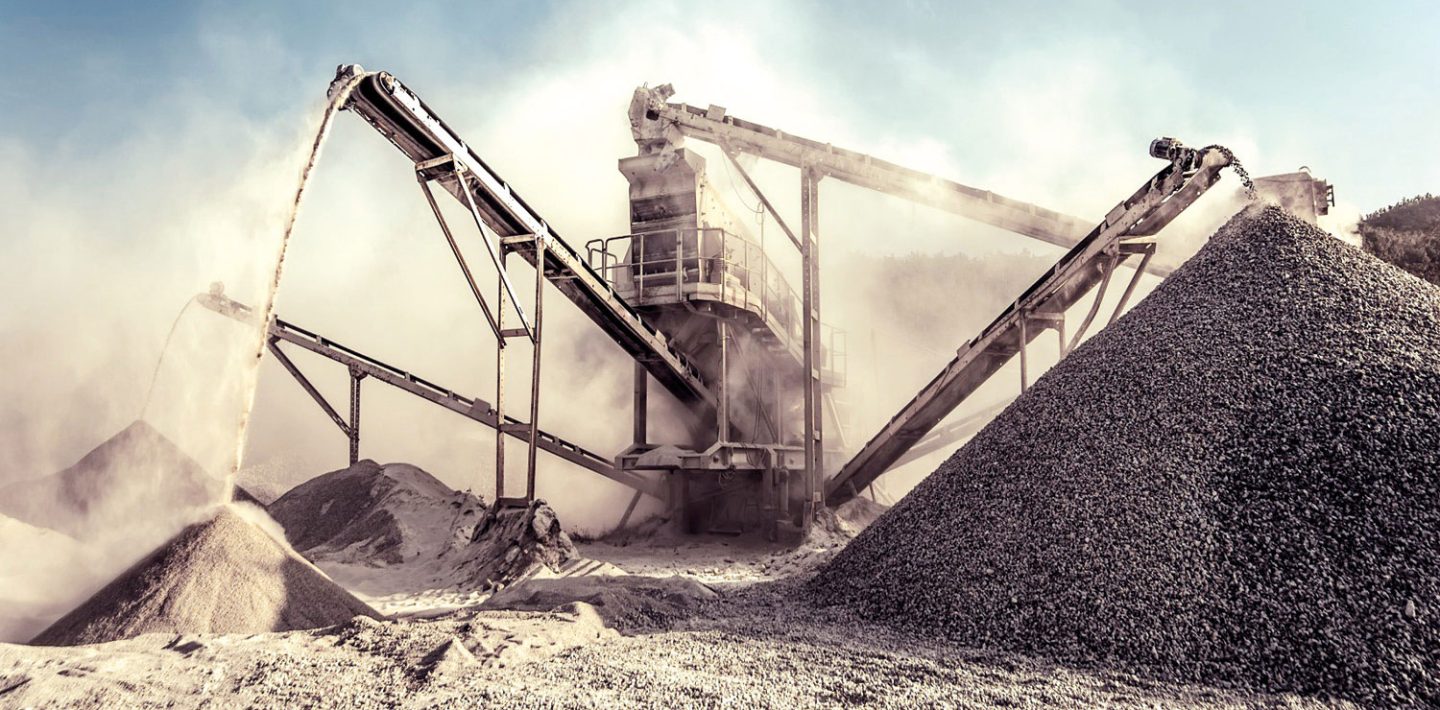
The collaboration with AIUT has now led to the realisation of an international project in Africa. An application from LAPP Poland now supports the work of a forklift in the Togo cement plant.
But what exactly does this work look like? Loose materials used in the cement production process must be moved and stored using the forklift. To perform these tasks, the forklift truck is mobile – it moves on a rail platform.
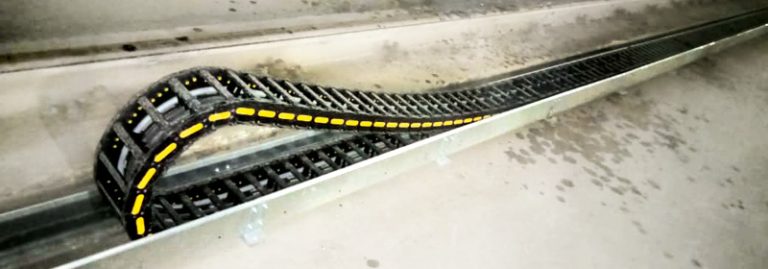
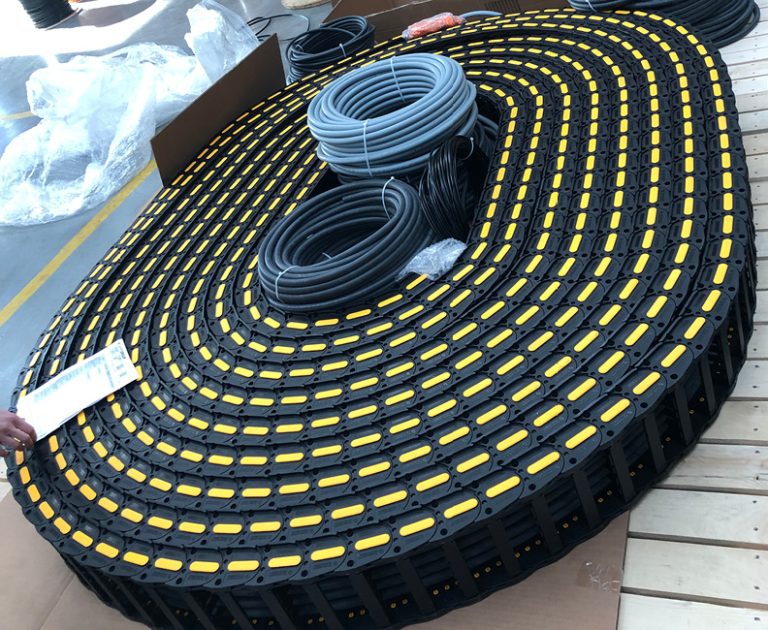
The necessary chain guiding system with cabling had to be replaced as the existing machine often failed. The reason for the failure was that the conveyor belt transporting bulk material was too close. As a result, falling lumps of said material repeatedly got into the guide and damaged the construction.
LAPP Poland provided the optimum solution to this problem: a new guiding system that is mounted at a safe distance from the conveyor. This minimised the risk of damage to the guide due to external influences.
However, selecting a suitable rail for the project was at least as complex as the industrial process of cement production itself. This usually consists of five main technological processes: the extraction and processing of raw materials, the incineration of clinker, the grinding and, finally, the packaging.
It was therefore necessary to carry out a series of data analyses in advance, which on the one hand recorded the weight and size of all components that will be in the chain. Secondly, the distance over which the devices travel had to be defined. It was also determined how and in which direction (vertical or horizontal) the chain should be assembled. Cables and wires with similar diameters were also to be grouped using separating strips. The minimum bending radii of the guide itself should be equal to or greater than the recommended radius of the stiffest cable in the assembly.
The results of the analysis led to the selection of the 328SU model in the sliding guide series, as the sliding guides are designed for transporting cables over long distances. Typically, the length of the guide corresponds to around half of the movement range of the device. Accordingly, the length of the guide in the cement plant in Togo is approx. 40 m with a range of movement of approx. 80 m. On the other hand, each of the installed cables has a total length of 122 m. Special separating strips inside the guide prevent the wires from overlapping.
Three special cables, all equipped with a PU cable insulation, were selected for continuous operation. This makes them very robust, abrasion and cut-resistant, as well as resistant to oils and drilling sludge. The ÖLFLEX® FD 855 P control cables were used as they are also ideally suited for use under the most demanding operating conditions. It is adapted to a wide temperature range (flexible from -40 °C to +80 °C), halogen-free and self-extinguishing. Their small outer diameter enables the smallest absolute bending radii among all standard cables for mobile applications. The ÖLFLEX® CHAIN 90 P power cable was used, however, as it is single-core and very flexible. As a result, it can be used as an alternative to multi-core cables where there are exceptional space requirements or minimum bending radii. Last but not least, the cable HITRONIC® HDM700 8G62.5/125 OM1 was used. Thanks to its small size, it is convenient to install and enables high flexibility due to a small bending radius. The cable is also ideal for high-frequency data transmission as it does not contain any metal elements and is therefore completely resistant to electromagnetic interference.
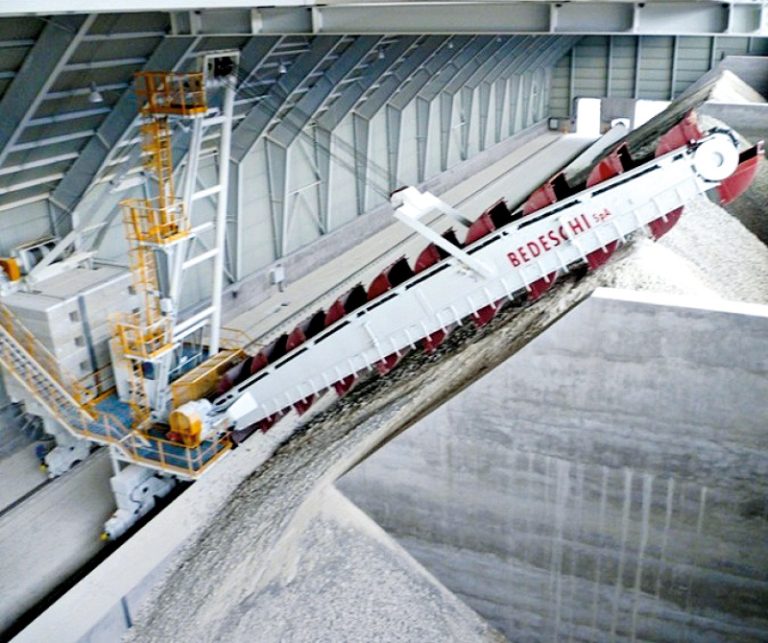
Like all cables used in continuous operation at LAPP, these cables have previously been tested in special stations. Real loads are simulated, which, however, go beyond the normal working conditions: the cables are subjected to torsion or considerable acceleration in the special devices. In this way, the service life of the cable in the intended application can be safely determined. For the time being, thanks to the reliable solution and robust cable from LAPP, nothing will go wrong in the coming years at the cement plant in Togo.
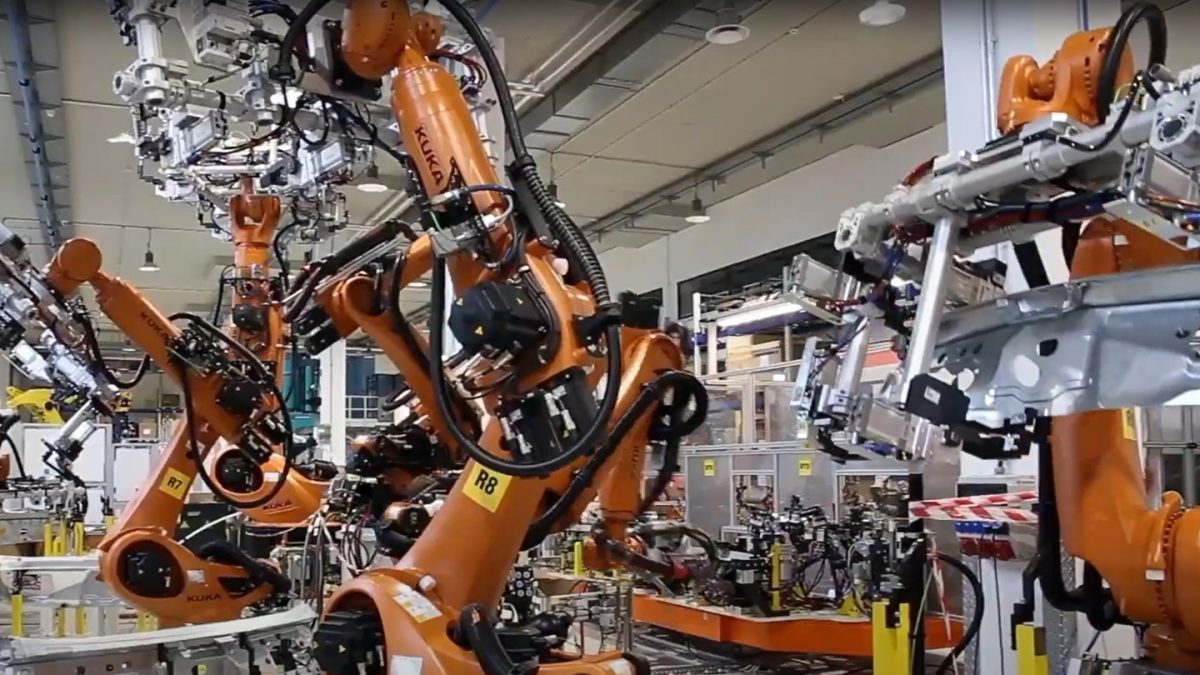
Video: © AIUT: Automation and robotics