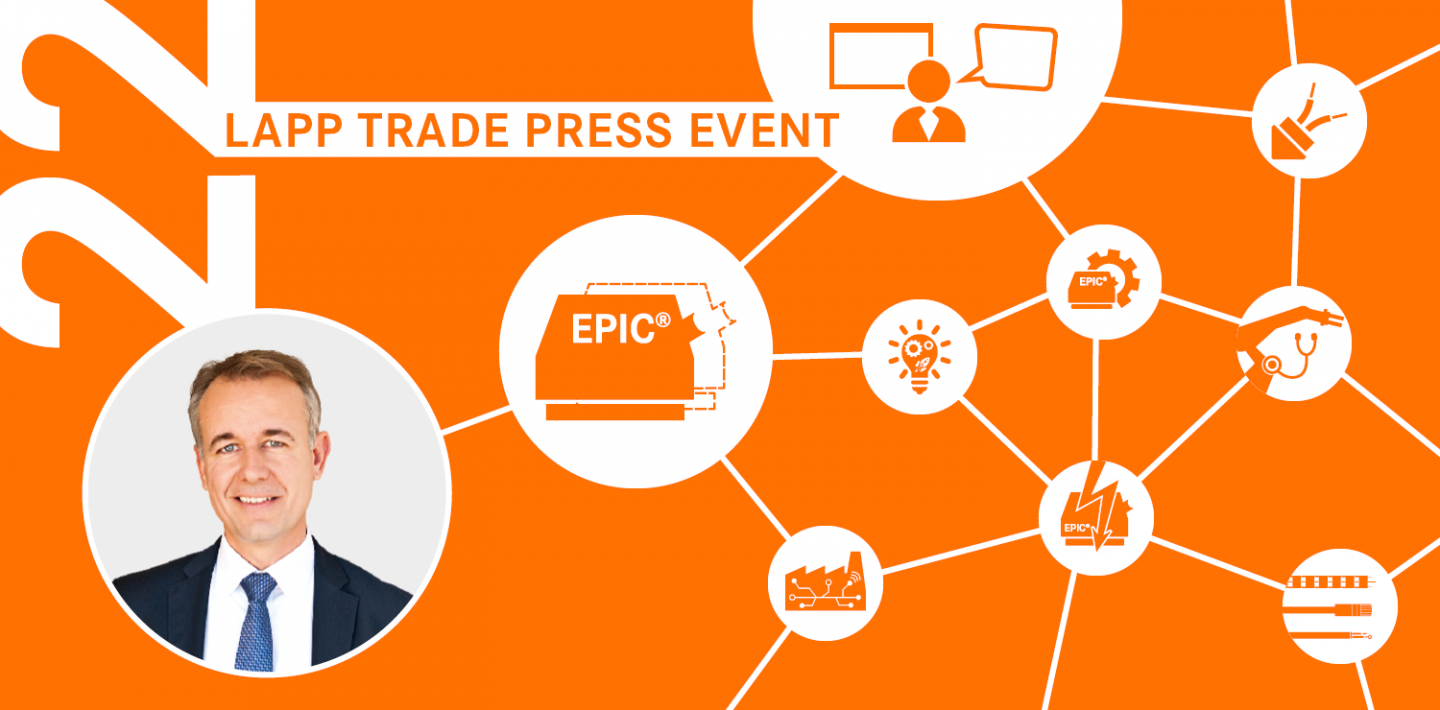
To safely separate and connect cables, EPIC® connectors are and remain indispensable in mechanical engineering, control cabinets and outdoor applications. And there is still plenty of room for optimisation. After all, the trend towards miniaturisation doesn’t stop at connectors. In many areas of industry, applications are becoming smaller and smaller, while the power density increases. Connectors must also keep up with this trend. This is particularly clear in automation technology (IC), which is currently likely to have a key influence on industrial development and drive it forward. As size M12 circular connectors are most commonly found in this environment, it is evident that the standards for this connector also need to increase.
In order to transmit more power to the applications, a greater current than the previous 12A will be required in the future. An output of 16A is increasingly in demand. However, since previous M12 connectors had already been developed close to the limits of the feasible, the question arose as to how this performance increase could be achieved.
Why M12 L – what really counts for customers
There are already a few manufacturers that have M12 L-coded connectors. However, it can be even better. The new M12 L-coded connector from LAPP not only guarantees high power density, but is also much smaller. “Miniaturisation and high power density without cutting back on the quality of the connection are crucial to provide the best service to customers,” says Martin Guserle, Head of Business Unit EPIC® Connectors at U.I. Lapp GmbH. The new M12 L connector only uses 43% of the space of the predecessor technology (7/8″) and occupies 56% less space than the largest competitor housing. It is also 100% PROFINET-compliant, has vibration-resistant and climate-resistant 360° shielding and can also be delivered with K-coding (630 V) in the first stage. In addition, all cross-sections defined by the PROFINET user organisation (PNO) are possible (0.75/1.5/2.5 mm²).
The digital path to new innovations
The new M12 L-coded connector is an all-in-one solution that overcomes all seemingly impossible physical challenges in an extremely small housing. But how does this work? The digital twin makes it possible. “In the past, the development processes were much more complex. Designs were created based on empirical values, followed by the construction of a prototype. The prototype was then tested in a laboratory and it was often found that technical changes were still required. This process was commonly repeated several times before the desired result was achieved”, recalls Martin Guserle. Nowadays, speed is becoming increasingly important when it comes to innovations. A greater amount of digital testing on the product leads to faster development cycles. Physical samples are simply created using a 3D printing process to verify the look and feel of the product as well as the handling and assembly in production and at the customer site. “Since connectors are now generally planned and calculated in advance, we can find the best technical solution in a targeted manner, thus avoiding a huge amount of resources,” says Martin Guserle.
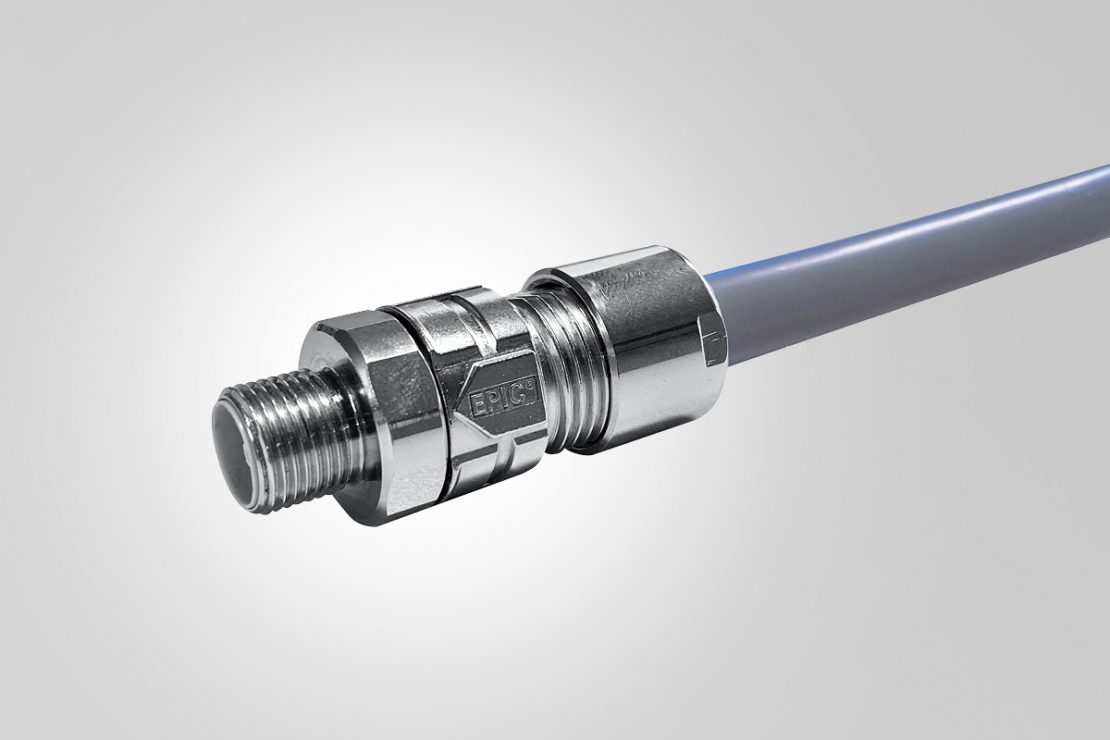
LAPP currently uses various simulations to achieve this increase in performance:
- The finite element method (FEM) is a general numerical process used for different physical tasks. It is a strength test for bodies with a geometrically complex shape which is used because classic methods prove to be too complex or impossible. The FEM is used to calculate and check technical designs so that critical points on the components can be correctly dimensioned.
- Calculating the thermal load using the example of M12 L. Due to the limited installation space, the required 16A current poses an extreme challenge for the component. When so much current is transmitted using tiny contact areas due to the design, heat is generated that has to be controlled in the connector. As a result, new products are “digitally” calculated at LAPP to guarantee a safe design. This ensures that the products will function reliably throughout their entire service life. This enables a reliable mastery of the absolute limits, making the maximum power density possible in the smallest feasible connector housing.
- 3D printing for first handling sample: Once all calculations and simulations have been completed and integrated into the design, LAPP creates a first 3D sample. This is a real sample which can be used to assess the ergonomics, installation space and design. This means that the design process is provisionally complete, and the tool engineering process can begin in order to plan and implement the series tools for series production.
- Filling simulations – Moldflow®: In addition to ensuring functionality, the design of the connector must also guarantee reliable manufacturing. The filling simulation provides an insight into the design of the tools for the injection-moulded parts and also indicates optimisations that may be required for the product. The aim is to simulate the tool in advance to perfect the design.
Martin Guserle says, “With our work on the digital twin, we are now able to find out exactly where the maximum limits lie, for example in terms of temperature distribution, contact resistance and current load, and we can achieve the optimum in all aspects. This makes the development processes much quicker, more resource-saving and more cost-effective.” LAPP got involved with these issues very early on and is one of the leading providers using all kinds of digital tools for innovations.
Customer design-in process
Customers are increasingly using digital portals to develop their machines, systems and tools. Special databases such as ZUKEN and EPLAN, which feature an ever-growing number of manufacturers, are increasingly being used to select suitable connectors. On these platforms, customers receive all the information about the product, including the digital 3D models – i.e. the digital twin of the actual product. “Our experience shows that most customers are now only interested in the digital twin and are becoming much less interested in physical samples. This indicates the change from product to digital information, as further digital processing can be carried out directly by the customer”, says Martin Guserle.
Why does the future belong to the digital twin?
The digital twin contains much more information about the product than would ever be possible with a physical product sample. This information collected during development is then used for the Design-In, which is used throughout the entire life cycle right through to recycling. The digital twin is therefore the basis for AI applications. These could enable a status display for the connector right through to predictive maintenance. It is already commonplace for products to be created and further processed without actually being physically constructed. It is also foreseeable that these digital components and systems will communicate with each other and develop each other. Due to its usage location and design requirements, the connector is an ideal component to perform additional functions if equipped with more intelligence.