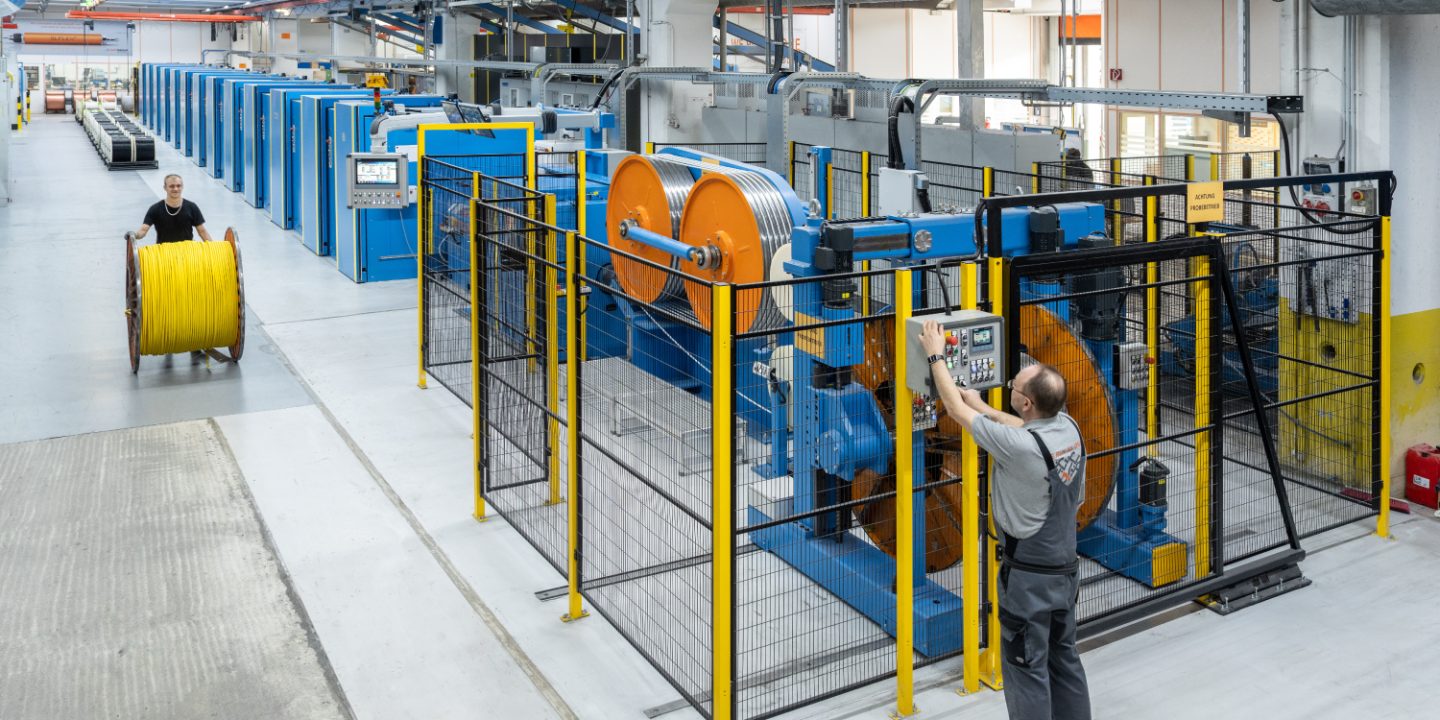
What do you need a tubular stranding machine for?
Joachim: In tubular stranding, single cores are twisted into a bundle of wires. With this, additional cores or conductor bunches are wound in several layers around a core material that is routed through the machine axis. The structure is based on the specification required for the respective cable type or application.
Why did you require a new tubular stranding machine at LAPP?
Joachim: The new tubular stranding machine was necessary to achieve our output of more than 35,000 kilometres per year at the cable plant, in line with our Strategy 2027. This represents a huge increase in our existing capacity in the area of stranding. In short, the latest technology will make us even more powerful and efficient and significantly increase our output of stranded products.
What does a system of this type look like?
Joachim: The new tubular stranding system at the Stuttgart cable plant is almost 50 metres long and looks a bit like a flat, orange rocket. It is the largest and most modern machine of its kind, with over 200 cubic metres of concrete removed for its construction.
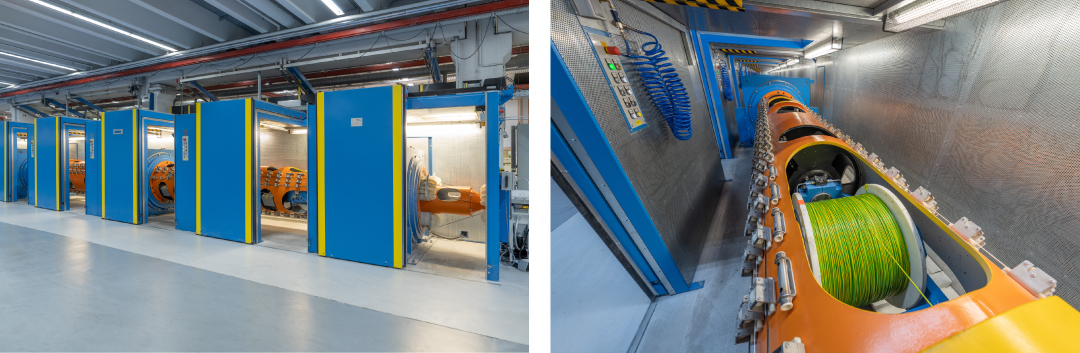
What is the greatest benefit of the new tubular stranding machine?
Joachim: The new tubular stranding machine is particularly powerful. Its maximum speed is 700 revolutions per minute. This makes it ten times faster than existing tubular stranding machines. Accordingly, more cables can be produced with it. Instead of the previous maximum speed of 32 metres per minute, the tubular stranding machine now emits up to 150 metres of stranded cable per minute. Needless to say, the entire process is digitally controlled: the control is monitored via ProfiNet using 13 integrated cameras. Pneumatic tightening and release of the coil and automatic refilling of talcum also make the new tubular stranding system highly efficient. Sustainability has also been taken into account in this investment of course. For example, the main drive motor for the pipe and double disc extraction is water-cooled, which serves as preparation for heat recovery.
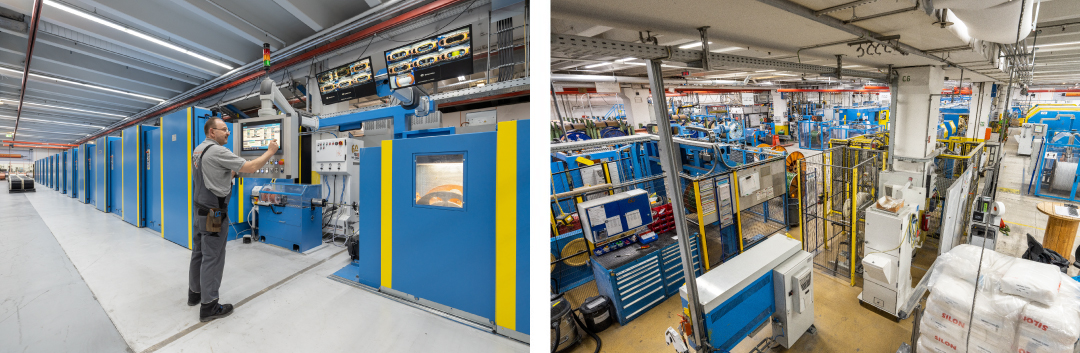
What other changes have there been at the site, what else is planned?
Joachim: As part of Strategy 2027, an increase in output of over 70 percent will be attained at the cable plant in Stuttgart, where the tubular stranding machine is a key component. It will also enable us to expand our portfolio with ‘premium-quality’ cables. Further process optimisations are also planned for the entire cable plant, as well as investments in new systems, such as a new extrusion facility and new, optimised transportation systems. To be able to produce successfully in a high-wage country, investment in digitalisation and automation is essential.