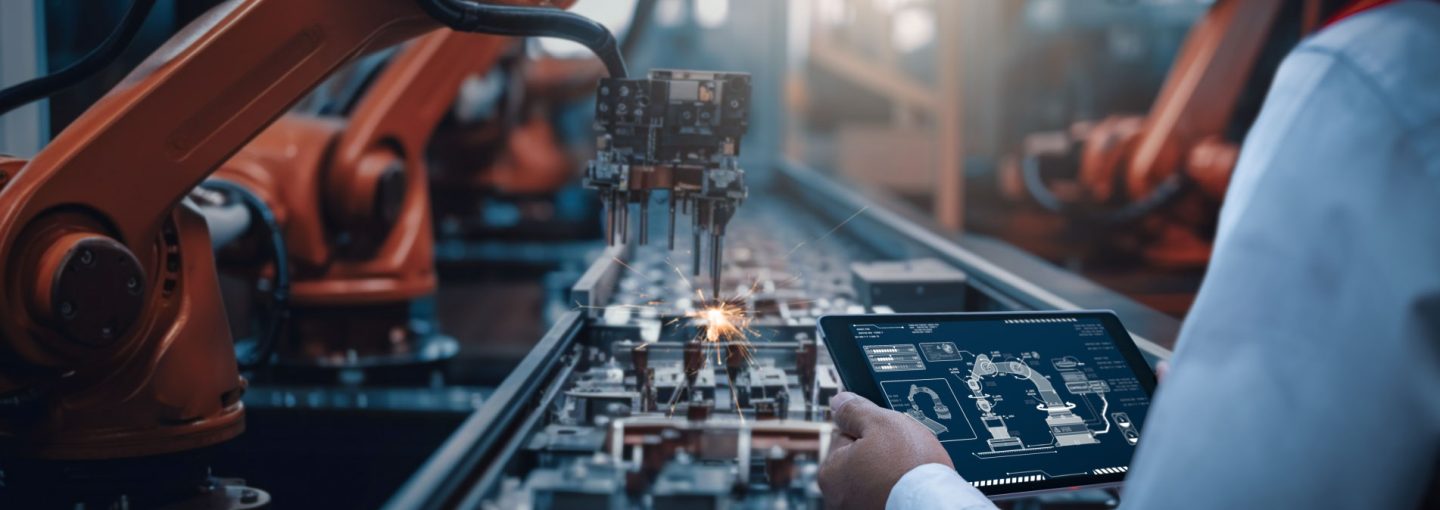
What is Industry 5.0? Prof. Oliver Riedel has increasingly been faced with this question recently. The Executive Director of the Fraunhofer Institute for Industrial Engineering IAO in Stuttgart and Director of the University Institute for Control Engineering in Stuttgart responds to this question with an anecdote. Around six years ago, a friend from Japan wanted to know: “What is Industry 4.0?”. Riedel explained the networking of things and cyber-physical systems just as the Industry 4.0 platform had been conceived when it publicly launched the term in 2011, sparking some serious hype. The friend then asked: “And where does this leave the human being?”. Riedel had to admit that, in Germany, a lot of attention was paid to how machines communicate with one another, but not to how they communicate with people and what this even provides for people. However, the IAO has never lost sight of this matter, emphasises the Fraunhofer scientist.
Back in 1981, the institute laid the foundations for what is now known as the further development of Industry 4.0 – Industry 5.0 – with its guiding principle of “human-technology organisation”: technology that serves people and is combined with social aspects and sustainable management.
The fact that Riedel’s friend was able to painfully highlight the issue with Industry 4.0 with such confidence is linked to the Japanese concept of Society 5.0. What this means is “a society that is geared towards people which strives for a balance between economic progress and solving social challenges through a system that strongly integrates cyberspace and physical space”. This is what is now becoming important in Germany with Industry 5.0. With Industry 5.0, this Japanese perspective is now also being incorporated into our industrial landscape. For the first time in the history of the industrial revolutions, the focus of Industry 5.0 is on the well-being of people and no longer just on maximising digitalisation and machine networking to further increase efficiency, as is still the case for Industry 4.0. Instead of replacing people with machines, the aim is to enable people to better manage their work. “Better” doesn’t just mean “more efficiently”, but rather working in a way that is perceived as meaningful and promotes the protection of physical and mental health.
From Industry 4.0 to 5.0
In 2011, Henning Kagermann, President of the Research Council of the German Academy of Science and Engineering and former board member of SAP, coined the now ubiquitous term ‘Industry 4.0’ at the Hannover Fair. Machines need to be further networked and processes automated in order to increase efficiency and transparency. Just five years later, Kagermann used the term ‘Industry 5.0’ for the first time at the Hannover Fair 2016, to describe “intelligent, networked and flexible production” that puts people at the centre.
In 2021, the European Commission addressed the concept of ‘Industry 5.0’ in its white paper. “It takes into account the lessons learned from the pandemic and the need to develop an industrial system that is inherently more resilient with regard to future shocks and stresses and really integrates the social and environmental principles of the European Green Deal.”
The biggest challenge here is that the technical complexity in factories is constantly increasing and people are barely able to keep up. This is why filters are needed to reduce complexity to the right level, suggests Oliver Riedel. Artificial intelligence (AI) and machine learning (ML) could be such filters that support people. Conversely, AI also depends on human support. With the new AI studios, the experimental environment in the model factory and the topic-centred innovation networks, the IAO offers transformation formats for industry.
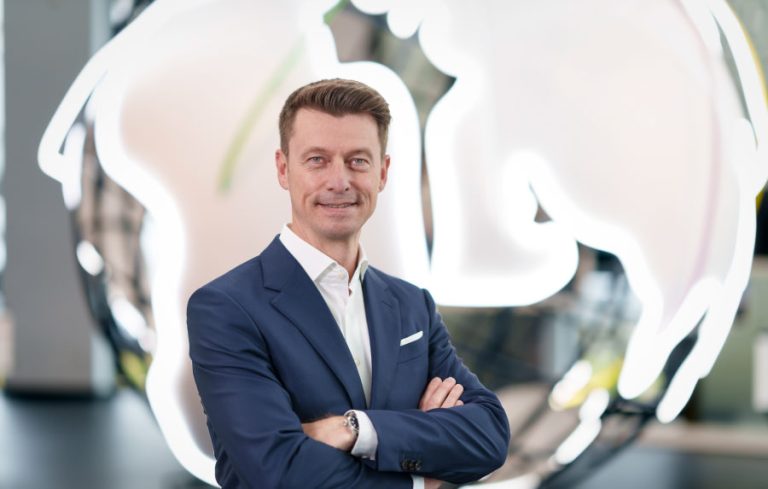
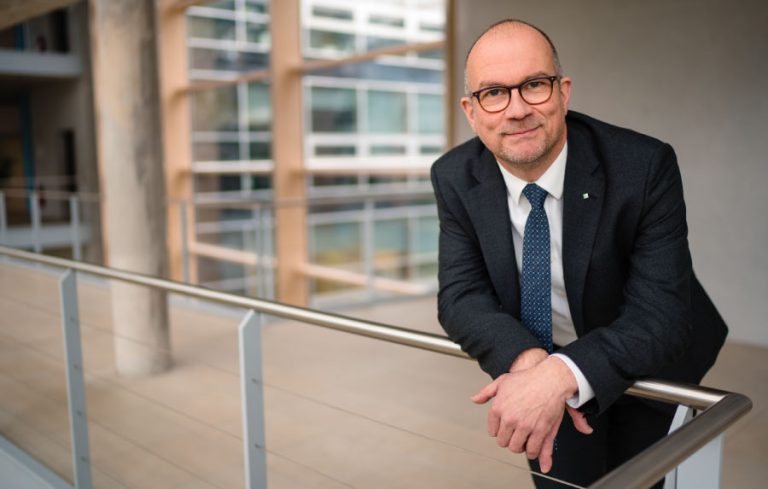
This is illustrated by the following example: one of the doctoral students of Prof. Riedel studied arc welding for his doctorate and developed a process that uses machine learning with an acoustic sensor to determine the quality of welding points. The aim is to increase quality and relieve workers of tedious inspection work. The question was how many welding points the model requires before it is sufficiently trained. He started with a few thousand. At the end of the doctoral course, following many hours in the laboratory, the sobering result was that 120,000 welding processes had to be fed into the model before it could specify the quality correctly. “AI and ML always need people as their initial spark”, says Riedel. For the IAO Director, AI is therefore not competition for people or a threat to jobs. “The aim of AI is to reduce technical complexity for the benefit of people and is thus a good example of the idea behind Industry 5.0.”
According to the IAO Executive Director, Industry 5.0 offers great opportunities for companies like LAPP. He has been in contact with the chief technology officer for years to discuss the possibilities for the company. These are internal – for example in the creation of products and their manufacture, but also in the culture.
At LAPP, the focus has been on employees since its founding and they are seen as part of the LAPP family. The aim now is to focus primarily on the people working in production at LAPP through innovation and optimisation. “Our employees are the key success factor at LAPP. As a result, our strategy focuses not just on how new technologies can be used efficiently in our production, but also on how these technologies can best support our employees – i.e. the interaction of humans and artificial intelligence in procedural workflows”, says Hubertus Breier, Chief Technology and Innovation Officer at LAPP.
The medium-sized company has been relying on AI applications in day-to-day work for several years. In the financial division, for example in the case of electronic account statement processing, account statements in account statement post-processing are now interpreted fully automatically from the cloud at LAPP. Supply Chain Management also relies on an AI solution when searching for new suppliers. The software used there can search the Internet at high speed, find suppliers all over the world, evaluate them and generate a list of the most promising companies. The purchasing team can then approach this in a targeted manner.
The focus on people is particularly evident at the LAPP Group’s French cable production plant: Câbleries Lapp SARL in Forbach, France, is the first plant to undergo extensive modernisation as part of the optimisation strategy in the LAPP Group’s global production network. An example of this is the optimisation of the wire line: traditionally, the layout of this production line consisted of one line. This means long journeys for employees. The new structure is arranged in a U-shape around the people. The aim here is to place all of the plant’s workstations next to each other as much as possible. This shortens the walking distances by 96 percent for employees, reduces set-up times from 10 to 6 minutes, and the machine can produce almost 50 percent faster. Customers, in turn, benefit from this.
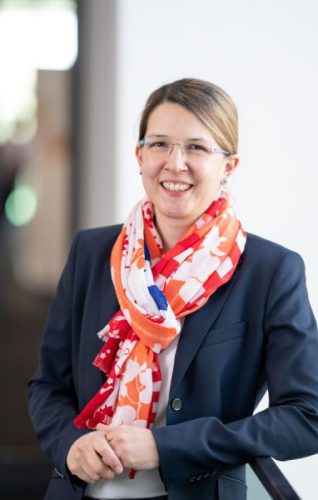
Externally, the idea of Industry 5.0 is reflected in an even stronger focus on the needs of customers and their employees. For example, a customer orders 20 kilometres of Ethernet cable. Through this order, LAPP knows that the customer wants to secure fail-safe communication in their factory. As a partner to the industry who is in constant contact with customers, the connection specialist can therefore meet customer needs not only with cables, but also with hubs and switches – and with the highest quality standards.
This way of thinking about reducing complexity in highly automated and technologised machine parks is not new to LAPP. One example is ETHERLINE® GUARD, a small box that assesses whether the cable should be replaced in the near future based on the transmission quality of a data cable. Another is the Health Check Service for data networks, which, among other things, detects EMC problems and suggests improvements. A new addition to the innovation team at LAPP is the smart cable drum, which automatically orders replenishment when the cable runs out. This brings us full circle to Industry 5.0 and LAPP’s efforts to always put customer needs first: “Our technology serves to reduce complexity and make life easier for people at customers’ sites.”, summarises Dr Susanne Krichel, Head of Innovation & Advanced Technology. “While this topic seems to be ‘old hat’ in Japan, we still have a lot of catching up to do – but the fact that this approach is now receiving so much emphasis in our industry also shows me that LAPP is taking the right path in order to ultimately contribute to a world where people have a better quality of life.“