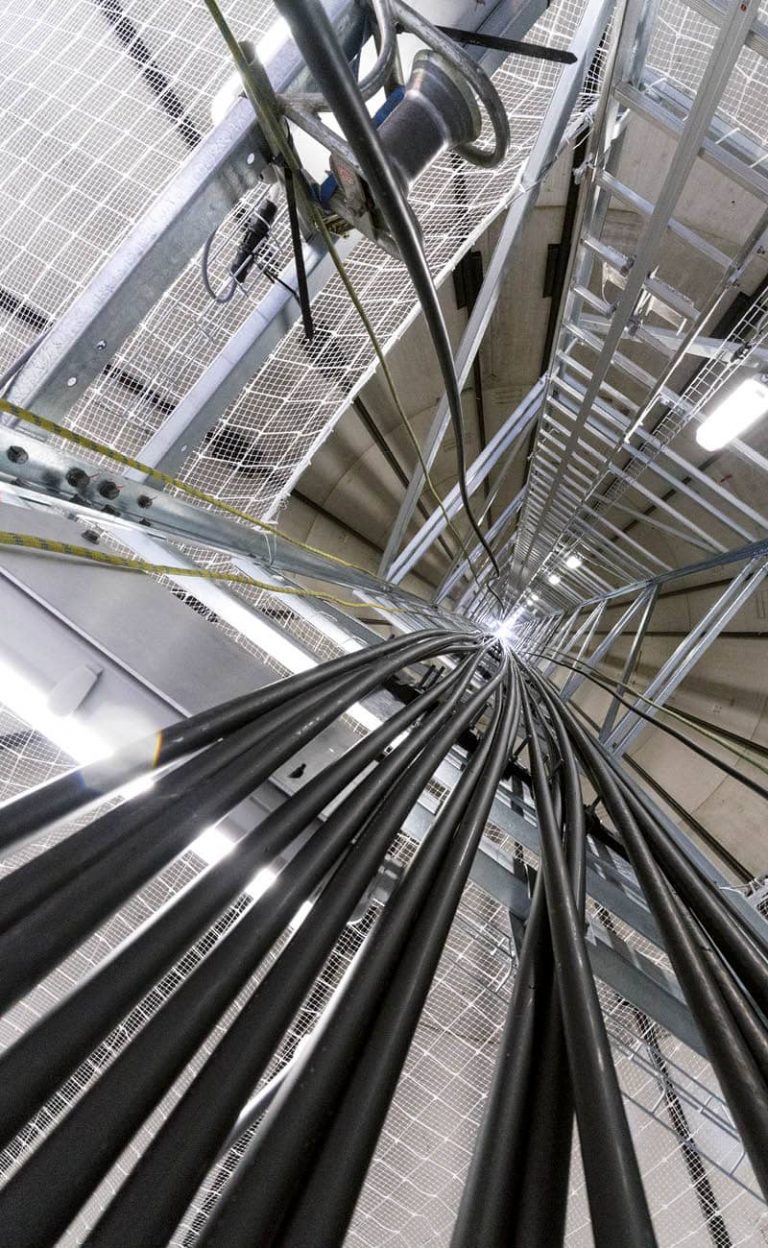
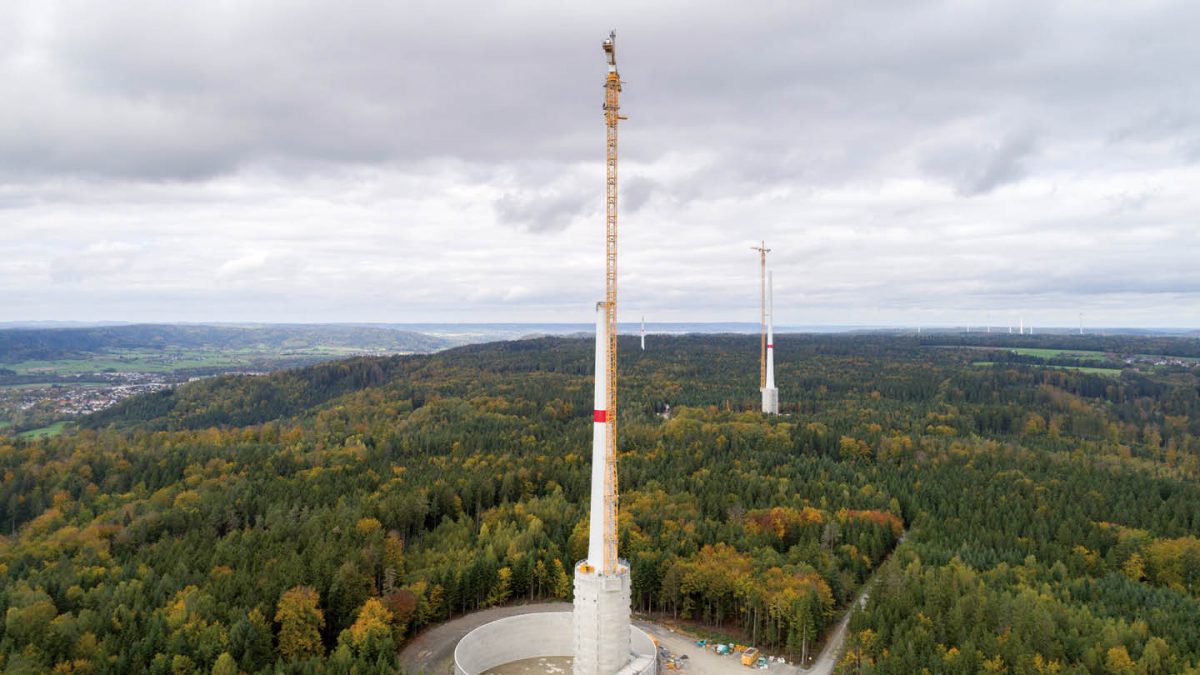
Video: © Max Bögl Wind AG
Further projects anticipated
Max Bögl is planning further hybrid systems based on the same concept. The construction company has stated that it prefers medium-sized companies as suppliers due to their reliability and their high level of identification with projects like this, so LAPP will definitely be in contention again. LAPP is also in the running for international projects. Enquiries like this are a welcome challenge for LAPP as the company’s ability to produce the required cables either in Germany or at other plants in Europe and also to call on a centre of excellence in Singapore and a production site in Shanghai are a major strength. Andreas Müller says: “We also have sufficient know-how in Asia to supply major orders for wind power plants with premium quality.”