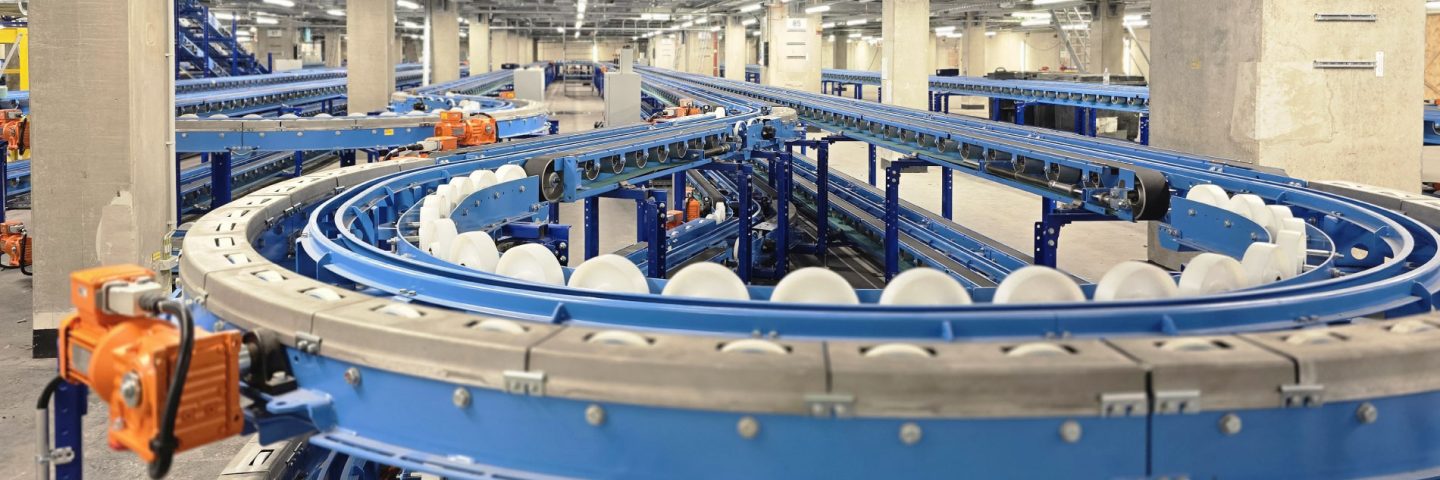
The scales are relentless: the suitcase weighs 20.5 kilograms instead of the permitted 20, but the friendly lady at the check-in counter turns a blind eye and the next moment the luggage is swallowed up by a conveyor belt. Then the nervous thrill at the destination: Has my suitcase arrived? Many passengers can only guess what happens between check-in and successful baggage reclaim. Thousands of suitcases are transported at breathtaking speed along the airport conveyor belts, sorted and brought to the right airplane. Sophisticated technology ensures that everything runs smoothly.
Anton Pajonk knows exactly how this works. The engineer founded the company SEAP Automation in 1992, which specializes in industrial companies, especially airports and the automotive industry – “wherever something is being loaded or conveyed,” says the founder. Numerous major projects for customers such as Frankfurt am Main Airport, Daimler AG, Zurich Airport, Opel, Miele, BMW and the Smart plant in Hambach are on his list of references. His current order is the largest to date: baggage logistics in the new Terminal 3 at Frankfurt am Main Airport. Conveyor belts move the baggage through the tunnel of the terminal at speeds of up to 2.5 meters per second. The project is right on schedule, thanks to good project management and good product availability from partners such as LAPP.
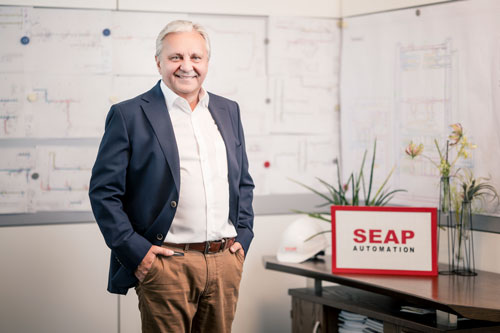
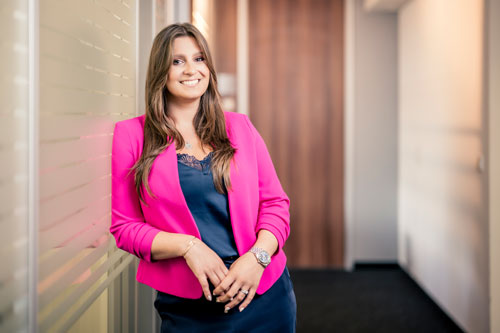
For Pajonk, high quality, flexibility, family management and strong customer loyalty are the reasons for SEAP Automation’s success. SEAP Automation has already acted as general contractor and subcontractor for major projects such as the modernization of Terminals 1 and 2 in Frankfurt. SEAP Automation is now implementing the new construction of Terminal 3 together with its long-standing mechanical engineering partner Beumer Maschinenfabrik from Beckum.
Together with various partners, we have worked hand in hand on the successful implementation. For example, some of the automation technology was supplied by Schneider Electric.
Normally, large automation companies such as Schneider Electric or Siemens supply the cables for the power supply and data networking at the same time. This is not the case in Terminal 3 or in other projects in which SEAP Automation is involved. For 30 years, i.e. since the company was founded, SEAP has ordered most of its cables from LAPP.
The advantages for LAPP are the high quality of the products, the ability to deliver at short notice and the partnership-based consulting approach.
“The cooperation with the connection specialist on the Terminal 3 project couldn’t be better,” praises Julia Pajonk, member of the management board and authorized signatory of SEAP Automation, which will take over the company in the coming years. LAPP delivers many kilometers of cable to the construction site on schedule. There is a dense crowd of dozens of suppliers, which is why the supervisor only allows trucks onto the site according to a fixed schedule. If a driver misses his time slot, he has to go back to the supplier and try again a few days later – which delays the work. It is also not possible to temporarily store building materials on the site. The NYCWY power feed cables in particular have to be delivered just-in-time. These cables have four wires with a cross-section of 120 square millimetres each and are as thick as a forearm. A cable drum weighs several tons and cannot simply be placed in a corner on the construction site.
“LAPP has met all deadlines, there have never been any problems,” says Julia Pajonk.
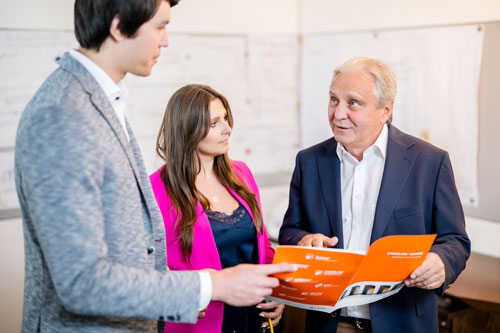
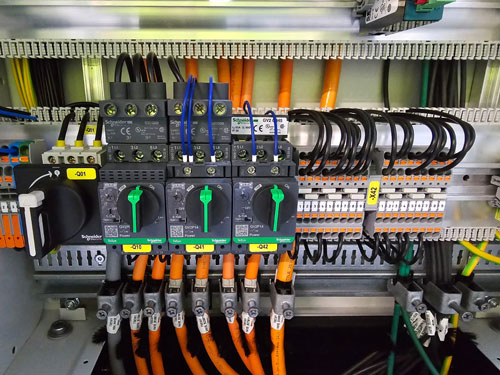
So far, SEAP Automation has ordered around 85 kilometers of cable from different product families, each in various versions, for example with or without shielding or as a particularly flexible version. A large proportion is made up of ÖLFLEX® servo and control cables. UNITRONIC® data and ETHERLINE® network cables are also ordered. SEAP Automation is also increasingly ordering pre-assembled patch cables and sensor/actuator cables, with a total of 2,100 units ordered to date. “But this is just the beginning,” says Marc Ehinger Account Manager at LAPP, who looks after SEAP Automation, “in the end it will be several hundred kilometers of cable.”
Why will SEAP Automation continue to use cables from LAPP in the future? In addition to the quality of the products and the reliable logistics, LAPP repeatedly impresses with its planning skills and support in tricky situations, such as when parts have to be reordered spontaneously. Anton Pajonk: “We are in close and very good contact with Marc Ehinger and have always received perfect advice.”