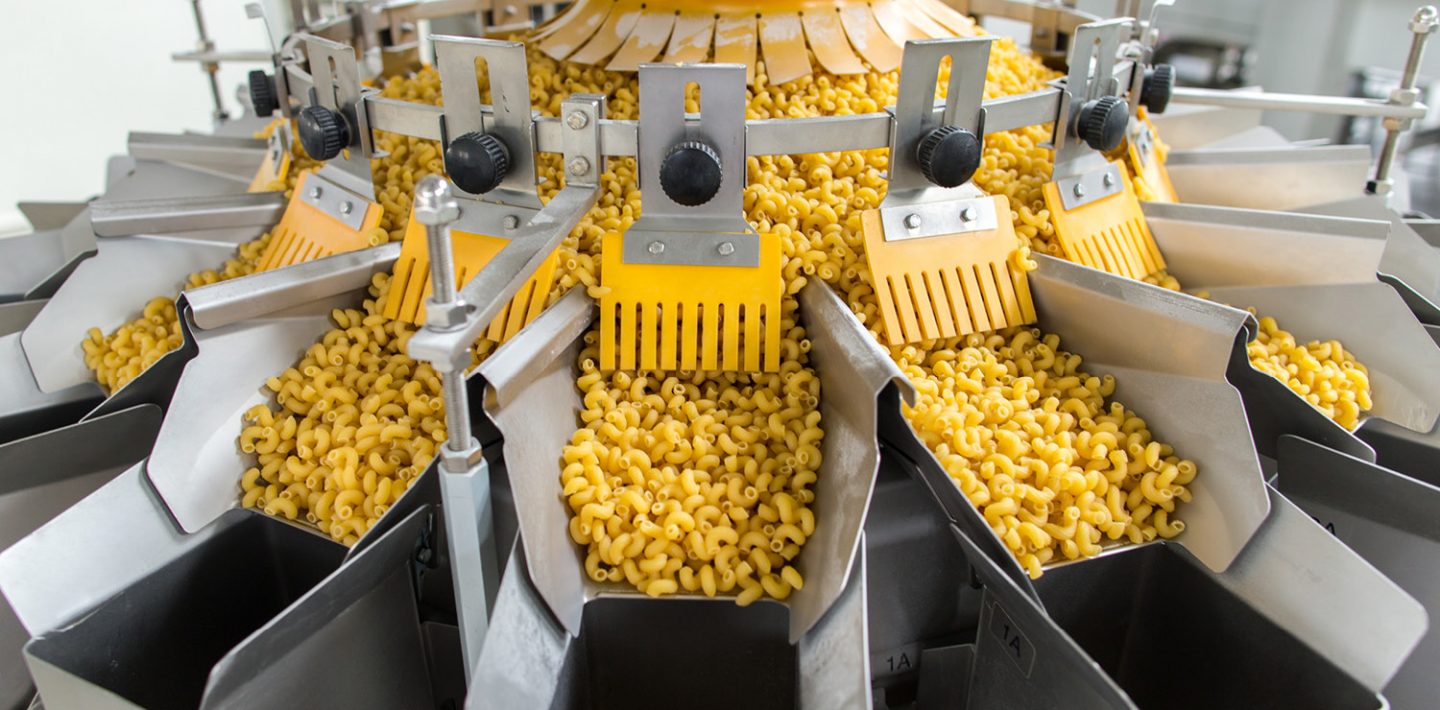
During the coronavirus pandemic, there has been a lot of public interest in the subject of hygiene, especially in the food industry and particularly due to infections in slaughterhouses. The situation has reiterated that hygiene is not something that takes care of itself in food processing; it takes a constant effort to maintain. This also applies to LAPP. “Hygiene measures have been tightened up even more because of coronavirus,” says Joachim Strobel, product manager for EPIC® connector systems. “We currently have a few new connector products in development.” They are designed to ensure that germs cannot adhere to them, and can also be cleaned using hot steam and aggressive cleaning agents.
LAPP has already built up an extensive portfolio of similar products. However, customers sometimes demand special solutions. LAPP has developed exactly this kind of solution for an Italian manufacturer of drying systems for pasta. It is a circular connector that supplies the fans used to dry the pasta. The air flows through the huge drying chambers at 100 to 130 degrees Celsius.
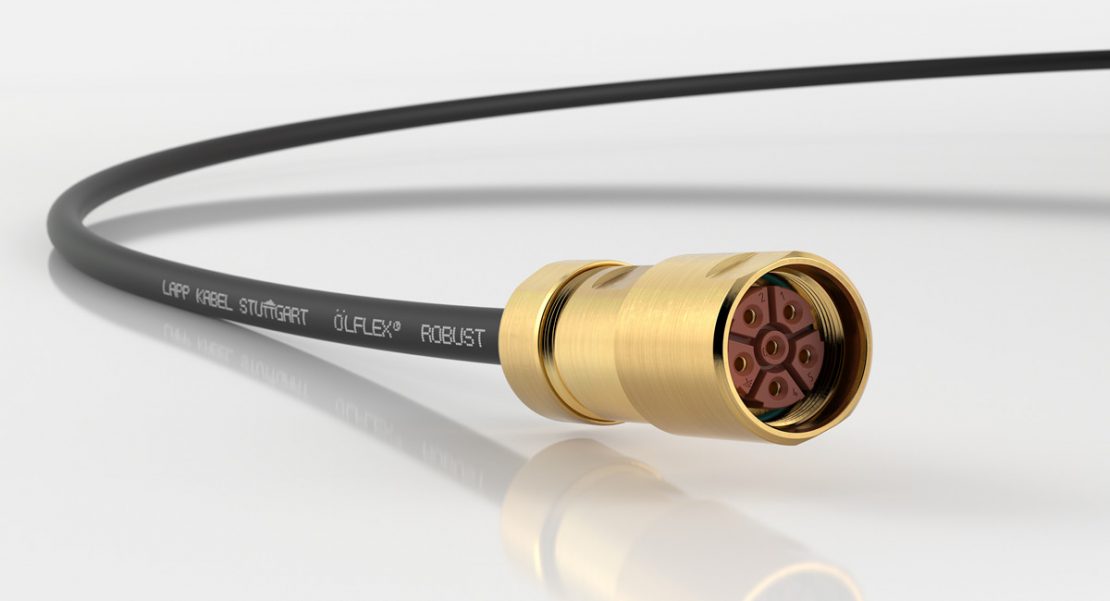
Drying in a hot bath
In the past, the fans were hard-wired, i.e. bare conductor ends were screwed into terminals. This took even qualified electricians several minutes, and less experienced electricians could even confuse the wires. And if a fan fails, every minute is precious. In a large drying system, an hour of downtime can mean a production loss of several tonnes of pasta.
The manufacturer of pasta drying systems therefore decided to use special connectors for connecting the fans in the future. The LAPP engineers recommended a special copper alloy as an alternative to expensive stainless steel. It can withstand the required temperatures and the acid that evaporates from the pasta, but is still relatively easy to work mechanically, meaning that the cost of the connector is not much higher than that of a standard product. The housing also has good EMC properties with good mechanical stability. “Together with the customer, we developed the connector system and tested it thoroughly for a year. In food production, every eventuality has to be considered and checked,” said Joachim Strobel.
Nice and smooth
The EPIC® connectors are designed in accordance with hygienic design principles, i.e. with the fewest possible corners and edges. Here too, the material used has a number of advantages. It has a smooth surface, even without a coating that could flake off and fall into the product zone.
Since every chain is only as strong as its weakest link, a great deal of attention was also given to the cable. It also has to withstand mechanical stress, lactic acid and heat. LAPP silicone cables were chosen. They are resistant to vegetable and animal fats and can withstand temperatures of up to 180 degrees Celsius. The seals in the connector are made of fluorinated rubber (FKM), a high-quality sealing plastic for many applications. To prevent errors during assembly, LAPP recommends pre-assembled cables and connectors.
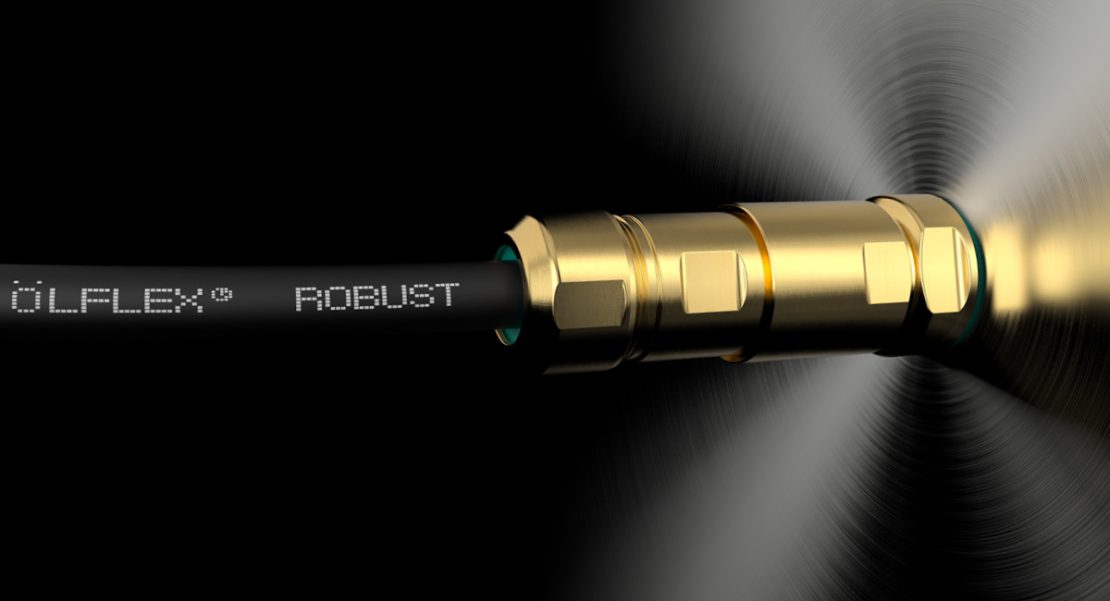
Withstands even unfamiliar cleaning agents
The customer tested the new connector with patented connector geometry for a year in one of its production systems. The test was successful and technical approval was subsequently granted. The new connector will be used on the fans in the coming generation of drying systems. “The concept has a lot of potential for other applications in the food industry, and stainless steel connector versions are also feasible”, said Joachim Strobel. He explained that food processing machine manufacturers often do not know which cleaning agents customers will use on the machines. Often, even the food manufacturers themselves do not know. This is because cleaning is often outsourced to subcontractors who do not always provide precise information about the substances they use. However, the example of the user described shows that LAPP engineers work with customers to find the right solution for every application.
Download brochure