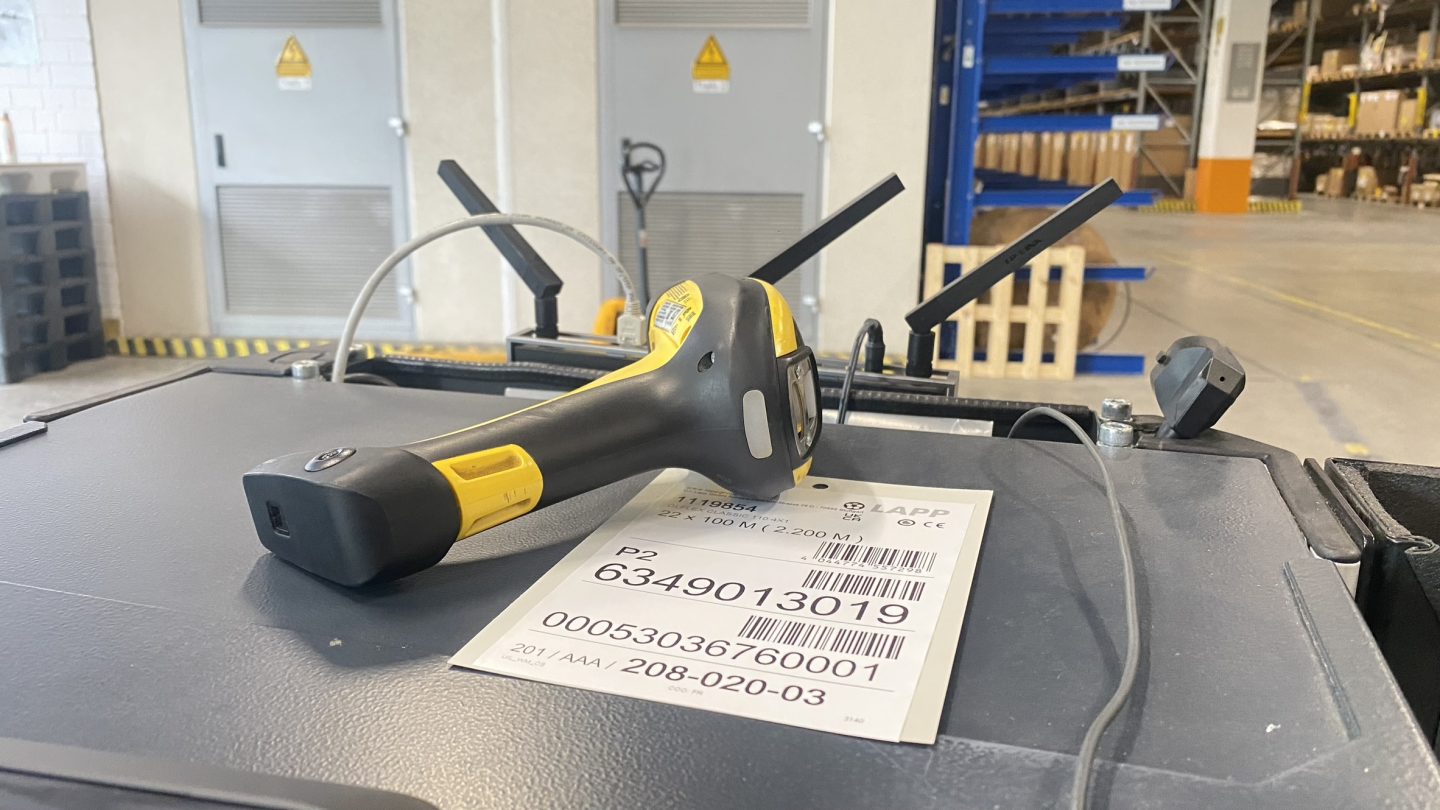
Logistics is sometimes reminiscent of the cult game, Tetris. New components – in this case packages or entire pallets – are constantly being added and have to be moved quickly to the right place. If you make mistakes, chaos will ensue. This is also the case in logistics. However, processes are not as two-dimensionally and clear in reality as they are in a game. They are more complex and extensive. For instance, intralogistics at LAPP, the Stuttgart-based global market leader for integrated solutions in the field of cable and connection technology, comprises three different areas of work: incoming goods, cutting processing and dispatch. In between, there are clear process chains during which packages are moved. And these require precise coordination.
To be able to track the packages and their content at any time, LAPP Logistics employees use self-adhesive labels to mark the goods. To this end, the logistics employees are equipped with printers at their workstations. Whenever they process a package, they enter the necessary data into the PC, print the label, pull it off the backing liner and stick it onto the package. This allows the goods to be tracked in the logistics at any time. Processes subsequently run smoothly. “The system initially offers many advantages,” explains Allen Frederick, Logistics Systems and Services employee at LAPP, “but it presents us with a crucial problem: it produces masses of special waste.” This comes in the shape of a yellow supporting foil, which is no longer usable once the labels have been removed and ends up in the trash. With four million labels a year, this adds up to quite a lot, Frederick knows. The carbon tape needed for printing also has to be replaced regularly. This creates even more waste.
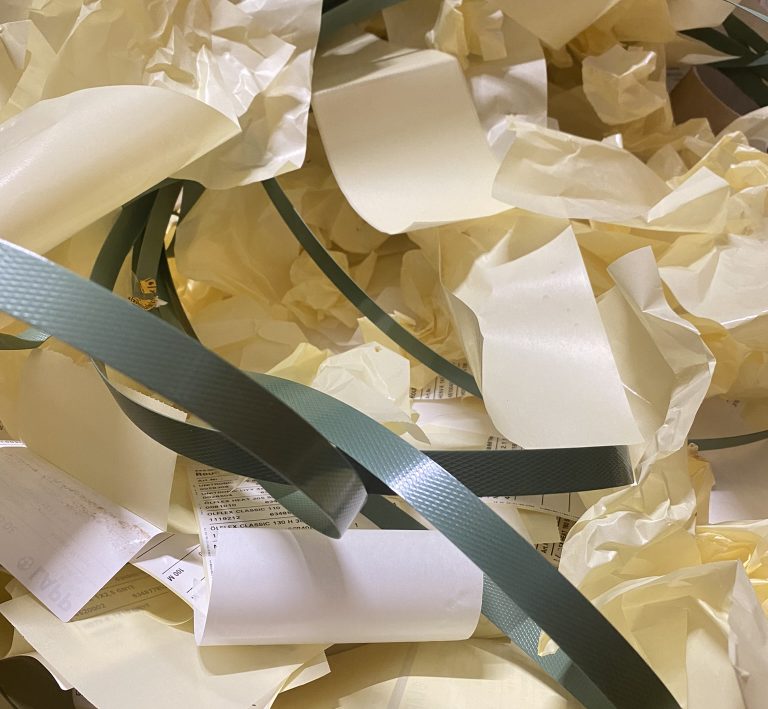
A rubbish trail from Stuttgart to Lübeck
Years ago already, this was a thorn in the eye of Allen Frederick. At LAPP Logistics, he is part of the first-level support team at LAPP, which deals with hardware and software problems – and is also constantly working on optimising existing systems. “If you take a map of Germany and draw a straight line from Stuttgart to Lübeck – then you have the length of the trail of supporting foil that gathers in our garbage at LAPP in Stuttgart every year”. That’s around 571 kilometres. And the rubbish trail is not just long, but also heavy: it weighs 5.5 tons. More than five small cars. Mr Frederick had two problems with this: “Firstly, disposal is expensive. With this amount from Stuttgart only, the costs for LAPP amount to just under 1,400 euros per year,” explains Mr Frederick. Secondly, both disposal and the production of backing liner and carbon tape are a burden for the environment. Production of the liner material for the needs of LAPP logistics alone gives rise to five tons of CO2 per year. This is equivalent to half of Germany’s annual per capita CO2 footprint.
The solution without liner material
“There must be other labelling systems,” Mr Frederick thought in 2019. Getting rid of single-use products in households or gastronomy has been a topic of discussion for a long time. Why should it not be in logistics too? But the search for alternatives was difficult – there simply were none. Frederick was not satisfied with the situation and stuck at it. In February 2021, it suddenly seemed like the riddle had been solved: “Linerless labels” from Zebra Technologies. These do not need the silicone-coated backing liner, as they are self-supporting. Rather than being individually prefabricated labels, they are a rolled up label tape, with the adhesive surface on the bottom and the printing surface on the top. As the tape has a special adhesive on it, it can be rolled up without any problems. The adhesive surface sticks to the printing surface below. A finished roll is inserted into a printer specially designed for the process, which then prints on the top without any carbon tape – since a thermal printing process is used – and cuts the respective label to the required length using an integrated knife. The finished labels detach themselves easily from the surface underneath without leaving any excess backing liner behind. There is no need to dispose of carbon tape either. Subsequently, it is not just the waste that is completely eliminated. Even more labels are available per roll – a total of 748, as opposed to 475 before.
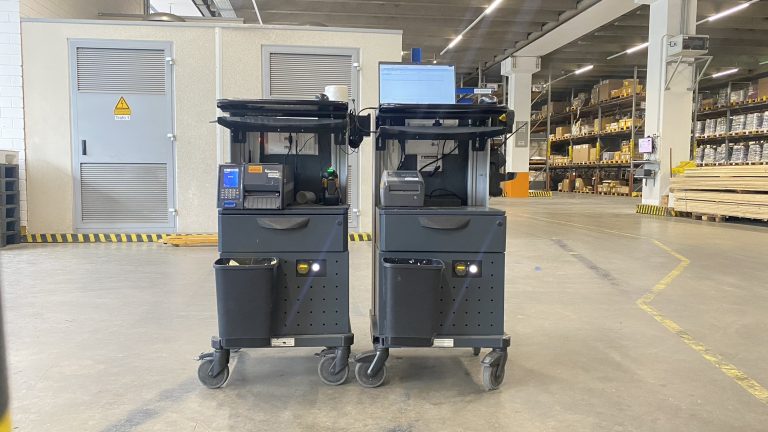
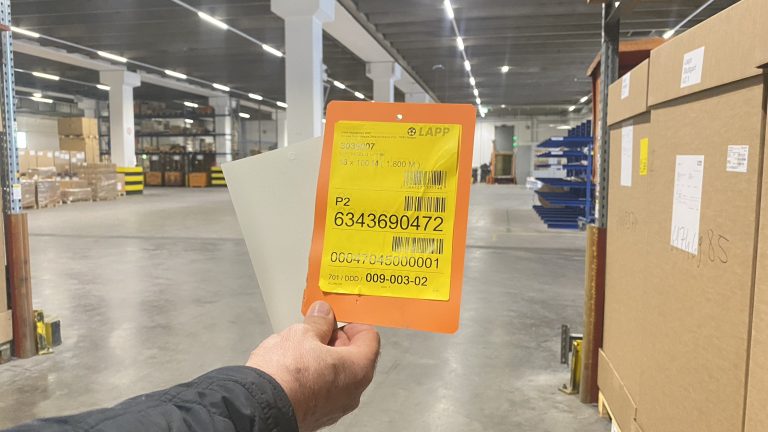
Putting it to the test
Mr Frederick was convinced of the idea and intended to start a test run for this process at LAPP’s logistics department in Stuttgart. Maria Dobritzsch, Global CSR Manager at LAPP, immediately gave the green light for the trial run following a visit to the logistics centre in Stuttgart. “LAPP is always working on making processes more sustainable and saving resources,” Ms. Dobritzsch explains, adding: “Employees play a crucial role here. They know the processes very well and can thus easily identify optimisation potentials.“
At the beginning of 2022, a total of three stations were converted for the three-week trial run – in dispatch and incoming goods. The processes were observed over a period of several hours. “In the beginning we had a concrete challenge,” recalls Mr Frederick. “Printing in a fast-track mode.” If, for example, employees want to print 30 labels in one step, this was not a problem with the backing liner. The print order with the corresponding number of labels was entered and then a long ribbon with finished labels was emitted from the printer, which could be pulled off bit by bit. This, however, does not work with the linerless process because the label has to be removed immediately from the printer. According to Mr Frederick, the concern was that this kind of collective printing would result in a clump of labels that would all stick together. However, there was a simple solution: a sensor in the printer now ensures that the printing process pauses at high printing volumes until the label has been removed. This avoids any sticky chaos. On the contrary: Thanks to the sequential, individual printing, there is no longer any risk of labels being interchanged, since they always have to be affixed immediately.
Cost reduction on many levels
But there’s more besides. Lots of other benefits of liner-free labelling ultimately convinced LAPP to implement the system on a large scale after the test run. On the one hand, it saves costs – not just due to the elimination of disposal. Standard printers for the linerless process cost less than half the previous devices. Less material also reduces transport costs – and LAPP requires less storage space. The endless label strip, which can be cut into any size by the printer, means that you no longer have to purchase different label sizes. Another advantage is the improved time efficiency: “In the past, we had to change label rolls much more frequently. With the linerless process, this has been significantly reduced since there are more labels per roll. This means we have less downtime,” says Mr Frederick. The elimination of the carbon tape also saves time when changing the tape.
But it’s not just cost reductions and efficiency that LAPP is pleased about, it’s also the improved environmental performance: “With the smooth process, we have been able to significantly reduce our CO2 footprint,” explains Ms. Dobritzsch. ” Such measures are enormously important for our further development as a company and the achievement of our sustainability goals.” And Allen Frederick is satisfied too. “The employees insisted on keeping the system after the test run,” he laughs. There is also a great deal of international interest at LAPP. The test phase in the logistics centre in Stuttgart has already been successfully completed and the system is now being rolled out there. “Of course, we will not throw away the old devices right away. We will continue to use them in parallel and replace them only gradually,” he explains. German-wide rollout in all LAPP logistics centres is due to be completed by the end of 2024.
Smooth-running logistics processes – with no waste, no chaos and plenty of happy faces. Just the way you’d want it. Just like a good round of Tetris. But more complex.
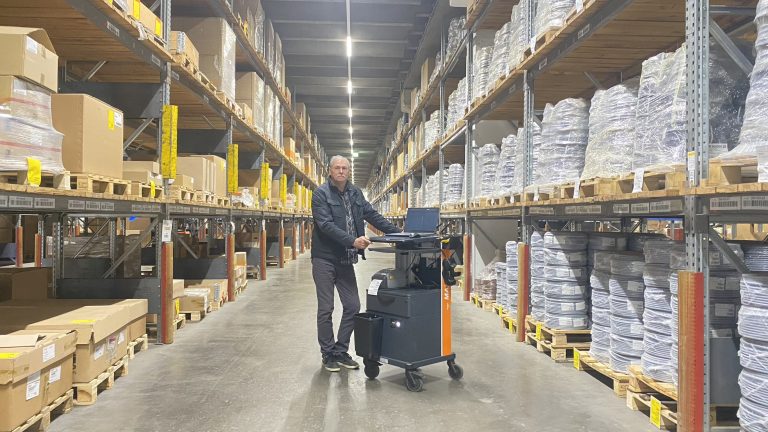