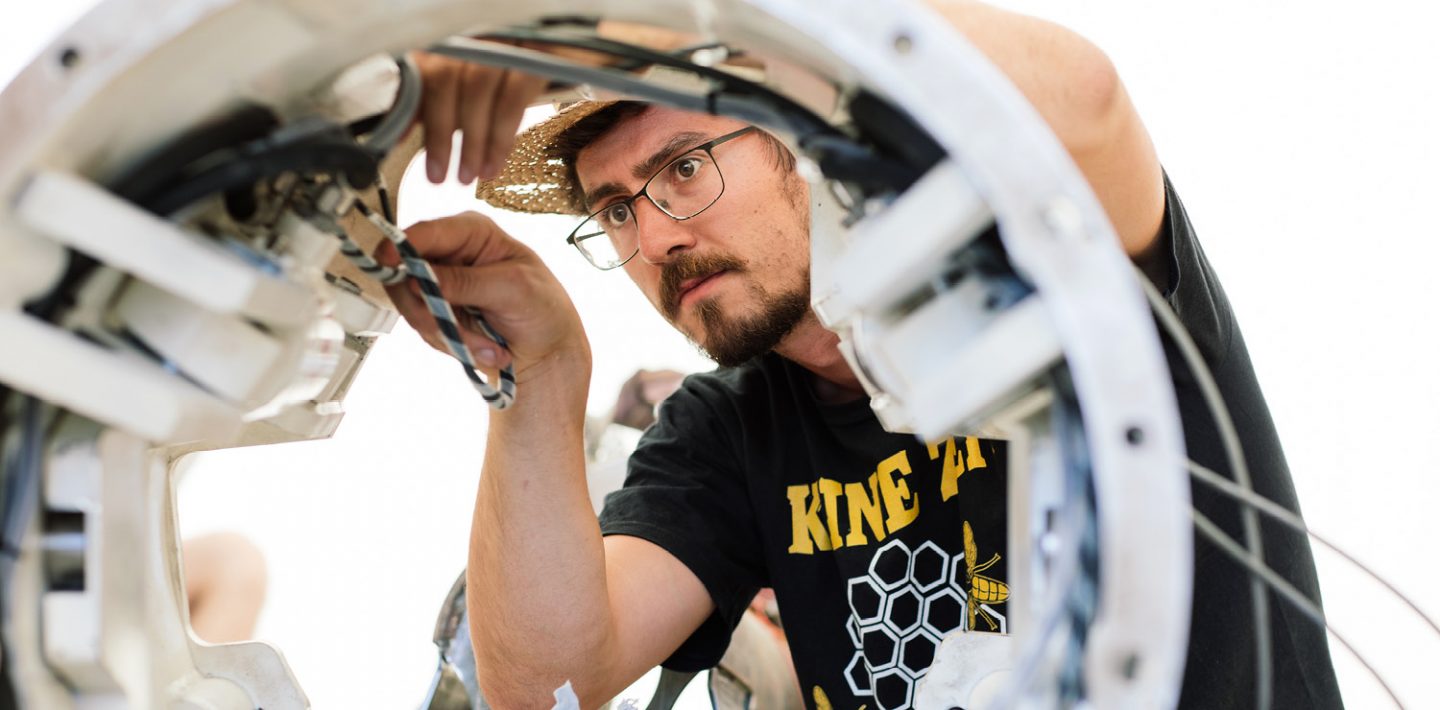
“You can really see that the Technical University of Munich is a veritable source of talent”, says Alois Heimler, experienced manager from the automotive team at LAPP, with a smile. He and Patrick Olivan, Senior Business Development Manager Services, have worked closely with TUM Boring over the past few months – both in the strategic and technical planning of the machine. Ultimately, the entire LAPP product family can now be found in the machines of the TUM Boring team. The key reasons why the young student team approached LAPP was the experience that LAPP was able to draw on as an established player on the market – and the broad portfolio that they could choose from at the connection experts in Stuttgart.
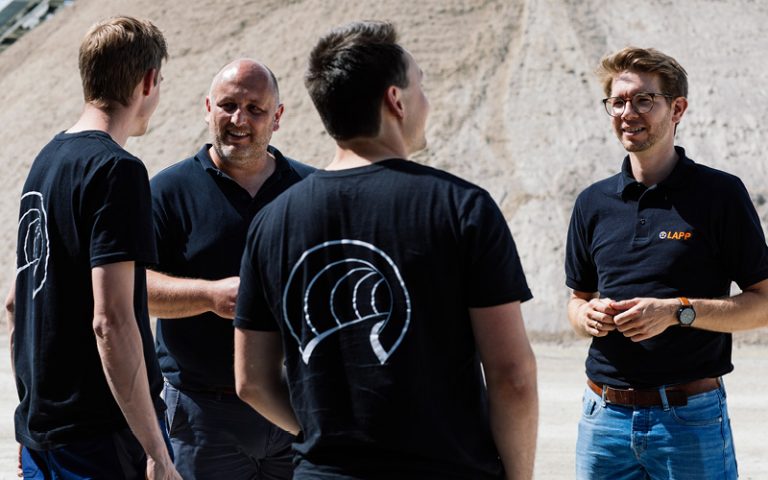
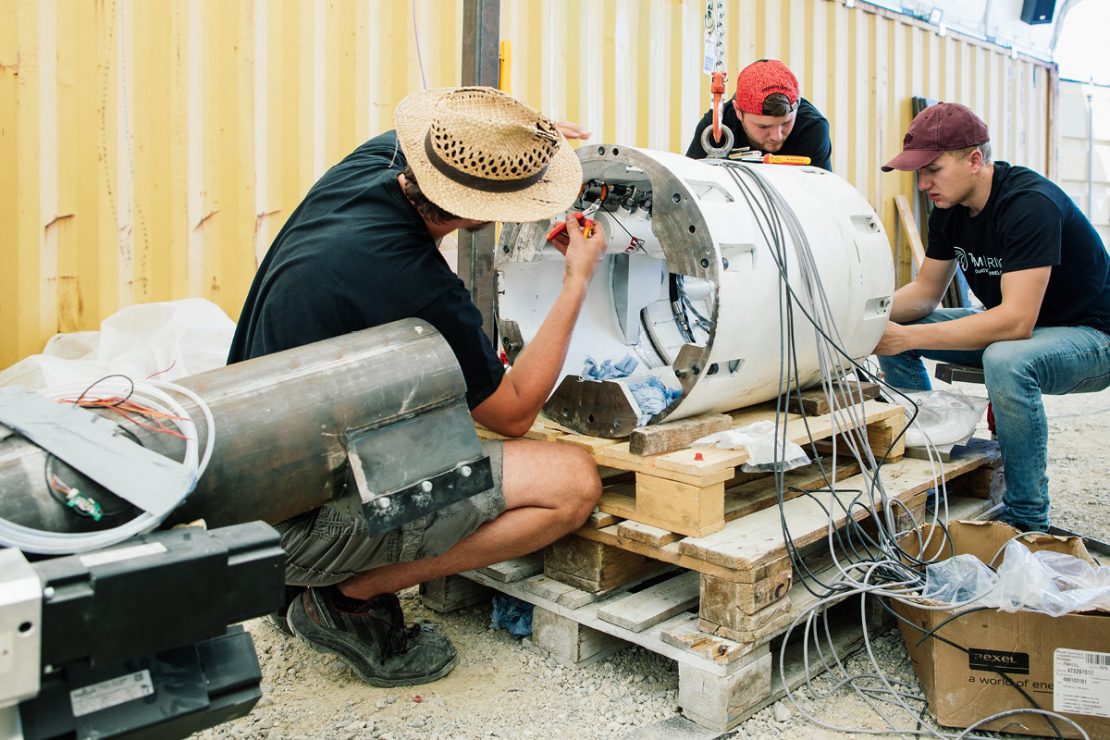
A team with a vision
LAPP was also convinced by the tunnel drilling project. TUM Boring is made up of around 60 students from 16 countries who independently handle planning, project management, operational implementation of their concept and marketing. Together, they are working towards one goal: redesigning urban mobility. They have the opportunity to do this in Elon Musk’s “Not-a-Boring Competition”. “In the long term, motorised traffic must take place underground,” said Jona Roßmann, who is responsible for External Relations Management at TUM Boring.
Anyone living in a large city or travelling regularly there knows what Jona Roßmann is talking about: CO2 emissions, noise, accidents and eternal congestions make everyday life extremely difficult. An example shows that underground transport is worthwhile: using a tunnel solution, the approximately 16 kilometre long route between Munich city centre and Garching could be travelled six times faster than it currently can by car and eight times faster than by underground. But the tunnel solution is time-consuming, costly and above all involves long-term construction.
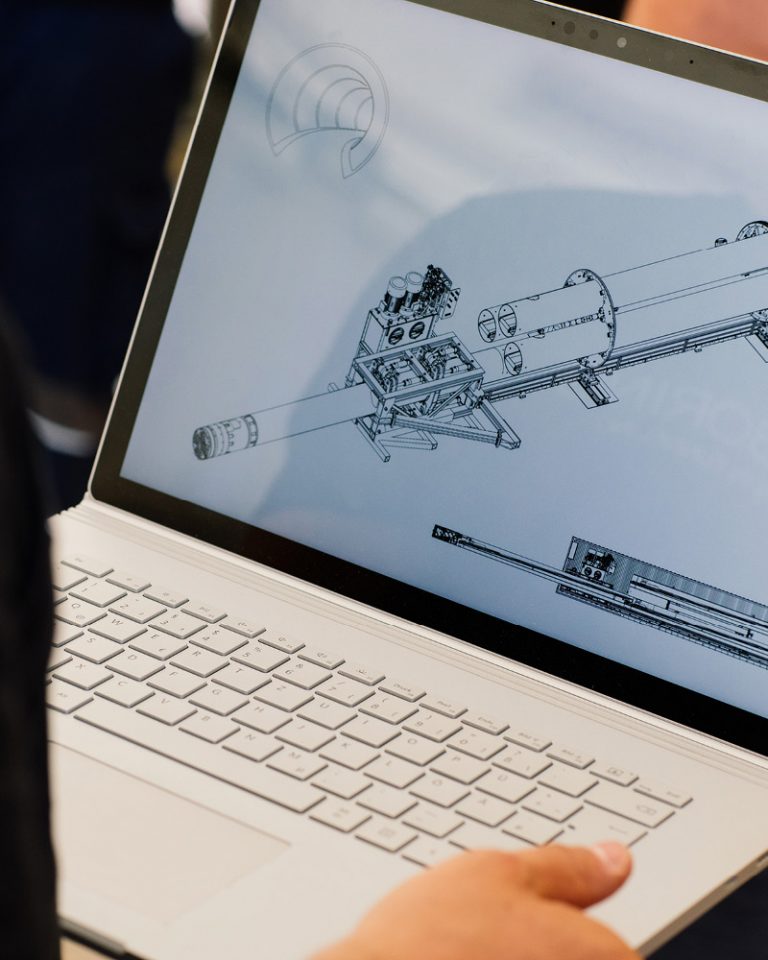
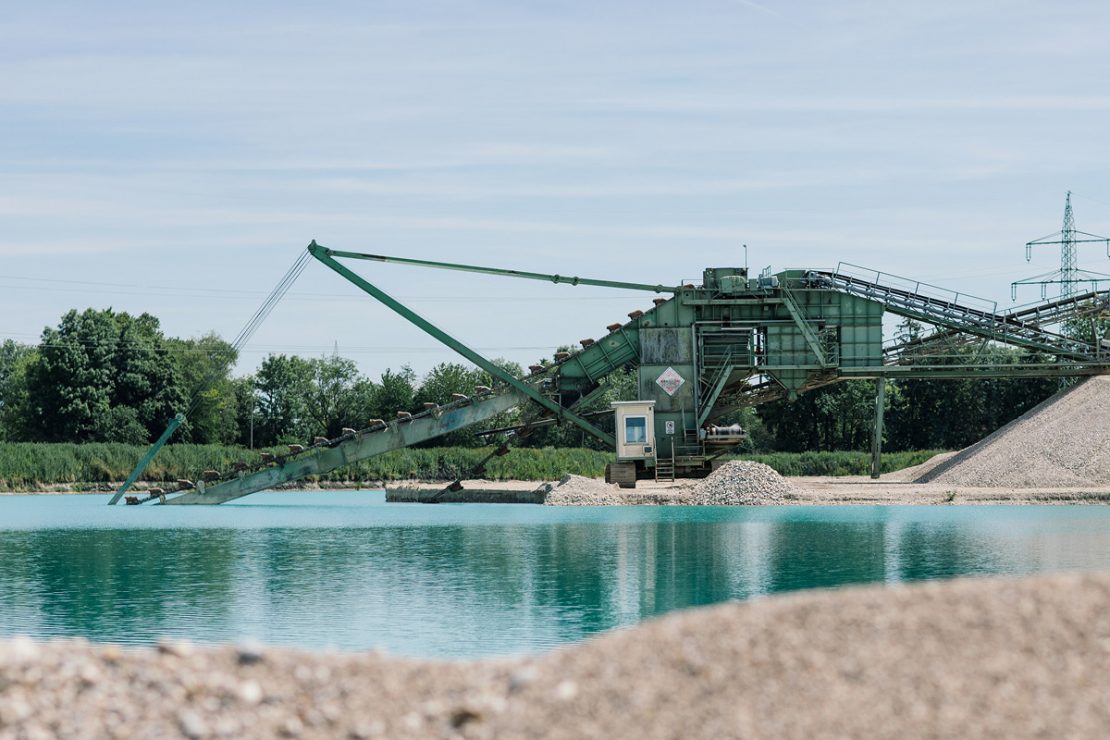
Together with eleven other teams of finalists, TUM Boring has the opportunity to design a tunnel boring machine that is faster and hence more economical than the current standard – making it possible to realise the vision of a new kind of mobility. Tunnel boring machines currently work at a slower pace than the creeping speed of a snail. “It would thus take extremely long to build up a safe, sustainable and significantly faster infrastructure for mobility underground using this technology,” said Sophie Defauw, who not only handles press enquiries at TUM Boring, but is also responsible for getting the team to the USA and finding accommodations for it.
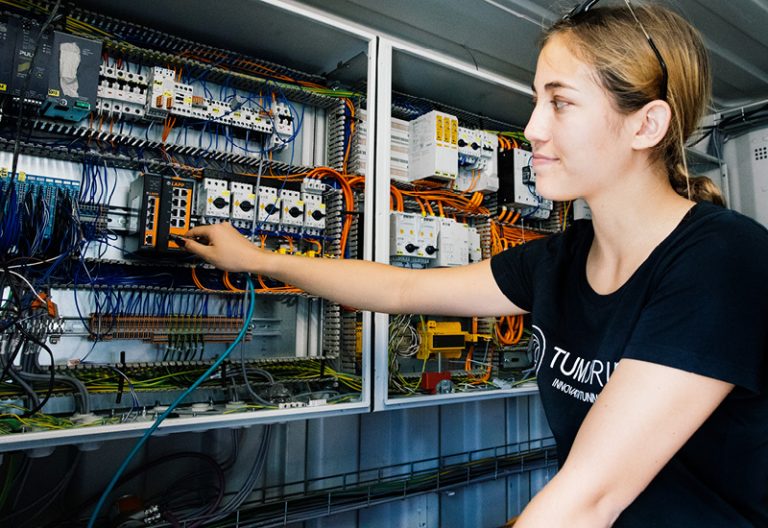
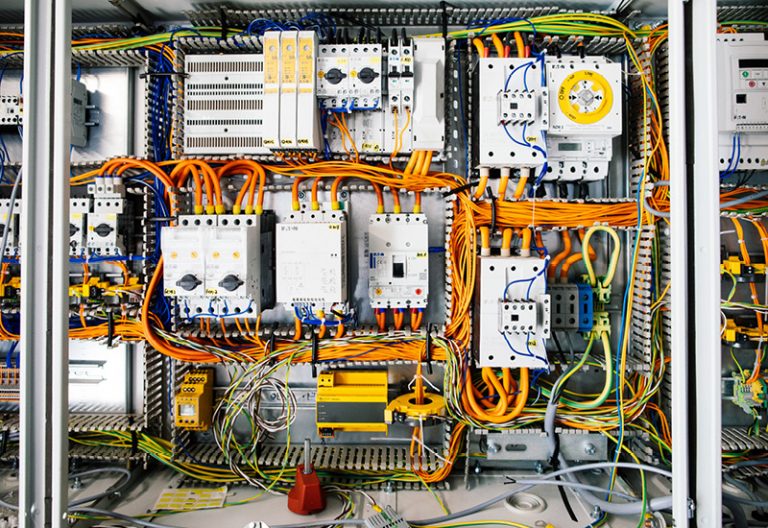
The 20-year art history student from Colombia has already worked as a columnist for six different magazines in four different languages – and as a teenager, she taught herself programming. “I’m delighted to be part of the team and such a revolutionary project”, says Defauw, as one of the sixty talented team members. The group is teeming with innovative energy, which impressed LAPP from the outset.
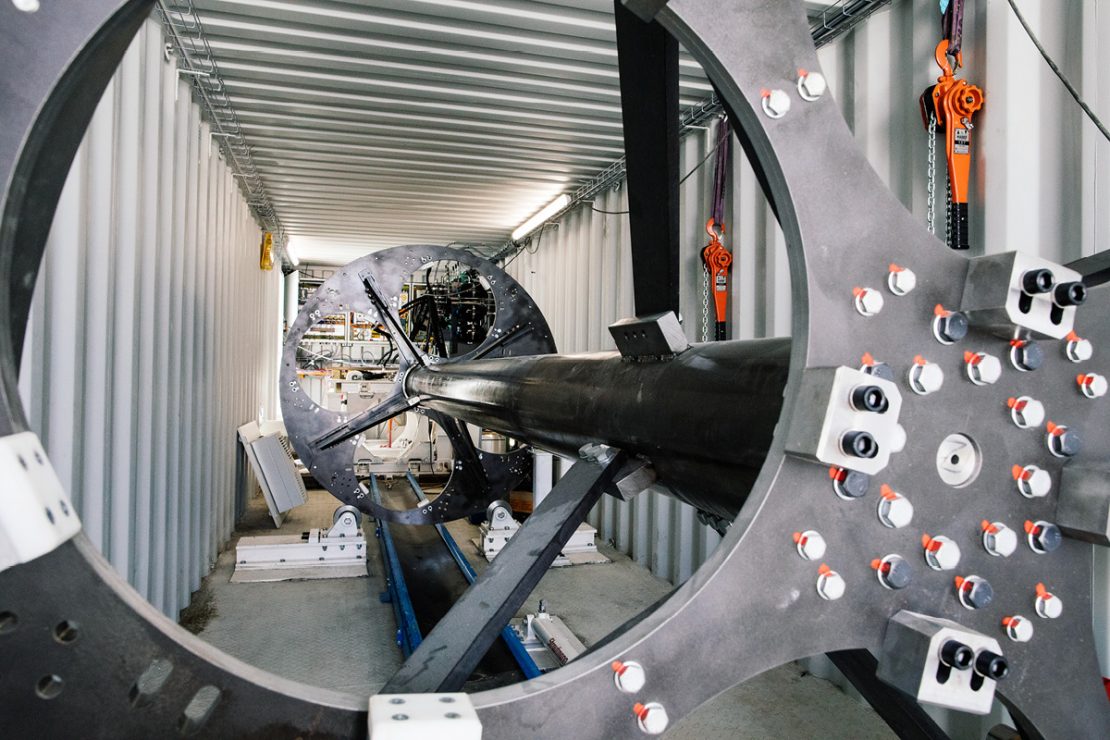
From theory to practice
When TUM Boring knocked on their door, LAPP was thrilled: “They had really good ideas and we noticed right away that they were serious,” said Alois Heimler. However, the process from the idea to the machine was far from simple: “The devil really lies in the detail”, says Johannes Drexler, who is responsible for the control system at TUM Boring. He is referring to the very agile and challenging development process for the machine.
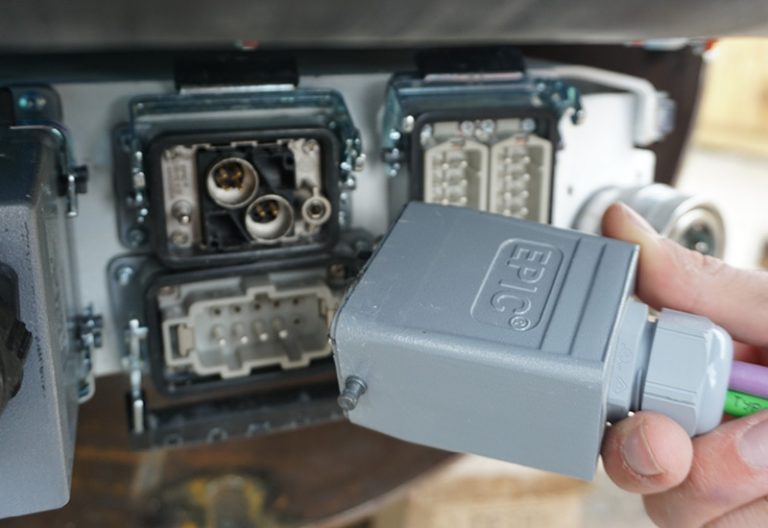
In autumn 2020, the team began designing initial plans and concepts – in autumn 2021 the tunnel boring machine has to compete against eleven other machines from all over the world. He and Jona Roßmann are particularly proud that the team has designed and implemented a competitive tunnel boring machine within a few months. They encountered one hurdle after another. Implementing the technical concept even required a connector housing that did not exist before.
“We were able to quickly configure one from LAPP to suit our requirements,” said Johannes Drexler. Sometimes the ideas were a real hit in theory, but difficult to implement in practice. Plans and ideas had to be flexibly adapted – and this in turn had an impact on technical details within the machine. “At some points, we realised that we needed to rethink,” recalls Roßmann.
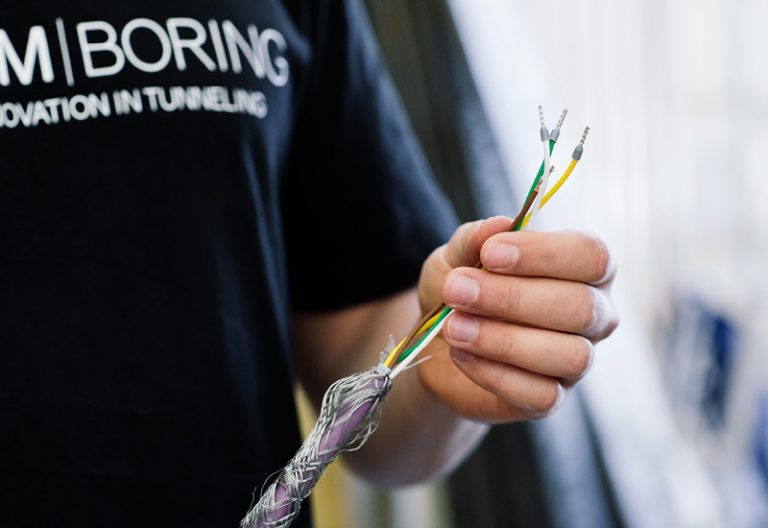

“But we have always relied on being able to openly discuss our ideas with LAPP and get honest feedback on them – and our contacts at LAPP have provided us with great technical support in finding pragmatic solutions.” TUM and LAPP formed a good team, says Patrick Olivan: “It was important for us do more than just provide support with products – we also wanted to support the students with our experience. For this reason, the telephone line between TUM and LAPP was ringing off the hook for days and even weeks at a time. The results of this collaboration are really visible.”
Young talents deserve to be supported
“Always!”, laughs Patrick Olivan when asked whether LAPP wants to support these kinds of student projects in the future. The two LAPP engineers feel transported back to their own student days. “It’s fun to try out something new time and time again until it fits”, remembers Alois Heimler, who studied industrial engineering himself. So, both of them are delighted to be able to check how the students in Neuching are doing and see how the joint theoretical planning on the CAD model is now taking shape in practice. There are just a few weeks to the final, and Heimler and Olivan are already convinced that this team will win. Promoting young talents is a given for them, which is why their support was clear from the outset: “These are the solution developers of tomorrow”, says Patrick Olivan before disappearing again into the container behind the tunnel boring machine.
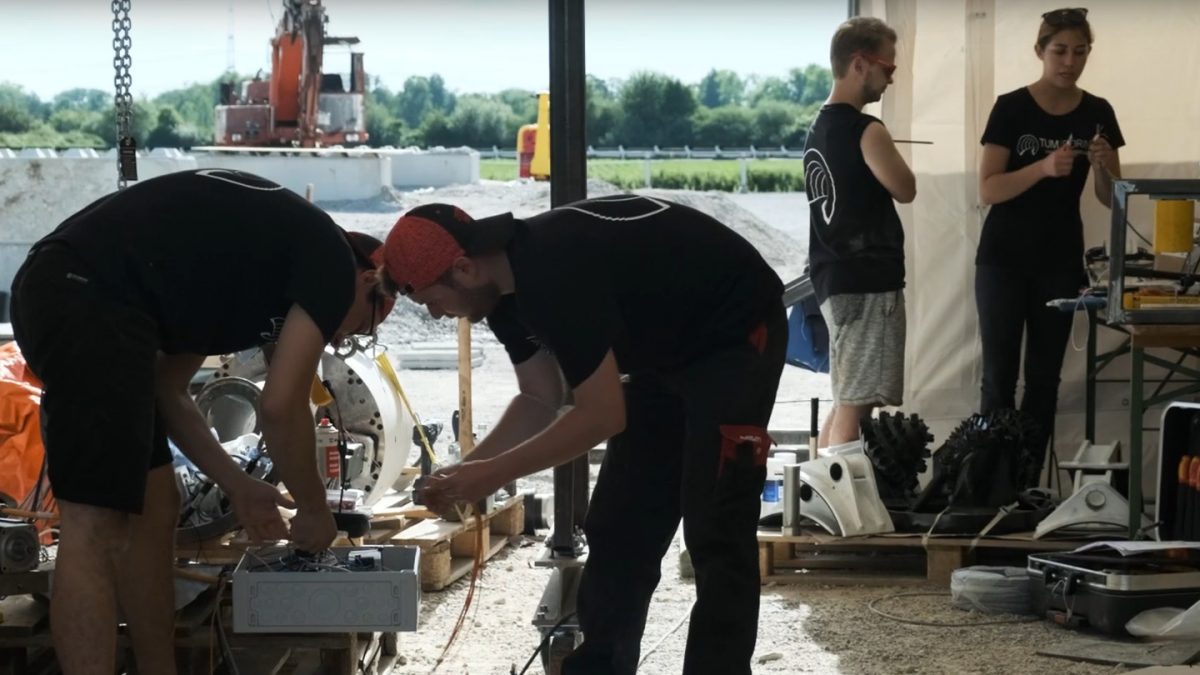
Video: © LAPP supports TUM Boring – Innovation in Tunneling in Elon Musk’s competition