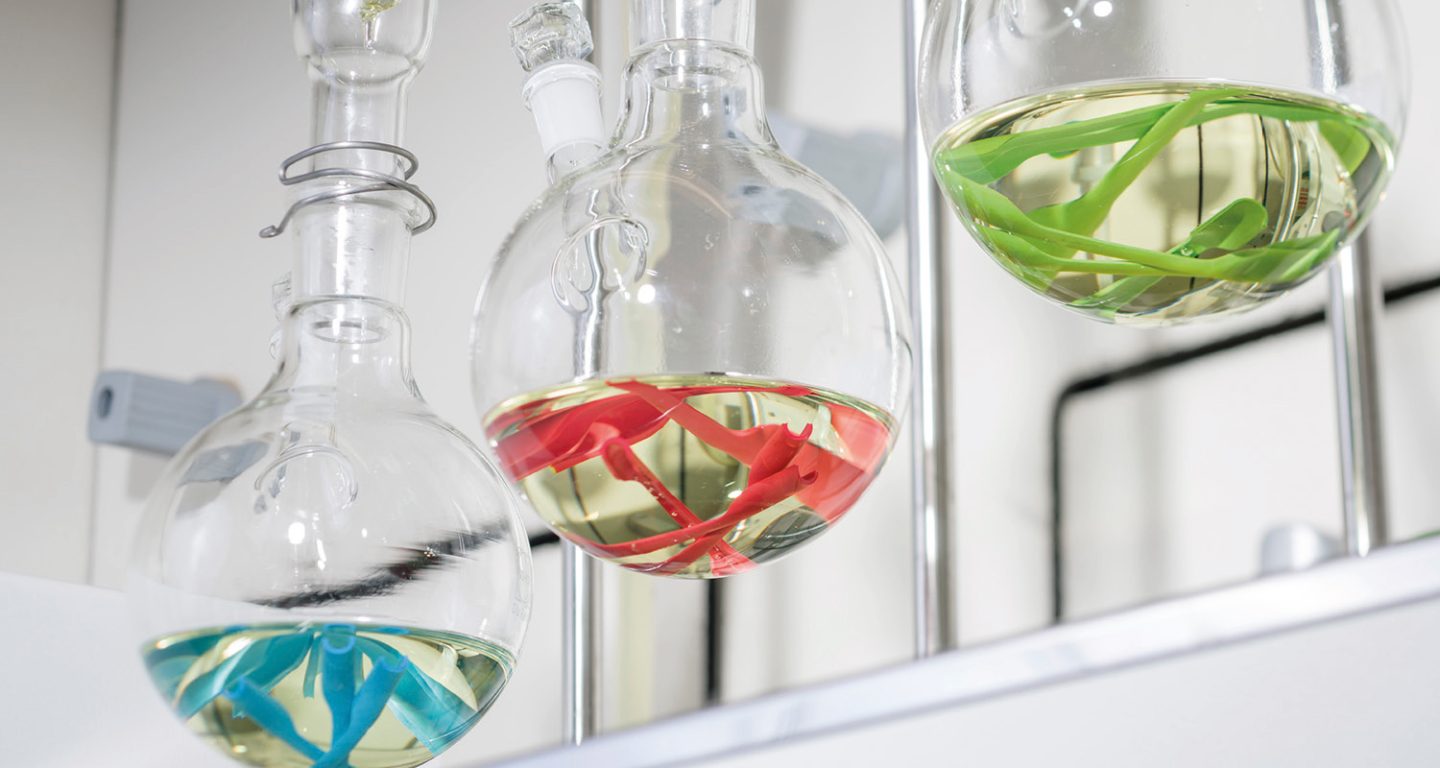
What properties should good signal, control and data cables have for tough use in production? Oil resistance is at the top of the list alongside good electrical properties. Oskar Lapp recognized this when he invented the first control cable with color-coded cores at the end of the 1950s with ÖLFLEX®. The front part of the name suggests that this cable is particularly resistant to oils, lubricants and many other media. That is true to this day. However, there are occasionally cases where customers contact LAPP because an ÖLFLEX® or another cable from the LAPP portfolio has been corroded by certain chemicals. The chemists in the LAPP laboratories quickly find out what is happening. “The offender is usually an additive in a lubricant or a chemical in a newly acquired cleaning agent that reacts with the cable sheath, which is not actually suitable for this application,” says Tanja Wieland, Head of Cable & Analytics Laboratory at LAPP. This could lead to the plastic being destroyed – bringing production to a halt. Wieland therefore always recommends consulting LAPP in advance, as this is the best insurance against unexpected failures.
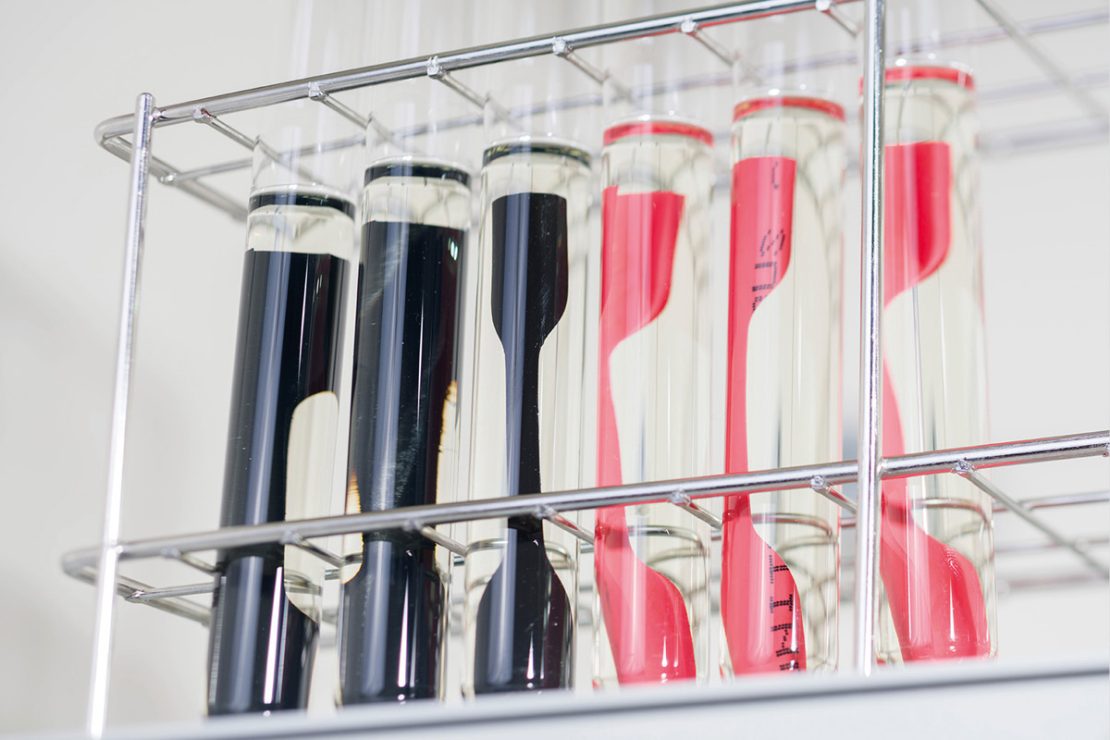
Not all oil is created equal
Everyone can differentiate olive oil from motor oil. But who knew that there are hundreds of oils, especially for industrial applications, with different mixtures? There are additives that prevent foaming, emulsifiers for an intrinsic connection with water, demulsifiers that prevent exactly this, additives to prevent corrosion, oxidation inhibitors and much more. What makes it more difficult is that oils with the same designation, such as a HLP46 hydraulic oil, noticeably vary depending on the manufacturer. Anyone who wants to be on the safe side can have samples of their cables tested in the LAPP laboratory against the substances used within the production environment.
Production downtimes can be avoided by using cable types suitable for the application. But buyers often turn to cables that have worked well in other applications, for example cables with a “normal” PVC sheath. However, a small change in the composition of a chemical can lead to completely different aging behavior. The experts in the LAPP laboratories know this. The laboratory in Stuttgart alone has tested 650 substances so far, including oils, cleaning agents and cooling lubricants in many variants. However, it is impossible to think of every conceivable combination in advance – especially as customers usually do not inform their suppliers of this. After all, customers often don’t know what exactly is being used. An example from the food industry: production facilities are often cleaned by external companies using aggressive substances, whereby these companies do not tell their customers which chemicals these substances contain. Even changing the cleaning company then becomes an incalculable risk.
Air humidity as reaction accelerator
LAPP experts recently learned what can happen if a customer handles cables and chemicals too carelessly at a chemical company in Thailand. There, the outer sheath of some cables literally melted. After just one to two weeks, all that was left was a sticky mass. The cause was caprolactam, a basic material used in polyamide production, which quickly dissolved the PU sheath. In this case, the cables met dust or solid flakes of caprolactam. Due to the high humidity, the flakes absorbed water and reacted with the sheath material. With a resistance test, the LAPP laboratory experts found cables that are resistant to caprolactam and that to this day are still in use without any failures. Specifically, these are cables from the ROBUST range which are also well suited for use in the food industry and can also withstand high-energy UV-C radiation, for example in air disinfection devices.
LAPP now operates laboratories in Germany, Italy, France, the USA, South Korea, Singapore, and India, among others. “We can respond quickly to these kinds of inquiries,” promises Jens Kärcher, Global Coordination Manager Laboratories at LAPP. In most cases, the test is carried out as follows: several pieces of the sheath material are placed in a glass flask and covered with the liquid that is suspected of being a perpetrator. The temperature is then increased to speed up the aging process. This takes a few days to weeks. The first test after this is always a mechanical test, where the tensile strength and elongation are determined in a device and compared to the brand-new material. The laboratory experts also assess whether the material has shrunk or swollen. If necessary, they weigh the sample to check whether parts of the material have dissolved or whether liquid has been absorbed.
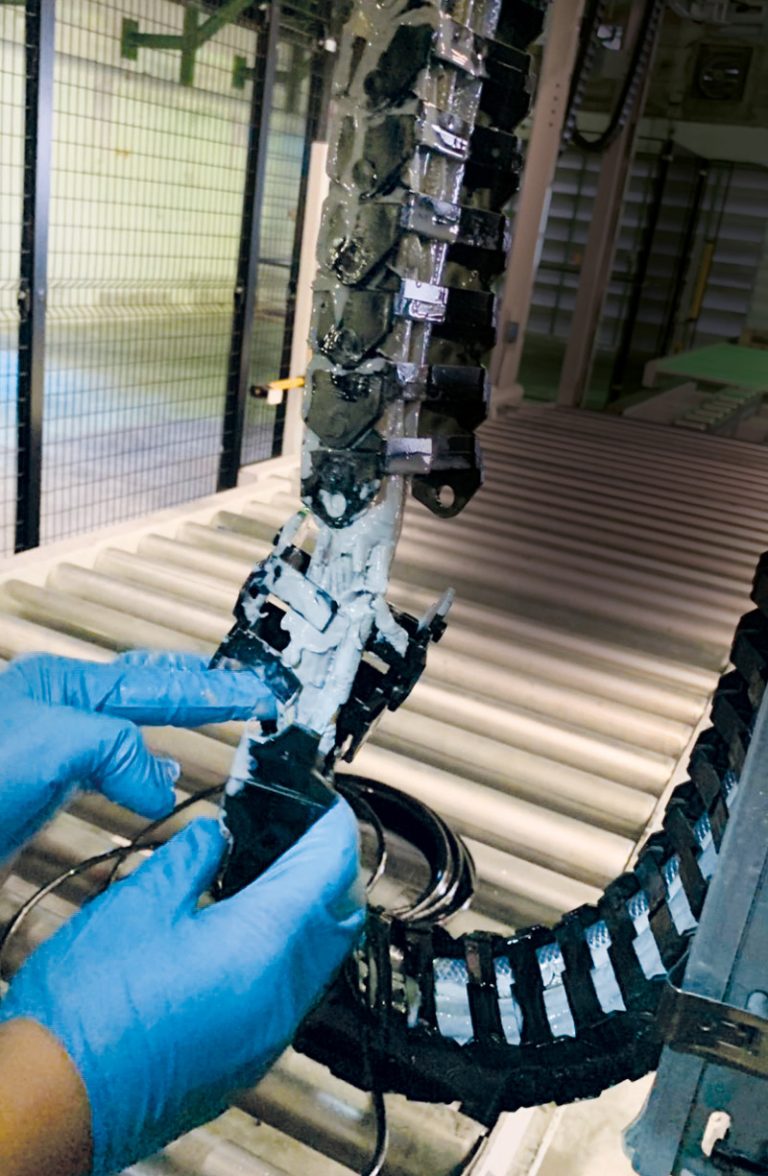
Particularly critical hygiene areas
Ecolab, a US company that provides products and services for industrial cleaning and hygiene, for example in the food industry, laundries, or hospitals, has more far-reaching requirements. At Ecolab, it is also necessary to carry out a visual inspection of the plastic samples: is there discoloration, has the surface has changed? A function test is also required by Ecolab to measure whether the dielectric strength of a cable has suffered.
A pasta producer in Italy also experienced a surprising failure. There, the cables met synthetic transmission and multi-purpose oil. Here too, the plastic became brittle at some points. The user did not expect this because they had not expected that the oil and cable would be exposed to high heat. The test in an oil bath at 110° Celsius showed clear signs of dissolution of the plastic after two days. In this example, the LAPP laboratory was also able to recommend a more suitable cable type.
In conclusion, if you want to avoid unpleasant surprises, you should contact the experts at LAPP in advance when selecting cables. They can find the right product for any tough environment.