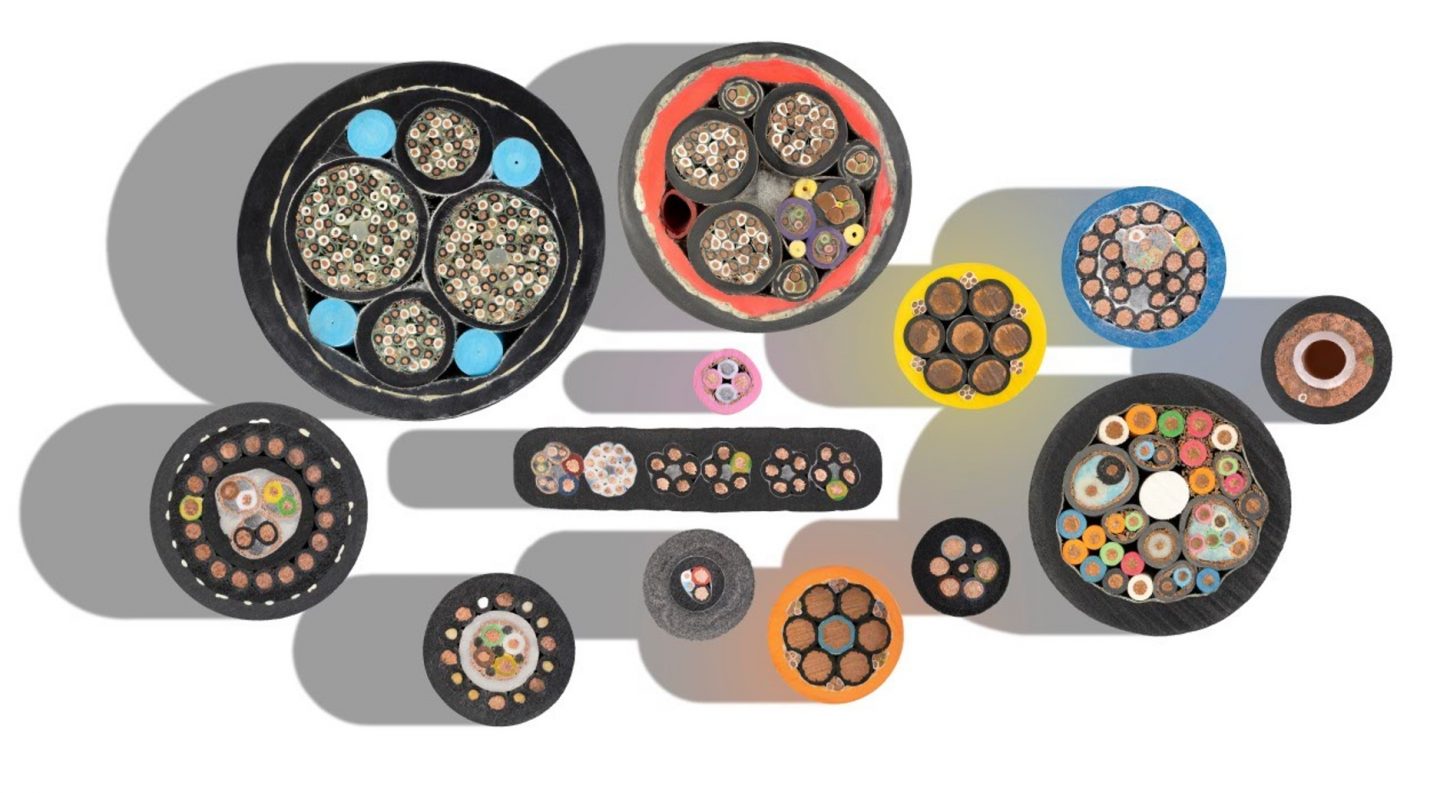
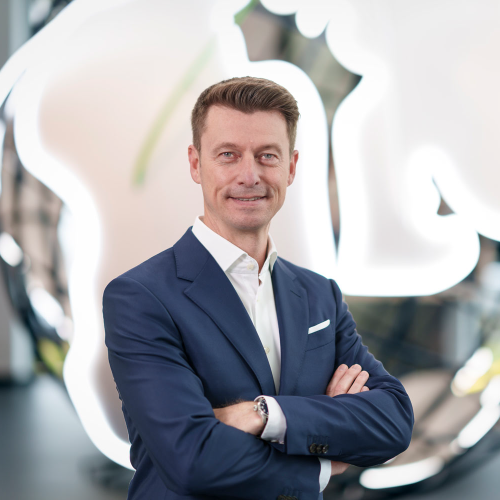
“It has always been our claim that we can fulfil customer wishes, no matter how elaborate or complicated they may be. Our company founder, Oskar Lapp, has always done this and we continue to do so today. The only difference is that we have built up a huge pool of expertise over the past decades and can find solutions for almost any customer problem,” emphasises Hubertus Breier, Chief Technology Officer at LAPP.
In the past five years alone, LAPP has launched over 200 new products on the market – many of which have an innovative character. Just a few examples include the ETHERLINE® GUARD condition monitoring device for preventive maintenance of important data connections, the ÖLFLEX® SERVO FD zeroCM® motor connection cable, which has been proven to reduce leakage currents by up to 60 % compared to conventional motor cables thanks to the innovative zeroCM® technology, and the ETHERLINE® FD bioP Cat. 5e Ethernet cable with a bio-based outer sheath made from over 40 % renewable raw materials.
In addition, LAPP fulfils individual special services for customers. A uniquely broad spectrum of expertise makes this possible. This includes the areas of mechanical design, material development and production, plastics processing, functional design & simulation, analytics and mechanical testing as well as sensor technology & IoT.
1. Mechanical construction
The construction of a cable is designed according to standard specifications and, above all, according to the respective application requirements. Permanently moving cables in drag chains, where the mechanical load is high, are particularly demanding. Such cables must function reliably for several years and over many millions of bending cycles. Therefore, all construction parts, from the copper strands to the insulation, the braiding and the jacket, must be able to withstand these high demands. For drag chains, for example, ultra-fine stranded copper is used instead of solid round material for the conductor structure. This is significantly more flexible. A high resistance to bending cycles is achieved through short lay lengths (the length of the distance that a single stranding element requires for a complete circuit) in the stranding. The shorter the lay length, the more flexible the finished cable. Shielded cables also require a design with an inner sheath to protect the cores from abrasion with the braid. The shield also follows a shorter “lay length”. A mechanically robust jacket (e.g. made of TPU or TPE) is also important, which is flexible and abrasion-resistant and can withstand permanent bending while remaining in permanent contact with the drag chain.
Constructive design also plays a major role in plug connections, e.g. in solar plugs: Here, a stable electrical connection without heating the contact point is particularly important. The plug also needs a secure and effective locking and unlocking mechanism. The selection of suitable materials and a suitable design reduce friction and wear. With the smallest installation space and highest voltage, the clearance and creepage distances must also be optimised. Added to this is reliable assembly – pre-assembled or on site at the customer’s premises. To meet these requirements, LAPP uses high-quality, wear-resistant contact materials with appropriate surface treatment (e.g. corrosion resistance) and an optimised design (e.g. enlarged contact surface). Insulation materials with low water absorption are used (e.g. to prevent flashover at the smallest distance). And to avoid errors during installation, LAPP has developed pre-assembled solar cables that guarantee reproducible high quality.
2. Material development and production
The UV resistance, flexibility or sustainability of cables depends on the customised plastics and additives for the sheathing. Up to 20 formulation components are possible for a sheathing. These formulations are the most important expertise in plastics materials technology. Through compounding, the properties are customised for the respective application. Until now, LAPP has sourced these granulates from external manufacturers. The company recently acquired its own compounding plant in Bhopal, India, and can now mix compounds itself and thus also “design” them. The current focus is on PVC. This means that the entire process chain, from the raw materials to the ready-to-use compound or granulate, is in the company’s own hands. However, due to the necessary quantities, LAPP continues to work closely with external manufacturers worldwide. This focus also contributes to the development of sustainable products, which LAPP is working hard to develop. The first “organic” product recently went into series production. The ETHERLINE® FD bioP Cat.5e data cable consists of a bio-based outer jacket and ensures the same product properties as the fossilised plastic version.
3. Plastics processing
Put simply, a cable consists of plastics and metals. Above all, the right choice of plastics influences the application-specific behaviour. Here is an example: In the solar or rail industry, the highest demands are placed on the jacket material. The focus here is primarily on resistance to solar radiation (UV light) and moisture, the customer’s desire for reduced wall thicknesses, a higher current load, a longer service life and improved fire behaviour. If – as in these industries – a normal plastic is no longer sufficient, cross-linking processes for the plastics help to increase the service life of the cables. The associated electron beam crosslinking is an established process for optimising and strengthening plastics using ionising electron and gamma rays. After irradiation, the plastics have significantly improved properties in terms of heat resistance, stability and abrasion resistance. To this end, LAPP has set up and commissioned electron beam crosslinking plants in Korea and India. In addition to the existing production facilities, LAPP has established a special triple extrusion system in Bhopal, India, which enables plastics to be extruded in three layers in a single production step. These include material systems such as XLPE (cross-linked polyethylene), ZHFR (halogen-free, flame-retardant compound), NYLON (stronger and more elastic than polyether), EPDM (special rubber, used for swimming pool linings, among other things) or EVA (ethylene vinyl acetate, used for shoe soles, among other things).
But plastic is not only extruded at LAPP – piece goods such as screw fittings and connectors are injection moulded. For the injection moulding of connectors or other system products, e.g. from the SKINTOP® portfolio, multi-cavity moulds with hot runner technology are used, for example. Advantage: One mould (hollow mould for plastic injection) with several cavities produces more parts. This reduces preparation time and increases productivity. Hot runner systems produce less plastic waste, as the plastic is kept liquid until just before the cavity.
4. functional design & simulation
In order to reflect the many mating cycles during the service life of an electric vehicle, 10,000 mating cycles must be verified for the approval of charging cables.
High insertion forces can lead to wear and damage, which reduces durability. In addition, there are other factors such as weather influences and temperature fluctuations that place certain demands on the design. The finite element method (FEM) is used to develop models for an optimised loading pin mechanism, which also allows the interaction of material and contact to be taken into account. In addition, a detailed contact force analysis supports tribological design optimisation.
As electromagnetic interference is a recurring problem when using frequency converters, LAPP has developed the innovative zeroCM® technology, which has been proven to reduce leakage currents by up to 60 % compared to conventional motor cables. The LAPP research team first designed a mathematical replacement model of the cable and optimised this digital twin in terms of electrical engineering simulations to achieve an electrically symmetrical cable design. The theoretical results were validated internally and with external partners through experimental measurements.
In addition, the wire insulation system must be adapted to the respective application in order to withstand the electrical fields occurring in the application, even in the event of voltage peaks or travelling wave reflection. Conductors with different potentials and dielectrics physically form a capacitor whose capacitance favours signal distortion in cables, slows down the speed of signal propagation or can place additional load on the output stages of clocked controllers. The aim is therefore to optimise the capacitance by selecting the right materials and wall thicknesses as well as ensuring high process stability during production. LAPP uses the 2D and 3D finite element method (FEM) to analyse the potential distribution within cables and improve the field distribution. For example, the capacity-optimised ÖLFLEX® SERVO 796 CP and the ÖLFLEX® VFD SLIM were developed, the latter with a semi-conductive layer for field homogenisation. LAPP also uses FEM to optimise the current density distribution. The skin and proximity effect can reduce efficiency, particularly with large cross-sections, even in the low-frequency range. The FEM model helps to optimise cable dimensions, select materials and improve current and heat distribution.
5. analysis and mechanical testing
Customers expect uniform quality standards worldwide from internationally operating companies. To guarantee this, LAPP operates laboratories around the world – in Germany, Italy, France, the USA, South Korea, Singapore and India – totalling 13 locations worldwide. They are equipped with state-of-the-art measurement technology and established processes to ensure maximum standardised test conditions. Tests are also carried out here in direct contact with customers.
During the analytical testing of cables and connectors, for example, weathering tests are carried out in the laboratory or outdoors to ensure long-term resistance to UV radiation, moisture, temperature fluctuations and other environmental influences. These outdoor weathering tests help LAPP to optimise its high-quality products for harsh environments and to gain “real” field experience in test trials.
In addition to energy cables, data cables, which are primarily used in drag chains or robots, are also tested in the dynamic endurance test. The focus here is on signal integrity despite high dynamic continuous loads. In the drag chain test, the cables are permanently monitored and the number of cycles is recorded. A communication module links this data. This allows the measured values to be recorded fully automatically during dynamic tests and application-orientated statements to be made about the signal integrity.
Assessing the fire behaviour of cables and wires requires extensive testing. The European Construction Products Regulation (CPR) law describes strict requirements for all products that are permanently installed in buildings and in which people are present. Since April 2022, LAPP has had a state-of-the-art test laboratory at its Edolo site in Italy where CPR-classified cables are tested. The 300 square metre facility now offers all the necessary testing options, including a four metre high chamber in which cables are suspended vertically and exposed to a flame. A light sensor measures the density of the flue gas, for example. The laboratory also carries out tests that are not yet required by the CPR, such as fire resistance tests. Because toxic gases and smoke can be produced during such tests, the laboratory is equipped with an activated carbon filter and an exhaust gas scrubber.
6. Sensors & IoT
LAPP has continued to expand its portfolio of services over the past few years. In addition to configurators, customised cables or assemblies, digital self-services on the website and just-in-time deliveries, IoT and sensor-based services have recently been added:
Many companies claim that they do not have a reliable overview of their own cable inventory. The LAPP eKanban is an intelligent and networked cable inventory management system that promises lower process costs and efficient warehousing and helps to prevent production downtime. It works with a smart sensor that generates data points about rotations on the cable drum and sends them to the cloud, providing customers with digital and real-time information about the fill level of the cable drums. This makes it easy to see how much cable is still available on the drum at any time and from anywhere.
With the market launch of the ETHERLINE® GUARD as a monitoring device for the service life of ETHERNET-based data lines up to 100 Mbit/s three years ago, LAPP was already driving forward the topic of IIoT and software/algorithm development. Several parameters are recorded without inserting an additional sensor into the cable and calculated together in such a way that a service life statement can be made. This was supported by extensive measurements in the LAPP test centres.
Hubertus Breier: “This wide range of expertise and customised special solutions makes us unique on the global market. Nowhere else can customers get so many solutions and services from a single source. And we still have big plans.”