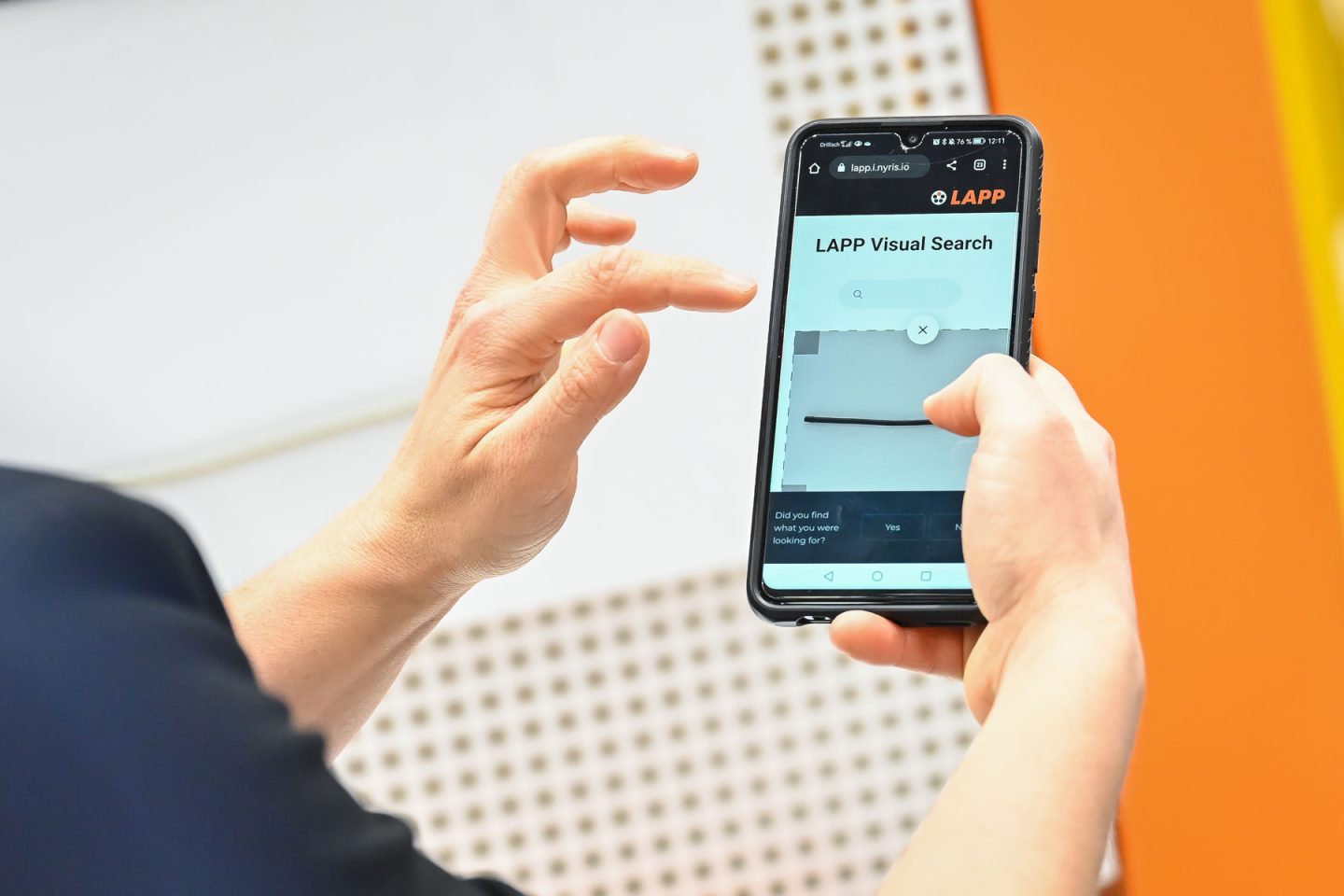
Innovation is a top priority at LAPP and is an important part of the company’s DNA. But how are new innovations created? “Technology push” and “market pull” are the most common answers when companies are working on new ideas. Manuel Richter, Team Leader Digital Sales at LAPP, is a real enthusiast for digital transformation. Together with Dominik Schmalzried, Global Business Process Owner Digital Innovation, he has dedicated himself to the mission of driving LAPP’s digitalisation forward. Together, the two have already revolutionised cable inventory management on the customer side with a new digital eKanban solution. “For LAPP, innovation means developing things that fulfil customer needs – and the idea of an image search with a shop link can be a real added value for our customers. At the same time, digitalisation for us doesn’t just mean digitalising old, existing business processes, but also breaking completely new ground that is only made possible by the digital world. This is precisely the mission of digital innovation at LAPP,” says Dominik Schmalzried.
Dominik Schmalzried and Manuel Richter first evaluated whether image recognition could become an LAPP use case based on customer behaviour: The process of identifying a correct item is very time-consuming on the customer side. While the imprint on cables provides information about the supplier, type designation and specification, the situation is different with cable glands, for example. “Only the supplier is printed on them. The customer would have to painstakingly research the article name and measure the diameter and length or look it up in the manual,” says Manuel Richter. “That’s why we have developed a solution for all our products to save this time. Our goal: from image to order in our online shop in a few seconds with as few clicks as possible.”
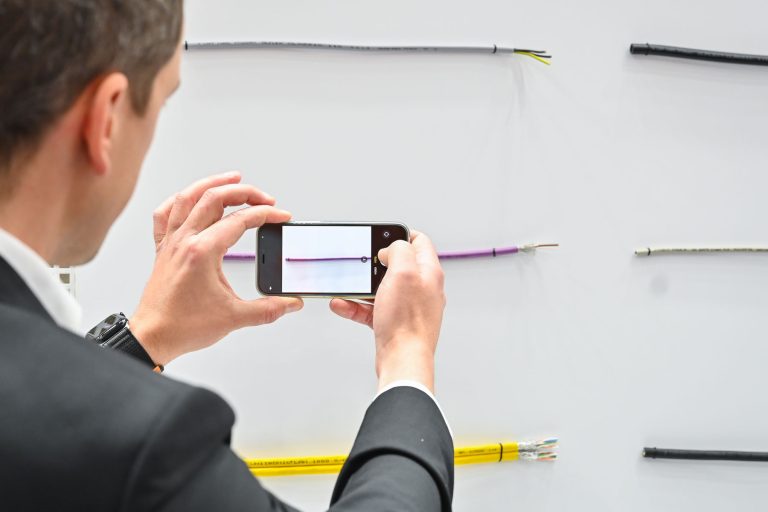
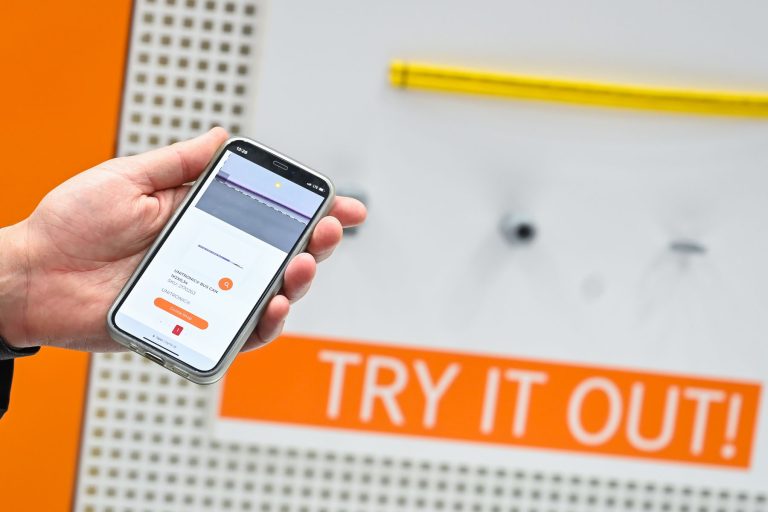
The solution for the customer is a responsive web application that is directly connected to the LAPP online shop. Anyone who has a photo of the product to be identified can either upload it via the browser or take a photo with their smartphone via the mobile application. The system in the background determines the corresponding product based on the parameters. This can then be placed in the online shop’s shopping basket with a single click and the ordering process can be initiated. The application can also be used to develop completely new ways of interacting with customers.
A large amount of data is required to correctly identify the products. The basis for reliable identification is LAPP’s product information system. This stores all the information, such as synthetic data, for each product. This information is used to train the AI using machine learning. This software is fully customised to LAPP’s needs and consists of two main elements: The first part is the so-called Optical Character Recognition, or OCR for short), which enables text recognition on cables and thus makes the cable identifiable much faster than the alternative of having to manually type the text into a search field. The second part is called “pattern recognition” and enables the automatic identification of specific features and patterns in data. Complex geometries of three-dimensional components, such as cable glands, can be made recognisable for the AI application.
Dominik Schmalzried was in charge of the technical side of the project and knows: “We are really pushing the boundaries of artificial intelligence here and enabling everyone to become a product expert. The customer can scan the product in front of them by taking a photo with their smartphone and they have all the information at their fingertips.”
However, the team led by Manuel Richter and Dominik Schmalzried has also looked beyond this. The LAPP solution not only allows them to recognise their own products, but also those of competitors: “This means we can also offer our customers our alternatives to competitor products.”
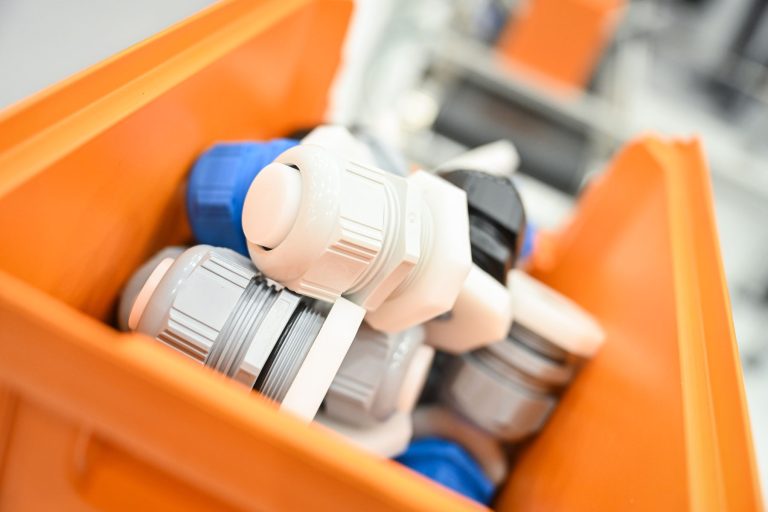
LAPP’s innovation prize, the Eddie Lapp Award, is awarded annually for outstanding innovative projects in which LAPP employees have been involved. An independent jury assesses the projects submitted and honours them. In order to promote a culture of innovation, the company gives all employees additional freedom alongside their day-to-day work to get involved in development projects with potential.