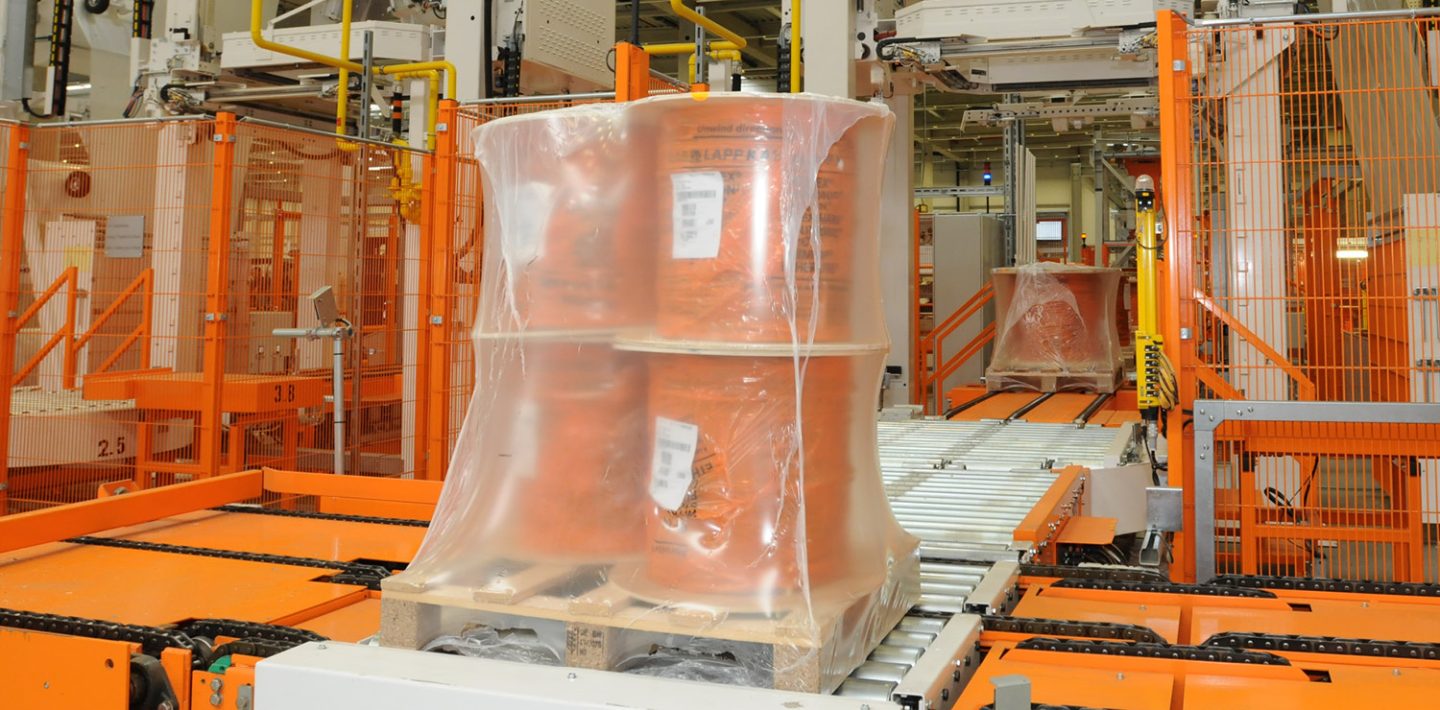
The pressure on companies to act in a more sustainable manner is constantly growing. On the one hand, from the society in which customers and business partners expect this, on the other hand, from the politics that adopt ever stricter requirements. “There is a genuine interest in pushing this issue forward in many companies, but at the same time we have to admit that economic aspects are still the most important factor, which is why we probably need this pressure”, said Pia Krebs, Packaging Engineer at LAPP. “The good thing is that sustainability and efficiency can go hand in hand if it is done right”.
She and her colleagues at LAPP have reduced plastic packaging material and increased the proportion of recycled raw materials through several internal initiatives. LAPP is also working on a process for reusing cable drums, which will make it easier for the environment and on the company’s account when it comes to the valuable raw material of wood. Three examples of the three “Rs” of circular economy – reduce, reuse, recycle, which can lead to greater sustainability and lower costs elsewhere.
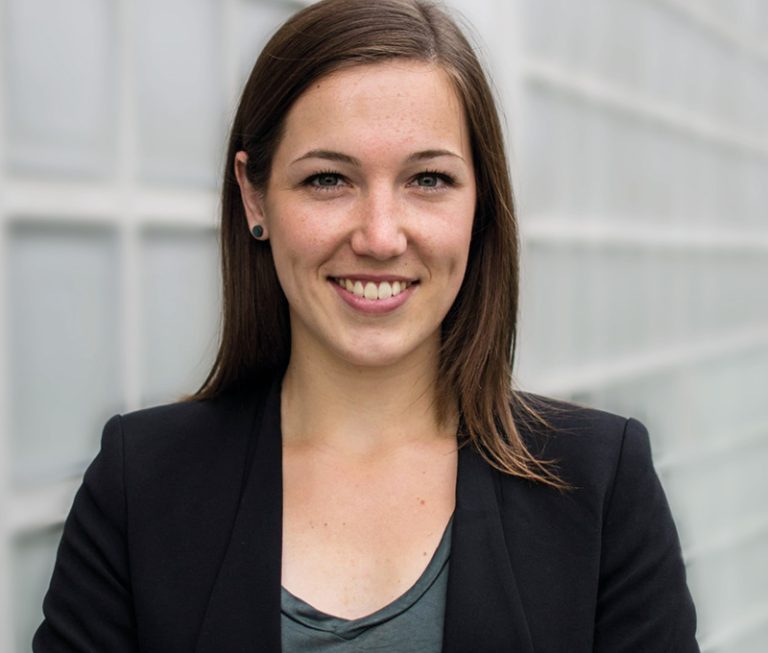
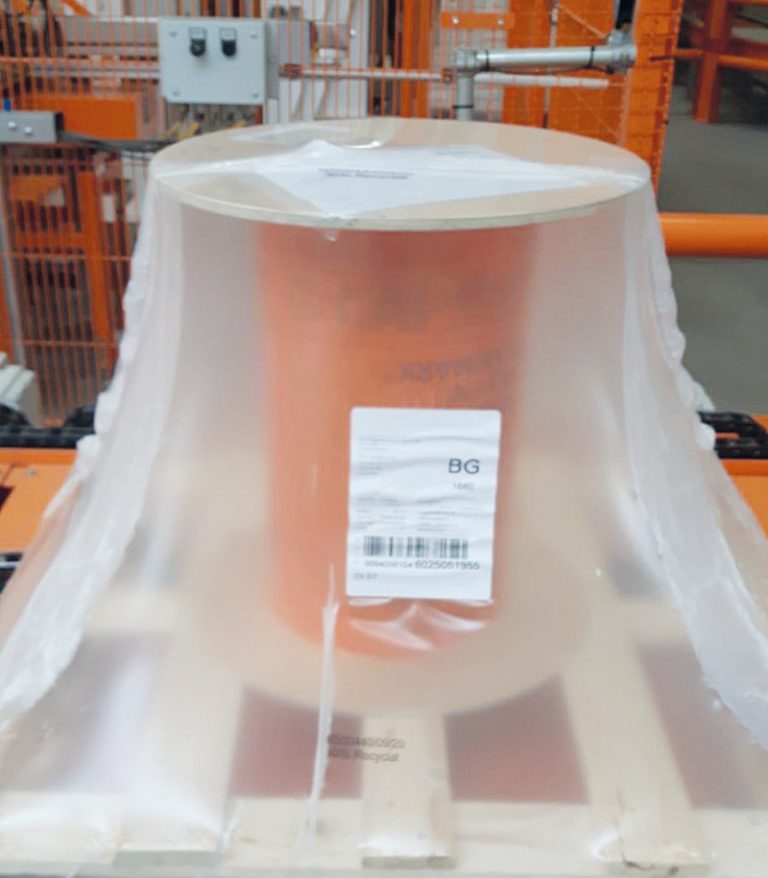
Less packaging, less costs
Sounds simple and obvious, but it’s not that trivial: anyone using less packaging saves costs and raw materials. A reduction makes particular sense for the raw material of plastic, which is usually extracted from fossil sources. Ultimately, these sources and their degradation are responsible for a significant proportion of our CO2 emissions. At the same time, the conventional use of plastics, for example for packaging products, is not based on meaningless addiction to waste, but rather fulfils a purpose. For example, packaging protects the goods from external influences and stabilises them along the transport route. This also applies to the plastic foil that LAPP uses for packaging its cable deliveries.
“We were able to save a lot of material here by reducing the film thickness from 80 to 70 μm”, explains Pia Krebs, “but we first checked using a number of tests to find out whether we could secure our load just as well”. It turned out that it was possible, and the measure is not only a success in terms of resource consumption and climate friendliness, but also already saving 30,000 euros annually. “We already use the thinner films at our Ludwigsburg sites and will also use them in Stuttgart soon. As soon as our logistics centre in Hanover is relocated, we are expecting a saving of at least 40,000 euros”, adds Pia Krebs.
As much recycling as possible
Alongside reducing, however, the packaging materials are also crucial. Ideally, where materials cannot be reduced, the recycling rate should be as high as possible in order to conserve resources and the climate. This is also obvious in theory, but it requires precise insight into practice: “First of all, we need to distinguish between ‘recyclable’ and actually ‘recycled materials’”, explains Pia Krebs. “‘Recyclable’ primarily refers to the possibility of recycling. However, if this has not actually occurred, it is merely a theoretical added value”. Secondly, the application determines how much recycled material is possible, just like with the material reduction. For shrink films, which LAPP uses to secure goods on pallets, a formulation with 30 per cent recyclate is now used. More than this is not possible at the moment because “the recyclate can act like small impurities and, if a higher proportion is used, this would disrupt the shrinking ratio”, explains Pia Krebs. But even here, a certain proportion is possible. For other foils, such as drum foils, whose function such as dust protection and branding is not restricted by recycled material, a formulation with a significantly higher level of recycled material is currently in the testing phase.
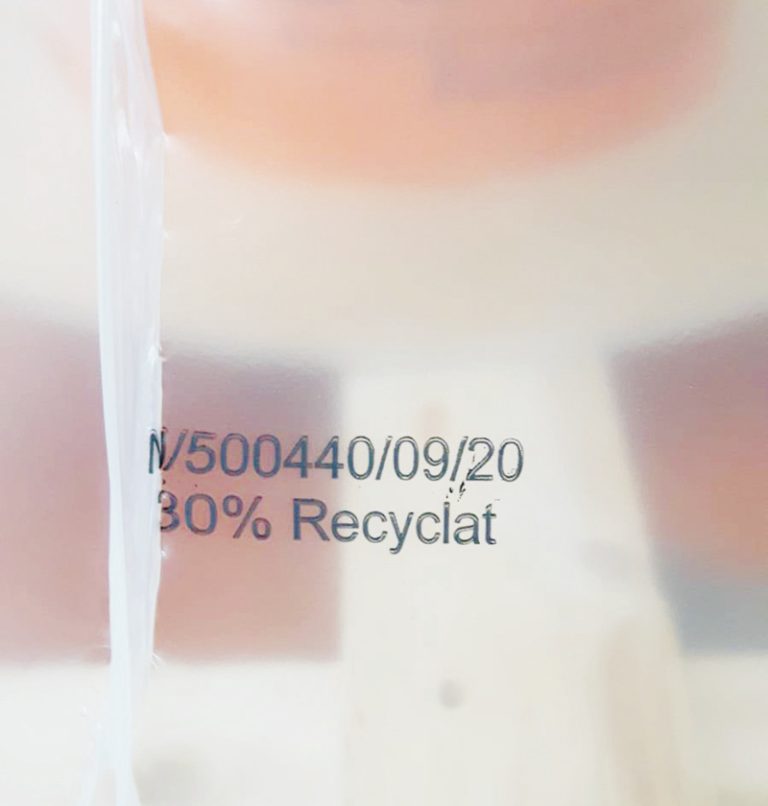
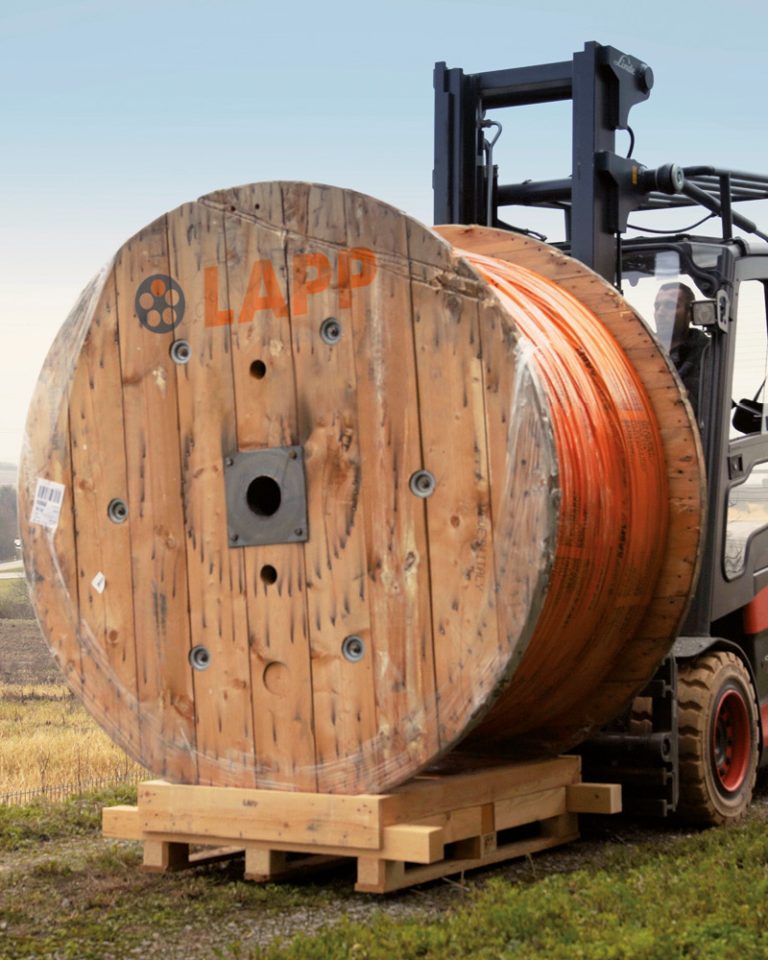
Circuit system for cable drums
Cable drums are also an important topic in the packaging of connection solutions. They are usually made from the valuable raw material wood. At LAPP they are up to 2.50 metres high and weigh up to 450 kilogrammes when they are empty. These drums are far too good for a single use. However, transporting and consolidating the empty drums is a challenge, especially for a supplier such as LAPP that supplies markets all over the world. “We used to collaborate with a service provider, but we depended on it too much and the system simply stopped working with new business areas and markets”, explains Pia Krebs. For this reason, LAPP is currently developing a process that solves these challenges and ensures that a re-usable drum can be reused several times.
“This is driven by a desire for more sustainability as well as cost issues”, says Pia Krebs. And regarding potential legal requirements for the future: “We are currently well positioned and still feel relatively little pressure from the legislator in Germany, but we are seeing developments such as the extra tax on plastics without recycled content in Italy and England. This will also happen here at some point. That is why we do not want to be surprised by anything, so that we are now proactively adapting to it with our measures. We can only advise every company to do the same”.
To LAPP Recycling