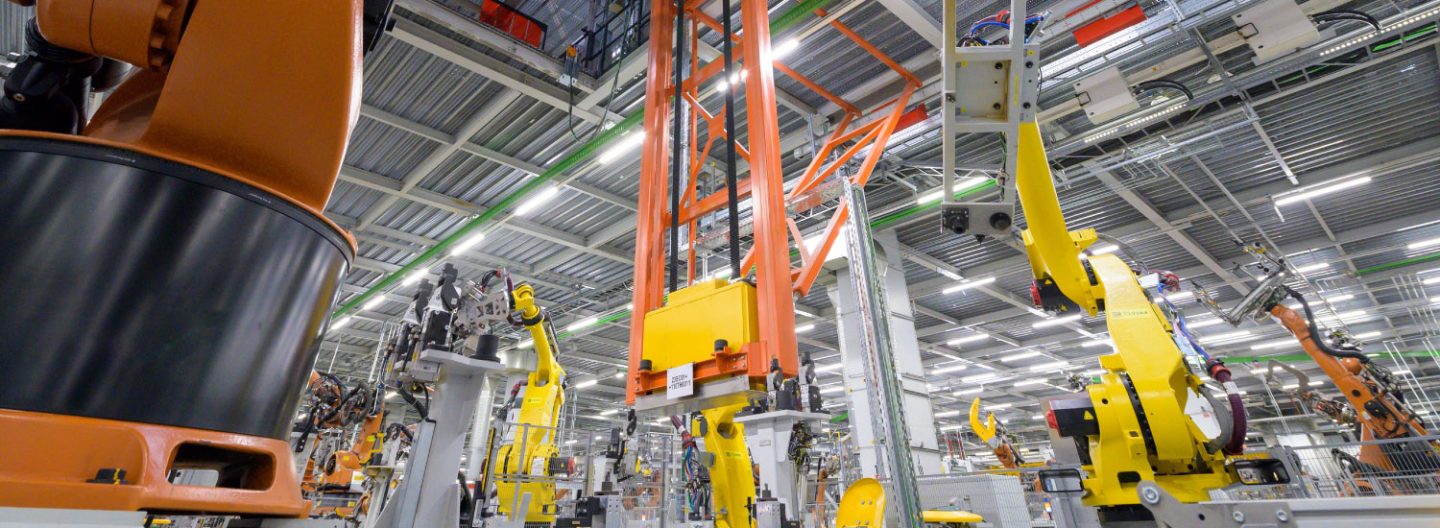
In Germany, the land of the automotive industry, the major automotive manufacturers are still among the flagship companies in the Federal Republic. They represent the largest sector in the manufacturing industry and are therefore the most important industry sector in the country in terms of turnover. Accordingly, their production systems are large. Depending on the location, they resemble small towns, provide jobs for hundreds of people and operate with an ever-increasing degree of automation. A large number of robots are used for punching, welding, riveting and gluing in a car body construction line, which process the components with the utmost precision. In turn, they demand lots of electricity. “Probably more and more direct current in the future,” says Alois Heimler, Strategic Marketing Manager Intralogistics & Automotive, from LAPP and knows: “The magic word is less voltage changes.”
For visitors to the production system at the BMW Group plant in Dingolfing, this magic remains hidden at first, because the innovation of the body construction system at the plant is only visible at second glance. All robots and machines work as usual with the same speed and precision. Component after component enters the production line, passes through work step after work step and becomes more and more similar to the final car body every minute. The only difference is that the system is operated with direct current – in our alternating current world, this is still a rare way of supplying power in an industrial environment. Connection solutions for production lines come from LAPP.
Saving energy with recuperation
The switch from alternating to direct current is particularly suitable for body construction. To date, machines and robots account for a large proportion of the electricity consumption of an industrial system and offer correspondingly large potential for savings. The potential for savings is particularly high in highly dynamic processes, such as those found in industrial robots. The production lines move along programmed paths to assemble the individual components of a car body into a vehicle. In doing so, they accelerate briefly and then decelerate again. This means that a robot collects a lot of energy for a short time to initiate a motion sequence or to convert it into kinetic energy. In braking torque or in lowering mode, however, electrical energy is generated again from the kinetic energy (the drive is now in generator mode). This kinetic energy is generally not stored in alternating current (AC) systems and is lost as thermal energy; this is why braking resistors were previously used to “burn” the excess energy. This is not the case in the direct current (DC) grid: “Here, the energy is fed into the DC intermediate circuit, other DC consumers or energy storage units. This means that the energy released during braking processes can be sent back to the grid centrally for all consumers without major conversion losses,” says Alois Heimler, explaining brake recuperation. It therefore enables direct energy exchange between all drives, as is the case in robots.
Especially in times when sustainability is increasingly demanded and promoted, the utilisation of previously unused braking energy is useful, as it can save a considerable amount of energy. And this is not the only advantage of a DC network: instead of lots of decentralised conversions from AC to DC, there is only one central energy conversion, which supplies all systems with direct current. Bonus point: If the electricity comes from renewable sources such as photovoltaics or wind power, it is available as direct current, even if the consumers are increasingly designed for direct current. “DC is therefore a key element in the energy revolution,” says Alois Heimler. The exact savings when switching to DC vary depending on the system and its load utilisation. However, results between 15 and 20 % are realistic.
LAPP’s direct current portfolio for the automotive industry
It is precisely with this sustainability concept in mind that LAPP started several years ago and was the first manufacturer to develop a cable portfolio for various applications in the low-voltage range, which is attracting increasing interest. The cables are also used in body production in Dingolfing. These include the ÖLFLEX® DC 100. With its maximum voltage of 0.75 / 1.5 kV, it is the ideal basis for energy-efficient DC networks in industrial systems and makes it the first choice for automotive manufacturers. The ÖLFLEX® DC Grid 100 is also installed. As a DC infrastructure and cable for direct burial for direct current networks, it offers a flexible, fine-wire structure in industrial systems that can even be used in dry, damp and wet environments. This makes it ideal for connecting industrial systems to the DC grid. The ÖLFLEX® DC Robot is used in the system’s robot. The requirements for robotics applications in automotive manufacturing are high. The cable was specially developed to withstand such extreme conditions. Its exceptional flexibility allows robots to move with precision while remaining resistant to torsional and alternating bending loads. Its compact design also saves valuable space. Portable applications are indispensable for the production line and LAPP has the right solution for this too. The ÖLFLEX® DC Chain 800 can be used in cable chains with long travel distances or high accelerations. The special stranding assembly with short lay lengths allows the smallest bending radii. Its outer sheath made of specially designed thermoplastic polymer is highly chemical resistant and has increased oil resistance.
All cables have an additional advantage over the well-known AC cables: while 5-core cables are required for AC voltage, one to two conductors are less often used for DC voltage. The lower number of conductors means that less material is required: far less copper is needed for DC cables than for their AC counterparts. This also makes them significantly more space-saving and particularly interesting for applications in tight spaces or in control cabinets too. The potential for material savings here is around 40%.
The body construction system at the BMW Group plant in Dingolfing is an application pilot that is currently testing DC technology in practice. It was initiated as part of the DC-INDUSTRIE2 project. The German research project investigated the opportunities and challenges of direct current technology in industrial production systems. In the long term, researchers are planning to convert entire factory halls to direct current. The results of DC-INDUSTRIE2 constitute guidance on creating energy-efficient solutions and standards. LAPP too is a project partner. The ÖLFLEX® DC 100, which was created as part of the project, is now on the market as a series product. But it is not just the research project that connects the two companies, it is also a long-standing partnership. DC cables with special cable cross-sections were produced by LAPP as a prototype for the automotive manufacturer in no time at all.
“We believe that in the future, more and more production systems will be supplied with direct voltage”, summarises Alois Heimler. This is also supported by the growing interest in LAPP’s DC portfolio, which marks an important step towards the energy transition. Accordingly, the family-owned company is gearing itself up for the future and has not only restructured its global research and development, but also the management of laboratory and test centre activities in order to be able to respond more quickly and agilely to developments in the industry.
LAPP Whitepaper „Calculating the cable cross-section for direct current”
Benefit from the knowledge of our DC experts. The guide will help you calculate and select cable and wire cross-sections for AC and DC systems.
Download LAPP Whitepaper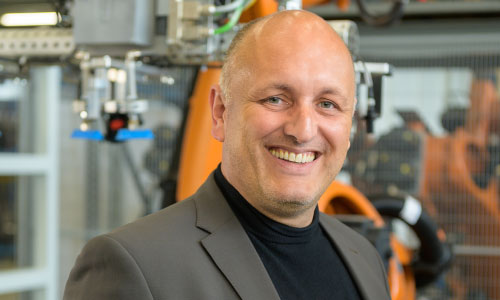
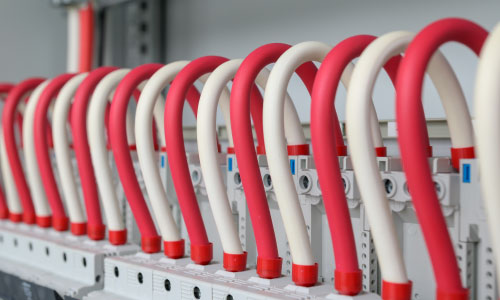
DC-INDUSTRIE2
Both BMW and LAPP were part of the DC-Industrie2 research project. The project and its researchers set themselves the task of developing a concept for an intelligent DC supply system. One of the tests was whether a DC system can supply a production hall with direct current at low cost. The project was successfully completed on schedule in March 2023 with the conclusion: DC is ideal for a sustainable electrical grid and can be easily integrated into production. The findings will be incorporated and further developed in the Open Direct Current Alliance (ODCA) working group, which was set up by the ZVEI. In the project LAPP researched the long-term stability of insulation materials for DC cables.
ODCA
The Open Direct Current Alliance (ODCA) was founded by the Zentralverband der Elektrotechnik- und Elektronikindustrie (ZVEI) in cooperation with companies from industry, science and research to promote the development and market introduction of direct current networks. With 56 participating companies (33 at its launch in 2022), including LAPP, the ODCA is committed to a resource-efficient and carbon-neutral world. Through the use of direct current technology, the Alliance aims to achieve more efficient energy transmission in order to support society’s goal of sustainability.