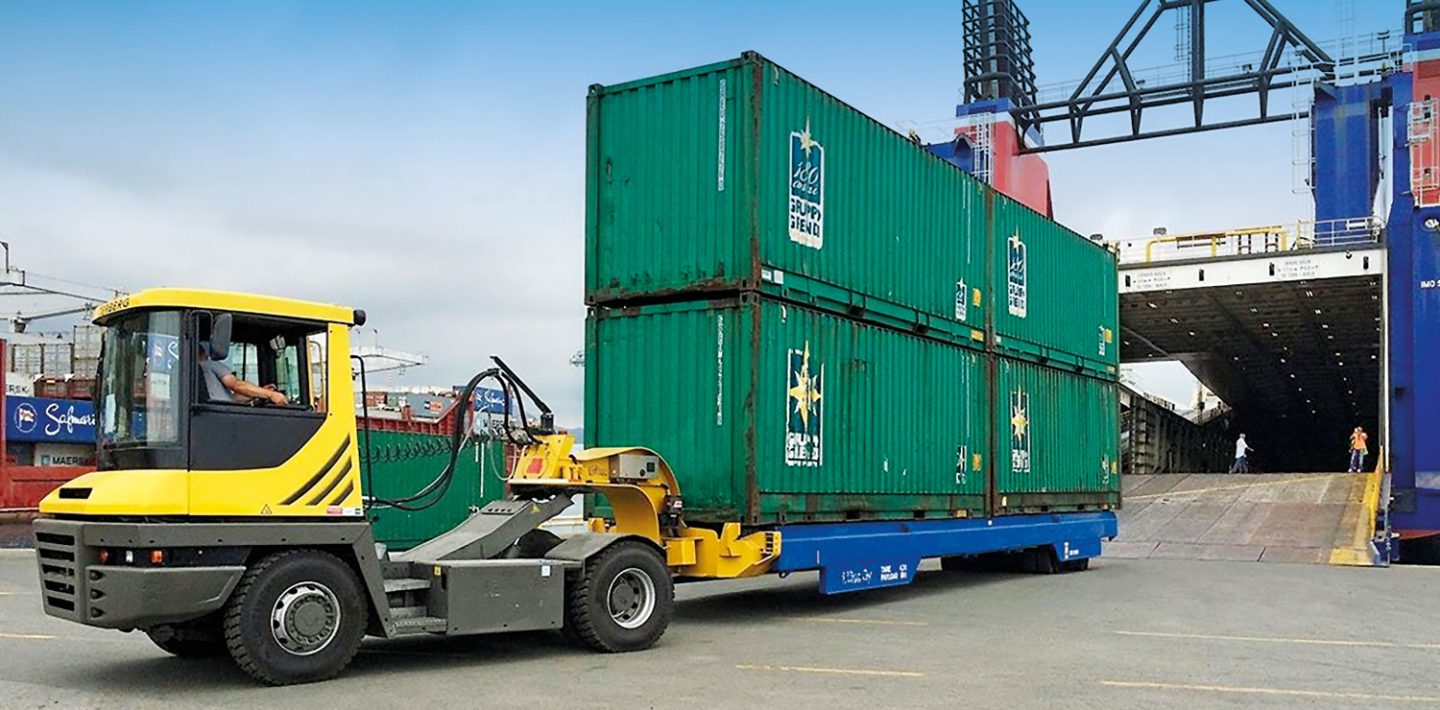
A new customer, a high demand: companies quickly get under time pressure. Manual cabling can then become an annoying time killer, and in the hectic pace, mistakes happen, plus the added value is zero. More and more companies are getting around this by placing the assembly of cables, cable harnesses and drag chains in the hands of a specialist: LAPP. With LAPP Harnessing Solutions, the world market leader for integrated cable and connection solutions has created an offer for ready-made assemblies that has become a real success model. “This saves our customers time, reduces warehousing, simplifies ordering and increases quality,” emphasises Pavla Borovianova, Market Manager for LAPP Harnessing Solutions. LAPP assembles the components of the eight LAPP brands into one system. The customer gets everything delivered ready to use.
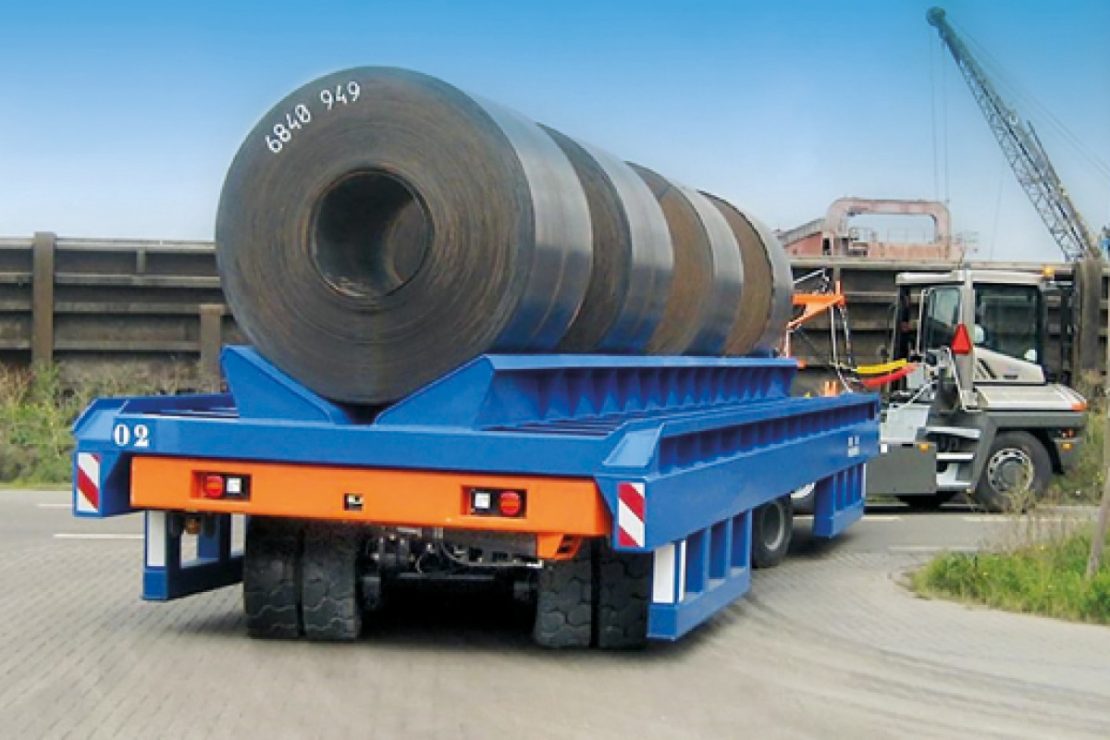
Trailers for shipping containers
These advantages have also convinced a global provider of logistics solutions for heavy goods in ports or terminals. Their speciality is heavy trailers with an overlying cassette that holds the goods to be transported – for example, heavy cable drums or containers. The trailer has steering wheels and a hydraulic suspension system that levels itself and prevents the load from tipping over. All these systems are controlled and monitored by the trailer’s central system. To connect these systems and sensors, LAPP products are used. As the environmental conditions in ports are aggressive towards electrical equipment, the cables and connectors must be resistant to moisture, corrosion and hydraulic oils. Failure would be costly, for example if the unloading or loading process of a cargo ship were interrupted.
The provider for logistic solutions and heavy goods has been sourcing components from LAPP for many years, including ÖLFLEX® 400P, UNITRONIC® PUR M12 sensor cables, SKINTOP® cable glands and the SILVIN® RILL PA6 conduit system. Especially the durability and reliability of LAPP’s solutions are convincing, that is why also assembled products such as cable harnesses from the LAPP Harnessing Solutions range are now purchased by this customer. “This saves our costumer a lot of time when assembling the trailers”, explains David Nowacki, Application Engineer at LAPP.
In the first phase, LAPP provided several samples, which were tested and then approved and entered into the trailer’s technical documentation. Recently, delivery of the first series assemblies has begun. These are two types of wiring harnesses. They connect control units with sensors and valves in the hydraulic system. In the coming months, the provider for logistic solutions will work on standardising its mechanical and electrical solutions. “Then we will prepare a new type of cable harness together with the customer,” says Dawid Nowacki, Application Engineer.
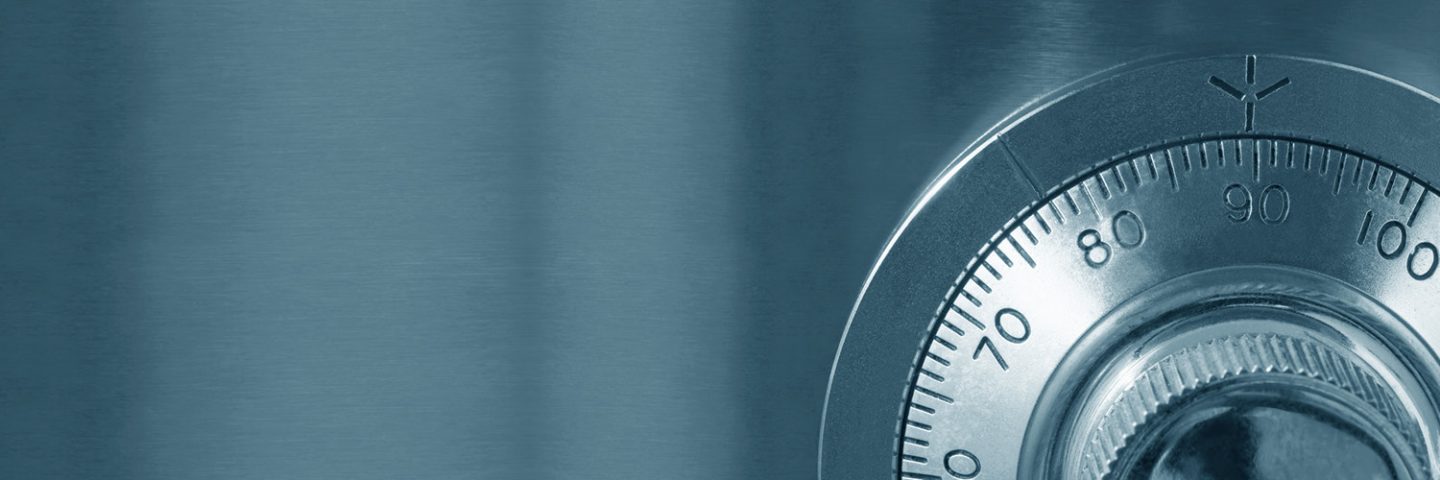
Safely stored
The second case is all about maximum security – this time of cash, jewellery and other valuables, about a leading manufacturer of safes, document storage, gun cabinets and banking systems in Europe. Łukasz Żelichowski, Business Development Manager at LAPP explains: “Our customer approached LAPP with the wish to develop a special cable.” The colour of the outer insulation was to be grey and each individual core was to be unidentifiable, i.e. without any printing and also in grey insulation. This should make it difficult to identify connections within the cable harness and for competitors to copy the solution. In addition, each of the cores should be crimped according to customer requirements.
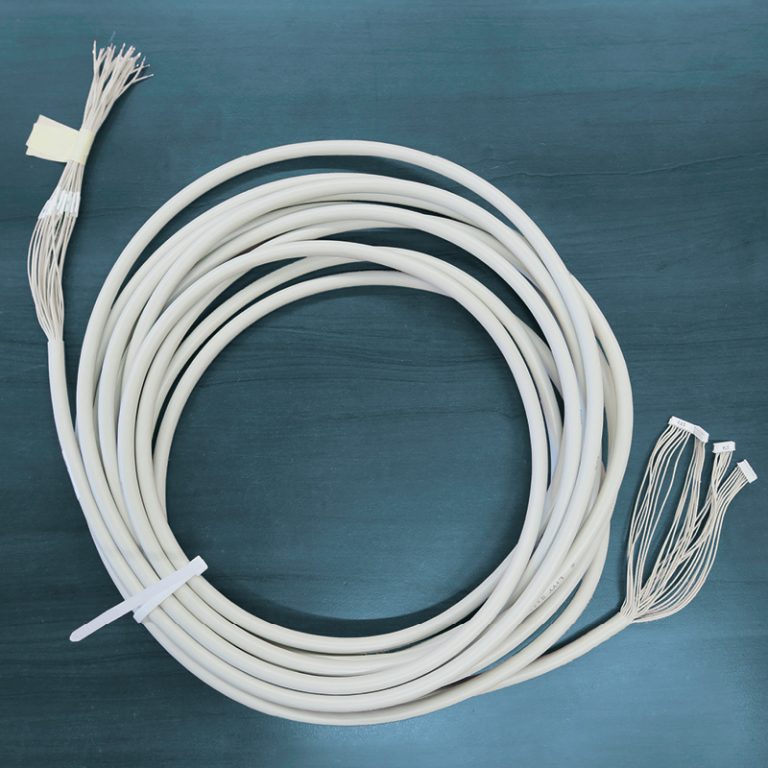
LAPP created documentation that included the lengths, the geometry of the wiring harness and the production requirements. The next step was to supply a sample for approval by the customer before the start of series production. The wiring harness bears the FLEXIMARK® LCS 35 WH self-laminating label, which indicates the date and series of each wiring harness. LAPP already produces the wiring harness for this safe manufacturer in series, the annual requirement is 1000 pieces. Łukasz Żelichowski says: “Thanks to LAPP, they can now better protect our intellectual property against competitors.”